汽轮发电机组通流部分零胀差实现方案研究
刘建生
摘 要:由于汽轮机胀差的存在,通流部分轴向间隙较大,在汽轮机各级之间造成了较大的汽流涡流、回流损失,本文对汽轮机级内、级间损失的产生机理进行了分析,提出了汽轮机汽缸和转子的零胀差设计理念,并提出了汽轮机轴系及缸体的参考改进方案,通过该项设计能够在一定程度上提高机组运行效率,为汽轮机的设计制造和电力企业的设备选择提供了一定的借鉴。
关键词:汽轮发电机组;通流部分;轴向间隙;零胀差;改进方案;研究

Research On The Scheme Of Zero Expansion Difference In The Flow Passage Of Steam Turbine Generator Set
Liujiansheng
随着国内工业经济的进步,汽轮发电机组向着大容量、高参数的方向迅速发展,目前600MW,1000MW机组迅速发展,并成为当前主流发电机组。在汽轮发电机组容量增大的同时,汽轮机的缸体由双缸变为三缸,甚至扩展为四缸,机组轴系也在不断加长,大容量汽轮发电机组轴系超过35 m,有的甚至超过40 m。轴系长度的增加不但对设备的制造和安装质量提出了更高的要求,也使机组在启停和运行中的轴系膨胀更加难以在运行中控制,给机组轴系的运行和维护提出了更高的要求。
本文就当前流行的600MW、1000MW汽轮发电机组结构进行介绍,对汽轮机缸体、轴系的结构进行分析,就减小通流部分轴向间隙,进一步提高机组运行效率进行研究分析,提出汽轮机通流部分动静结构之间零胀差的理念,研究汽轮机零胀差实施方案,减小汽轮机的级内和级间损失,为汽轮发电机组的设计和制造提供新的思路,旨在进一步提高汽轮机发电组的运行经济性。
1 汽轮发电机组结构
按机组容量和制造厂家的不同,国内汽轮发电机组的结构形式有着一定的差别,现以1000MW机组为例进行说明。目前1000MW汽轮发电机组的典型布置一般为单轴四缸四排汽设计,从机头到机尾依次串联,1个单流高压缸、1个双流中压缸及2个双流低压缸。汽轮发电机组轴系总长达50多m,汽轮机长度超过35m。图1为国内某制造厂生产的1000MW汽轮机组结构示意图。
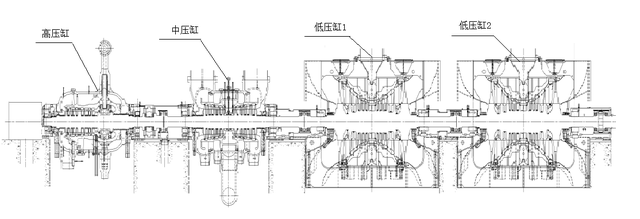
图1 某制造厂生产的1000MW汽轮机组结构示意图
1.1 汽轮机组汽缸及轴系布置
按机组轴系和缸体膨胀设计的不同,目前国内安装的1000MW汽轮机组布置主要有以下两种形式:
(1)该结构汽轮机机组转子共有汽轮机高压缸、中压缸、低压一缸、低压二缸4根转子组成,通过靠背轮进行连接,机组的推力轴承位于高中压缸之间的#2轴承箱位置,因此机组轴系以#2轴承推力轴承为死点向两侧膨胀;汽轮机高压缸、中压缸和低压缸分别有自己的死点位置,国内哈汽、东汽设计的1000MW机组都采用此种布置方式。尽管高压缸侧转子和气缸温度较高,启停中温差变化较大,但由于轴系较短,因此热膨胀的影响并不明显;但由于低压转子位于汽轮机转子的末端,膨胀伸长较大[1],因此位于后部的2个低压缸在启停过程中热膨胀影响最大,对轴系、缸体胀差需要进行严密的监视。
