
纤维金属层压板是一种新型的混合轻质复合材料,由金属基材和纤维增强塑料组成。由于混合结构,FML具有出色的机械性能,包括高比强度和刚度,良好的抗疲劳性和出色的损伤容限。然而,由于金属板和复合层之间的物理性能差异,FML的弱界面结合可能会导致分层和解粘失败。因此,改善FML的层间力学性能至关重要。
为了改善FML的层间力学性能,一系列表面处理方法,如酸或碱蚀刻,阳极氧化,激光烧蚀,硅烷偶联剂处理和大气压等离子体,已经提出对金属板表面形貌进行修饰。
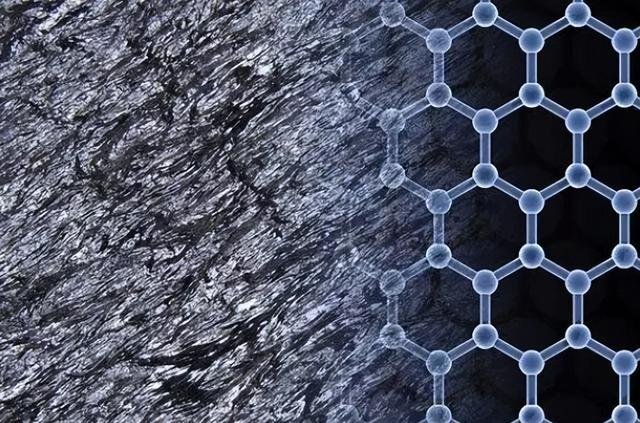
处理步骤:首先,将铝板用丙酮冲洗脱脂,然后在烘箱中干燥以除去水分,将铝板浸入M NaOH溶液中并在环境温度下超声处理30分钟以改变铝板的表面形貌,取出处理过的Al板并在蒸馏水中超声处理,直到铝与NaOH的反应终止,并且将洗涤后的Al板在60°C下干燥1小时。

然后,制备GO增强环氧浆料作为增韧夹层。GO叶间的详细制备过程与我们之前的工作相似。主要步骤包括通过机械混合和超声波振动制备GO/DMF悬浮液,将环氧树脂倒入GO/DMF悬浮液中并通过行星串和超声波混合,加热上述混合物以除去DMF,以及在不断搅拌下加入固化剂。
根据日本工业标准(JIS)K7086,进行了双悬臂梁和端部缺口弯曲测试,以测量GFRP/Al层压板的I型和II型层间断裂韧性。DCB和易恩孚试样的配置如下方图片所示。
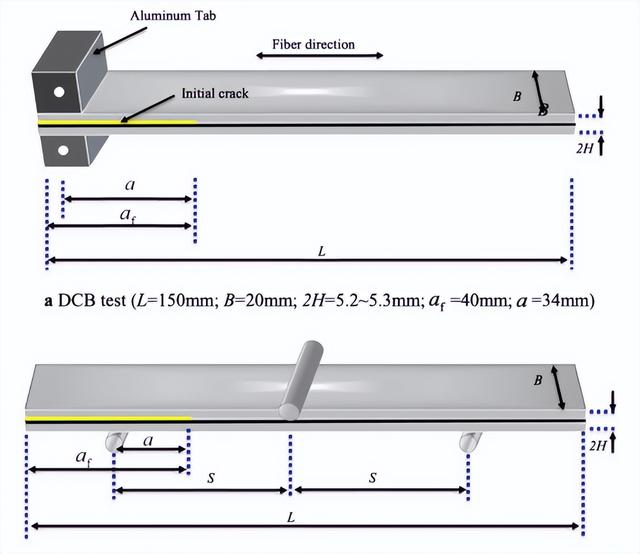
采用扫描电镜对试样的石墨片、GO、铝板和断裂表面的表面形貌进行了表征。同时, 采用透射电子显微镜和原子力显微镜观察了GO片的纳米结构。GO和铝基板的化学结构在ESCALAB 250Xi XPS系统上进行了表征。此外,分别采用光学干涉轮廓仪和接触角测角仪研究了铝板的表面粗糙度和润湿性性能。
