悬空打线工艺在 MEMS 芯片固定中的应用分析
张晋雷
(华芯拓远(天津)科技有限公司)
摘要:
为解决 MEMS 加速度传感器芯片贴装过程中的外部应力变化对芯片内部结构产生的消极影响,研究提出了微机械硅芯片悬空打线工艺,对加速度传感器芯片进行固定封装,并运用有限元仿真分析软件,以加速度传感器的动力输出参数为量化指标,对比分析传统黏合剂粘贴封装和悬空打线封装的实施效果。研究结果表明,悬空打线工艺可避免外部应力变化对 MEMS 芯片内部结构产生的消极影响,确保了 MEMS 芯片全温环境下的参数稳定;随着模态阶数的增加,封装前后不同封装方式的加速度传感器的固有频率均呈现非线性增加,前 4 阶封装前后的加速度传感器固有频率相近,而后 6 阶中采用悬空打线工艺封装的加速度传感器芯片固有频率明显大于采用传统黏合剂粘贴封装的加速度传感器固有频率,且前者与封装前的加速度传感器芯片固有频率较接近;封装前加速度传感器芯片的滤波前信号呈现剧烈的波动,经过滤波后的信号更加平滑,对信号的还原度更好,采用悬空打线工艺封装加速度传感器芯片的输出,其滤波前后的信号变化规律与封装前的信号变化规律较为一致,对于采用传统黏合剂粘贴封装的加速度传感器芯片输出信号呈现不同程度的失真。
引言
MEMS 芯片尺寸小巧精密,其工作性能极易受到安装工艺和环境的影响,在传统的黏合剂固定粘贴MEMS 芯片时,需要再芯片上涂抹黏合剂,黏合剂的厚度和弹性模量成为影响硅片应力和变形的重要因素 [1] 。为了使得 MEMS 芯片与陶瓷管壳之间的黏合弹性模量接近于零,本文提出了一种新型的芯片固定贴装工艺,并运用有限元仿真分析软件,以加速度传感器的动力输出参数为量化指标,对比分析传统黏合剂粘贴封装和悬空打线封装的实施效果 [2] 。研究成果可为 MEMS芯片的高质量固定安装提供参考。
1 微机电系统芯片悬空打线工艺
微机械硅芯片与基板的连接是高精度 MEMS(微机电系统)加速度计封装中最关键的步骤之一。由于不同材料之间的 TCE(热膨胀系数)不匹配,导致芯片贴装过程中引起的应力和应变对加速度计传感器的输出特性产生不利影响,其中,弹性模量和黏合剂的厚度是影响硅片应力和变形的最重要因素 [3] 。软胶材料具有更好的应力吸收能力,随着胶层厚度的增加,硅片的应力和变形减小。因此,需要在 MEMS 加速度计的芯片贴装封装中使用柔软而厚实的黏合剂,弹性模量越低越好,理想状态下弹性模量为零 [4-5] 。
本研究提出了一种新型的芯片固定贴装工艺,即悬空打线工艺。如图 1 所示,通过悬空打线工装将MEMS 芯片固定于管壳中,管壳设置为陶瓷管壳,这是因为陶瓷具有较高的绝缘性能和优异的高频特性,其线性膨胀系数与电子元器件非常接近,化学性能稳定且热导率高,随后,对 MEMS 芯片进行打线,使得MEMS 芯片通过金属线与管壳连接,金属线可以为金线或者铜线,采用金线时其径向尺寸为 25 μm,采用铜线时其径向尺寸为 50 μm,伸长量为 0.1 μm,完成打线之后通过外部的 PLC 控制器控制悬空打线工装向上移动脱离 MEMS芯片,此时 MEMS 芯片受到金属线自身的张力脱离管壳的内壁底部向上微微抬起,使得 MEMS 芯片底部与管壳留有间隙呈悬空状;随后,采用黏度值为 14 500 cp 的胶水于 MEMS 芯片与金属线连接所在表面进行涂覆形成防护层,满足固化条件后,对防护层进行固化,涂覆厚度覆盖 MEMS 芯片与金属线连接处的焊点 [6-7] 。