
简单来说,高温合金是含有至少一种镍、钴或铁元素的合金,在极端环境中表现出高性能和出色的稳定性。由于每种类型的高温合金中都存在各种元素,因此通过多年的工业生产,已经开发了定制的性能和应用,其中一种高温合金,即镍基合金,具有机械强度和抗蠕变性的显着组合合金718是镍基高温合金家族,被认为是最常用的合金718在航空航天,能源勘探和发电行业中具有广泛的应用。
具体而言,卓越的机械性能,包括对应力水平和温度的高耐受性,使其有资格在特别恶劣的环境中使用。
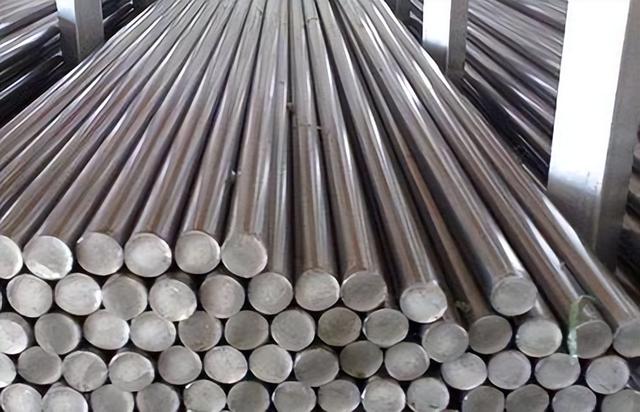
分析DED制造的合金718机械性能的主要样品制备步骤如下方图片所示。 最初,样品由 LASERTEC 65从铬镍铁合金 718 粉末中打印,使用线切割系统,然后将合金718样品形成狗骨形状。然后用UNSM处理样品的表面,从而形成硬化层。由于其极高的硬度,碳化钨被选为UNSM工艺中的击球材料。加工参数如下方图片所示。

QMESYS万能拉伸机用于对 UNSM进行 ASTM E718 标准的单轴拉伸测试。因此,图片显示了UNSM处理前后合金718的机械性能比较。合金718的主要力学性能是弹性模量,E,泊松比,ν,屈服应力,\(\正常尺寸{\sigma }_{y}\)和极限拉伸应力(UTS)。值得注意的是,DED生产的合金718表现出较差的机械性能。
建立气缸平面配置以执行微动磨损过程。SRV-5振荡台基于气缸/平面布置进行了一系列微动测试,未经处理/处理的合金718平面夹在下部试样支架上,而未经处理的合金718的圆柱体由上支架约束。为了实现微动行为,通过行程轴沿气缸的径向方向水平施加小振幅振荡位移δ。此外,载荷轴在上缸上提供恒定的法向载荷P,以达到接触目的。
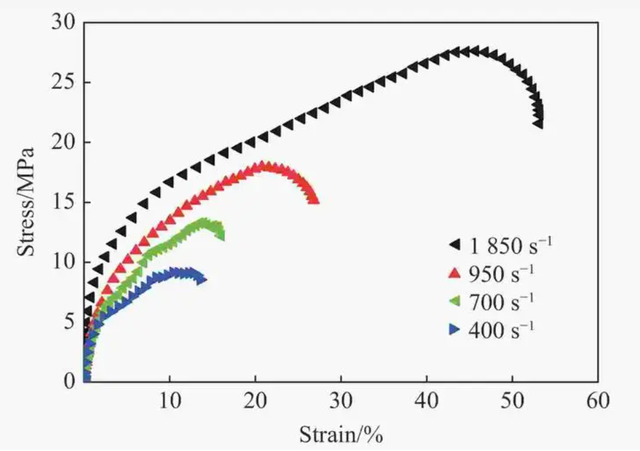
在微动过程中,摩擦传感器测量施加的位移和切向牵引力,这些力将转换为COF曲线。对于UNSM处理的试样,可以通过梯度硬度来评估微观结构的变化。研究中,使用微维氏硬度计来确定沿深度的硬度。
值得注意的是,每个深度的硬度测量重复了四次。可以观察到,当深度达到300μm时,UNSM处理的样品的硬度趋于稳定。此外,硬度值与未处理样品的硬度值没有显着差异,表明UNSM对深度大于300 μm的微观结构几乎没有影响。鉴于研究中用于UNSM的处理参数,因此受UNSM影响的最大深度为300 μm。
