船越造越大,港越建越贵。随着集装箱船尺寸膨胀,码头不得不超前建设,盐田港、宁波舟山港都规划建设了可靠泊3.2万TEU巨型船舶的超大型集装箱码头,可能有更多巨型港口投资正在路上。
把港口造大是老路子,也有一些码头设计另辟蹊径,号称要给码头带来革命。
一、浮动码头
浮动码头,顾名思义,就是漂在海上的码头,本身并不新鲜,浮动LNG码头、离岸作业平台等都有成熟经验。但浮动式的大型集装箱码头,还没有吃螃蟹的人。
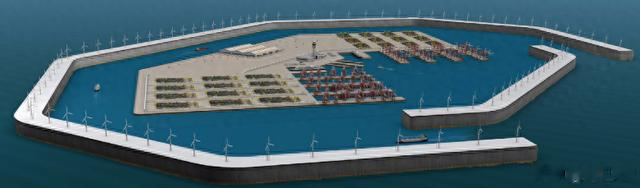
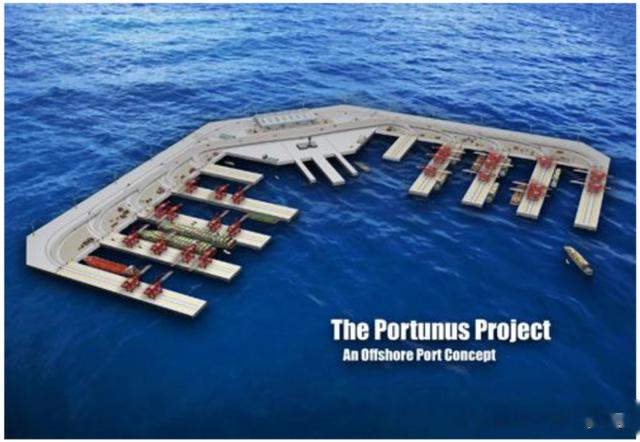
类似的创意倒是频出不绝。多年前,美国Lawrence Livermore国家实验室就推出了梭子蟹计划(PORTNUS Project),设计了一种“美味”的浮动码头。
梭子蟹码头的初衷是保护国土安全,锚泊在离岸几十公里处,以便在离岸港口检查货物。梭子蟹码头是转运码头,可在36小时内同时接卸8艘18,000TEU级别大型箱船。该码头计划采用AGV、三小车岸桥等先进技术,从经济角度看,6座梭子蟹码头造价约600亿美元,每年收益约53亿美元。遗憾的是,这种设计没有商业化的讨论。
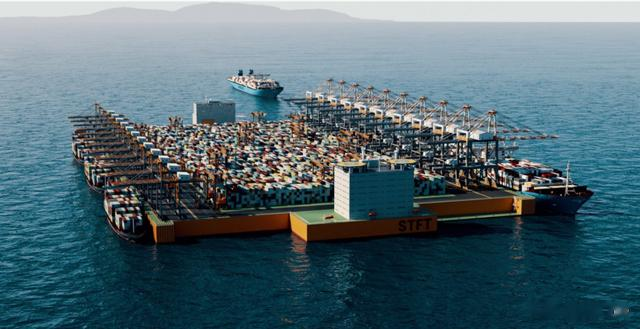
近年来讨论较多的是STFT,自2015年以来,SEA Technology就在开发这种浮动式的集装箱转运码头,以减少船舶大型化带来的高昂港口建设成本。
STFT是大型转运码头,采用模块化设计,将3个或4个船体焊接在一起,STFT平台面积可达21.5万平方米,可堆存6万个集装箱最大年吞吐量可达到500万-600万TEU。由于锚泊在30-40米水深的海上,STFT不用操心水深条件和疏浚成本,建设周期短;也不必担心船舶大小,能够接卸30000TEU级别的巨型箱船,还能通过焊接更多模块扩展码头大小。但是STFT需要考虑风浪及恶劣天气,长期维护成本可能更高(如腐蚀和金属疲劳)。
根据测算,部署一座STFT的总成本为25亿美元,如果年吞吐量达到80万TEU,就可以覆盖成本甚至有利可图。当然,在巨额投资面前,行业始终谨慎。
二、坞式码头
浮动码头多少有点不接“地气”,有的设计则在土地上上做文章。既然船舶只能一边靠住码头,桥吊在一侧作业,那么把船“夹住”,两侧同时作业,是不是就能效率翻倍呢?坞式码头就源自这种想法,码头像船坞一样,船舶进港后,两侧的桥吊同时进行装卸作业。
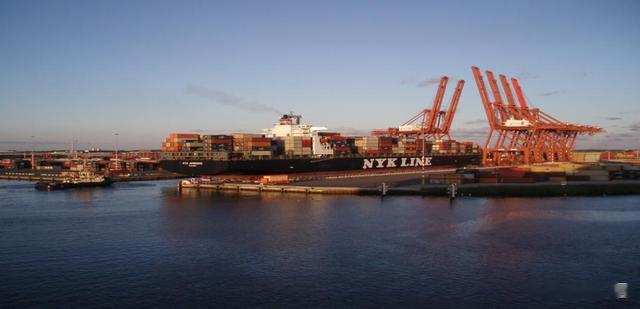
这种设计不只是纸上谈兵,2001年,码头运营商Ceres Terminals就在阿姆斯特丹港Paragon码头建立了一个坞式泊位,该泊位长400米,宽57米,在泊位两侧放置9台岸桥同时作业,理论上能做到每小时300个move,专为6000TEU及以上的新一代集装箱船设计。但是,需求不足等原因使得该码头没能成功,几度易手后最终关停。
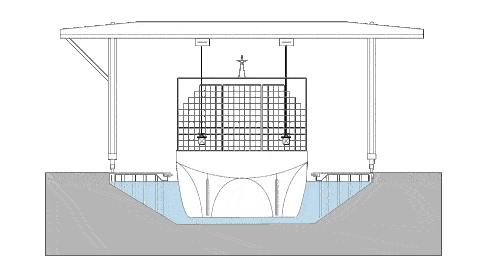
近年来,当最大集装箱船级别来到24000TEU,科尼又复活了坞式码头设计。除了船坞式的码头布局,设施设备也进行了革新,包括弃用岸桥,使用横跨码头两端的大型龙门吊来进行装卸,后方使用立体堆场等(详见“不用岸桥的码头,每天能做到10000个move?”)
