
文|万象硬核
编辑|万象硬核
«——【·前言·】——»
锂离子电池的热行为描述了电池在工作过程中热量的产生和分布状况,掌握电池的热行为是对电动汽车电池组进行热管理的首要工作,可为管控电池温度场和提升整车的可靠性提供帮助。
准确的了解电池的发热行为,可以从一定程度上遏制电池因过热而导致的热失控现象,从而减少电池燃烧的概率,但目前的大部分方法都无法精准的对电池的热行为进行监测,或者存在耗时过长等弊端。
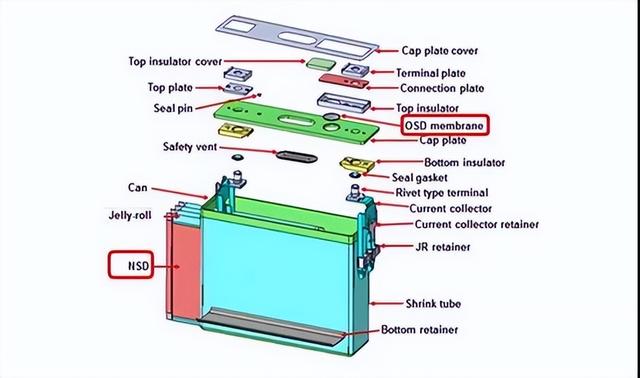
在国外某电动汽车电池生产厂商所使用的电池热行为监测方法,依然是传统的电池生热模型,但这些方法表征电池的产热行为耗时较长,已经无法适应现代社会对它们的需要。
针对方形硬壳锂离子电池的产热行为表征问题,结合理论分析与实验研究提出了一种量化分析新方法——热补偿法。那么,这种方法是否可以弥补目前电池生热行为检测耗时过长的不足?
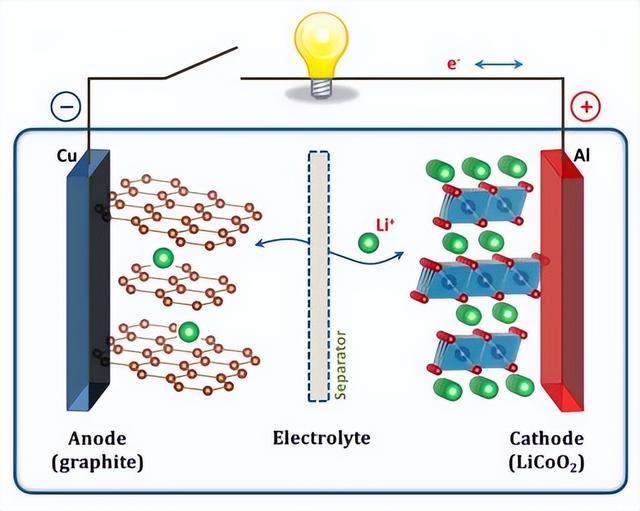
电池热补偿产热理论模型
当电池在实际环境中工作时不可避免会有热量损失,图1示意了电池在实际环境中工作和停止工作后的温变过程,图中Ti为电池的初始温度(环境温度),Tmax为电池的最大温度,0至t2为电池的工作时段,其温度不断上升,t2至t3为电池停止工作后的自然冷却时段,其温度自由下降。
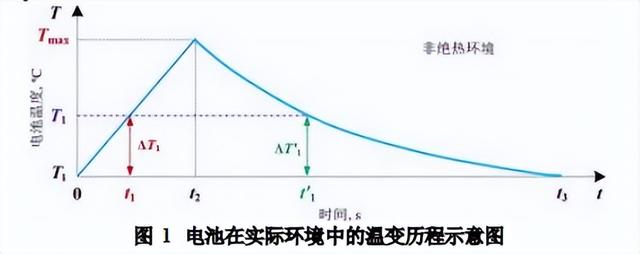
锂离子电池的产热部位主要为内芯和正/负极耳,由图1:
在0~t2时段,电池内芯均匀产热,由能量守恒定律:

式中Pin为电池内芯的生热率,Pin-loss为电池工作时段的内芯热损,cin、min和Tin分别为电池内芯的比热容、质量和温度。
