
文|万象硬核
编辑|万象硬核
«——【·前言·】——»
锂离子电池作为新能源电动汽车的主要动力源,其热特性管理不仅制约着电池寿命及续航里程,一旦出现热蔓延,将导致电池热失控,引发安全隐患。
锂离子电池,正常工作温度处于-20℃~60℃,理想工作温度范围20℃~40℃。故锂离子电池热特性有两个评判指标,一个是单体电池最高温度低于40℃,另一个是单一电池组温差不超过5℃。对于锂离子电池后端产线设备行业,一般要求单一充放电设备内单一电池组温差不超过4℃。
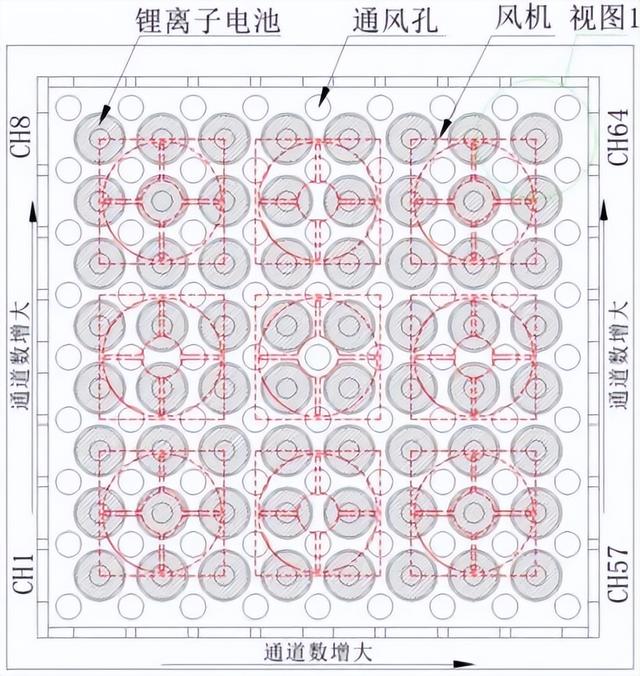
因此给电池降温显然是一件非常重要的事,但仅仅是降温还不够,而是要根据特定发热位置进行降温,因此风扇的位置和排列至关重要。国外某厂商,因为降温不及时导致电池温度过高而引起事故。
针对锂离子电池充放电设备内电池组温升过高、温度一致性不好的问题,以风冷系统充放电设备为研究对象,基于数值传热学理论,建立热力学计算模型并结合测试验证。那么这样是否可以降低电池过热而引发的各种问题的危险性?
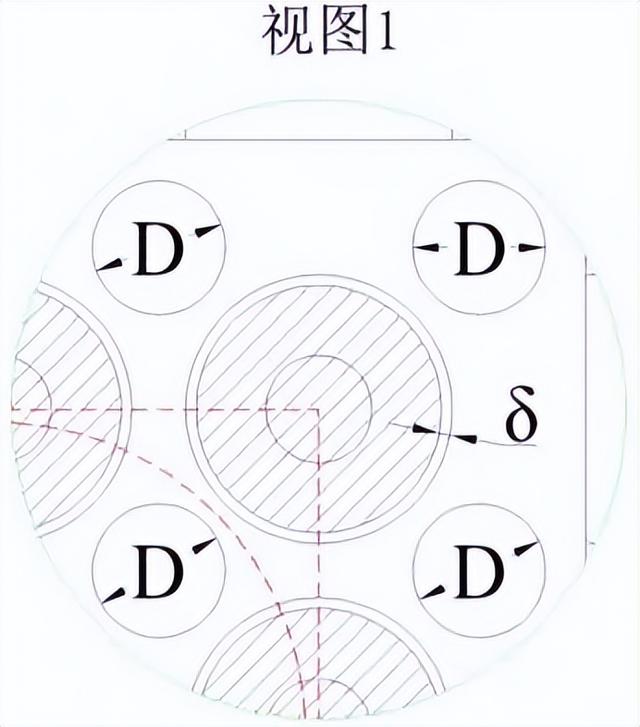
数值计算方法
简化的充放电设备模型由电池组、托盘、机构平台及风机组成,如图1所示。电池组包含64只4695锂离子电池,主要参数见表1。电池组呈8×8方式阵列,横向或纵向相邻两只锂离子电池中心距为60mm。
托盘内通风孔及环形风口用于空气流通。每只电池对应四个直径为D的托盘通风孔,对应一个尺寸为δ环形风口。机构平台底部风机将空气强制导入托盘内,通过电池组周围通风孔或环形风口,带走电池表面热量,形成对电池组的热特性管理。
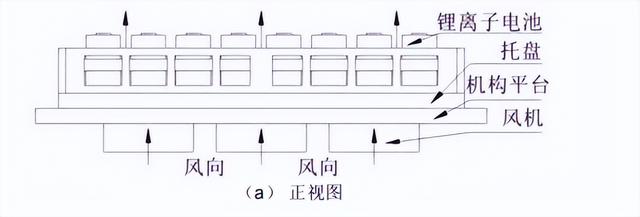
通过抽象充放电设备内散热特性,确认影响电池组热特性的主要因素是托盘通风结构与风机布局,以下研究将基于上述两点着重展开。