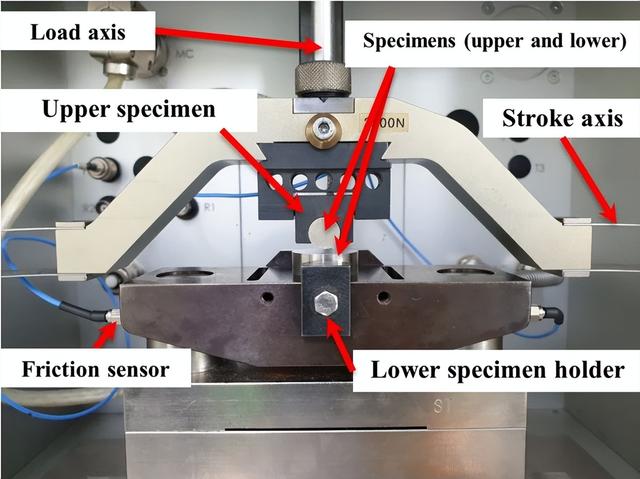
除了机械性能的变化外,UNSM处理还会影响718合金样品的摩擦学参数,例如COF和磨损系数。研究了UNSM技术对合金718在各种载荷条件下的耐磨性的有效性。
考虑到恶劣的工作条件,正常载荷P分别设置为627 N,880 N和1005 N。由于合金718在微动磨损过程中的应力状态的大小将超过其屈服应力,因此会发生塑性变形。此时,随着硬化模型的引入,塑性行为可以纳入本研究。半滑动距离δ = 120 μm,微动频率设置为 30 Hz,因此完成 11,20 个循环大约需要1.3分钟。COF定义为一个周期内测得的摩擦力幅度与微动磨损过程中施加的法向载荷P之比:
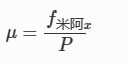
因此,在各种法向载荷下,COF随时间的演变如图所示。在磨合阶段会出现陡峭的峰值和谷值,即从测试开始到大约 1.5 分钟。然后,COF的曲线在微动磨损的稳态阶段稳定在恒定值。
在微动测试的补充之后,用轮廓仪测量表面的磨损量,然后用有限元结果进行验证。此外,根据有限元模型中使用的微动磨损算法,即耗散能量模型,实验测量的磨损损失将在下一节中计算为基于能量的磨损系数。因此,磨损系数将被转移到有限元模型中,用于后续的微动磨损模拟。
在ABAQUS商业软件中构建了与实验装置相对应的圆柱/平面配置有限元模型针对平面应变问题,构建了二维有限元模型。四节点平面应变单元 (CPE4) 在圆柱和平面零件中指定。
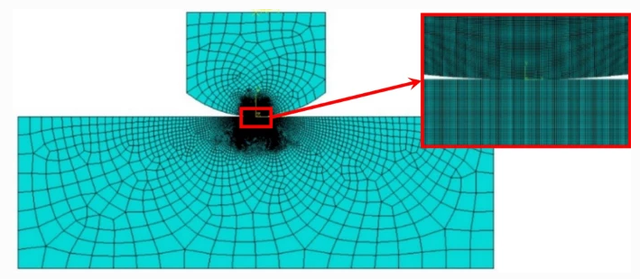
为了计算磨损损失,参考文献中研究了各种磨损规律。最广泛使用的基于接触力学的磨损计算公式是阿查德模型和耗散能量模型。对于阿查德的磨损模型,具体的磨损率可以表示为:
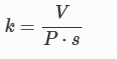
其中\(F\)是载荷,\(V\)是磨损损失体积,\(s\)是切向滑动距离。\({k}_{A}\) 是阿查德磨损系数,假设它是沿接触面的常数。此外,\(p(x)\) 和 \(\delta (x)\) 分别表示局部接触压力和局部相对滑动幅度。