(2)该结构的汽轮机组结构设计较为特殊,汽轮机缸体和第一种布置方式相同,机组的推力轴承也位于高中压缸之间的#2轴承箱位置,但机组的汽缸并未设计死点,因此4个汽缸在机组启停机运行中均处于自由状态,汽缸膨胀靠缸体和台板的滑动来完成,由于这种布置结构转子和汽缸缸体可以一起进行膨胀和收缩,汽轮机轴系和缸体的胀差更易于控制。目前上汽1000MW机组就采用这种布置方式。
1.2 两种布置方式的优缺点
当汽轮机启动加热或停止运行冷却以及负荷发生变化时,汽缸和转子都会产生热膨胀或冷却收缩。由于转子受热表面积比汽缸大,且转子的质量比相对应的汽缸小,蒸汽对转子表面的放热系数较大。因此,在相同条件下,转子的温度变化比汽缸快,转子与汽缸之间存在膨胀差,而这个差值是指转子相对于汽缸而言,故称为相对膨胀差(即胀差)[2]。 对于上述两种结构方式,在机组启停过程中汽轮机的胀差是始终存在的。
对于第一种布置方式,由于各汽缸缸体均有膨胀死点,汽缸缸体在机组进汽受热时向两侧膨胀,但转子以#2轴承向两侧膨胀,就会造成位于后部的低压缸在启动受热过程中前部动静部分的间隙越来越小,后部趋于增大,为满足启停要求,机组进汽控制变得更为复杂。在机组启停中要对汽轮机暖机和升速率加强控制,对各汽缸尤其是低压缸的胀差参数进行严密监视,防止产生动静碰磨事故[3]。
但对于第二种布置方式,由于各汽缸缸体未设置死点,汽缸的膨胀较为灵活,在机组启动进汽时,转子和汽缸均以#2轴承为死点向两侧受热膨胀,汽轮机中压缸、低压缸缸体受到连接支撑的作用,和转子的膨胀方向相同,但由于启动中汽缸的膨胀慢于转子,因此最小的动静间隙位于低压缸的后部,只要在设计中留有足够的动静间隙,就能避免动静碰磨事故。该种布置方式的安全性和缸体底部的滑动支撑台板有关,如果在机组启停中台板滑动不畅,就会造成膨胀受阻,影响机组的安全运行。
2 汽轮机组结构存在的问题
经过几十年的发展,汽轮机的设计理念已由原有的手动数值计算转变为全三维甚至是全四维模拟设计[4],计算流体力学(CFD)的成熟和现代设计手段的增强,不但加快了大型汽轮发电机组的设计速度,也大幅提高了汽轮机发电组的运行效率。
由于汽轮机轴系和缸体之间胀差的存在,造成了机组动静间隙在设计中预留较大,容易造成较大的叶型损失和涡流损失。为了避免汽轮机启停过程中动静碰磨事故的发生,在汽轮机通流部分的设计中主要考虑了叶型的优化,采用前加载或后加载来优化动静叶流道,但未对轴向部分进行相应的完善,造成了轴向间隙偏大,如图2所示。
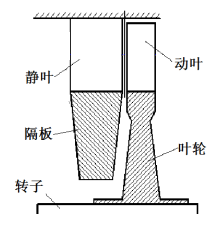