在t2~t3时段,由能量守恒定律:

式中P'in-loss为电池停止工作后的内芯的热损,Tin-drop为由热损引起的下降温度。
对于图1中任意时刻的电池温度T1,其对应的电池在工作时段于t1时刻的热损Pin-loss与在电池自然冷却阶段于t'1时刻的热损P'in-loss相近(Pin-loss≈P'in-loss),原因为它们的温差相等(ΔT1=ΔT'1=T1–Ti)。
则由式(1)和式(2)可得:

锂离子电池正/负极耳的产热量可根据电热学原理进行计算:
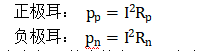
式中Pp和Pn分别为电池正极耳和负极耳的生热率,I为电池的工作电流,Rp和Rn分别为电池正/负极耳的电阻。
联合式(3)至式(5)可得电池的总生热率P:

由式(6),只要知悉电池内芯的温升率和由热损引起的温降率,及其正/负极耳电阻等,即可确定电池的总生热率,为确保准确,在表征电池内心的生热率时,应尽量选用内芯中心的时变温度数据进行计算。
实验布置及测试过程
测试对象为方形硬壳磷酸铁锂电池,尺寸为17mm×79mm×124mm,正极材料为磷酸亚铁锂(化学式LiFePO4),其质量、比热容、容量、标称电压分别为328g、1080J/(kg·°C)、8.0Ah和3.2V。
图2展示了测试装置实物图及其爆炸简图和热电偶布置方式。
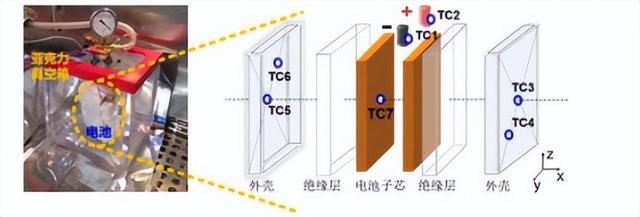
图2中,TC1和TC2被分别布于电池正/负极耳处。根据电池的对称性,在其两主面中心部位,和其左上角、右下角位置各布一个热电偶,其中TC4和TC6分别距电池底部和顶部的距离均为电池高度的1/4。