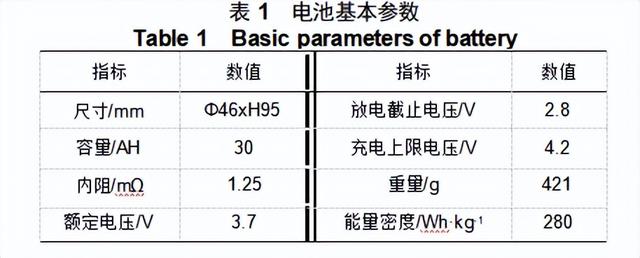
锂离子电池生产涉及多种工艺结合,故其内部结构相对复杂,同时会发生各种热、化学反应,为了便于研究充放电设备散热性能,对锂离子电池单体仿真模型做相应简化处理。锂离子电池简化为各向异性的实心圆柱体,产热恒定。电池产热计算公式:

式中:q为电池热量,W;V为电池体积,m3;I为电池电流,A;U0为电池开路电压,U为电池工作电压,V;T为电池温度,℃。
充放电设备内热交换过程以热对流为主,锂离子电池组与空气对流关系如下:
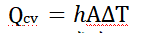
式中:Qcv为对流传热量,W;h为表面对流换热系数,W/(m2·℃);A为对流接触面积,m2;ΔT为电池温度与空气温度差值,℃。
流体介质遵循连续性方程、动量守恒方程和能量守恒方程。
基于压力求解器,选用工程上更经济的Standardk-ɛ湍流模型[20],采用二阶迎风格式的Coupled算法,使用双精度对控制方程进行稳态求解。空气物性参数为常数,温度为25℃,大气压力为常压,气固边界无滑移。托盘、机构平台与空气进行自然对流散热,对流换热系数5W/(m2·K),模拟充放电设备电池组1.5C(45A)倍率放电时温度分布情况,单体电池生热率48800W/m3。
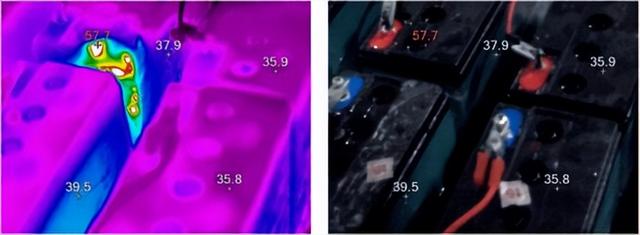
针对电池组通道序号定义,充放电设备模型图1(b)中,左下角为通道1,左上角为通道8,右下角为通道57,右上角为通道64,其他通道序号依据从下到上、从左到右的顺序依次递增。
利用ANSYSICEPAK对充放电设备风冷系统进行研究,对全计算域划分适应性强的非结构化网格。为提高计算精度,在流固壁面交界处建立边界层,并对其进行加密处理。
