方法研究
①从流程上入手。可以发现工艺流程中是否存在不经济、不合理、停滞和等待等现象;
②从工序上入手。可以发现加工顺序是否合理,流程是否畅通,设备配备是否恰当,搬运方法是否合理;
③从作业入手。可以发现工序中的某项作业是否一定必要,是否可以取消,是否还有更好的方法
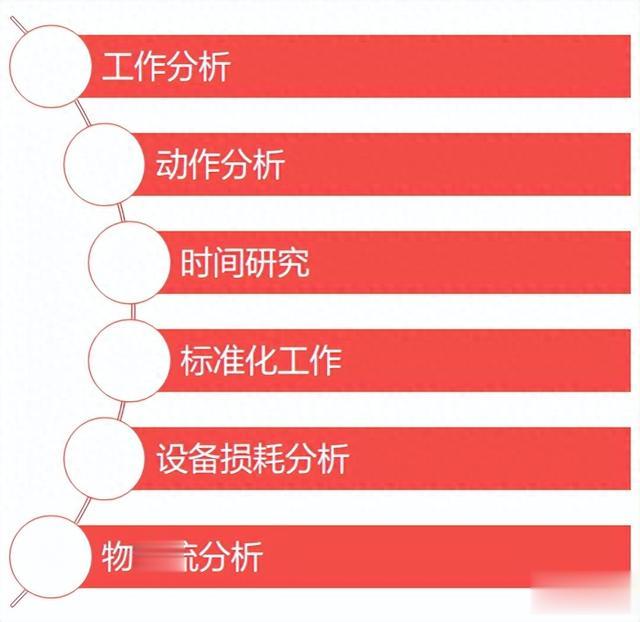
工作分析
方法一:工作分析单元
下图这五个基本层次统称为工作分析单元。
当然,所使用的分析单元的具体层次取决于所要分析的工作。通常,建议持续改善的实践者以工作研究为目的,首先学会识别分析的不同层次——无论是为了描述整体工作还是为了更细致的观察,每一层次都应有明确的目的。
一般建议使用中间层的主要步骤或工作要素作为工作分析的起点。这是因为,在大多数情况下,这一层次当中的动作浪费、效率缺乏、步骤的唯度等会变得明显。
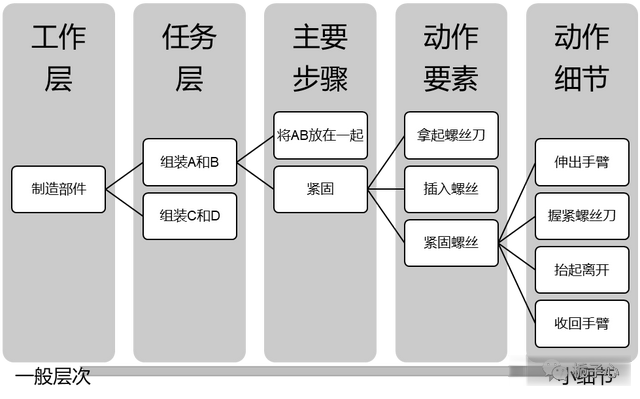
方法二:TWI工作方法分析
英文原意为:在企业内部(不脱产)的培训
TWI是第二次世界大战时,由美国军方的技术人员开发并普及的一种训练方式。
自第二次世界大战后导入日本以来至今为止,除广泛应用于生产部门及服务部门以外,也被活用于各行各业的职场,且均取得了巨大的成果。