为监视电池内部温况,破除其小侧面(垂直y轴)中心部位外壳,将TC7置于两电池子芯(电池内芯由两个相同规格的子芯并联组成)接触面的中心部位,然后采用真空封泥密封开口,并采用PI绝缘胶带紧绷密封区域。
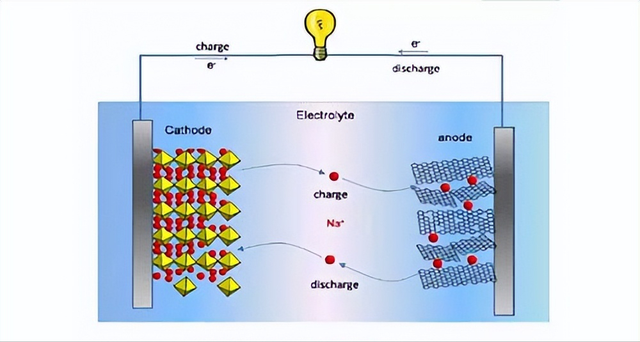
而且测试过程中将测试装置位于恒温箱内部,由其提供初始温度和恒定的环境温度,为减弱辐射换热,在装置的四周和底部贴敷镀铝反射膜,测算过程分为“热损标定”和“正规测算”两大步骤,下面通过实例演示具体过程:
为准确测算电池的生热率,须首先确定其工作过程中的热损。因为环境温度和SOC对锂离子电池的热损影响较小,故本次实验仅选择初始温度0ºC、SOC0.5工况即可满足热算标定需求。
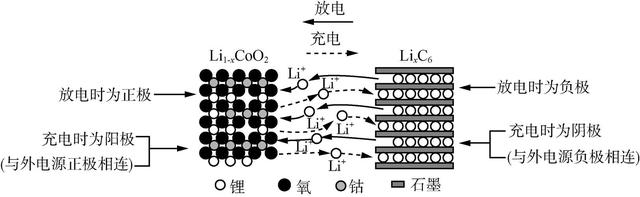
热损标定过程:待所有准备工作就绪,将电池、测试装置及恒温箱的初始温度调至Ti(0ºC);其次,对电池以1C倍率进行充放电循环至其温度接近Ti+45ºC时为止;最后,为节约时间,当电池温度自由降落至Ti+5ºC时停止实验。
实验结束,处理数据时,为计算方便,将电池温度与炉温间的温差T-Ti降至41ºC时的时间记为0点。根据上述步骤,得到的电池自由温降曲线如图3。
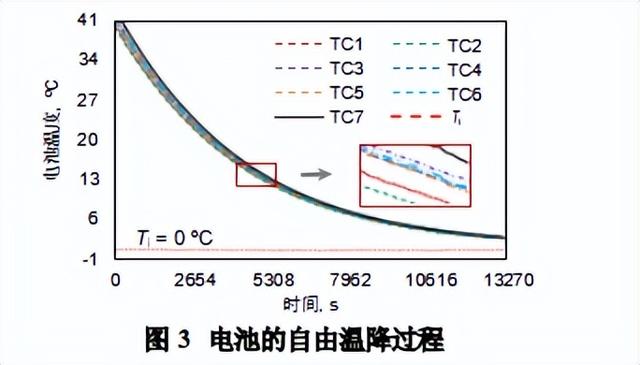
由图3,求取电池的平均温度Tavg,继而计算温差Tavg-Ti,并对Tavg-Ti与时间t的关系进行回归分析,并对拟合方程求一阶导数,得电池的温降率dTdrop/dt,再继而求取dTdrop/dt与Tavg-Ti间的曲线关系,如图4。
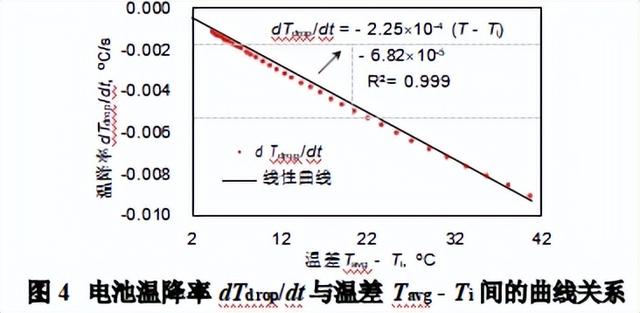