GO的特征采用SEM和TEM对石墨和GO薄片的表面形貌进行了表征,可以观察到石墨片的多层结构。而 GO 的 SEM 和 TEM 图像在图中。这表明石墨的多层结构分层,氧化石墨烯已成功合成。制备的GO厚度约为0.968 nm,表明从石墨中完全剥离后实现了单层氧化石墨烯纳米结构。此外,GO的分散状态在聚合物的增韧中起着至关重要的作用。GO的分散性差可能会对从树脂到GO纳米片的应力转变产生不利影响。
因此,需要对分散GO进行表征和评估。在0.5wt%浓度下掺入GO在树脂中表现出良好的分散性,而在较高浓度下可以观察到GO的轻微聚集,这可能导致应力集中,从而削弱环氧树脂的强度和韧性。
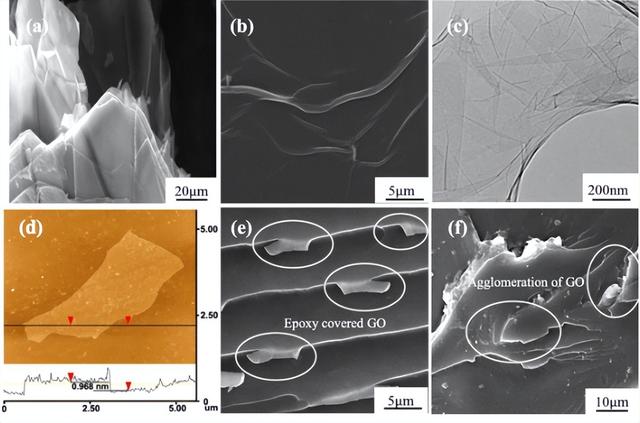
GO表面的化学结构是影响GO在聚合物中增韧效率的另一个重要因素,负责GO与树脂基体之间的界面相互作用。采用X射线光电子能谱(XPS)对所制备的GO的表面化学性质进行了鉴定。GO的C 1s光谱分为四个峰,分配给四种类型的碳键:C–C/C = C ,C–O (286.9 eV),C = O 和O–C = O 。

一般来说,FRP复合材料与金属之间的界面脱粘涉及界面和内聚破坏,这通常受到金属板表面特性的影响。因此,采用各种测量仪器对铝合金表面的表面微观组织、粗糙度、化学成分和润湿性等物理化学性质进行了表征。
可以看出,经碱蚀处理的Al合金表面变得比脱脂Al合金表面更粗糙。在碱蚀处理的铝合金表面可以观察到许多微尺度的孔和谷,这有利于环氧树脂和GO的填充形成机械互锁,增强复合材料/金属界面的结合强度。此外,还使用光学干涉轮廓仪测量了碱蚀刻前后Al合金板的表面轮廓。
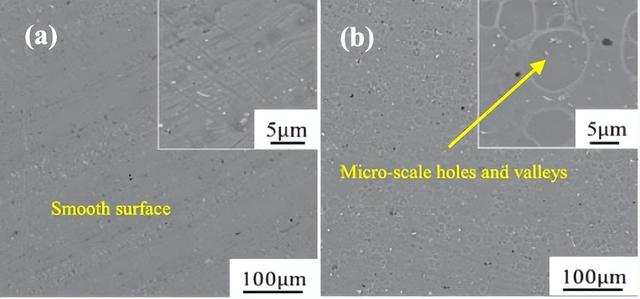