考虑到网格数对仿真计算影响较大,选用4套网格数验证电池组最高温度及最大温差变化趋势,如图2所示。当网格数量大于440万时,电池组最高温度及最大温差趋于稳定,考虑计算精度及经济性,最终选择440万网格。
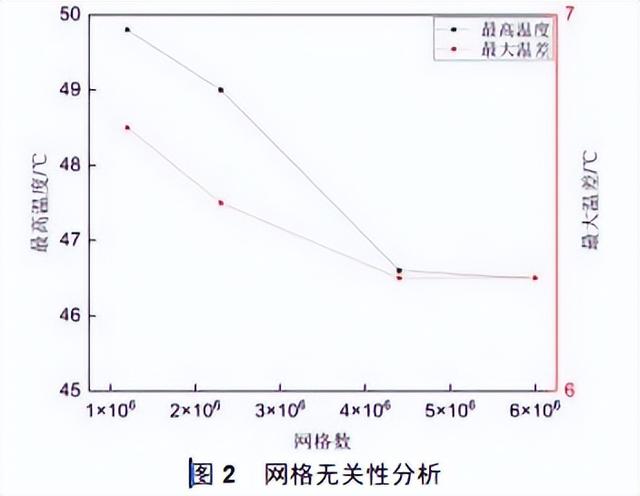
通过充放电设备测试平台(D=20mm,δ=0mm,风机正对电池,风机数量Fan=9),分别进行0.5C(15A)、1.0C(30A)、1.5C(45A)三种倍率放电温升测试,每只电池上表面单独配备一只温度传感器,可实时采集电池上表面温度。选取电池组中实测温度最高的电池通道,与仿真值对应通道对比,如图3所示。
其中仿真值监控点与实测监控点一致,均为电池上表面。由图3可知,随着放电倍率增大,电池最高温度逐渐上升;当电池以1.5C倍率放电时,电池温度急剧上升,放电后期电池热量堆积,使其温度分布超过热管理需求。整体看来,实测值与仿真值温度分布趋势基本一致,两者拟合度较好;不同倍率下,两者最大偏差为4.2%,表明热力学仿真模型相对准确。
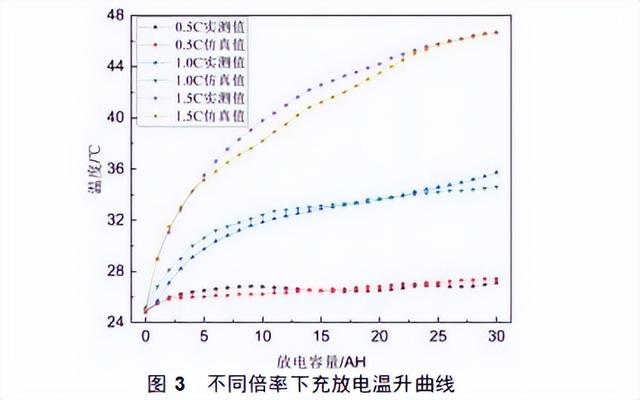
托盘通风结构对电池组热特性影响分析
充放电设备风冷系统的空气流体,主要通过流经托盘通风结构带走电池表面热量,实现对电池组热特性管理。托盘通风结构,包括托盘通风口D及托盘环形风口δ用于空气过流。为了探究不同托盘通风结构对电池组热特性的影响,设计如下方案:
方案1研究托盘通风孔的影响,当δ=0mm时,对比不同托盘通风孔D(20mm、22mm、24mm、26mm)对电池组温度分布及充放电设备流场的影响程度;

方案2研究托盘环形风口的影响,当D=20mm时,对比不同托盘环形风口δ(0.5mm、1.0mm、1.5mm、2.0mm)对电池组温度分布及充放电设备流场的影响程度;