由图4,电池的温降率dTdrop/dt与温差Tavg-Ti近似呈线性关系,斜率为-2.25×10-4。cmdTdrop/dt为电池的热损。
实验初始,电池满电,调节电池、测试装置和恒温箱炉温为Ti,然后给电池以X倍率放电,并实时记录电池的温变状况,待电池电压降至2.0V,停止实验。根据上述实验过程,当Ti为0°C,X等于1时,电池的温变状况如图5。
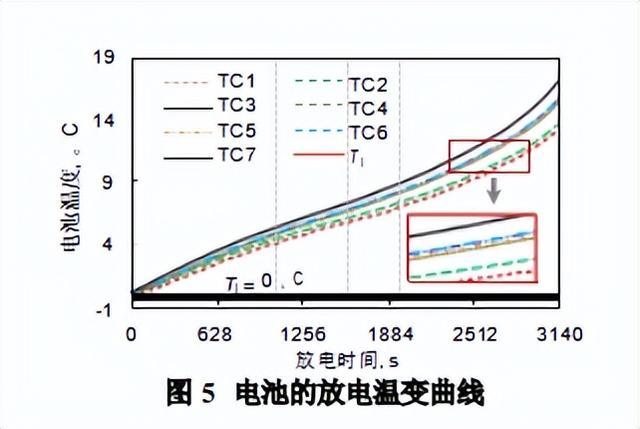
由图5,电池工作过程中,中心温度(TC7,即Tin)较高,外部温度较低,这主要是由电池外部热损较大所致。此外,极耳温度最低,其外壳各测点(TC3~TC6)的温升较接近。
电池正极耳的温度略低于负极耳温度,原因为电池正极电流集流体和正极耳的材质分别为铝合金和不锈钢304,相较于材质分别为合金铜(TU1)和铅黄铜的负极电流集流体和负极耳,其热导率较低,疏散电池内芯热量的能力较差。
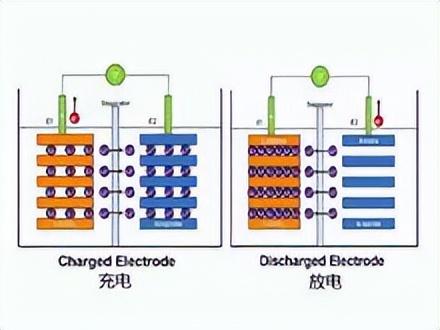
对图5中测温点TC1(Tn)、TC2(Tp)和TC7(Tin)的温升数据与时间t的关系进行回归分析,并对拟合方程求一阶导数,得温升率dT/dt。图6展示了该工况下测温点TC1、TC2和TC7的温升率与工作时间的曲线关系。
计算图5中TC1、TC2和TC7测温点与环境温度间的温差,将该温差代入图4中的方程,即得电池温降率与时间的曲线关系,如图6。
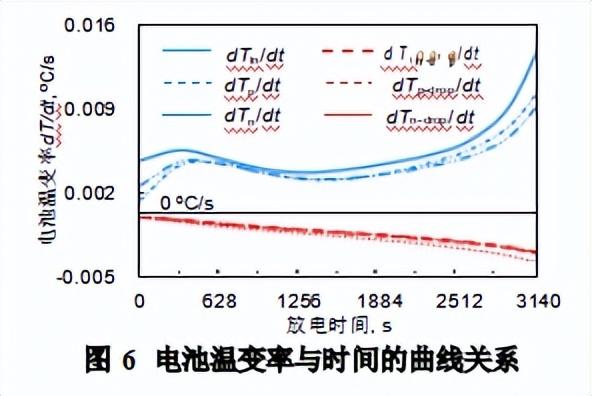
由图6,随放电时间,电池每一产热部件的温升率均呈“先快-后缓-再快”的变化趋势,在放电末期出现明显的“上翘”现象。温降率随放电时间向负向逐渐增大,这主要是由电池的温升逐渐增大所致。
结果与讨论