然而,在许多数值模拟结果中,耗散能量模型往往与实验结果吻合较好。特别是,在高接触压力条件下,使用Archard模型的磨损预测不太准确。因此,本文选择能量磨损模型将带应力的磨损计算整合到有限元中。Paulin提出磨损量与摩擦功的一部分成正比。它将引发结构转变,使FEM能够捕获磨损周期内的塑性行为。实验测量表明,总磨损量与耗散的能量成正比。
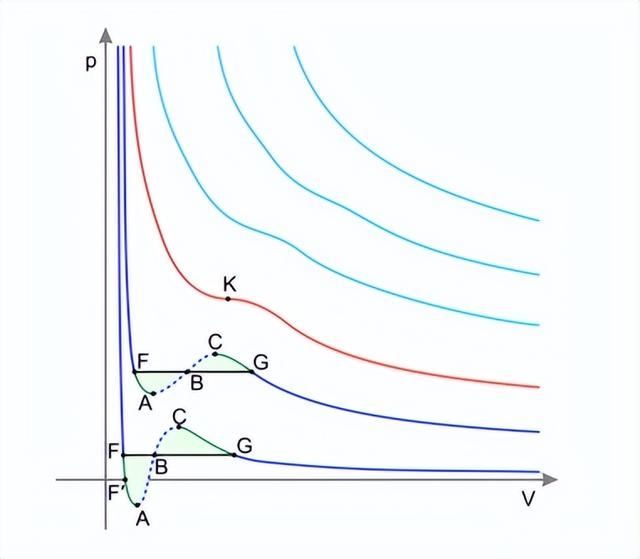
与其他形式的损坏相比,微动磨损在粗滑动条件下起着主导作用。加载历史如图所示。其中法向载荷\(P\)施加在加载步骤内的垫子上表面的中心。为了研究恶劣条件下的微动磨损行为,本文将接触面之间的滑动状态设置为全局滑动。切向振幅为 δ = 120 μm 的圆柱体运动被定义为滑动步长变体位移的边界条件。经过 20,000 次微动循环后,在卸载步骤中提取正常负载 \(P\)。

由于关键部件经常暴露在恶劣的操作条件下,这不仅是由于合金718在大微动距离下的磨损性能,而且还由于高法向载荷。如前所述,圆柱形意图在627-1005 N范围内承受三个相对较高的载荷。
此外,大应力状态引起的塑性应变的存在对表面应力状态分布和耐磨性有重要影响。在方程的基于能量的磨损模型中表明,局部应力\({q}_{i}(x)\)对于增量磨损深度计算和磨损表面更新很重要。因此,有必要捕获合金718样品在高负载条件下的塑性行为。
其中 \({\left.\sigma \right|}_{0}\)是零塑性应变下的屈服应力,\(Q\)和\(b\)是材料参数。具体来说,\(Q\)是屈服面尺寸的最大变化,也表示硬化饱和属性。材料参数\(b\)定义了屈服面尺寸随塑性应变演变而变化的速率。在本研究中,合金718样品的每个硬化参数都是通过基于方程的曲线拟合确定的。根据单轴拉伸试验的实验数据,拟合方程曲线如图所示。
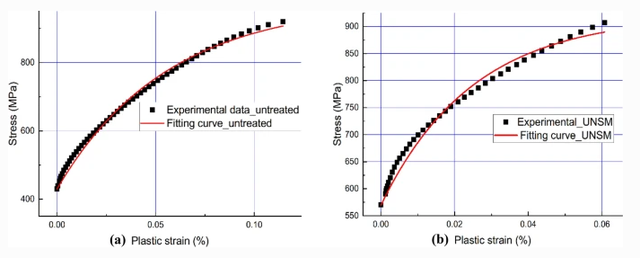
根据实验测试,UNSM处理后的合金718样品表现出更高的机械和摩擦性能。UNSM修改的主要因素包括杨氏模量\(E\)、硬化参数、COF和磨损系数。为了研究UNSM对使用有限元的耐磨性的影响,第一步是从实验测试中提取相关结果因素到有限元仿真。