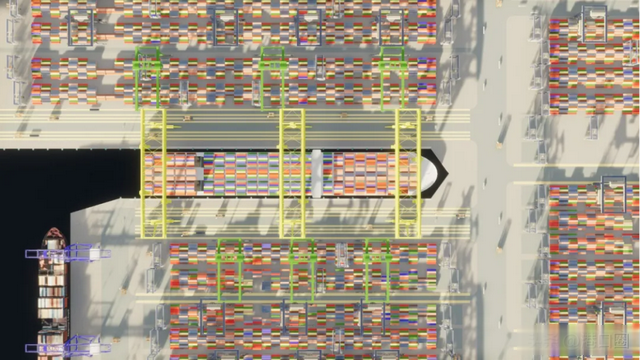
每台龙门吊相当于2台双小车岸桥,性能加倍,在装卸20000TEU级的大船时,4台龙门吊可以在39个小时内搬运14000个箱子,大大减少大型船舶在港口的周转时间,让码头效率跟上集装箱船大型化的脚步。
三、做加法或做减法
除了在岸线上创新,后方堆场、设备也是突破口。


2011年,新加坡海事及港务局举办了“下一代集装箱港口”挑战,新加坡国立大学、上海海事大学、振华重工组团打造的“SINGA Port”拔得头筹。SINGA Port的特色是给堆场做加法,设计了双层堆场。
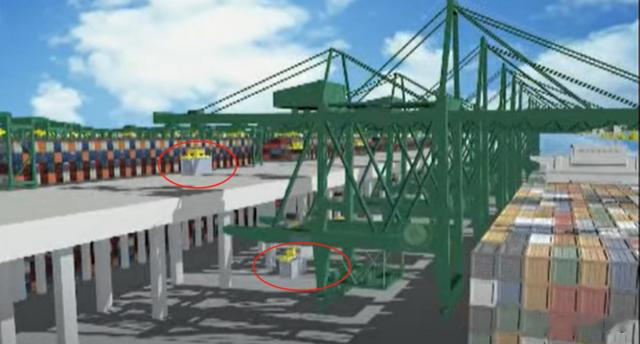
堆场上再叠一个堆场,取放箱的面积相当于翻倍,以针对新加坡土地不足的问题。同时,岸边作业的岸桥采用三小车设计,可以同时在上层和下层堆场取放箱,大大减少集装箱周转时间,一小时内可移动152TEU。不过,如今还在建设中的大士港,依然采用了较为传统的码头设计。
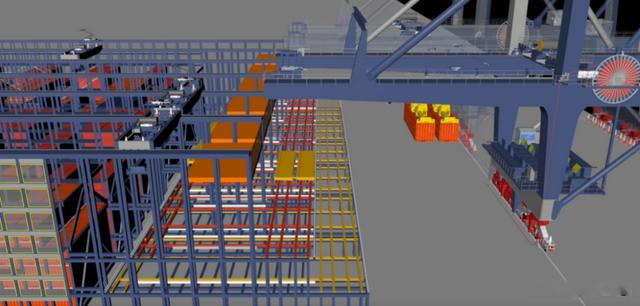
有加法型设计,也有减法型创意。在自动化集装箱码头的各个环节中,水平运输最为复杂。青岛港曾推出过一种设计,直接减掉了港内水平运输环节,而是使用了一种叫做R-AGV的立体轨道吊,岸桥小车直接在堆场轨道吊外的平台上取放箱,自动化轨道吊负责将箱子送进自动化的立体堆场。
由于是立体堆场,轨道吊也不再移动,而是由吊具在连续不断的箱区中接力吊箱,最终与外集卡对接。立体堆场的顶部则铺满了光伏电池,用来节能减排。与传统的全自动化码头相比,这种设计的海侧装卸船效率能提高50%以上,陆侧疏港效率提高100%以上。只不过,如今主流的发展方向是有人、无人集卡混行,这一创意很难成行。
港口圈(ID:gangkouquan)认为,在相对保守的港航业,革新性的设计很难落地。船公司在港口装卸市场的话语权更大,他们只是一味把船越造越大,码头方要考虑的地方就太多了。不过,当全球头部码头运营商中船公司的比例越来越高,船公司也该给码头建设带来一些新东西了。