【编者按】
SMT无疑是电子组装技术的核心,然而,波峰焊、返修、清洗、敷形涂覆和胶材应用等也是电子组装技术不可或缺的重要工艺技术,普遍应用于军用及航空电子产品、通讯产品、汽车电子以及医疗电子等高可靠性产品的研发与生产。这些工艺技术在一般的工厂往往不被重视,因而也很少有比较深入的研究。鉴于此,本次将重点介绍波峰焊、返修、清洗、敷形涂覆和胶材应用等工艺技术的常见问题及解决方案。
摘要:现代电子产品向多功能、微型化和高密度方向发展,通讯网络产品上使用越来越多的细间距器件,间距最小到0.4mm,同时一些核心器件(如CPU)的尺寸越来越大,从55mm到80mm。用常规的返修工艺,出现合格率差和效率低,甚至无法返修的情况。从工程应用的问题出发,对当前系统单板中的返修难题进行分析研究,并针对问题提供解决办法。
关键词:细间距;高密度;大尺寸单板;返修
1、概述
随着电子产品的快速发展,电子产品体积向更大和更小两级化发展,对生产和逆向返修带来很大的挑战[1-3]。尤其对通信类产品,本身对可靠性要求高,如何保证返修品质,即可靠性返修是PCBA(Printed Circuit Board Assembly)返修的核心[4]。本文重点介绍PCBA返修中几种典型工艺与常见问题。
2、预热
预热是成功返修的前提,在返修之前使用烘箱来预热基板,可避免"爆米花”现象。所谓“爆米花“现象是指SMD(Surface Mounted Devices)湿度高于正常器件,返修时因快速升温导致内部开裂。不同于回流炉焊接是在密闭的环境下,温差较小,返修是局部加热,PCB上各区域的温差较大,在未预热或未充分预热的情况下,返修在高温下长时间加热会出现基板脱层,生白斑或起泡,变色等问题。同时返修时PCB变形问题也很严重,尤其是较薄的PCB,单板变形很容易导致BGA虚焊或短路问题,而提前预热可有效解决该类问题。
3、大尺寸大热容PCBA返修
3.1 存在问题
1)大尺寸大热容单板吸热量大,受热不均,容易变形。
2)大尺寸的BGA(Ball Grid Array)受热不均,焊接温差大,容易出现短路和虚焊。
如图1所示,PCBA尺寸:840mm×300mmx3mm,BGA尺寸为55mm×55mm。
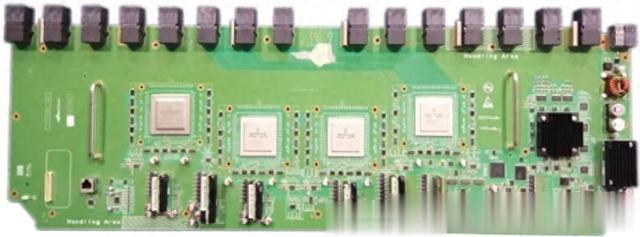
图1 大尺寸单板
3.2 解决方法
1)整板充分预热,将BGA各焊点的温差控制在10℃以内。
2)利用托架或支撑顶针,降低单板变形如图2所示。
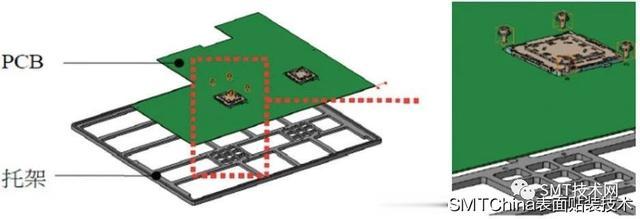
图2 用工装降低PCBA变形
3)优化印锡钢片,因短路一般发生在BGA的四个角,可以通过减少钢网四个角的开口面积减少连锡问题。
4、大尺寸大热容PCB焊盘除锡
传统除锡方式为烙铁+吸锡编带接触式除锡,这种除锡方式对一些焊盘间距小、热风焊盘多的单板有潜在风险,风险主要有:
1)烙铁接触时间长会熔铜。
2)焊盘脱落。
3)刮伤焊盘周围绿油导致短路。
4)一些特殊芯片,锡球中间有chip元件的,除锡时烙铁很容易碰到chip元件。
芯片手工除锡如图3所示。
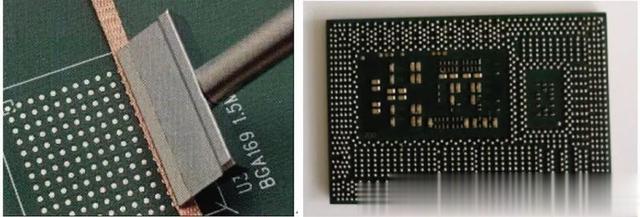
