0引言
河沙的大量采集不仅破坏河流生态环境,还会导致天然河沙资源日益匮乏。而机制砂原料分布广泛、资源丰富,其使用降低了水泥混凝土工程成本,并且广西东部地区有着丰富的花岗岩,如果将其生产为机制砂,能极大地降低工程成本。然而,花岗岩机制砂的石粉含量、用水量、压碎值较大,颗粒粗糙、级配较差,因此,掺入花岗岩机制砂往往会降低混凝土的工作性能、力学性能及耐久性。许多学者研究发现,机制砂混凝土的力学性能与材料用量密切相关。基于此,为确定机制砂混凝土配合比的最佳设计参数,众多学者均对机制砂混凝土进行配合比设计优化,并证明其力学性能、工作性以及耐久性均满足设计要求。因此,花岗岩机制砂混凝土配合比设计在水胶比、砂率、石粉含量、外加剂掺量以及集料级配等方面都有一些特殊要求。为提高花岗岩机制砂混凝土的各项性能,应从原材料用量和材料设计参数出发,设计并优化花岗岩机制砂混凝土的配合比。
目前,国内外学者对机制砂的力学性能、工作性能及耐久性能的研究取得了一定成果,但对花岗岩混凝土配合比设计优化研究鲜有报道。为改善花岗岩机制砂混凝土的力学综合性能及耐久性,本文将采用正交试验方法,探究各因素与花岗岩机制砂混凝土工作性及力学性能的显著性影响程度,提出花岗岩机制砂路面混凝土的最优配合比。
1原材料及试验方法
1.1原材料
1. 1.1水泥
所用水泥为广西华润红水河牌水泥,其技术指标见表1。
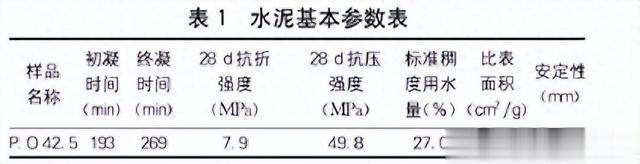
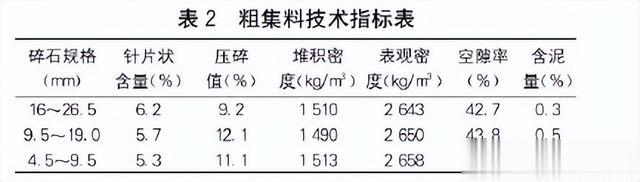
1. 1. 2 集料
粗集料为花岗岩碎石,技术指标见表2。细集料采用细度模数为2.823、石粉含量为3.6%、堆积密度为1545kg/m²、堆积空隙率为42.8%、表观密度为2702kg/m²以及压碎值为19%的花岗岩。
1. 1.3外加剂
外加剂是减水率为15%的WYF-H缓凝高效型减水剂,具体技术指标见表3。

1.2试验方案设计
将胶凝材料用量(A)、水胶比(B)、粉煤灰掺量(C)及砂率(D)作为影响因素,各因素水平见表4。试验采用正交表L16(44),安排16组试验组合。选用落度、抗弯拉强度、抗压强度和劈裂抗拉强度4个指标,对花岗岩机制砂混凝土配合比进行优化设计。