将电池总放电时间10等分,并将电池放电时间自始至末的等分节点1、2、3、……、11依次记为SOC值1.0、0.9、0.8、……、0。由此,得到电池在0°C环境下以1C倍率放电时其内芯、正/负极耳的生热率与SOC的曲线关系,如图7。
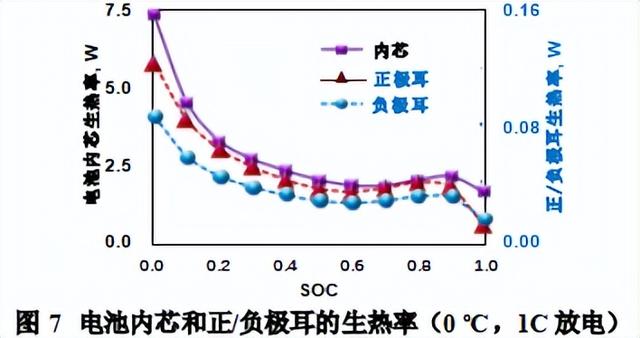
由图7,电池内芯和正/负极耳的生热率随SOC降低均呈“先快-后缓-再快”的变化趋势,尤其在放电末期增大较明显。该图亦显示,在该工况下该电池内芯的生热率占主导优势,占总生热率的96.9%,其正/负极耳生热率仅占3.1%;其中,电池正极耳的生热率较负极耳大,这主要是受其材质影响。
依照上述测试方案,本文测试了该电池在其它温度工况如-20ºC、-10ºC、10ºC、20ºC和30ºC下1C倍率放电,以及在30ºC下以3C、5C、7C和9C高倍率放电时的生热特性,并对比了其内芯和正/负极耳在不同工作温度和工作电流下的最大温升幅度和放电容量,如图8。
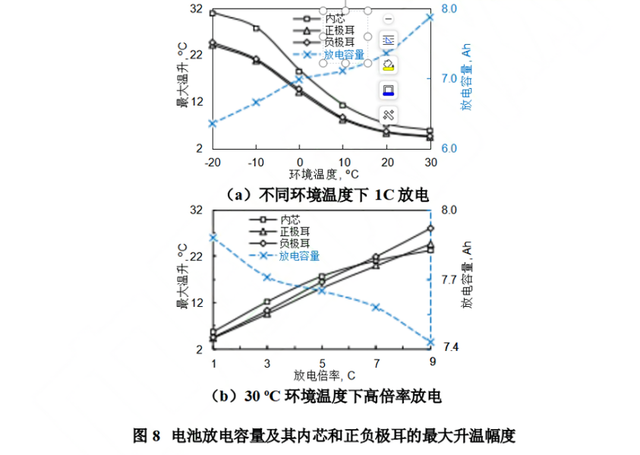
由图8(a),电池的温升幅度随工作温度的降低而增大,放电容量随工作温度的降低而降低,当环境温度为-20ºC时,电池放出的容量不及额定容量的80%。
由图8(b),电池的温升幅度随工作电流的增大而增大,放电容量随工作电流的增大而降低,当电池以9C倍率工作时,只放出了额定容量的92%。对比电池内芯和极耳的温升,发现当其以1C倍率工作时,极耳温升明显低于内芯温升,且负极耳温升较大。
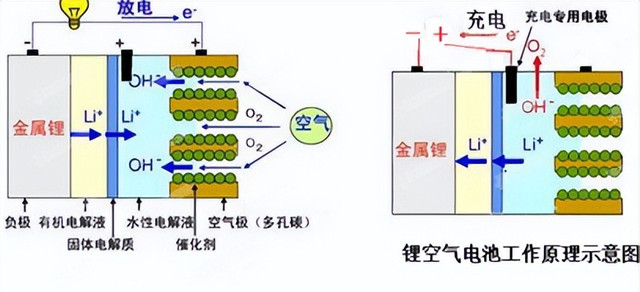