图4为不同托盘通风孔对应电池组温度云图,由图4可知,不同工况下电池组温度分布趋势一致,电池组温度呈现对称型分布,且中间区域温升高于周边区域。在充放电设备风冷系统中,电池组作为固定热源进行热辐射扩散热量,需利用风冷系统进行对流换热降低电池本体温度,当电池组内部流场不畅时,将导致中间区域热量集聚,形成温度中间高、周边低的现象。
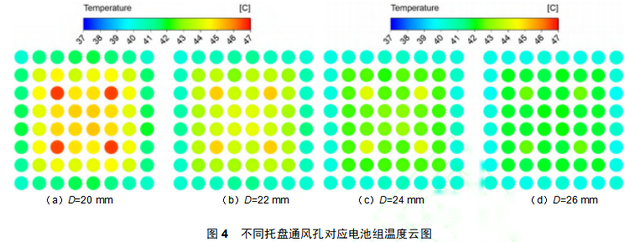
图5为不同托盘通风孔对充放电设备系统性能的影响。由图5(a)可知,随着通道数依次增大,对应通道温度呈现周期性变化;随着D增大时,电池组局部高温出现明显下降,且最大温差显著减小。
图5(b)则表明,托盘通风孔D的数值大小与各工况下电池组温升及温度均匀性基本呈线性关系,当D=20mm时,电池组最高温度46.6℃(温升21.6℃),最大温差6.3℃;当D=25mm时,电池组最高温度42.8℃(温升17.8℃),最大温差3.1℃。通过增大D,至多可使电池组最高温升下降8.2%,温度均匀性改善50.8%。
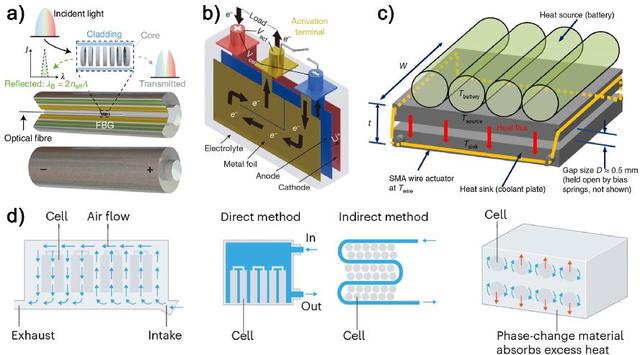
由图5(c)及(d)可知,随着D增大,风阻逐渐下降,通风量则持续上升,电池组表面湍动能缓慢提高,但总体数值较低。这说明通过改变托盘通风孔D,可以一定程度上改善风冷系统流场通风量,从而对降低电池最高温升、改善电池组温度一致性,有积极影响。但电池组表面湍动能处于相对低位,
说明电池表面换热强度不高,对流换热性能不佳。因而仅通过改变托盘通风孔,不能将电池组最高温度控制在40℃以内,说明托盘通风孔D对电池组的热特性影响有限。
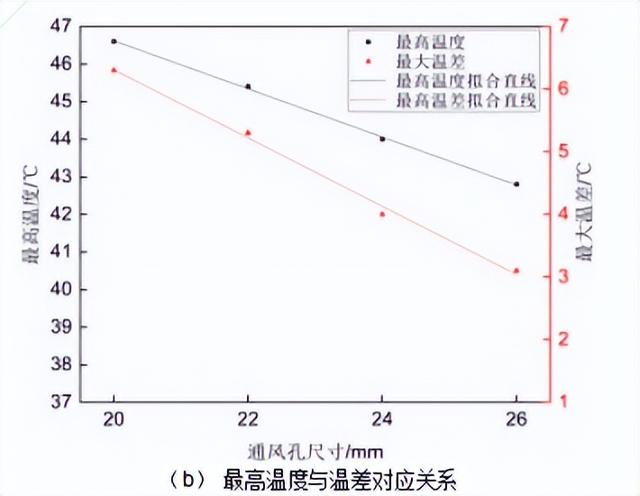
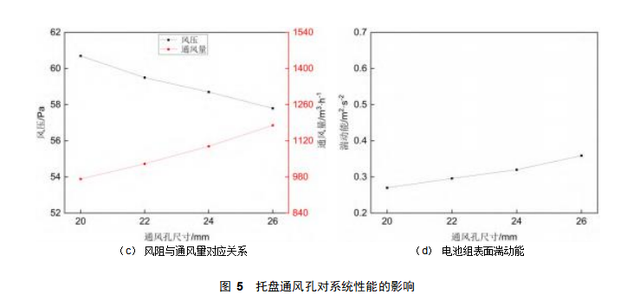
图6为不同托盘环形风口对应电池组温度云图,相比于图4,图6中电池组整体温升下降更明显,这说明托盘环形风口δ比托盘通风孔D更能影响电池组温度分布。