采用XPS分析了不同表面处理下铝合金表面的化学改性。图片显示了未蚀刻和蚀刻的铝合金表面的Al 2p和O 1s的窄扫描光谱。a显示了未蚀刻表面的去卷积Al 2p电离光谱,该光谱只有一个峰,结合能为74.4 eV,对应于γ-铝氧化物。未蚀刻表面的O 1s光谱被分成2个峰,分配给Al2O3分别为和氢氧化铝。
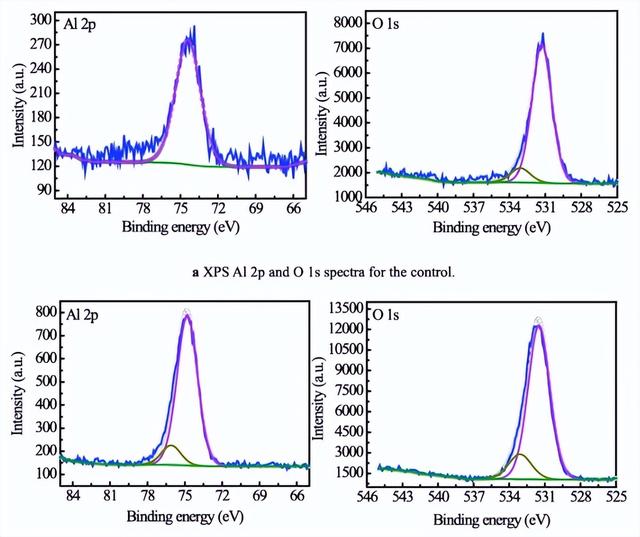
图片显示了蚀刻表面的去卷积Al 2p电离光谱,其中位于74.8 eV处的第一个峰与Al相关2O3,76.1 eV处的峰值对应于氢氧化铝。蚀刻表面的O 1s光谱显示两个峰,一个为Al峰2O3和另一个用于氢氧化铝。比较未蚀刻和蚀刻的Al合金表面的结果,Al 2p结合能的变化意味着Al合金的表面化学性质已因表面处理而改变。
同时,蚀刻表面O 1s峰的氢氧化物与氧化物强度比高于未蚀刻表面,由于氢氧化铝和环氧分子上的羟基之间形成更多的氢键,可以提高界面附着力。

DCB测试对不同类型的GFRP / Al层压板进行了,图片显示了荷载P和裂纹开口位移之间的关系。可以发现,FMLs试件的荷载和裂纹开口位移响应的总体趋势几乎相似,即外加荷载先线性增加,然后以非线性模式略微增加,直至荷载达到最大值,最后阶段逐渐下降。
由于裂纹扩展萌生的不确定性,临界荷载定义为P-COD曲线与一条线的交点,对应于比初始曲线高5%的顺应性。

图片显示了临界载荷PC的测试样本。我们可以看到,PC对于GO0.5%的标本与平原相似,远远少于其他类型的标本。铝合金经碱性蚀刻预处理后,CSH-GO0%试样的附着力明显增加,表明表面处理在界面粘接中起了重要作用。
