
颗粒增强金属基复合材料由金属和硬颗粒结合而成,以实现优于其组件的性能。在金属基体中,铝基金属基体仍然是观察到最多的材料,因为它具有合适的基质-颗粒键合、基体结构的简便控制、简单、加工成本合理和材料选择广泛。
它具有迷人的特性,例如高比刚度、低密度、更高的抗疲劳性、可控的热膨胀系数和高温下的出色尺寸稳定性。当密度较低时,与未增强的基体材料相比,PRMMC表现出更高的强度和刚度以及各向同性行为。然而,复合材料的摩擦学和力学特性主要取决于基体材料的组成、尺寸和增强阶段的体积分数以及制造方法。

有几个因素会影响填料颗粒在基质中的分布,例如流变行为、填料颗粒的均匀混合以及填料和基质材料随时间和温度的一致性。电气、机械和化学性能可以通过使用不同类型的增强材料来实现,例如连续纤维、不连续纤维、薄片纤维和短纤维和 MMC。
熔体搅拌铸造工艺用于制造铝基金属基复合材料。搅拌铸造是开发金属基复合材料的最成熟的技术之一。搅拌铸造因其灵活性、简单性和大批量生产的适用性而进行商业化。此外,搅拌铸造允许传统的金属加工,从而最大限度地降低产品总成本。使用铸造方法制备MMC的成本约为其他竞争方法的三分之一到一半,对于大批量生产,成本预计将降至十分之一。
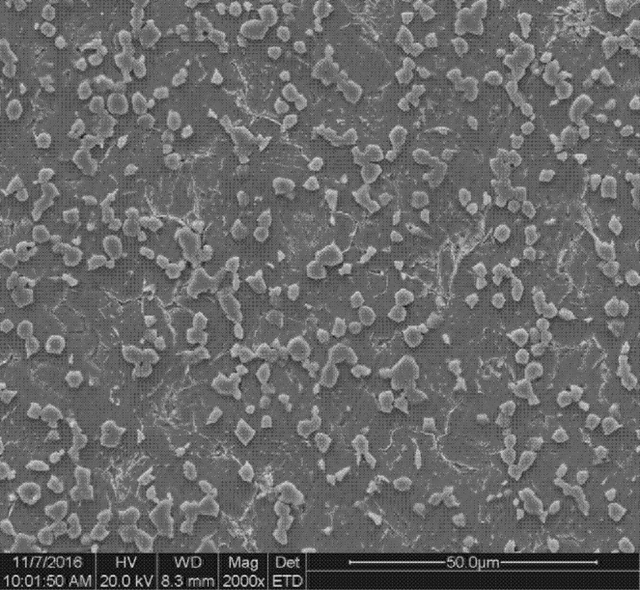
实验细节:如图所示,在该实验中使用了圆盘上的针式摩擦计。1. 使用的引脚是SS304和铝基复合材料被用作圆盘材料。每次实验将进行30分钟。
改变转速和施加载荷以观察整个实验过程中的摩擦变化。此外,在每次实验之前和之后,使用数字称量天平测量试样的重量,测量值之间的差异是磨损率。在整个实验过程中,与测试盘中心保持17毫米的摩擦距离。
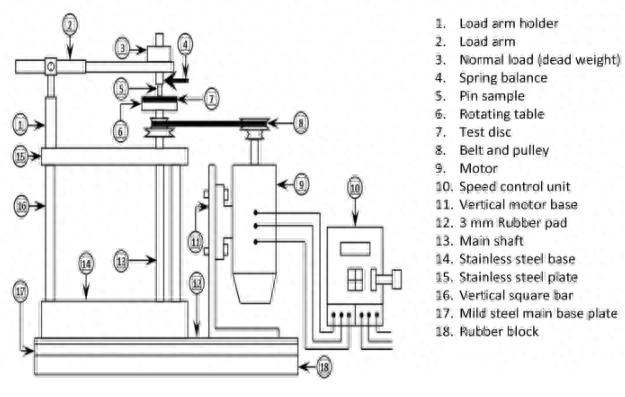
法向载荷和滑动速度对摩擦系数的影响:图片显示了摩擦系数与法向载荷变化的比较。纯Al6063的摩擦系数高于Al基复合材料。此外,摩擦系数随着填料颗粒百分比的增加而降低已嵌入到矩阵中。
当发向载荷为74、68.71和6 N时,所有组合的摩擦系数分别降低到约5%、7%和5.10%。然而,在减少施加的载荷下,粗糙度的接触最小化,并导致犁地动作,从而增加了摩擦系数。先前的一项研究表明,随着法向载荷的增加,由于表面温度升高,表面上可能会形成氧化层,该层提供自润滑作用并减少摩擦。