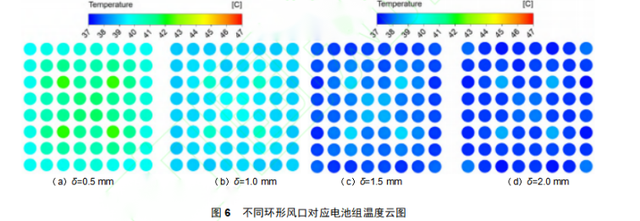
图7为不同托盘环形风口对充放电设备系统性能的影响。图7(a)可知,随着δ增大时,电池组温度波动相对更加平缓,当δ≥1.5mm时,电池组各通道温度均低于40℃。
图7(b)则表明,托盘环形风口δ对电池组温度分布影响呈现非线性关系;随着δ增大,电池组最高温度分别为42.4℃、40.4℃、39℃、38.3℃,最大温差分别为2.8℃、1.9℃、1.4℃、1.2℃;各工况下电池组依次下降4.7%、3.5%、1.8%,温度均匀性改善32.1%、26.3%、14.3%,这表明δ对电池组温度分布的影响,随着δ数值增大而逐渐减弱。
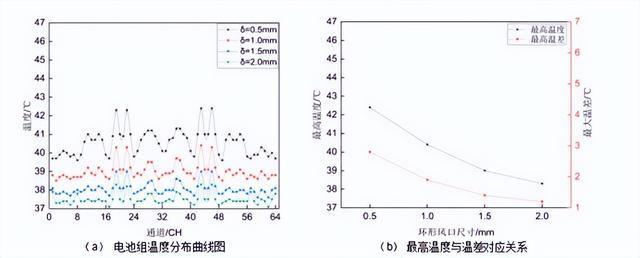
由图7(c)及(d)可知,不同托盘环形风口δ与不同托盘通风孔D对充放电设备内风压及通风量的影响趋势基本一致,但环形风口δ对电池表面湍动能的影响程度是通风孔D的1.8倍。
综合来看,托盘环形风口δ对电池组温度分布影响更显著,甚至起关键性影响作用。造成这种现象主要有如下原因:①托盘环形风口紧贴着锂离子电池外表面,可以引导冷空气流经电池表面,提升电池表面对流换热系数,从而达到改善电池组散热效果的目的;②托盘环形风口的引入,可以提高电池表面附近的湍流度,湍动能强度的提升同样可以导致传热率的增加,起到增强风冷系统对流换热的效果。
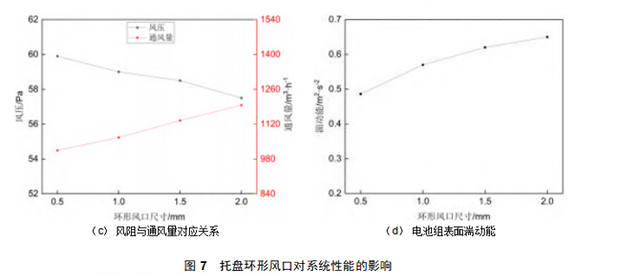
风机布局对电池组热特性影响分析
充放电设备利用风冷降低电池的最高温度,并改善电池组温度均匀性性。作为风冷的主要动力源,风机布局的位置及数量将会显著影响电池组换热效率。为了探究不同风机布局对电池组热特性的影响,设计如下方案:
方案3研究风机位置的影响,当D=20mm,δ=1.5mm时,对比不同风机位置对电池组温度分布及充放电设备流场的影响程度,如图8所示;
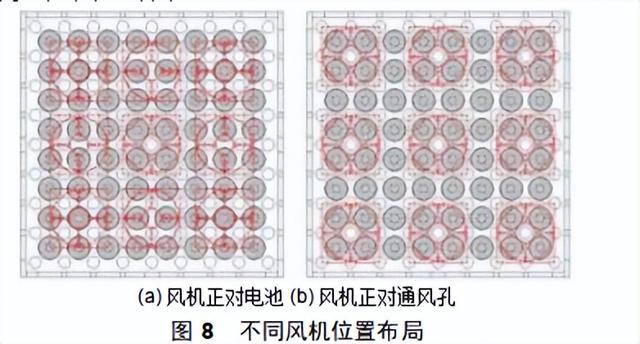
方案4研究风机数量的影响,当D=20mm,δ=1.5mm时,对比不同风机数量对电池组温度分布及充放电设备流场的影响程度,如图9所示;
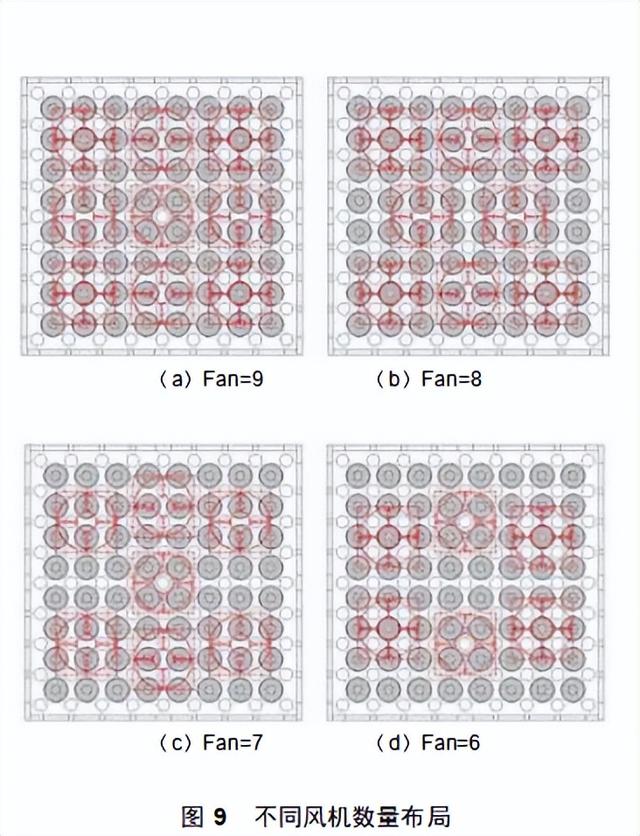
图10为不同风机位置对应电池组温度云图,与图10(a)相比,图10(b)电池组局部高温更明显,且高温区域明显增多,说明不同的风机位置布局对电池组的温度分布有显著差异。
图11为不同风机位置对充放电设备系统性能的影响。
由图11(a)及(b)可知,对比风机正对电池的工况,风机正对通风孔时,电池组周边区域温度相对稳定,中间区域各通道温度均有明显上升,尤其电池组的最高温度39.6℃趋近于40℃临界点,最大温差则上涨21.4%,这显然不利于电池组的热特性管理。图11(c)及(d)表明,风机正对通风孔时,充放电设备内通风量提升了31.4%,这是因为风道正对通风口,
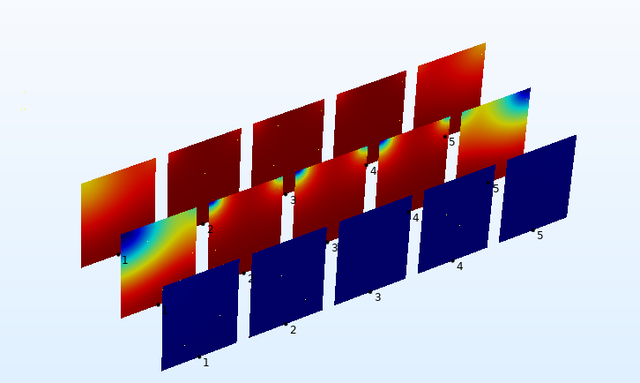
充放电设备内流场相对更加顺畅。但风机位置的偏移,会导致流场流体远离电池组表面,充放电设备内空气流体虽然呈现增加势态,但流体并未流经电池组表面,导致电池组表面对流换热效果下降。同时电池组表面流体的减少,也致使电池组表面湍动能呈现减弱趋势,再一次降低了电池组表面换热性能。
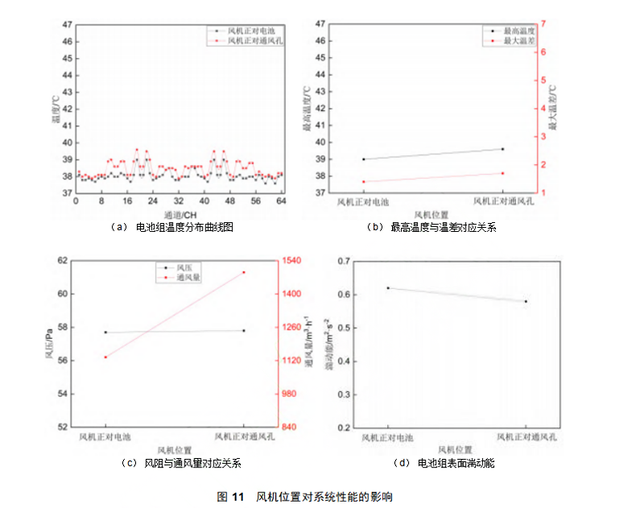
图12为不同风机数量对应电池组温度云图。由图12可知,不同风机数量会导致电池组的温度分布趋势不一致;Fan=8和9时,电池组温度分布范围较接近,当Fan=6和7时,电池组温度分布范围明显加大,且局部高温明显。