值得注意的是,临界荷载PC对于SH-GO时,结合碱蚀刻和添加0.5重量%GO时,试样的含量进一步增加,得到的最高PC比平原和GO160.0%试样高约5%,表明表面处理与GO叶间可能存在协同增韧作用。然而,PC随着GO含量的进一步增加而下降,这可能是由于GO在较高浓度下的团聚。
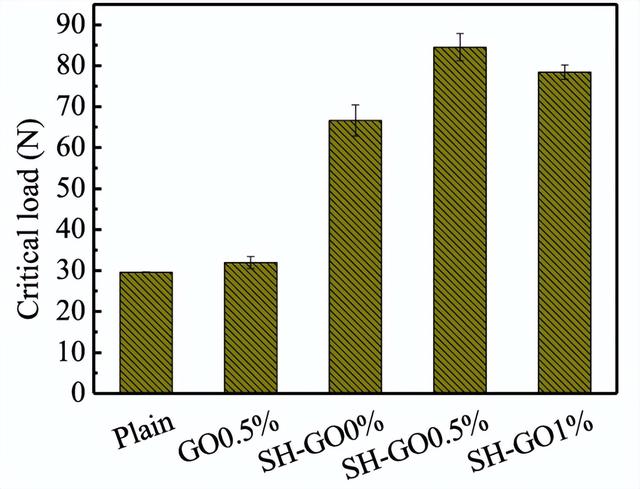
可以看出,对于普通试件和GO0.5%试件,I型断裂韧性与裂纹扩展增量∆a无关,这也表明脱脂铝合金与玻璃纤维层合板之间的界面结合较弱。然而,对于其他类型的试样,可以观察到典型的断裂行为,其中I型断裂韧性首先随着裂纹的扩展而增加,然后由于玻璃纤维桥接效应而变得稳定。
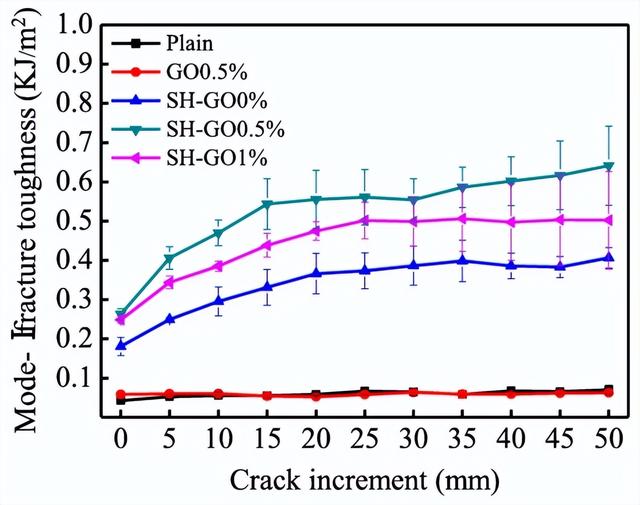
为了更好地理解表面处理和GO叶间对GFRP/Al层合板层间力学性能的影响,I型断裂韧性G集成电路和抗断裂性G红外总结在图中。其中G集成电路是 R 曲线和 G 上的起始值红外是裂纹延伸范围内的五个点的平均值∆A从20到40毫米。
G无显著差异集成电路和 G红外在平原和GO0.5%标本之间。然而,G大幅增加了225%和600%集成电路和 G红外对于SH-GO0%试样,当用碱性化学蚀刻处理Al合金板时可以观察到。这种增强是由于Al合金板的表面形貌和化学性质以及润湿性通过碱性蚀刻处理得到改善,如“模式I层间断裂韧性”部分所述。
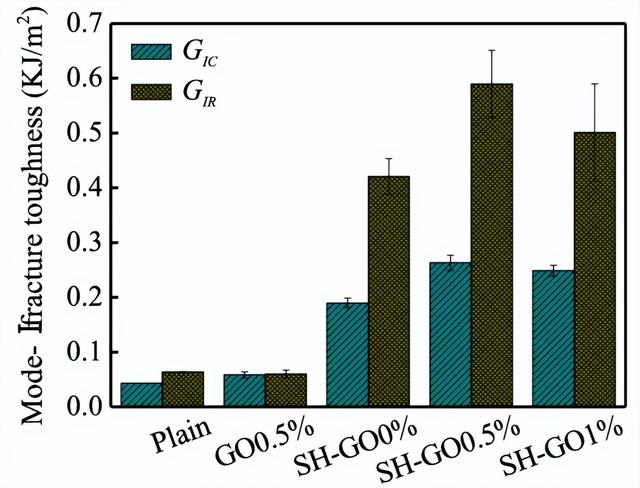
通常,载荷-挠度曲线在初始阶段显示线性响应,然后在最大负载之前显示非线性响应,然后在最后阶段突然下降。这显示了临界载荷PC和模式II层间断裂韧性G国际投资委员会根据载荷-挠度曲线计算的测试试样。