当电池在30ºC环境温度下高倍率放电时,其内芯温升与极耳的温升相差较小,且工作电流越大,电池极耳的温升增大越明显,尤其当放电倍率大于5C时,电池极耳温升大于内芯温升,这主要是因电池极耳的生热率随工作电流的增大而增大,当其单位体积生热率大于内芯时,其温升幅度亦大于内芯。
由图8还可知电池负极耳的温升幅度大于正极耳,而图7却显示电池负极耳的生热率小于正极耳,原因为电池负极耳材质为铅黄铜,其比热容较材质为不锈钢304的正极耳低,从而较低的生热率将引起负极耳较大的温度变化。
依据上述分析,图9展示了电池总生热率(内芯和正/负极耳)与SOC的曲线关系。
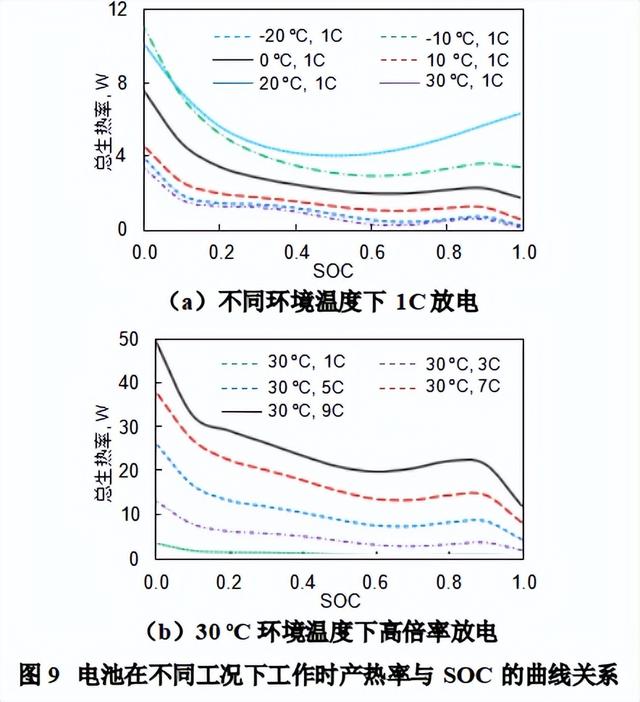
由图9(a),当电池以1C倍率工作时,其生热率随工作温度的降低而增大,主要原因为,工作温度越低电池的内阻越大,反应产生的焦耳热越多。由图9(b),当电池在30ºC下高倍率放电时,其生热率随工作电流的增大而增大,主要原因为,电池生热率与工作电流的平方近似成正比。
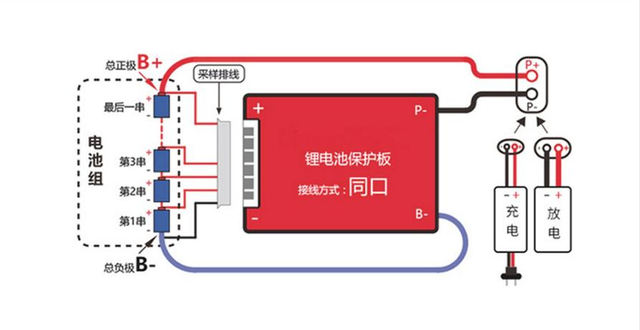
由图还发现,在每一工况下电池在放电末期的生热率均出现明显的“上翘”现象,这主要由其内阻在放电末期增大较多所致。
对图9中电池生热率与SOC(取值0至1.0)的关系进行回归分析,然后对拟合方程求积分,得电池的平均生热率:
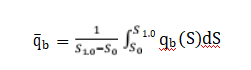
式中qb为电池的平均生热率,S代表SOC,S1.0和S0分别表示SOC值1.0和0。图10展示了电池平均生热率与温度、放电倍率的曲线关系。
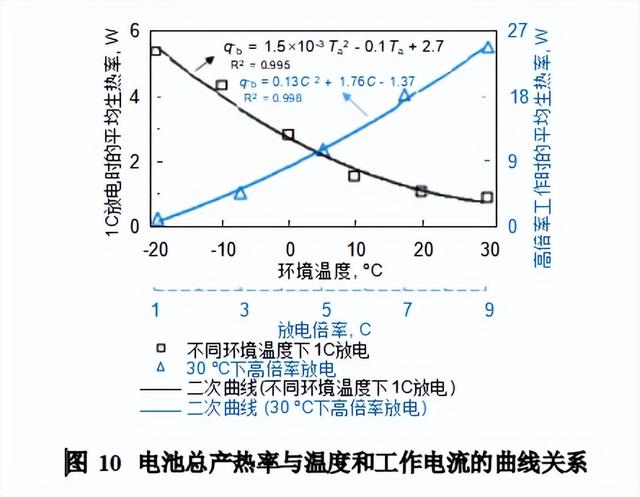
由图10,电池的平均生热率与温度、放电倍率均呈二次曲线关系。Lin等和Drake等均得到了类似趋势,但这两项研究分别采用ARC和热流计(HFM)测试电池的生热率,测试成本较高。