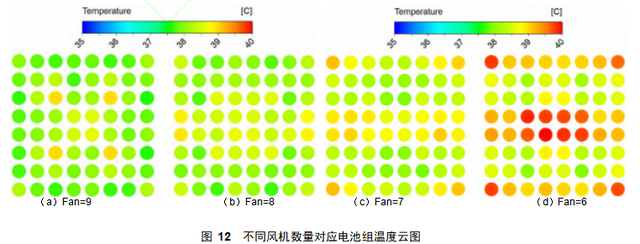
图13为不同风机数量对充放电设备系统性能的影响。由图13(a)及(b)可知,风机数量对于电池组的温度分布呈现积极影响,随着风机数量增加,电池组最高温度持续下降,且电池组温度一致性更趋近;当Fan=6时,电池组最高温度处于40℃临界值;当Fan=9时,电池组最高温度下降到39℃,温度一致性改善30%。
图13(c)及(d)表明,风机数量与充放电设备内通风量及电池组表面湍动能呈正相关,与Fan=6相比,Fan=9时,通风量提升23.8%,电池组表面湍动能上升21.6%,电池组表面换热性能得到极大提升,因而电池组热特性表现更优秀。虽然Fan=6时,电池组热特性相对较差,但整体亦能满足需求,而当考虑碳排放时,风机数量越少则意味着越能节省系统能耗及成本。
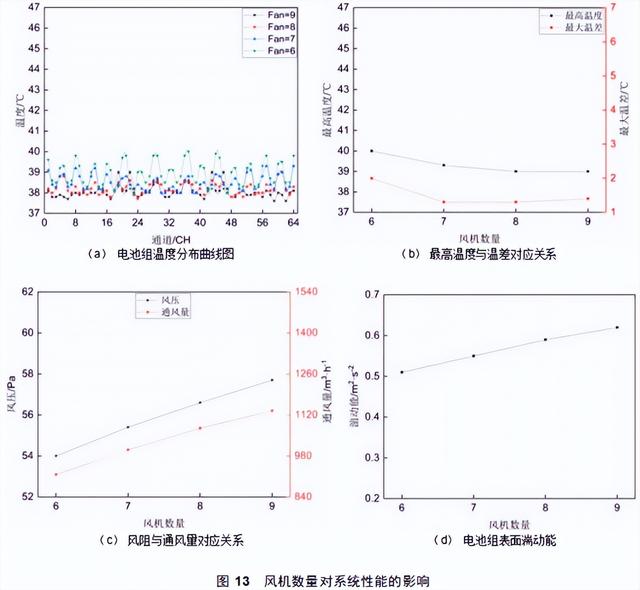
结语
托盘通风结构对改善电池组热特性管理有显著影响,托盘环形风口可将电池组表面湍动能提升80%,对强化电池表面换热性能、促进风冷系统对流换热效果起关键作用,当δ≥1.5mm时,电池组满足最高温度低于40℃且最大温差小于4℃的热特性需求;托盘通风孔在有限范围内(D=20~26mm),不能使电池组热特性满足需求;
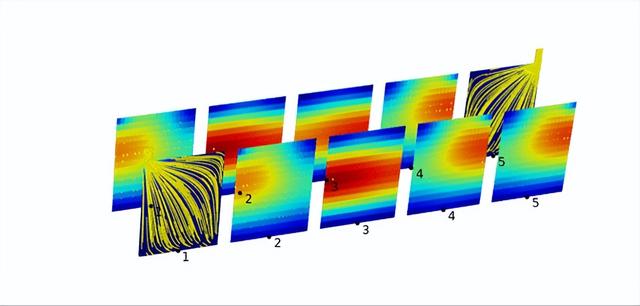
风机布局同样影响电池组热特性管理,相较于风机正对电池时,当风机正对通风孔时,虽然通风量提高31.4%,但并未实质性改善电池表面对流换热效果,反而致使电池组最高温度趋于40℃临界值,最大温差上升21.4%;
风机数量越多,风冷系统通风量及电池表面湍动能提升越明显,当Fan=6时,电池组最高温度为40℃,若考虑节能需求,风机数量处于6~8时,一方面能满足热特性管理需求,另一方面则有助于节省系统能耗,同时降低系统成本。