需要注意的是,定义临界荷载的标准PC对于易恩孚标本与DCB标本相似。我们可以看到,两者 G国际投资委员会和 PC的ENF标本与DCB标本具有相同的倾向。SH-GO0.5试件II.型断裂韧性和临界荷载的最大值分别比普通试件高381%和99%。
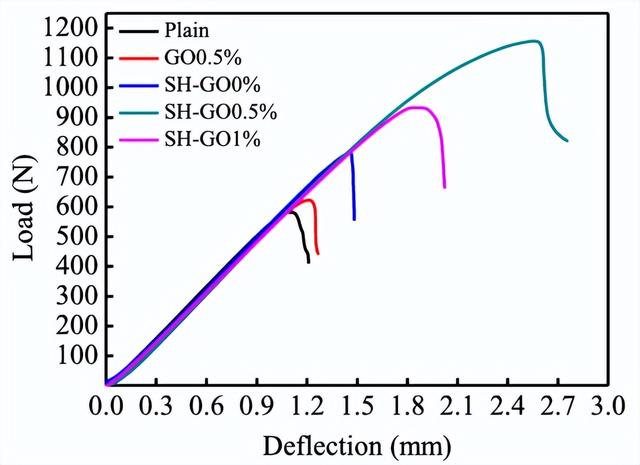
为了进一步揭示其增韧机理,采用SEM观察了GFRP/Al层合板的断裂形貌。
下方图片显示了DCB测试后GO0.5%,SH-GO0%,SH-GO0.5%和SH-GO1%试样的断裂面。关于GO0.5%试样所述,断裂表面具有光滑的外观,在铝合金板的表面没有任何可见的玻璃纤维或环氧树脂附着。GO0.5%试验的失效类型是粘合失效。至于SH-GO0%试验。可以观察到一些断裂纤维和环氧树脂附着在表面或嵌入微孔隙中,这表明碱蚀刻可以促进Al合金板与聚合物基体之间的机械互锁,进而改善它们之间的界面结合。
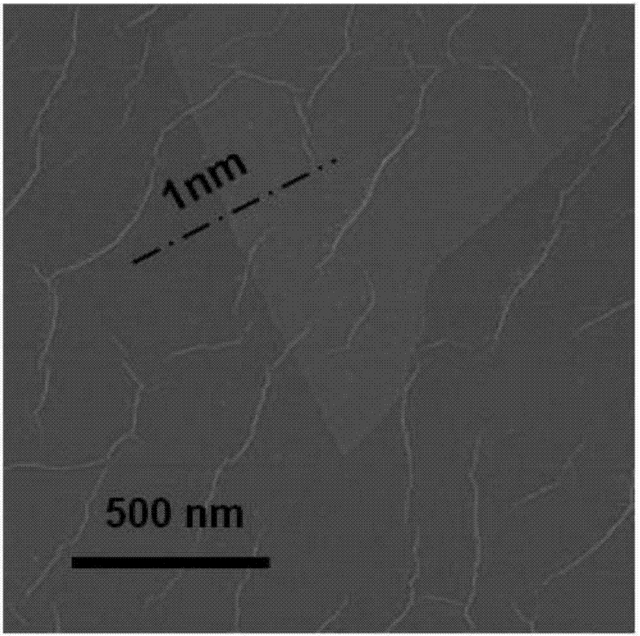
SH-GO0%试验的失效类型是内聚力和粘性的组合。与界面破坏相比,树脂分子脱粘引起的内聚破坏可能消耗更多的能量,表明SH-GO0%试样比GO.5%试样具有更高的I.I型断裂韧性。关于SH-GO0.5%和SH-GO1%试验。
可以观察到更不规则和更粗糙的断裂形态,这将产生更大的断裂面积,并且需要更高的驱动力和能量。
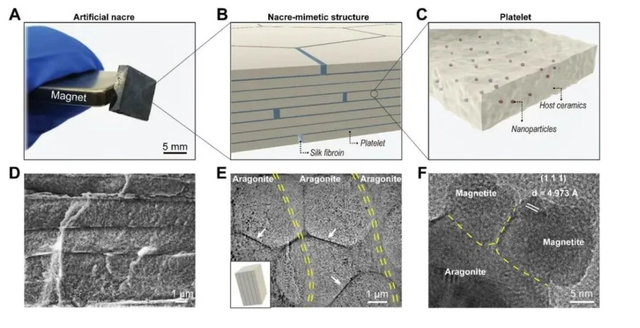
SH-GO0.5%和SH-GO1%试件的破坏类型几乎为黏性破坏,表明GO叶间添加可进一步提高GFRP/Al层合板的表面处理层间断裂韧性。可能的原因如下:GO由于其优异的力学性能,可以通过诱导裂纹挠度和裂纹桥接效应来有效提高环氧树脂的韧性,这通常需要更高的驱动力和更高的断裂能量。
