在汽车行业的发展进程中,新材料的应用一直是推动其不断进步的关键因素之一。我国汽车行业产能增长如骏马奔腾般迅猛,车用工程塑料产业也随之迎来了广阔的发展空间。如今,工程塑料正以一种势不可挡的姿态取代金属材料,从最初的装饰件逐渐迈向结构件与功能件的重要领域。而在众多工程塑料中,PA(聚酰胺)材料凭借其卓越的性能,在汽车行业中崭露头角,尤其是 PA6、PA66、PA12 等尼龙材料,正发挥着越来越重要的作用。
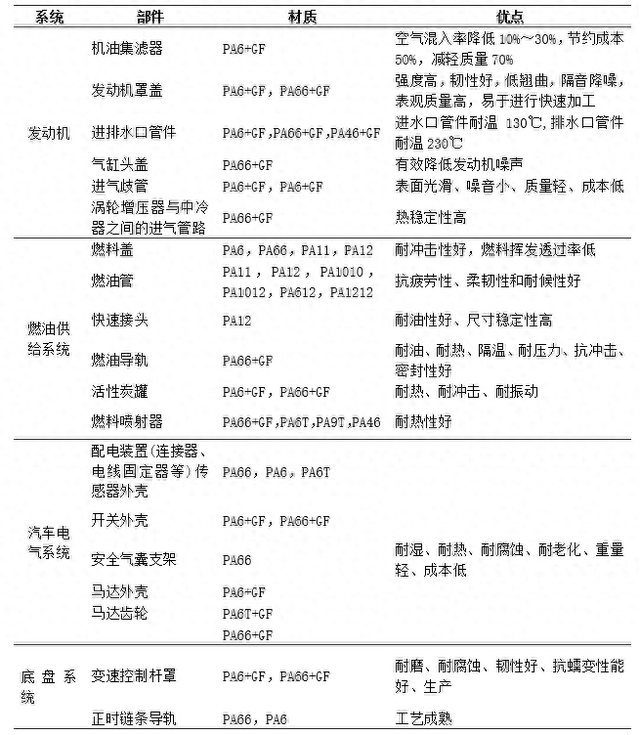
(PA在汽车中的应用)
PA 作为一种出类拔萃的工程塑料,其化学性能之稳定令人赞叹,对润滑油和汽油有着出色的抵抗能力。在当今节能减排的大社会背景下,PA 材料的优势愈发凸显。它在轻量化、耐热性、耐油性、阻燃性等多个方面的出色表现,使得其在汽车行业中的渗透率如同旭日东升般逐步提高。目前,PA 材料已经广泛应用于汽车发动机系统、电气系统、底盘系统等多个关键部位,其中 PA6 和 PA66 的用量更是占据了各类 PA 材料总量的 90% 以上,而 PA11 和 PA12 也凭借良好的柔韧性、耐腐蚀性、耐油性和尺寸稳定性,在燃油管、燃料盖、制动管等部件中获得了广泛的认可和应用。
先来看 PA6 材料在汽车中的典型应用。电池箱体作为保护和支撑动力电池模组、电池温控系统、电池管理系统等部件的关键组件,其重要性不言而喻。它肩负着防止动力电池系统在外界冲击或机械应力下受损的重任,因此对冲击强度、拉伸强度等力学性能有着极高的要求。目前,部分电池箱体选用了 PA 材料,其中又以 PA6 材料居多。然而,新能源汽车对电池箱体材料的阻燃性能要求极为严苛,未改性的 PA6 材料极限氧指数一般仅在 20%~22%,阻燃等级仅能达到 UL94 V-2 级,远远无法满足需求,必须进行阻燃改性。在阻燃剂的选择上,虽然卤系、磷系、氮系等多种类型都可用于 PA6 的阻燃,但卤系阻燃剂因燃烧时会产生腐蚀性气体及致癌烟雾,自 2003 年初欧盟发布相关指令后,其使用受到了严格限制。好在众多工程塑料公司积极投入研发,如朗盛集团推出的 3 种以 PA6 为基体的 Tepex 材料,就凭借着较高的纤维量,不仅具备极高的刚度、强度和能量吸收水平,还拥有 UL94 V-0 等级的阻燃特性。其中,Tepexdynalite102fr-RG600 (x)/47% 采用粗纱玻璃纤维增强,纤维呈多轴排列,不仅阻燃效果出色,还能精确匹配部件中的负载路径,可应用于新能源汽车电池箱体的控制单元外壳、隔板、盖板等高压部件。此外,长玻纤增强 PA6 在汽车结构件中的应用也日益广泛,玻纤作为增强骨架贯穿于 PA6 基体,能有效增强塑料制品的抗冲击性能、抗蠕变性能和尺寸稳定性,以仪表台横梁为例,长玻纤增强 PA6 仪表台横梁不仅能满足刚性和强度要求,还具有优秀的抗蠕变性能、耐疲劳性能以及出色的高低温抗冲击性能,全塑仪表台横梁的设计更是提升了生产效率,助力实现轻量化与 NVH 目标。
PA12 材料在汽车领域也有着独特的应用价值。在传统的内燃机汽车领域,杜邦、Arkema、Basf 等大型工程塑料公司开发的不同耐温等级的 PA12 材料,被广泛应用于油箱注油管、燃油输油管、曲轴箱通风管、发动机进气管、真空制动管等油液与气体管路之中。不过,PA12 的耐高温性能存在一定的局限性,在工作温度较高的管路中无法长期使用,例如内燃机汽车的发动机冷却水管一般不会选用 PA12 管路。但在新能源汽车领域,其电机冷却系统工作温度一般低于 80℃,电池冷却系统工作温度一般低于 60℃,PA12 材质完全能够满足耐温要求。与橡胶管路相比,PA12 管路优势明显,它不仅密度更低(PA12 的密度为 1.02g/cm³,而 EPDM 橡胶密度为 1.1~1.2g/cm³),管壁相对较薄(以内径 15~18mm 的管路为例,PA12 水管仅为 1.25~1.5mm,而 EPDM 橡胶管路的壁厚一般为 3.5~4mm),能使管路减重 65%,如广州汽车集团股份有限公司某车型采用 PA12 管路方案,管路系统质量实际减轻了 56%。