此次基于常规电池生热模型——Bernardi模型,检验本文“热补偿”产热测试方法的精度。
从电池工作过程中的微观产热层面出发,提出了主要包含焦耳热(qJoule)、熵变热(qentropy)、混合热(qmixing)和分解热(qdecom.)的电池生热模型(qb),其中后三项因占比很小可忽略其影响。最后Bernardi电池生热模型可简化为:

式中Rin为电池内阻,UOCV为电池开路电压,T为电池温度,单位K。
依此,分别基于HPPC(HybridPulsePowerCharacteristic,混合功率脉冲特性)方法和平衡电位法测试电池的内阻和熵变系数,结果见图11。
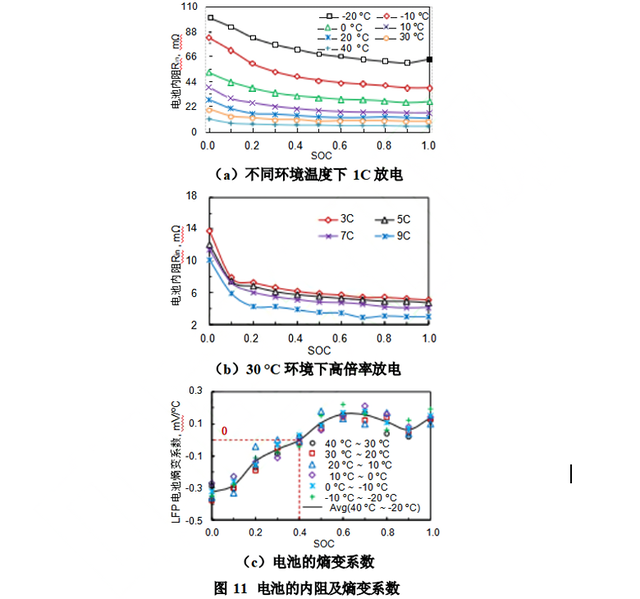
由图11(a、b),可知在每一环境温度及每一放电倍率下LFP电池内阻随SOC的降低而增大,原因为随着放电的进行锂离子Li+逐渐从电池石墨负极中脱嵌,扩散至正极,在放电中前期正极的Li+浓度较低,离子间的排斥力较小,Li+完成脱嵌-扩散-嵌入的阻力较小,在放电末期电池正极的锂离子浓度较高,离子间的排斥力较大,使Li+嵌入正极的阻力增大,宏观反映为电池内阻增大。
由图还可知,在每一SOC(10等分点)下LFP电池内阻随工作温度及放电倍率的降低而增大,前者原因为LFP电池的电解液是由锂盐电解质和有机溶剂组成,锂盐电解质在有机溶液中的溶解度随温度的降低而减小,溶解度减小时其输运电荷的离子数目将减少,使电解液的电导率降低。
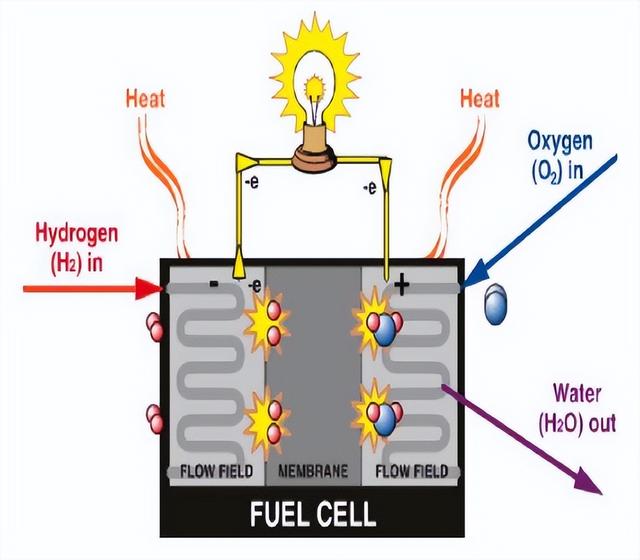
