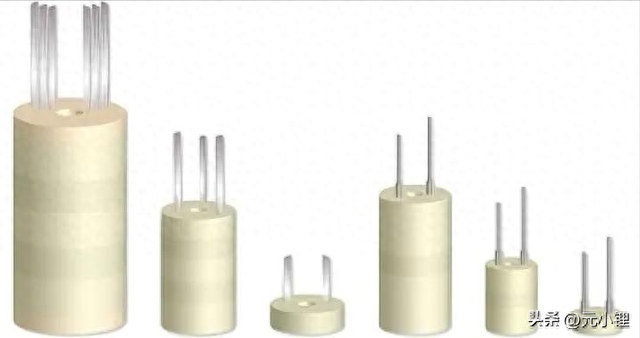
A样是原型设计,B样是工程验证,C样生产验证,D样量产前的最终验证。同时,小试、中试、量产是更通用的阶段划分,小试对应实验室阶段的初步测试,中试是放大生产,解决工艺问题,量产是正式生产。需要将这两个分类对应起来,比如小试可能对应A样和B样,中试对应C样,量产对应D样。
A样可能用于基本性能验证,B样进行可靠性和安全测试,C样验证生产工艺,D样确认量产能力。
锂离子电池开发中的A样、B样、C样、D样是基于APQP(产品质量先期策划)框架对产品成熟度的阶段划分,目的是确保产品从设计到量产的系统性验证。这一划分与传统的小试、中试、量产阶段相辅相成,但更聚焦于产品成熟度的递进验证。
基于APQP的产品成熟度阶段(A/B/C/D样)
阶段
目标
关键活动
与传统阶段的对应关系
A样
概念验证
- 实验室级样品- 验证电芯基础性能(如能量密度、循环寿命)- 材料选型、初步工艺设计
小试阶段
B样
工程验证
- 工程化设计定型- 全性能测试(安全、可靠性、环境适应性)- 初步工艺稳定性验证
小试向中试过渡
C样
生产验证
- 中试线或量产线试制- 验证生产工艺一致性(良率、设备匹配)- 客户联合测试(如车企的DV/PV试验)
中试阶段
D样
量产准备
- 量产工艺冻结- 完成PPAP(生产件批准程序)- 满足客户SOP节点要求
量产前最后验证
传统开发阶段(小试→中试→量产)
阶段
目标
核心任务
小试
技术可行性验证
- 实验室级样品试制- 材料/配方/结构优化
中试
工艺放大与稳定性验证
- 小批量产线试制(如百级电芯)- 工艺参数优化、设备调试
量产
规模化生产
- 千/万级产能爬坡- 持续改进(良率、成本控制)
关键差异与联系
APQP阶段更强调系统性验证:A/B/C/D样通过严格的测试节点(如DV/PV/PPAP)确保产品满足车规级要求(如ISO 26262、IATF 16949),而传统阶段更侧重技术实现。B样是核心分水岭:B样需通过针刺、过充、热失控等安全测试,是进入车企供应链的门槛;中试则需解决B样暴露的工艺问题(如极片对齐度、电解液浸润一致性)。D样与量产的关系:D样通过PPAP后,需完成OTS(工装样件认可)和SOP(量产启动),标志开发阶段结束。行业实践建议
车企客户需求驱动:若面向汽车领域,需严格遵循APQP节点(如A样对应RFQ阶段,D样对应SOP+90天)。材料/工艺风险前置:A样阶段需锁定关键材料(如正极/负极供应商),B样前完成电解液配方专利布局。数据闭环迭代:中试阶段需通过MES系统采集数据,反向优化设计(如极片厚度公差对膨胀力的影响)。通过结合APQP框架与传统开发阶段,可系统性降低量产风险,缩短开发周期(通常12-24个月)。
锂离子电池开发从A样到D样的具体实施步骤分解,结合APQP流程与传统小试→中试→量产阶段的关键任务,适用于动力电池、储能电池等场景:
A样阶段(概念验证)目标:验证技术可行性,锁定核心设计方案。时间:3-6个月核心步骤:
需求输入:明确客户需求(如能量密度≥300Wh/kg、循环寿命>2000次)。确定法规/标准(UN38.3、GB 38031、UL 2580)。材料选型与配方开发:正极(NCM/NCA/LFP)、负极(石墨/硅碳)、电解液配方筛选。关键材料供应商锁定(如隔膜用恩捷/星源材质)。实验室级样品试制:手工或小试线制作5-20个电芯(如18650或软包)。测试基础性能:容量、内阻、首次效率、高温存储膨胀率。概念验证(POC):通过针刺、过充、热箱等安全测试(参考国标要求)。提交《A样测试报告》,召开阶段评审会(Gate Review)。交付物:电芯设计图纸(Cell Drawing)、材料清单(BOM)、DFMEA初版。B样阶段(工程验证)目标:完成工程化设计,通过全性能测试。时间:6-9个月核心步骤:
工程设计定型:冻结电芯结构(如卷绕/叠片工艺)、极片参数(面密度、压实密度)。完成电池包PACK设计(模组结构、热管理方案)。工程样件(EVB)试制:小批量产线生产(100-500个电芯),验证工艺一致性(如极片对齐度±0.2mm)。全性能测试:安全测试:针刺、挤压、热失控蔓延(参照GB 38031)。可靠性测试:循环寿命(25℃/45℃)、日历寿命(SOC 80%存储)。环境测试:高低温充放电(-30℃~60℃)、振动/冲击(IP67)。设计优化迭代:根据测试结果调整设计(如增加涂层改善析锂问题)。完成DFMEA/PFMEA更新,冻结《产品规格书》。交付物:DV(Design Validation)报告、PPAP Level 3文件、工艺流程图(Process Flow)。C样阶段(生产验证)目标:验证量产工艺,满足客户PV测试要求。时间:3-6个月核心步骤:
中试线试产:使用量产设备(如涂布机、卷绕机)生产1000-5000个电芯。优化工艺参数(如涂布速度、烘干温度、注液量)。一致性验证:统计关键参数CPK(如容量CPK≥1.33,厚度公差±0.1mm)。分析批次良率(目标≥95%),解决电解液浸润不均等缺陷。客户联合测试(PV):交付客户进行整车级测试(如充放电策略、BMS匹配)。通过车企要求的滥用测试(如海水浸泡、火烧试验)。供应链准备:与供应商签订量产协议(如电解液月供10吨)。完成原材料PPAP(如正极材料的批次一致性认证)。交付物:PV(Process Validation)报告、量产工艺文件(SOP)、MSA(测量系统分析)报告。D样阶段(量产准备)目标:冻结工艺,完成PPAP,启动量产。时间:1-3个月核心步骤:
量产线试运行(OTS):在量产线连续生产3-5个批次(每批≥1000个电芯)。验证设备OEE(综合效率≥85%)、产能爬坡计划。PPAP提交:提交PSW(零件提交保证书)、全尺寸报告、控制计划(Control Plan)。客户审核(如车企SQE现场验厂)。量产启动(SOP):完成工艺冻结(如化成制度、分容参数)。启动首批量产订单(如交付车企1000套电池包)。持续改进:监控初期量产问题(如焊接不良率),启动8D整改。优化成本(如降低隔膜厚度、提升涂布利用率)。交付物:PPAP批准文件、量产控制计划、SOP启动确认书。关键工具与方法APQP核心工具:FMEA(失效模式分析)、SPC(统计过程控制)、MSA(测量系统分析)。测试标准:电芯级别:GB 38031、IEC 62660;系统级别:ISO 26262(功能安全)。数据管理:使用MES系统追踪电芯生产数据(如电压曲线、分容结果)。建立大数据平台分析早期失效模式(如微短路预警)。风险控制要点A样阶段:避免过早锁定不可量产的材料(如超高镍正极)。B样阶段:重点解决热失控问题(如陶瓷涂层隔膜导入)。C样阶段:预防工艺放大导致的界面副反应(如注液后静置时间不足)。D样阶段:确保供应链弹性(如电解液添加剂备选供应商)。通过以上步骤,锂离子电池开发周期可控制在18-24个月,满足车企或储能客户对质量、成本和交付时间的严苛要求。