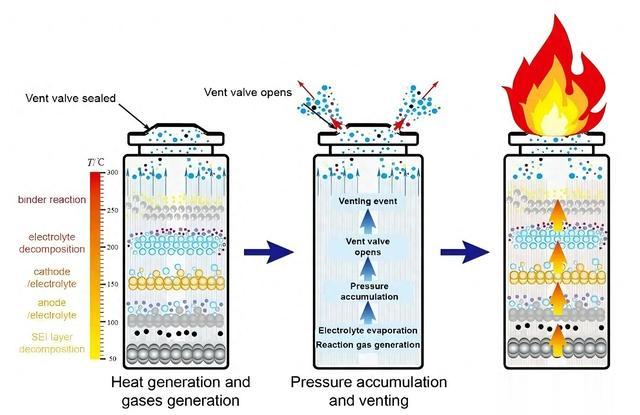
温度对锂电池性能的影响,包括充放电效率、能量密度和功率输出。高温和低温的不同影响,比如高温可能导致热失控,而低温会降低离子传输速率,影响性能。
寿命衰减方面。温度对循环寿命的影响很大,特别是高温加速副反应,导致容量衰减。不同温度下的存储寿命也是重点,比如长期高温存放导致的不可逆损伤。正负极材料、电解液和隔膜在不同温度下的表现,比如钴酸锂在高温下的不稳定性,石墨负极的锂析出问题。

锂电池系统的生命线
在锂电池技术快速发展的今天,温度管理已成为决定电池系统性能、安全与寿命的核心要素。作为锂电开发者,我们始终在与热力学第二定律进行博弈:既要抑制电池工作时的热量积累,又要克服低温环境下的性能衰减。这种看似矛盾的需求背后,是锂离子在电极间穿梭时引发的复杂热效应。
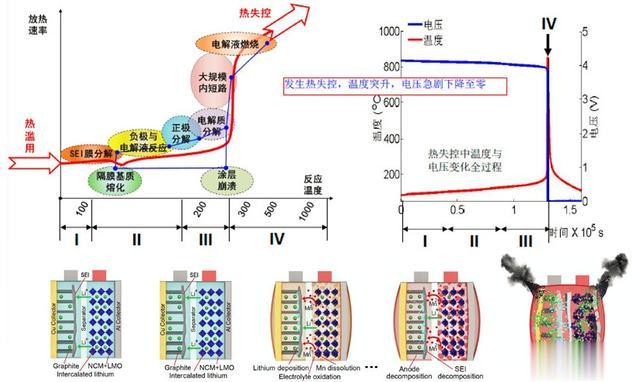
一、温度对电芯性能的动力学影响
锂离子在石墨负极中的嵌入反应存在显著的活化能垒(约50 kJ/mol),当温度从25℃降至0℃时,锂离子扩散系数降低约两个数量级,导致电荷转移阻抗(Rct)从20 mΩ激增至150 mΩ。这种动力学限制在充电末期尤为突出,当负极电位接近金属锂沉积电位时,低温环境会使锂沉积的临界电流密度从常温下的1.5C骤降至0.3C以下。
高温环境则引发相反的热失控风险。钴酸锂正极在55℃时晶格氧的析出速率提升3倍,三元材料(NCM811)在60℃下的相变活化能降低40%。此时电解液的氧化分解电流密度达到常温的5倍,产生的CO和CH4等气体使电池内压快速上升。实验数据显示,每升高10℃,电解液的分解速率提升2.5倍,这种Arrhenius型加速效应将电池推向热失控的临界点。
温度梯度引发的性能离散化更值得警惕。在1.5Ah的18650电芯中,轴向温度差超过5℃时,局部电流密度差异可达30%,这种不均匀性在模组层面会被几何级放大。某动力电池包的实测数据显示,当模组表面温差达到8℃时,单体容量离散度从2%扩大至15%,直接导致系统可用容量衰减12%。
二、材料层面的热响应机制

磷酸铁锂(LFP)正极的橄榄石结构在高温下展现出独特稳定性,其分解温度高达400℃,远高于三元材料的220℃。但这种稳定性是以牺牲动力学性能为代价的,LFP材料在-20℃时的有效容量仅为常温的65%,而NCM523仍能保持82%的容量。这种差异源于不同晶体结构中锂离子迁移路径的势垒差异:LFP的一维扩散通道对温度更敏感。
石墨负极的锂沉积存在温度阈值效应。当温度低于10℃时,SEI膜的锂离子透过率下降,导致沉积过电势超过150mV,此时即使以0.5C充电,锂枝晶成核概率也会增加5倍。最新的改性策略是在负极表面构建温度响应型SEI膜,当温度低于15℃时,膜内聚环氧乙烷链段结晶度升高,主动限制锂离子通量。
电解液体系的热稳定性呈现非线性特征。常规LiPF6基电解液在70℃时开始显著分解,而新型双氟磺酰亚胺锂(LiFSI)盐可将热分解温度提升至85℃。但高温下的副反应路径更为复杂,LiFSI在120℃时会发生自催化分解,释放的HF会加速正极材料溶解。这种矛盾特性要求开发者必须在热稳定性和副反应抑制间寻找平衡点。
三、热管理技术的创新方向
相变材料(PCM)的潜热利用正在突破传统边界。石蜡/膨胀石墨复合材料的热导率可达15 W/(m·K),是纯石蜡的30倍。当集成于21700电芯表面时,可在3C放电时将最高温度压制在45℃以下,且温度均匀性提升40%。更前沿的研发聚焦于动态相变材料,其相变温度可随SOC状态智能调节,在低SOC时降低相变点以增强散热,高SOC时升高相变点以抑制析锂。
拓扑优化的液冷板设计将流动传热效率推向极限。通过计算流体动力学(CFD)仿真获得的仿生流道结构,可使冷却液努塞尔数提升25%,压降降低40%。某款量产动力电池包的蛇形微通道液冷板,在25℃环温下可将电芯温差控制在±2℃内,且泵功损耗减少30%。这种结构创新配合乙二醇/水混合液的沸腾传热强化,使散热功率密度达到1500 W/kg。
热-电耦合控制算法正在重新定义BMS的智能边界。基于电化学-热耦合模型的状态估计器,可实时预测各区域的析热速率,并与模糊PID控制器联动调节冷却系统。某实验系统在应对US06工况时,温度控制精度达到±0.5℃,同时将能耗降低45%。更前沿的研究将深度学习融入热管理,通过LSTM网络预测未来30秒的热负荷变化,实现超前控制。
四、跨尺度热设计的系统整合
在材料-单体-模组-系统的多级传热链中,界面热阻管理是关键挑战。采用垂直石墨烯阵列的界面材料,可将电芯与冷却板间的接触热阻从30 mm²·K/W降至5 mm²·K/W。这种各向异性导热材料在厚度方向的热导率高达20 W/(m·K),而面内方向仅1.5 W/(m·K),有效抑制横向热扩散造成的温度梯度。
在极端环境适应性方面,自加热技术已实现突破。通过植入镍箔的感应加热方案,可在1分钟内将-30℃的电池加热至10℃,能耗仅为传统PTC加热的60%。更创新的方案是利用电芯内阻产热,通过高频脉冲电流在30秒内完成低温启动,这种自加热方式的热效率可达95%以上。