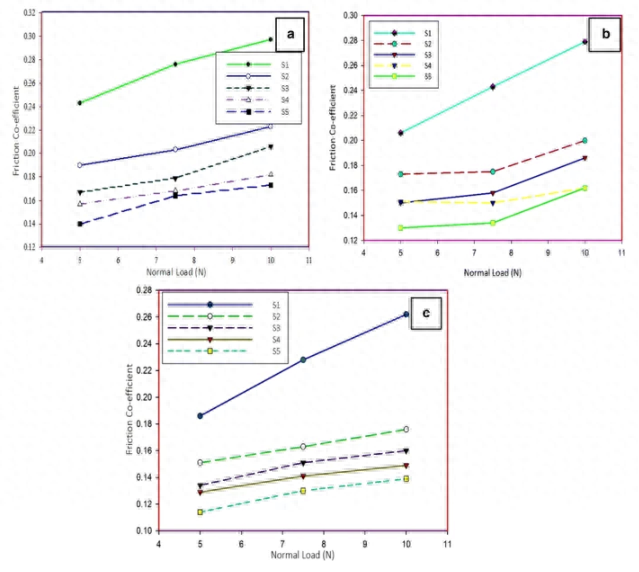
Al 6063 在工作正常载荷为73 N的情况下,从母体合金到复合材料的滑动速度分别为6.58、5和63.1 m/s时,分别降至0.5%、1.1%和5.5%。2、可以检查随着法向载荷的增加,摩擦系数增大。然而,摩擦系数随着SiC颗粒的增加而降低,在样品S5 [Al(6063)–10%SiC–1%Al2O3–1%氧化钛2]。
摩擦系数随着滑动速度的增加而降低可能是由于剪切速率的变化,这影响了配合材料的力学性能,这些材料的强度在较高的剪切应变率下很高,导致实际接触面积小,在干接触条件下摩擦系数低。这些结果与Chowdhury等人的发现非常吻合。
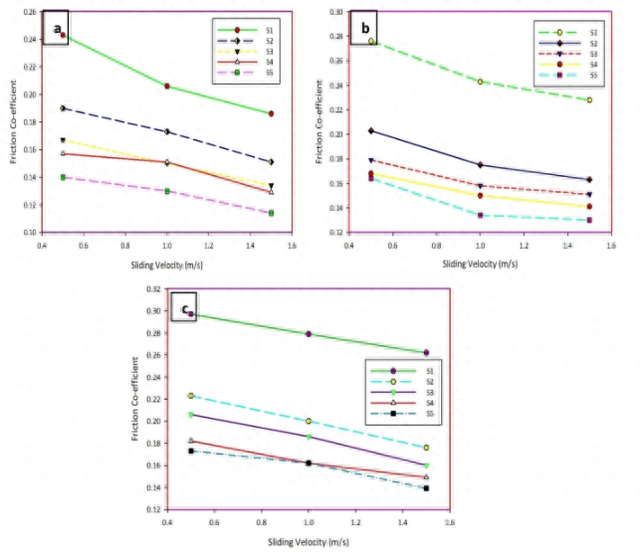
图片b显示了不同类型的销盘组合的摩擦系数随滑动速度的变化。Al 6063 (Al 6063–SiC–Al) 的摩擦系数2O3–二氧化钛2)在68.3 N法向载荷下,当母合金到复合材料的滑动速度分别为81.3、75和4.0 m/s时,变化分别为5.1%、1.5%和7.5%。
图3c表示Al 6063在71 N工作正常载荷下,母材到复合材料的滑动速度分别为6.83、3和88.4 m/s时,变化分别为0.5%、1.1%和5.10%。然而,复合材料的摩擦系数随着颗粒的增加而降低由于颗粒的润滑作用,改善了搅拌浇注复合材料的抗摩擦性能。以前的研究人员认为,配合表面之间氧化层的存在减少了滑动摩擦。观察到,随着滑动速度的增加,S5 [Al (6063)–10%SiC–1%Al 的SiC颗粒百分比最高时摩擦系数最小2O3–1%氧化钛2]。

滑动速度和法向载荷对磨损率的影响:图片a,b显示磨损率随着所有销和圆盘组合的施加载荷的增加而增加。然而,可以公开,在较高的负载下,氧化物薄膜被稍微去除,导致更高的磨损损失。当销上的载荷增加时,接触面积相对于标称接触面积增加,这增加了两个接触滑动面之间的摩擦力。增加的摩擦力和实际接触表面积导致严重磨损。