同时,GO片表面的官能团有助于GO与环氧树脂之间的强界面结合,在从环氧基体中取出GO的过程中可能会消耗更多的能量。此外,GO的加入增加了树脂基体的反应性官能团。因此,与SH-GO0%试件相比,SH-GO5.1%和SH-GO0%试件的I.型断裂韧性进一步提高。
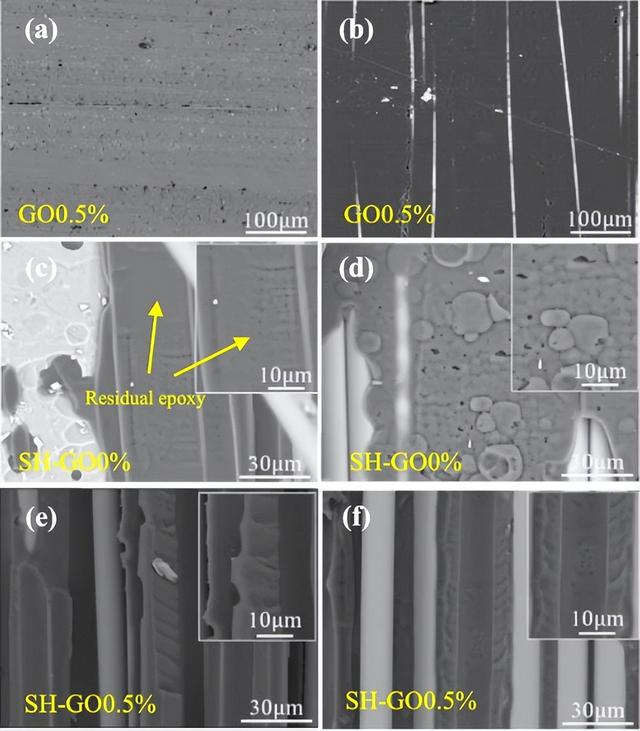
基于上述分析,证明了表面处理和GO-环氧树脂夹层对提高Al/GFRP层合板I型层间断裂韧性的协同作用。然而,过量的GO可能会对断裂韧性产生负面影响。因为GO的聚集可能引起应力集中并降低环氧树脂的韧性。SH-GO1%的I型断裂韧性低于SH-GO0.5%试件。
还采用SEM研究被测试样的ENF断裂表面。对于GO0.5%的试样,Al板和GFRP侧的断裂面相对光滑,与GO0.5%试件的DCB断裂形貌相似。对于SH-GO0%,可以观察到粘附在Al板表面上的断裂纤维和残留的环氧树脂, SH-GO0.5% 和SH-GO1%标本,这意味着与GO0.5%试样相比,会发生内聚破坏和更高的断裂韧性。
此外,SH-GO0.5%和SH-GO1%试件的铝板表面和复合侧存在大量典型剪切唇,表明损伤区增大,塑性变形较大,可能导致II.型断裂韧性高于SH-GO0%。此外,GO的聚集也可能是SH-GO1%试件与SH-GO0.5%试件相比II.型断裂韧性较低的主要原因。
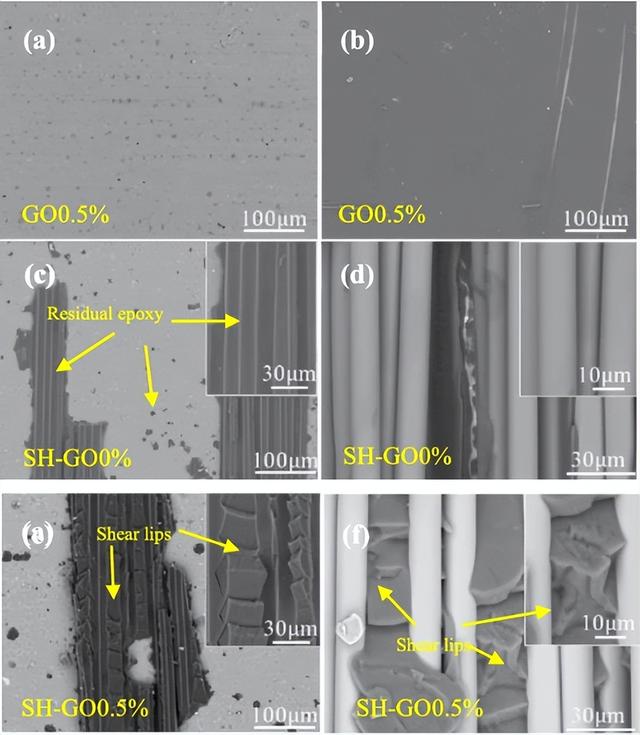
我们研究结合了碱蚀刻等表面处理和GO-环氧树脂层间材料,协同提高了Al/GFRP层压板的层间力学性能。DCB和ENF结果表明,碱蚀刻处理和GO0.5%环氧树脂叶间试件具有最高的I型和II.型层间断裂韧性,分别比普通试件提高了510%和381%。
此外,采用不同的表征技术研究了铝板的表面特性和被测层板的断裂表面,以揭示其协同增韧机理。