此外有机溶剂的粘稠度随温度的降低而增大,粘度增大将导致离子扩散速率减慢,如上因素使电池内阻因温度的降低而增大;后者原因为锂离子电池的极化电位随放电倍率的增大而增大,而极化内阻随放电倍率的变化关系与极化电位随放电倍率的变化关系相反,该现象可由Tafel方程解释。
由图11(c),当SOC为0.4时,LFP电池的熵变系数dUOCV/dT接近0;当SOC约在1.0~0.4区间时,dUOCV/dT大于0,此时LFP电池的可逆热为吸热;
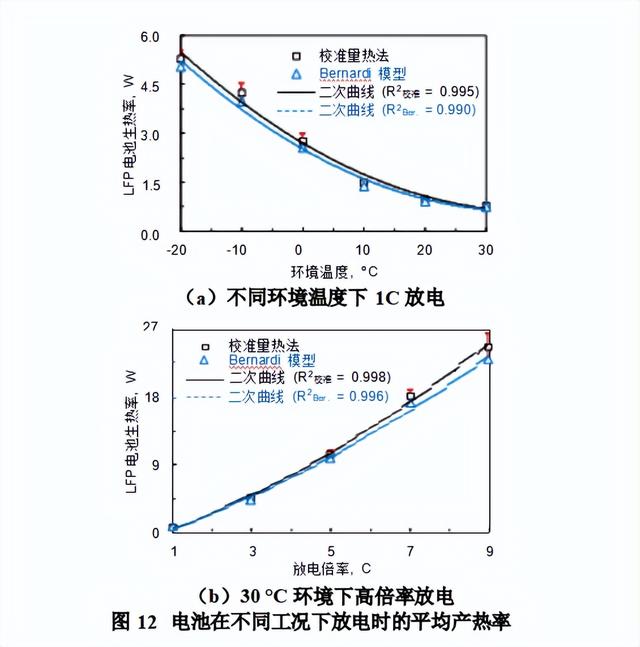
由图12,锂离子电池的平均生热率随温度的降低而增大,随放电倍率的增大而增大,与二者均呈二次曲线关系。基于本文提出的校准量热法的测算结果与基于Bernardi模型的测算结果相近。经比较,最大偏差5.7%。
该分析表明,我们提出的热补偿产热率测试方法是有效的,造成偏差的原因主要由测试仪器和热电偶的精度,以及电池极耳沿引线的热量损失和人为因素等引起。
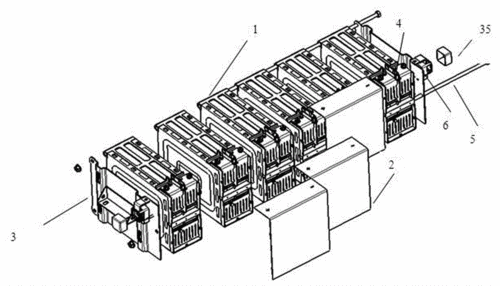
结语
我们提出了一种面向方形硬壳锂离子电池产热特性的新表征方法——热补偿法。开展实验探讨了一款方形电池的产热性能,并对热补偿法的准确性给予了验证。
电池生热率和温升随工作温度的降低而升高,随工作电流的降低而降低,工作效率随工作温度的增大和工作电流的降低而增大。并且电池的生热率与工作温度、工作电流分别呈二次曲线关系。
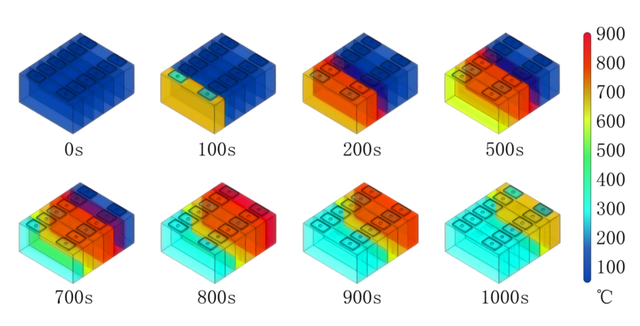
实验验证结果显示,采用这次方法测算电池生热率,其结果与基于传统Bernardi模型的测算结果吻合一致,最大误差不超过6%,准确性高我们提出的电池产热表征方法——热补偿法,具备成本低、操作灵活、效率高等优势,市场应用前景较好。