因此,摩擦推力和剪切力随着施加载荷的增加而增加,从而加快了磨损速度。这是由于增强颗粒SiC,Al的聚集2O3和 TiO2.发现滑动速度对摩擦系数的影响是反比的。在低速时,摩擦系数很高。随着速度的增加,摩擦系数的速率降低。铝也观察到了类似的趋势。这些数字还表明,在相同条件下观察到Al 6063制动盘的最高磨损率值。最低磨损率值的结果表明,Al 6063圆盘在所有条件下的磨损率均高于复合材料。

上面提到的结果是,SiC的百分比越高,在不同工况下的摩擦系数和磨损率越低。每当法向载荷增加时,摩擦和磨损率就会增加,这解释了研究人员报告的增强颗粒的均匀分布。在齿轮、凸轮和轴承密封件等非生产性摩擦应用中,随着法向载荷水平的降低,SiC 的百分比可以增加。
在加工、抛光和剃须等生产摩擦中,反之亦然。摩擦和磨损率随着其他操作因素的变化而受到不同影响。从SEM图像中可以看出,磨损碎屑和犁地效应随着滑动速度的增加而增加。Ramesh等人也观察到了类似的趋势。
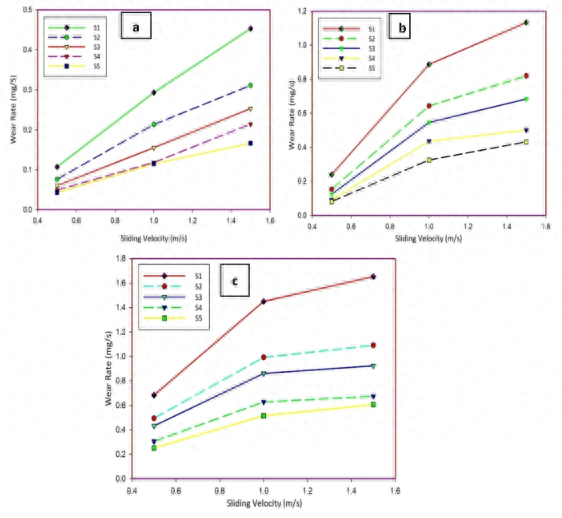
微观结构分析:摩擦和断裂表面的形态通过SEM分析表征。观察到的摩擦和断裂表面的形态在微观范围内。图7a-f显示摩擦和断裂形态受微观结构的影响很大。扫描电镜图像显示磨损碎屑、磨损轨迹和由于摩擦而累积的粗加工表面。
扫描电镜图像显示断裂、空隙和微裂纹表面。由于微裂纹和空隙的存在,MMC的颗粒与基体之间的界面强度较差。此外,这是由于磨损率和摩擦系数实验分析而发生的。由于犁地效应,已经产生了大尺寸的磨料磨损。
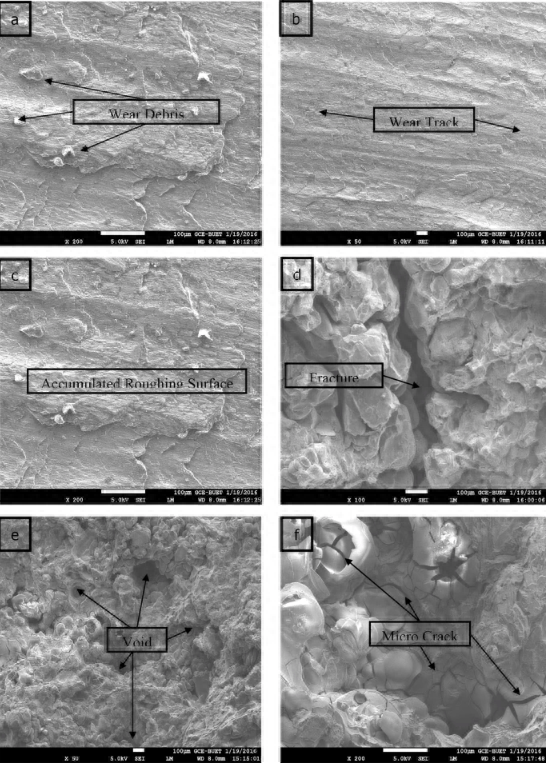
图片显示了 Al-84.31%、C-13.86%、O-1.57% 和 Si-.26% 复合材料的 SEM 和 EDX 显微照片。复合材料中铝的最大百分比。
来自几个斑点标签的EDX光谱也显示在图中。微观结构显示存在其他元素,如C,O,Si和Ti,这些元素可以通过EDX光谱中的Al峰检测到。在点0.16中,可以在MMC中观察到强烈的铝峰值。SiC、Al界面层的形成2O3和 TiO2粒子通过对EDX结果的探索得到证实。显示了几乎均匀的粒径分布,其中颗粒的平均直径为0.18μm。
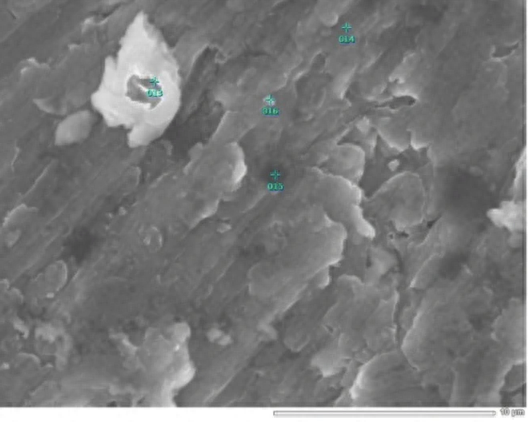