1. 3试验方法
为确保水泥混凝土路面具有良好的长期服役性能,混凝土拌和物在浇筑成型过程中应具有良好的工作性,且尽量避免泌水和离析,凝结硬化后花岗岩机制砂路面混凝土也必须具备足够的抗拉及抗压强度。基于此,本研究选用落度、抗弯拉强度、抗压强度和劈裂抗拉强度4个指标,对花岗岩机制砂混凝土配合比进行优化设计。花岗岩机制砂路面混凝土工作性能及力学性能的测试方法见表5。
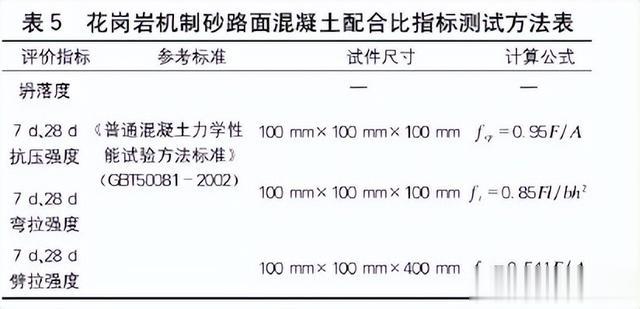
2试验结果及分析
2.1落度测试结果
花岗岩机制砂混凝土正交试验测试结果见表6,落度极差分析结果见表7。

由表6、表7可知:
(1)水胶比是影响花岗岩机制砂路面混凝土工作性能的主要因素,随水胶比的增大,试件落度逐渐增大。这是由于水胶比越大,胶凝体系中的自由浆体越多,集料间的摩擦阻力越小,从而使得拌和物落度减小。
(2)对于花岗岩机制砂路面混凝土落度而言,各因素的影响显著性主次顺序为水胶比>胶凝材料用量>砂率>粉煤灰掺量。其中砂率对应的极差小于水灰比对应的极差,但与粉煤灰掺量对应的极差相近,说明砂率对落度具有一定的影响,掺入粉煤灰可以改善花岗岩机制砂混凝土的落度。
(3)胶凝材料用量的极差大于粉煤灰掺量的极差,且具有同一最优水平分别为A和C4,说明随着胶凝材料用量及粉煤灰掺量的增加,花岗岩机制砂路面混凝土落度逐渐增大。此外水胶比及砂率的最佳水平为B,和D1,最优组合为AB,C4D1。
2.2力学性能测试结果
2.2.1抗弯拉强度
路面混凝土抗弯拉强度极差分析结果见下页表8。
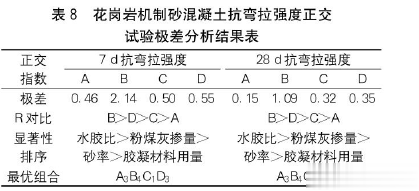
根据表8可知,花岗岩机制砂路面混凝土7d、28d抗弯拉强度影响因素顺序依次为:水胶比砂率粉煤灰掺量>胶凝材料用量,即水胶比对混凝土抗弯拉强度的影响最大,并且各因素的影响程度随龄期的增大逐渐减小。此外,在28d龄期内,水胶比对应的极差远大于粉煤灰掺量、砂率及胶凝材料用量所对应的极差,且在服役期间,花岗岩机制砂混凝土路面板主要受弯拉荷载,因此主要考虑28d抗弯拉强度最佳的各因素组合为A.BC,D3。
2.2.2抗压强度
花岗岩机制砂混凝土抗压强度极差分析结果见表9,各因素不同水平下抗弯拉强度平均值如图1所示。