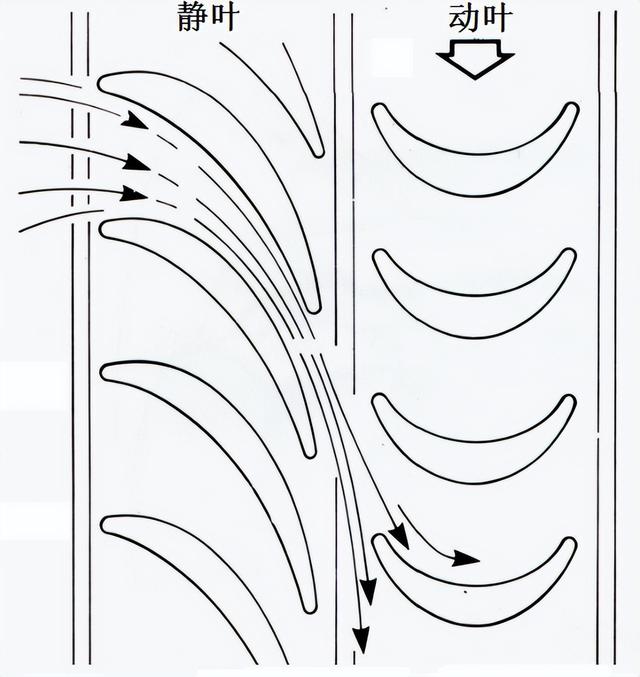
图2 汽轮机冲动式叶轮通流示意图
从图2可以看出,蒸汽由汽轮机静叶进入,经过静叶的流道整流、导向并加速后用于冲动汽轮机的动叶,动叶在汽流的冲动作用下旋转做功。
如果动静叶之间的间隙过大,就会造成在蒸汽高速流出静叶后无法顺利进入动叶做功,而是在静叶尾部和动叶端部之间形成明显的涡流和回流,产生较大的二次流损失,过热蒸汽的动力特性被大幅削弱。如图3所示,由于汽轮机动静轴向间隙A过大,会在静叶出口和动叶入口之间形成扰流,一般来说间隙越大,造成的涡流和回流损失也就越大。同样,对于静叶与转子之间间隙、动叶顶部间隙过大,也会造成蒸汽沿间隙回流,造成一定的扰流和倒流损失[5]。
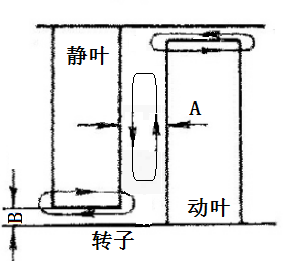
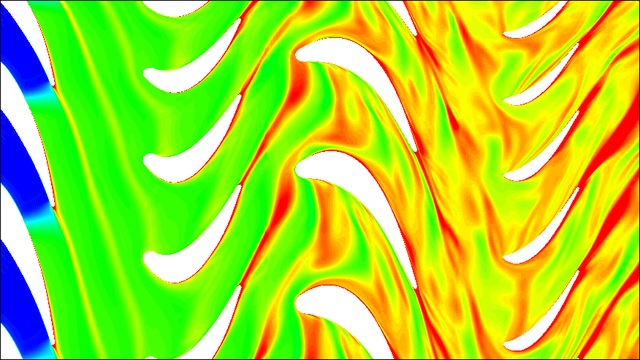
图3汽轮机级内扰流示意图
通过缩小汽轮机通流部分级内和级间的轴向间隙能够降低涡流、回流损失,减小动静叶的叶型和尾迹损失,能有效提高汽轮机的运行效率。汽轮机轴向间隙优化主要受限于汽轮机轴系和缸体之间的膨胀,对于前述第一种1000MW汽轮机布置方案来说,汽轮机第一、二低压缸冷态动静部分的轴向间隙要达到40~50mm,在热态运行中间隙也会在20~25mm左右(具体数值可以通过现场实测或有限元模拟方法得到),造成低压缸内部各级轴向间隙过大,通流部分运行效率受到较大影响。对于第二种布置方案而言,由于汽轮机轴系和缸体同方向膨胀,低压缸轴向间隙要小些,但也在20~30mm左右。
通过减小汽轮机轴系和缸体胀差可以有效减小或消除通流部分轴向间隙,满足汽轮机启停的顺利进行,并能够进一步提高汽轮机通流部分的运行效率[6]。
3 零胀差结构实现方法
传统方式设计的汽轮机轴系和缸体考虑了转子轴系扭矩很大、缸体笨重等因素,一直以来并未对轴系和缸体胀差进行相应的优化处理。在当前液压控制系统快速发展、轴系靠背轮离合装置得到较多应用、技术更为成熟可靠的条件下,使汽轮机通流部分轴向间隙的优化成为可能。
3.1 移动缸体方案
在不改变汽轮机转子的情况下,通过移动汽轮机各汽缸的缸体可以有效减小或消除汽轮机胀差。600MW、1000MW大型汽轮机的高、中、低压缸缸体重达上百吨,推动汽缸必须要对汽缸底部台板加装润滑装置,如前述第二种布置方案即采用滑动缸体来达到受热膨胀的要求。为了精确地移动汽缸缸体,可以采用可靠的液压伺服系统作为驱动动力,在汽缸的中部或两侧设计推拉机构。缸体推拉机构在机组启停及运行中实时跟踪转子位置的变化,并根据转子的位置对汽缸进行调整,使转子始终位于汽缸中部,保证通流部分的轴向间隙始终处于较小的间隙。通流部分动静间隙变小后,可以减小涡流和回流损失,有效提高机组运行效率。