图 3芯片手工除锡
5、PTH(Plating Through Hole)通孔器件返修
PTH返修通常是用小锡炉浸焊来完成,但对于较厚的PCBA或者吸热量大的器件,用小锡炉浸焊会有以下问题:
1)焊接时间长,容易掉焊盘。
2)焊接时间长,容易出现熔铜现象。
3)焊接时间不够,虚焊,透锡不良。
4)热冲击导致PCB变形,孔壁断裂,如图4所示。

图4浸锡时间长导致PCB孔内不良情况
解决方法:
1)返修前先预热PCBA,整板预热后再拆除器件。
2)要预先测量浸锡温度,浸锡时间要管控。
3)焊接新器件前也要整板预热,包括器件。
4)用BGA返修台拆焊。
6、BGA器件返修
6.1 BGA返修基本步骤
1)设置加热曲线;
2)拆除器件;
3)清理焊盘;
4)清洗;
5)印刷焊膏;
6)贴片;
7)再流焊接;
8)清洗;
9)外观检查及性能测试。
6.2 BGA返修各个环节需要注意的问题
6.2.1加热曲线设置
由于器件的热特性很大程度取决于器件的布局状况、器件本身特性和PCB状况,所以对于单板上每一个BGA器件都应设置相应的加热曲线。通常用测温板来标定器件的加热曲线,测温板的制作方法为:用钻头在焊点与PCB焊盘的结合处钻孔,将热电偶埋入孔中,填充红胶或银胶,然后加热固化。
BGA器件规格书中有推荐的回流温度曲线,利用测温板在BGA返修设备上进行温度调试得出满足该BGA的加热曲线。选择合适的加热曲线是BGA返修成功的关键,即加热曲线是整个BGA返修的核心。好的加热曲线如图5所示,尽可能让BGA的不同热容的焊点在同一液相温度内,不会出现过温现象。每个焊点的温差小,保证合理的液相时间,且不会连锡短路。
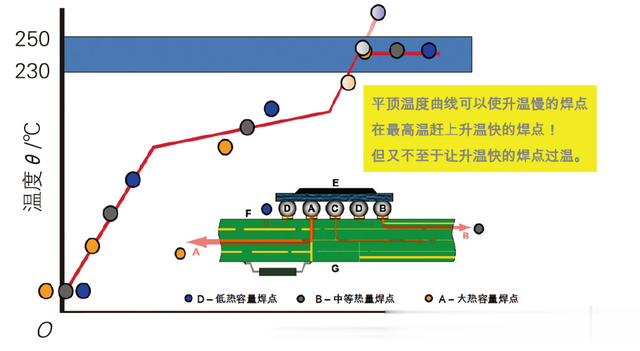
图5BGA加热曲线 图5BGA加热曲线
加热曲线与BGA返修台的设备性能有关。BGA返修台按加热方式分为红外加热、热风加热和红外/热风混合加热三种。红外/热风混合加热的方式最好,BGA各点的温度几乎是一样的,如图6所示。
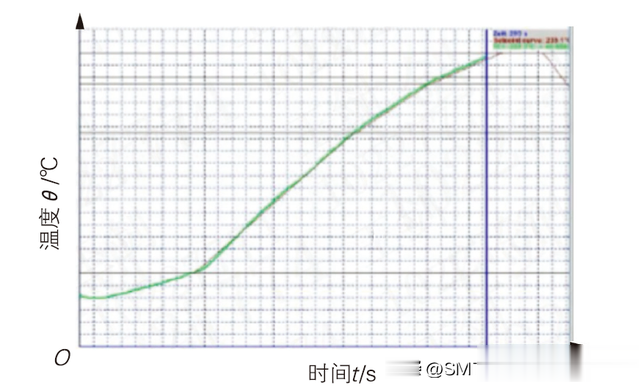
图6实际温度曲线与目标曲线重叠
6.2.1.1预热要求
整板预热的目的是减少对返修部位的热冲击,降低单板变形。预热过程要均匀稳定。一般来说,PCB整板要预热到120℃,对于热容量较大的BGA和较厚的PCB,需要更高的预热温度。预热温度要适当,太高若超过PCB基材的Tg(玻璃化转变温度)点,单板就容易变形,预热温度太低,又起不到减少变形的作用。
6.2.1.2拆除器件
当BGA所有焊点熔化后,用真空吸嘴把器件吸走,此时必须要确保所有焊点的温度都达到熔锡温度,无铅焊料最高温度235-245℃。如果未达到熔锡温度就拆除器件,可能会把焊盘拉起。
6.2.1.3焊盘清理
拆除器件后要清理PCB上的焊盘,得到平整度高的焊盘表面,以利于再次印锡。焊盘清理时要选择合适的烙铁温度和吸锡线,注意操作方法,避免损伤焊盘。对于一些贵重单板,建议采用非接触式的除锡工艺,先将焊锡加热融化,再用真空将焊锡吸走,可有效降低焊盘清理中的不良问题。
6.2.1.4印锡