而且,PA12 管路刚度较高,可一体成型制造完整水管,减少零件数量,提高系统可靠性,该车型采用 PA12 管路方案后,管路系统中的零件数量减少了 77%。此外,众多研究者还开展了满足特定场景需求的 PA12 管路研究,如日本 Toray 公司和 Polyplastics-Evonik 公司合作研发的三层挤压管,外层 PA12 材料和内层的聚苯硫醚 PPS 树脂材料用特殊黏结剂粘合,可承受 130℃高温,具有良好的耐水解性和耐热性,适用于较高温度要求的汽车冷却管路系统;专家张颖研发的满足燃油管路低渗透标准要求的 PA12 对称结构五层管复合管材以及燃油管路总成系统,也解决了混合燃油对燃油管路耐渗透性的更高要求。
PA66 材料在汽车行业同样有着亮眼的表现。在 “以塑代钢” 的汽车轻量化大趋势下,PA66 无论是在传统内燃机汽车还是新能源汽车领域,都为实现低碳排放的社会愿景贡献了突出价值。在零部件生产过程中,PA66 凭借着十倍于 PA6 的结晶速度,可在模具中快速成型,大大提高了生产效率。其性能相较于 PA6 更为出色,具有更高的尺寸稳定性、更低的吸水率和更高的熔点,被广泛应用于汽车各系统。以进气歧管为例,早期内燃机汽车进气歧管多选用 PA6 材料,随着集成增压器的应用和发动机的紧凑化,进气歧管的耐温要求从 130℃上升到 200℃,主机厂逐渐倾向于选择更高熔点的 PA66 来实现性能升级。PA66 的另一个典型应用是发动机支架或者驱动电机支架,PA66 玻纤增强产品应用于此,不仅能有效降低发动机或驱动电机的振动和噪声,还因为其能耐受 160~180℃的烤漆温度,集成于汽车白车身内部时,有助于增强车身力学性能,在车辆碰撞时吸收碰撞能量,保护司乘人员和动力电池,同时还能使车身减重超过 30%,提高车辆的操控性和续航里程。在新型 PA66 材料的研究方面,也取得了诸多成果,如无卤阻燃增强 PA66/PA6 合金成为了高压连接器材料的有前景替代技术方案,专家叶士兵等研究了不同比例下该合金的性能变化;刘颖等对不同纤维含量的短切碳纤维增强 PA66 力学性能进行研究,发现其应用于轻量化电池箱时,质量减轻 84%,最大应力减小 30%~50%,碳纤维含量对箱体最大位移影响较大;陆大光等制备了适用于汽车轧带使用的耐寒增韧改性 PA66 材料;张松峰等通过共混改性开发了以 PA66 为主体的汽车用冷却水管,其爆破强度大于 2.6MPa,材料成本降低了 40%。
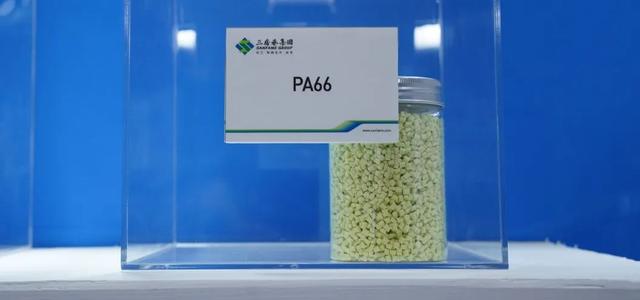
(图源:三房巷)
从市场用量来看,车辆塑料用量在一定程度上可作为衡量汽车设计与制造水平高低的标志。目前发达国家内燃机汽车单台塑料用量约为 150kg,其中 PA 所占比例约为 20%。而国内内燃机汽车单台 PA 用量目前约为 8kg,预计 2025 年将达到 15kg,2030 年有望增至 30kg。对于新能源汽车,参考特斯拉 Model3 等车型,预估 2030 年新能源汽车单台 PA 用量可以达到 50kg。从汽车销量数据来看,中国乘用车市场信息联席会数据显示,2022 年全国内燃机汽车销量为 1486.8 万辆,同比减少了 230.2 万辆,内燃机汽车正逐渐失去市场份额,国内外车企大多计划在 2030 年左右停止研发内燃机汽车,此后内燃机汽车将逐步退出历史舞台。而新能源汽车市场则呈现出蓬勃发展的态势,中国科学院院士欧阳明高预计,2025 年全国新能源汽车销量将达到 700 万~900 万辆,2030 年将达到 1700 万~1900 万辆。华安证券研究所预估,2030 年车用 PA 材料用量将达到 144 万吨。
发动机技术的不断进步、汽车新能源化的转型以及汽车轻量化的发展,不仅有效促进了节能减排水平和社会运行效率的提升,更为 PA 等工程塑料的应用带来了巨大的增量市场。在可以预见的未来,汽车行业对 PA 材料的需求必将持续增加,PA 材料产业已然驶入了高速发展的快车道。随着技术的不断创新和突破,PA6、PA66、PA12 等尼龙材料在汽车行业的应用前景将更加广阔,它们也必将在汽车行业的发展中书写更加辉煌的篇章。
参考资料:尼龙材料在汽车行业的应用及展望,张坤等网络资料