具体而言,传统未涂覆有防护胶的 MEMS 芯片而言其平均加速度 G 值为12,经过涂覆防护胶之后的 MEMS 芯片的平均加速度G 值能达到 600,防护胶选用硬度值为 14 500 PA·s的绝缘硅橡胶,固化条件为 150 ℃的温度环境,固化1 h,将防护层固化完成后将管壳转移至真空炉中进行封盖处理,进行封盖处理的同时对管壳的腔室进行抽真空操作,使得 MEMS 芯片与管壳之间的相对位置关系固定下来,确保了 MEMS 芯片在有限的范围内浮动,避免了产品转移过程上下轻微浮动范围过大可能对产品造成的损害或金属线焊点处出现断裂的情况。该新型工艺结构简单、便于操作,实现了弹性模量为零的悬空打线过程,避免外部应力变化对 MEMS 芯片内部结构产生的消极影响,确保了 MEMS 芯片全温环境下的参数稳定。

该新工艺中提出的悬空打线工装如图 2 所示。由于 MEMS 芯片尺寸小巧精密(6 纳米级),对精度要求高,悬空打线工装通过设置包含弹性件、压紧块、定位柱在内的缓冲机构实现对 MEMS 芯片压紧固定,同时也避免了工装刚性压紧固定可能对 MEMS 芯片表面压紧过度容易损坏芯片问题的出现;悬空打线工装通过设置一字槽有效限制了压紧块前后移动的空间,由于一字槽两侧均开设有圆孔,圆孔内穿设有轴销,压紧块面向 MEMS 芯片的一侧开设有定位槽,定位槽与轴销相互配合能够限制压紧块水平方向晃动,从而避免了压紧块回复到初始位置时容易左右晃动的问题,进一步提高了压紧块压紧固定 MEMS 芯片时的稳定性能。
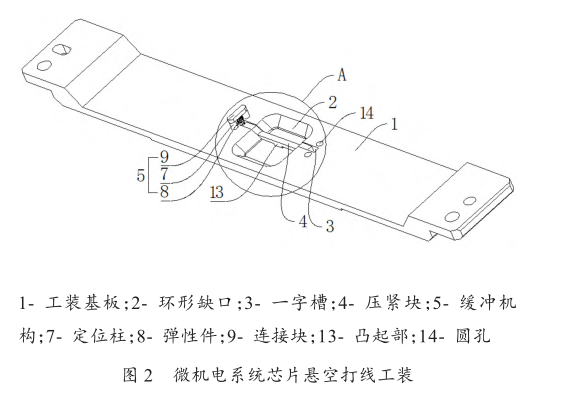
2 基于悬空打线工艺的加速度传感器输出性能分析
为了研究悬空打线工艺在芯片固定中的应用效果,借助有限元仿真分析软件 ANSYS 程序,建立了有限元分析模型,研究悬空打线工艺对加速度传感器输出型号的影响。计算时,高致密氧化铝陶瓷管壳的弹性模量为 296 GPa,泊松比为 0.28,密度为 3.97g/cm 3 ;加速度传感器芯片的弹性模量为 131 GPa,泊松比为 0.28,密度为 2.33 g/cm 3 ;绝缘硅橡胶的弹性模量为 0.1 GPa,泊松比为 0.30,密度为 1.80 g/cm 3[8] 。计算模型采用 8 节点 Solid45 进行网格划分,共计得到网格数量为 1 086 个,节点数量为 2 027 个。
图 3 和表 1 为封装前后微机电系统加速度传感器芯片不同封装方式前 10 阶的固有频率计算结果。从图 3 中可以看出,随着模态阶数的增加,封装前后不同封装方式的加速度传感器的固有频率均呈现非线性增加,采用悬空打线工艺封装的加速度传感器性芯片固有频率增速较快,而采用传统黏合剂粘贴封装的加速度传感器芯片固有频率增速较慢,3 者的前 4阶固有频率相近,而后 6 阶中采用悬空打线工艺封装的加速度传感器芯片固有频率明显大于采用传统黏合剂粘贴封装的加速度传感器固有频率,且前者与封装前的加速度传感器芯片固有频率较接近。传统黏合剂粘贴封装的加速度传感器芯片在高振动模态的低固有频率会导致芯片产生各种振动和扭曲,进而导致加速度传感器芯片的输出信号失真。