这些材料参数将带有几何数据传输到Python代码和用户的子程序UMESHMOTION中,以生成FEM中的微动磨损模型。 值得注意的是,由于用于磨损深度更新(耗散能量模型)的算法,微动磨损曲线的变化主要由COF和磨损系数决定,对接触压力分布的影响很小。因此,忽略梯度结构和残余应力的建模对数值模拟精度的影响可以忽略不计。
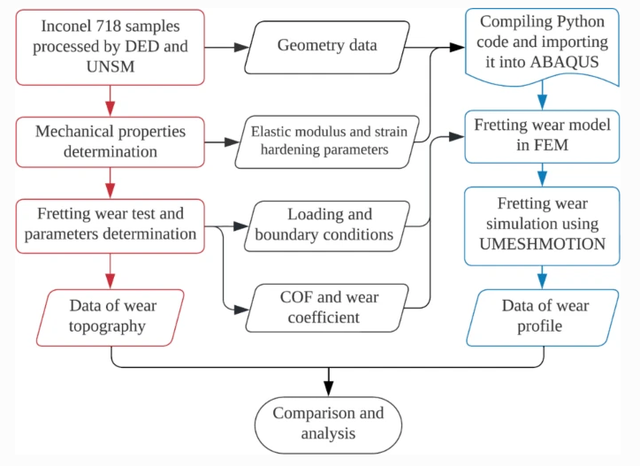
受益于有限元的灵活性,不仅可以考虑UNSM对718合金的整体影响,还可以考虑UNSM修改的每个参数的影响。设计了18个案例,分别考虑了UNSM整体、UNSM优化COF和UNSM优化的磨损系数对磨损性能的影响。
有限元模型的验证有一种理论,用于估计施加法向载荷下两个接触面之间的压力分布和接触面积。因此,赫兹接触方程可用于验证有限元模型中接触行为的准确性。验证的主要方面是接触压力分布,它由接触峰压力和接触宽度组成。关于赫兹接触理论,圆柱对平面配置的有效半径\(\overline{R}\)可以表示如下:
R¯¯¯¯=Rc
其中 \({R}_{c}\) 是圆柱体的半径。有效弹性模量 \(\overline{E}\) 分别使用圆柱体和试样的杨氏模量 \({E}_{c}\)、\({E}_{s}\) 和泊松比 \({\nu }_{c}\)、\({\nu }_{s}\) 定义:
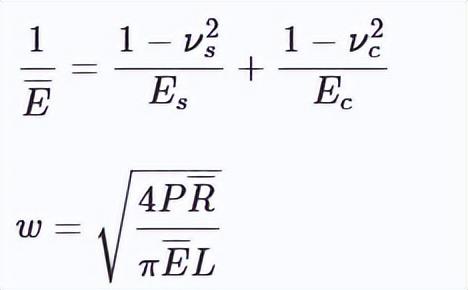
以未经处理的合金718为例,图中比较了FEM和赫兹解的接触压力分布。当法向载荷分别为 627 N、880 N 和 1005 N 时。结果表明,有限元模型得出的接触压力分布与解析解吻合较好。具体而言,未经处理和UNSM处理的样品的有限元模型的最大接触压力误差小于1%。结果表明,本研究中的有限元模型在载荷和边界条件、网格尺寸和网格几何形状下得到了正确的实现。
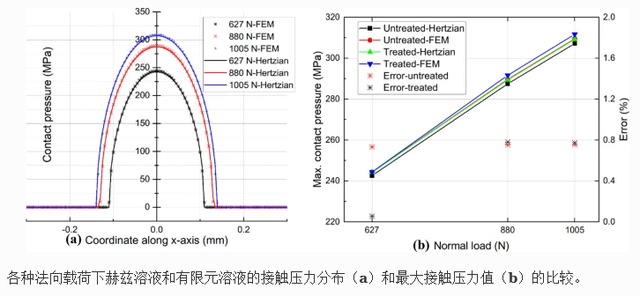
分析了UNSM对磨损性能的总体影响,并将结果与实验数据进行了比较,以验证有限元模型的准确性。指定哪些参数在微动磨损过程中起着重要作用以及每个人扮演什么角色具有挑战性。因此,不仅要考虑UNSM的总体影响,还要考虑每个UNSM修改参数对磨损性能的影响。
实验测量的力学性能表明,UNSM优化的弹性模量E略大于未处理的弹性模量E,分别为45.5和44.3GPa。未经处理和UNSM处理的样品之间的接触压力振幅差很小。即使法向载荷P达到1005 N,赫兹理论与有限元计算之间的差异也只有1%左右。因此,没有必要只研究UNSM优化的弹性模量E对磨损性能的影响。