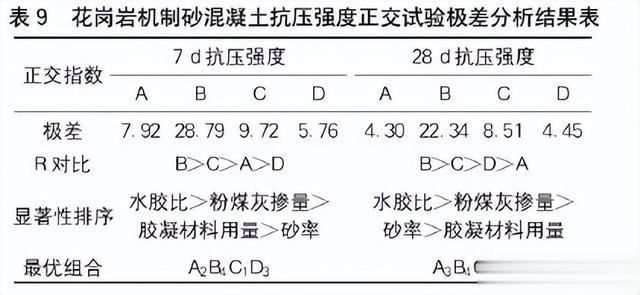
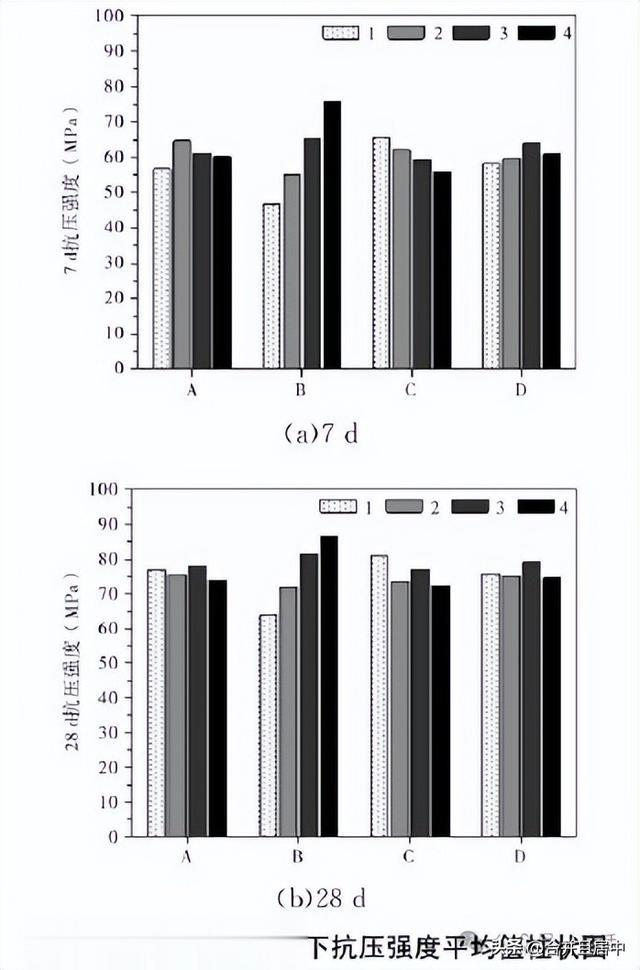
由表9可知,水胶比对花岗岩机制砂混凝土7d及28d抗压强度的影响最大,砂率对花岗岩机制砂混凝土7抗压强度的影响最小;水胶比对花岗岩机制砂混凝土28抗压强度的影响最大,胶凝材料用量及砂率对花岗岩机制砂混凝土28d抗压强度的影响最小。因此,砂率对抗压强度的影响最小,水胶比对抗压强度的影响最大,并且抗压强度随着水胶比的减小而逐渐增大。此外,在7d时,水胶比对应的极差远大于粉煤灰掺量、砂率及胶凝材料用量所对应的极差,且后三者之间同样相差明显;由于花岗岩机制砂的石粉活性较低,早期混凝土的抗压强度会受到一定的影响,因此28d时各因素所对应的极差会减小;粉煤灰掺量过大不利于混凝土抗压强度的形成,各因素对花岗岩机制砂混凝土前期抗压强度形成的影响更为显著。基于混凝土早期抗压强度满足设计要求,得出抗压强度各因素的最佳组合为A,B4C,D3。
由图1可知,随着水胶比的增大花岗岩机制砂路面混凝土7d、28d抗压强度不断下降;花岗岩机制砂路面混凝土7d、28d抗压强度随着砂率及胶凝材料用量呈先增大后减小的趋势;粉煤灰掺量的增大会降低花岗岩机制砂路面混凝土的7d抗压强度。可见,各因素对花岗岩机制砂混凝土各龄期抗压强度的影响规律与抗弯拉强度基本相同。
2.2.3劈裂强度
花岗岩机制砂抗劈拉强度极差分析结果见表10,各因素不同水平下抗劈拉强度平均值如图2所示。
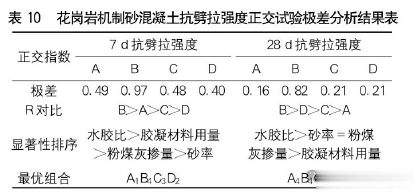
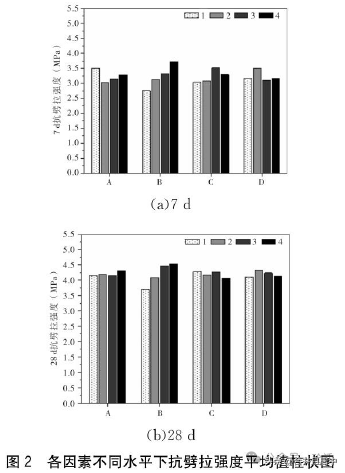
由表10可以发现,花岗岩机制砂路面混凝土7d抗劈拉强度影响因素的主次顺序为:水胶比胶凝材料用量>粉煤灰掺量>砂率,而28d抗劈拉强度影响因素的主次顺序为:水胶比>砂率=粉煤灰掺量>胶凝材料用量,说明水胶比对抗劈拉强度的影响最大。