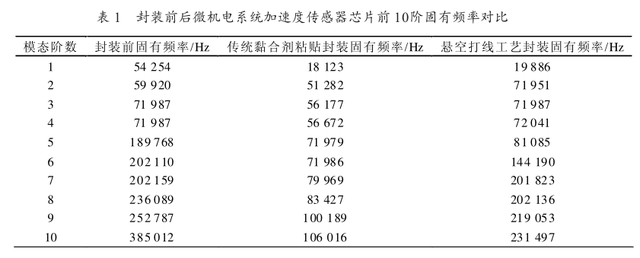
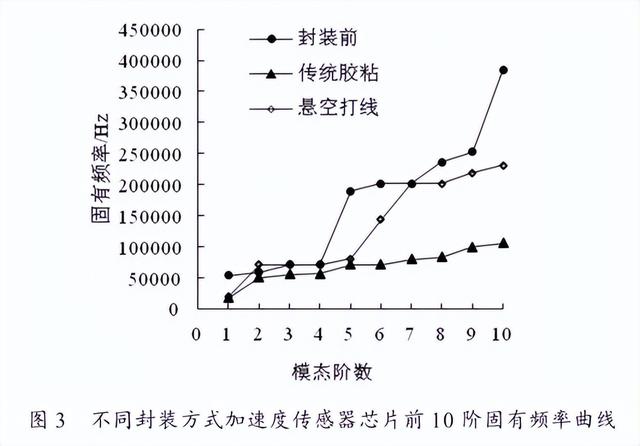
对封装前后的加速度传感器芯片施加矩形脉冲,矩形脉冲的周期为200 μs,0 μs~86 μs的持续加载速度为100 m/s 2 ,86 μs~200μs 的持续加载速度为 0 m/s 2 ,如图 4 所示。以传感器的振动位移为输出参量,采用傅里叶变换进行频率滤波,对比滤波前后的波形,结果如图 5~ 图 6 所示。

从图 5 中可以看出,封装前的加速度传感器芯片滤波前信号呈现剧烈的波动,在 0 μs~86 μs 的平均输出为 - 7.86 μm,在 86 μs~200 μs 的平均输出为0,表明输出响应与输出较为一致,经过滤波后的信号更加平滑,对信号的还原度更好,0 μs~86 μs 的平均输出为 - 7.86 μm,在 86 μs~200 μs 的平均输出为 0,能够真实反应输入信号。如图 6 所示,对于采用传统黏合剂粘贴封装加速度传感器芯片的输出,滤波前信号呈现剧烈的波动,0 μs~86 μs 的平均输出为- 7.23 μm,在 86 μs~200 μs 的平均输出为 0,信号呈现不同程度的失真,这主要原因是因为在粘贴过程中胶层的厚度不易控制,导致其涂抹厚度较小,这也是传统黏合剂粘贴封装最大的缺点,滤波后的信号平滑效果较差,对信号的还原度明显变差;如图 7 所示,对于采用悬空打线工艺封装加速度传感器芯片的输出,其滤波前后的信号变化规律与未封装前的信号变化规律较为一致,滤波作用可以对信号起到较好的平滑效果,输出型号能反映真实的信号特征,0 μs~86μs 的平均输出为 - 7.48 μm,在 86 μs~200 μs 的平均输出为 0。


3 结论
基于提出微机械硅芯片悬空打线工艺,对加速度传感器芯片进行固定封装,并运用有限元仿真分析软件,以加速度传感器的动力输出参数为量化指标,对比分析传统黏合剂粘贴封装和悬空打线封装的实施效果,得到以下几个结论:
(1) 悬空打线工艺是借助工装将 MEMS 芯片固定于管壳中,对 MEMS 芯片进行打线,使得 MEMS 芯片通过金属线与管壳连接;完成打线后将悬空打线工装移走,MEMS 芯片通过金属线与管壳连接且 MEMS芯片底部与管壳留有间隙呈悬空状,避免了外部应力变化对 MEMS 芯片内部结构产生的消极影响,确保了MEMS芯片全温环境下的参数稳定。
(2) 随着模态阶数的增加,封装前后不同封装方式的加速度传感器的固有频率均呈现非线性增加,前 4 阶封装前后的加速度传感器固有频率相近,而后6 阶中采用悬空打线工艺封装的加速度传感器芯片固有频率明显大于采用传统黏合剂粘贴封装的加速度传感器固有频率,且前者与封装前的加速度传感器芯片固有频率较接近。
(3) 封装前加速度传感器芯片的滤波前信号呈现剧烈的波动,经过滤波后的信号更加平滑,对信号的还原度更好,采用悬空打线工艺封装加速度传感器芯片的输出,其滤波前后的信号变化规律与封装前的信号变化规律较为一致,对于采用传统黏合剂粘贴封装的加速度传感器芯片输出信号呈现不同程度的失真。