为了鉴定样品中存在的不同化学官能团[30],傅里叶变换红外光谱(FTIR)是一种无损检测工具的标准方法。红外吸收(FTIR)如图所示。10. C-H拉伸3200厘米等各种主要化学官能团−1, C=C 弯曲处 1650 cm−1, N–H 弯曲处 1400 cm−1和芳香 sp2C–H 拉伸 1050 厘米−1被识别。
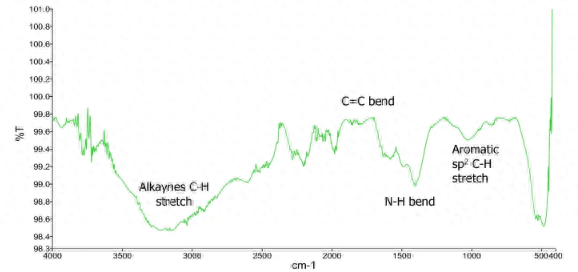
上面提到的结果是,SiC的百分比越高,在不同工况下的摩擦系数和磨损率越低。每当法向载荷增加时,摩擦和磨损率就会增加,这解释了研究人员报告的增强颗粒的均匀分布。在齿轮、凸轮和轴承密封件等非生产性摩擦应用中,随着法向载荷水平的降低,SiC 的百分比可以增加。在加工、抛光和剃须等生产摩擦中,反之亦然。
摩擦和磨损率随着其他操作因素(如滑动速度)的变化而受到不同影响。从SEM图像中可以看出,磨损碎屑和犁地效应随着滑动速度的增加而增加。Ramesh等人也观察到了类似的趋势。

本研究旨在通过不同百分比的SiC来降低铝基金属基复合材料的摩擦和磨损率。增强颗粒(碳化硅、铝)的影响2O3, TiO2)、滑动速度、法向载荷对磨损率和摩擦系数进行了研究。每当SiC填料颗粒的百分比增加时,在不同工况范围内,摩擦系数和磨损率就会以一定的速率逐渐降低。
由于表面粗糙度的降低、顶面硬度和密度的增加,观察到这些结果的趋势。此外,氧化层在摩擦接触界面负责减少摩擦力以及降低磨损率。进行了显微照片、FTIR 和 EDX 分析,并产生了关于改进摩擦学特性的一致结果。形态学研究揭示了磨损轨迹、微裂纹、空隙和叠层表面。基质和颗粒之间的界面键加固在磨损过程中起了重要作用。
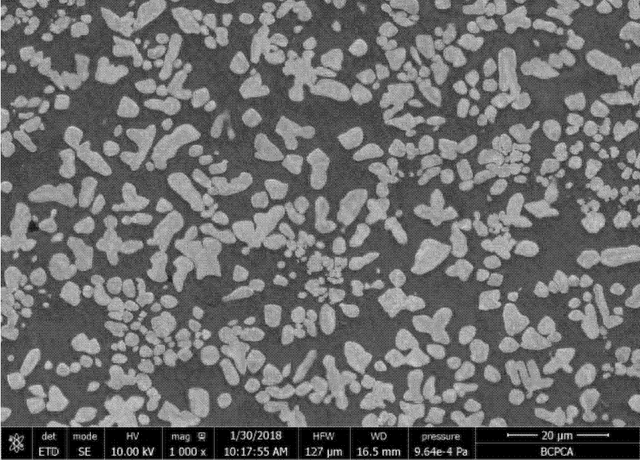
碳化硅,铝2O3和 TiO2Al-6063基体合金中的颗粒通过EDS元素映射的探索得到证实。使用FTIR分析鉴定峰值。结果表明,适当控制工艺参数(如法向载荷和滑动速度)可以改善摩擦性能。碳化硅的强化,铝2O3和 TiO2在铝基合金中,随着载荷和滑动速度的增加,摩擦性能显著增强,磨损率和摩擦系数得到最佳结果。从上述讨论和分析中,我们得出结论,Al-6063基金属基复合材料用SiC、Al增强2O3和 TiO2应首选用于低速应用。在文献中也观察到了类似的结果。