由图2可知:(1)花岗岩机制砂路面混凝土7d、28d抗劈拉强度随水胶比的增大而降低,这一趋势在后期逐渐减小,但相比于抗弯拉强度其变化幅度较小;(2)花岗岩机制砂路面混凝土7d、28d抗劈拉强度随胶凝材料用量增加呈逐渐增大的趋势;(3)随着粉煤灰掺量的增大,花岗岩机制砂路面混凝土7d抗劈拉强度先增大后减小,但总体变化幅度不大;(4)随着砂率的增大,花岗岩机制砂路面混凝土7d、28d抗劈拉强度先增大后减小,即砂率存在最佳值。
3最优配合比确定
本文选取重载交通作用下的高等级公路水泥路面混凝土作为研究对象,综合考虑了花岗岩机制砂路面混凝土的落度、7d及28d抗弯拉强度、7d及28d抗压强度、7d及28d抗劈拉强度,对花岗岩机制砂路面混凝土的最佳水平组合进行决策,进而确定最优配合比,使得混凝土拌和物在浇筑成型过程中满足施工和易性的要求,凝结硬化后具备足够的抗弯拉强度抵抗行车荷载,并使混凝土内部结构更稳定密实,耐久性更好。经正交试验得出的花岗岩机制砂路面混凝土各项性能对应的各因素最佳水平如表11所示。
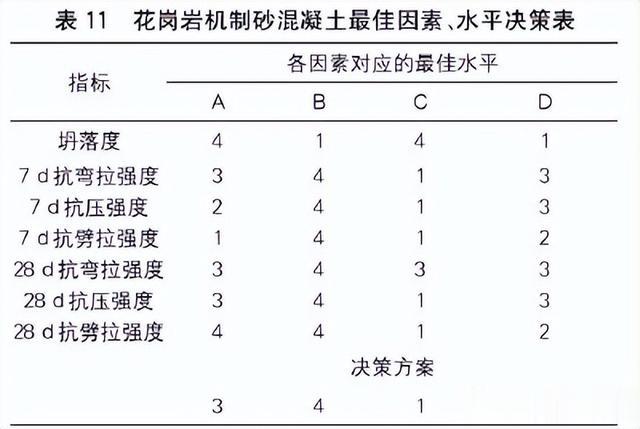
由表11可知,胶凝材料用量为380kg/m²、水胶比为0.34时混凝土的28d抗弯拉强度、7d及28d抗压强度最大。因此确定胶凝材料用量为380kg/m²,水胶比为0.34。
砂率在45%时混凝土落度抗弯拉强度达到最大,1234 但砂率在43%时混凝土7d、28d抗压强度、抗压强度达到最大值,并且考虑到砂率并不是抗弯拉强度的最显著影响因素,因此确定砂率为43%。
粉煤灰掺量是7抗劈拉强度、28d抗弯拉强度的最显著影响因素,并且粉煤灰掺量为10%时,机制砂路面混凝土的各项指标均达到最优,因此确定粉煤灰掺量为10%。基于此,确定花岗岩机制砂路面混凝土最优配合比如表12所示。
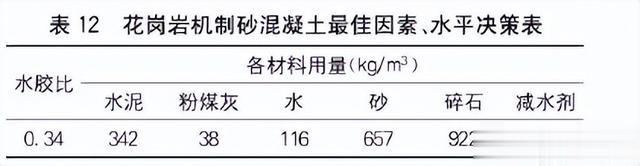
4结语
(1)路面混凝土工作性能评价主要基于落度而定,落度主要影响因素为水胶比,其次为胶凝材料用量及砂率,粉煤灰掺量的影响相对最小,砂率在一定范围内可以改善混凝土的落度。
(2)随着砂率的增大,花岗岩机制砂路面混凝土7d、28d抗弯拉强度呈先增大后减小的趋势,并且在41%时达到最佳值。砂率越高抗弯拉强度的发展越慢,过大的砂率对前期抗弯拉强度的形成不利。
(3)水胶比对花岗岩机制砂路面混凝土抗弯拉强度、抗压及劈裂抗拉强度的影响较大,其次为粉煤灰掺量、砂率和胶凝材料掺量。