当P达到1005N时,最大磨损深度达到约0.0058mm,这意味着试样处于相对不利的工作状态。此外,UNSM对磨损深度的缓解程度降至2.82%。同样,UNSM对磨损宽度的起伏程度也从8.57%降低到2.67%。磨损量可以通过积分曲线上方的面积来计算,然后与实验数据进行比较。它表现出前所未有的一致性,FEM与实验结果之间的最大误差小于2%,如下方图片所示。

综合分析后,可采用微动磨损模型研究各参数对磨损性能的影响机理。COF对于能量磨损模型准确预测磨损疤痕是必要的。当使用可变COF时,发现样品之间的磨损疤痕差异相对较小,特别是当微动循环达到高值时。该有限元模型仅采用恒定平均COF。无论样品是否用UNSM处理,COF的值随着P从627 N增加到1005 N而降低。
此外,由于UNSM使表面拓扑变平,因此在大多数荷载工况下,UNSM处理样品的COF低于未处理样品的COF。然而,当P达到1005 N时,与印刷时相比,UNSM修改后的COF值增加了5.6%。
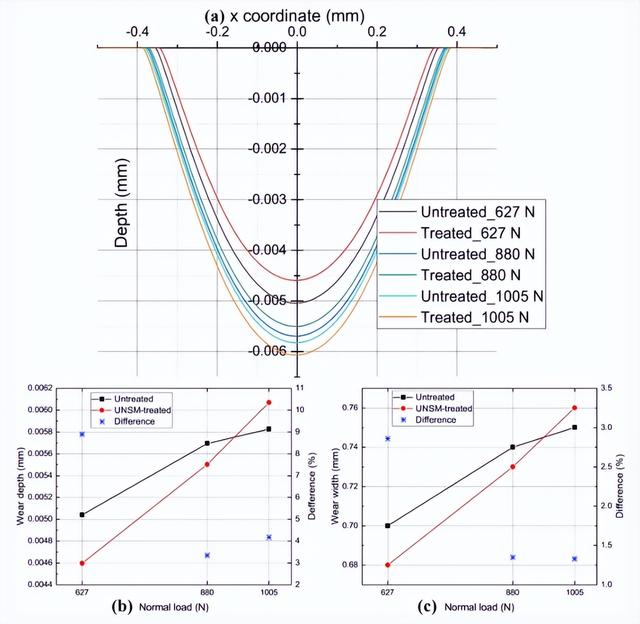
在这项工作中,合金718样品由DED从铬镍铁合金718合金粉末制成,然后通过线切割系统加工。由于表面质量差,UNSM技术用于改变合金718的表面性能。为了研究UNSM对磨损性能的影响,建立了基于耗能法的有限元模型。结论如下:
DED用于制备合金718样品,然后使用UNSM技术进行处理。单轴拉伸试验表明,UNSM可以显著提高合金718的力学性能。构建了基于面上气缸配置的微动磨损试验装置,该装置在三个高法向载荷P(即718 N,627 N和880 N)下对未经处理和UNSM处理的1005合金进行。此外,将各向同性硬化规律纳入本构模型,以捕捉高法向载荷P下的塑性行为。
有限元结果与实验测量结果吻合较好,循环2,20次后磨损体积误差在000%以内。此外,仿真结果表明,UNSM可以有效增强合金718在各种法向载荷下的耐磨性。当P = 627 N时,磨损深度的起伏度比未处理的磨损深度达到24.22%。然而,UNSM在高法向载荷P下的磨损性能提升不显著。当P = 1005 N时,UNSM诱导的磨损深度缓解下降到2.82%。