对可靠性要求高的产品,返修时需要印锡,锡量对可靠性都有较大的影响,锡量不足不能形成充分的共晶焊点,容易产生疲劳损伤,长期可靠性较低。印锡的方式有两种,其一是在PCB焊盘上印锡,其二是在BGA引脚上印锡。在PCB上印锡要求BGA焊盘周围有足够的空间以便操作钢网,在BGA焊球上印锡需要制作印刷工装。
6.2.1.5贴片
贴片主要保证器件贴片后的精度要求,为保证器件自对中效果,引脚面积至少60%位于焊盘上。
6.2.1.6再流焊接
再流焊接的温度参照拆除器件的温度设置。在焊接时注意对周围的其他BGA或QFN(Quad FlatNo-lead Package)器件采取隔热措施,如隔热工装等。热敏或潮敏器件也要采取相应的保护措施。
7、QFN返修
QFN由于封装结构的特点,返修有一定难度气
1)元件小,重量轻,在加热时易被热风吹移位。
2)PCB上布局密度大,QFN周围有很多阻容元件,狭小的空间难于印锡。
3)QFN周围元器件一般布局较密,周围器件易发生焊点重熔,导致金属间化合物(IMC)增厚,从而降低可靠性。
4)器件温度传导快,内部芯片容易因温度过高而受损,在受潮的情况下易产生”瀑米花”现象。
5)不当的加热曲线会导致元器件翘曲变形,PCB起泡、变形和分层等。
QFN返修基本同BGA返修相同,需要注意的是由于QFN器件周围布局较密,QFN拆卸后PCB上可供印锡的空间很小,一般情况下,在如此狭小的空间内很难保证锡膏印刷质量的。为了提高印锡质量,通常我们在QFN器件焊盘上印锡。印锡需要制作支撑工装和印锡小钢片,如图7所示。钢片开口根据QFN的焊盘专门开孔设计,开口大于QFN焊盘开孔的1.2倍即可,厚度根据间距不同,一般可取0.08~0.15mm即可,具体厚度可依据IPC-7525标准。通过计算面积比和宽厚比来确定,以保证印刷后的脱模效果。钢片的加工建议使用激光切割加电抛光处理,开孔截面采用下宽上窄的梯形,以利于锡膏脱模。
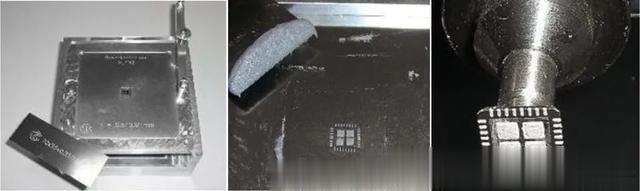
图7 QFN印锡
8、CPUSOCKET返修
CPU SOCKET返修的难点在返修过程中PCB变形较大,通常是向下变形,如图8所示。加之CPU SOCKET尺寸大,超过50mm,所以经常会出现虚焊。
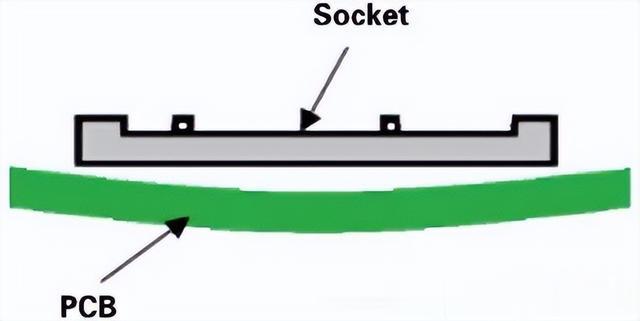
图8 CPU SOCKET单板变形示意图
通过测量CPU SOCKET位置PCB板SOCKET内外侧区域的平面度,测试数据如图9所示。可知返修的CPU1区变形较大,平面度实测0.193mm,正常焊接的CPU2区变形较小,平面度实测0.056mm。
9、总结
PCBA返修前一定要正确预热单板,同时随着PCBA组装密度越来越高,器件组装越来越精密,需要考虑自动或半自动返修方法[6]。传统的手持热风枪或烙铁来加热PCBA是不可控的工艺。因为不知道会对电路板、焊点和焊点周围的东西造成什么损坏。希望更多使用受控制的工艺方法,设定合适的温度曲线,这样就能够知道返修对PCBA其他部分的影响,以及对电路板的可靠性会产生哪些不利影响。总之,采用自动和半自动返修方法,过程严格遵循IPC-7711/7721标准中的返修程序,并完成相关测试和检验步骤,才能达到PCBA的可靠返修。

图9 CPU SOCKER平面度