3.2 移动转子方案
在不改变汽轮机缸体位置的情况下,通过实施改变转子的位置来实现减小或消除汽轮机胀差的目的。在汽轮机启动过程中,汽轮机转子和汽缸受热膨胀,高、中、低压转子之间的胀差通过调整靠背轮的长度来补偿,这就需要在靠背轮设置相应的液压调节装置,通过靠背轮之间的离合消除轴系和各汽缸缸体之间的位置差。但汽轮机转子靠背轮除用来连接轴系外,还要用来传递扭矩,在现有技术条件下实现转子间的轴向移动有较大的难度。
3.3 两种方案的优缺点
综上所述,移动汽轮机缸体方案较为容易实现。虽然汽轮机的缸体较为笨重,但汽轮机缸体底部和台板之间均安装有润滑装置,当前的先进的液压系统能够产生较大的推力和拉力,因此设计可靠的液压伺服系统足以满足缸体轴向移动的需要。和汽轮机调节汽门控制类似,采用液压伺服系统即可精确控制和实时调整汽缸缸体的位置,其动态响应特性也能够满足汽轮机的启停和运行要求。
4 结语
十三五期间,我国将继续推行能源优化和节能减排工作,国内汽轮机组还将继续向着大容量、高参数、低能耗发展,600MW、1000MW汽轮发电机组已经逐步成为主流发电机组。目前机组在设计制造中引进和借鉴了国外的先进设计经验,采用全三维、全四维设计理念,实施了多项通流优化措施,使机组效率得到了大幅提高,汽轮机节能改造更多地考虑了径向汽封间隙的调整,但级内和级间轴向间隙优化经验相对较少。本文就汽轮机通流部分的轴向间隙对级内和级间损失的影响进行了分析和研究,指出了轴向间隙过大将产生较大的回流、涡流损失,影响机组运行的经济性。通过对汽轮机结构的研究分析提出了相应的轴系、汽缸缸体的零胀差设计优化方案,利用液压系统实现汽缸和转子的同步膨胀,能够提高汽轮机在启停和运行中的安全性和经济性,为汽轮发电机组的设计和制造以及使用单位的选择提供了一定的借鉴。
参考文献
[1]何洪流,汽轮发电机低压缸胀差大原因分析及处理[J]. 贵州电力技术,2015,18(7):17-19.
[2]单以建,李新军. 某中间再热机组低压缸胀差偏大原因的分析及处理[J]. 热力透平, 2008, 37(2): 132-134.
[3]何健康,黄志强,周福宏,等. 韶关发电厂9号汽轮机低压缸胀差大的原因分析和处理[J].汽轮机技术,2000, 42(5): 307-310.
[4]邓志成. 超临界汽轮机轴向动静间隙有限元分析研究[D]. 上海:上海交通大学, 2013.
[5]张艾萍,暴丽,叶荣学. 汽轮机动静间隙对经济性与安全性的影响[J].汽轮机技术,2003,45(1): 23-24.
[6]史德坤. 缩小汽轮机动静叶间隙,提高热效率[J].中国电力,1959(24):60.
作者简历:
刘建生(1976-),男,本科,高级工程师,主要从事汽轮机、燃气-蒸汽联合循环机组的设备管理工作。E-mail: 1170852860@qq.com