当中所使用的基本技术可以简单称为工作分解法,它由简单的三栏表格构成。
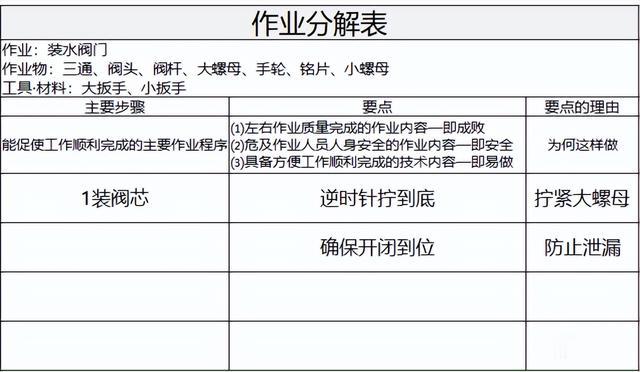
方法三:丰田工作分析
通过5W1H与ECRS进行工作分析的理念一直是丰田内部持续改善课程的主要内容。丰田对其所做的修正包括使工作分析单元更加具体化以及对用于分析和产生创意的表格形式进行改变。
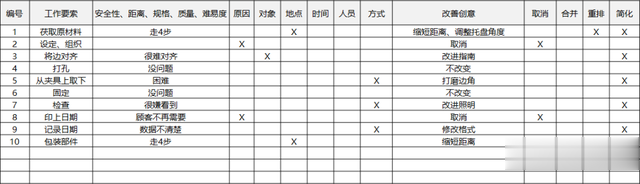
动作分析
作业分析
通过程序分析,实现了整个生产作业(工作)系统及其程序的优化,这就为各个操作(工作)岗位的
优化打下了基础,研究并解决每个操作(工作)岗位的作业优化和标准化,这便是作业分析的任务。
①含义:通过以人为主的工序的详细研究,达到使作业的结构合理、作业者的劳动强度减轻、作业的时间消耗减少、保证生产质量、提高作业效率的目的。
②作业分析的特征
•把详细分析、改进一个工作地的作业作为分析与研究对象;
•用程序分析基本手法,对以人为主体的作业系统进行分析;
•分析内容是影响该项作业效率和作业质量的各种因素,通常包括作业方法、原材料、设备与工装、作业环境条件等。
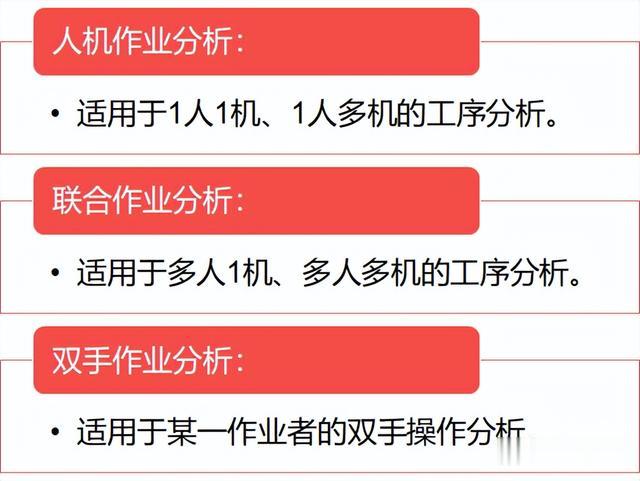
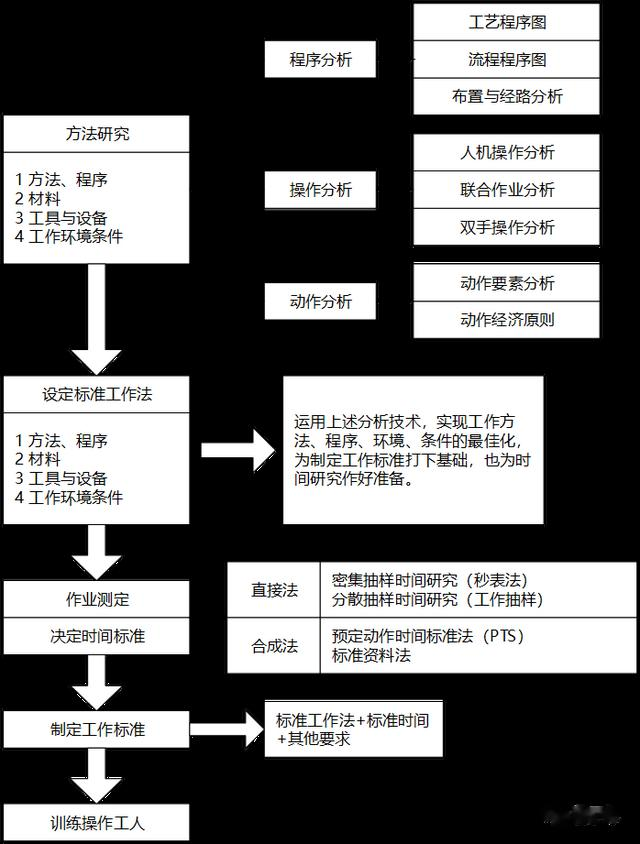
工作研究基本框架
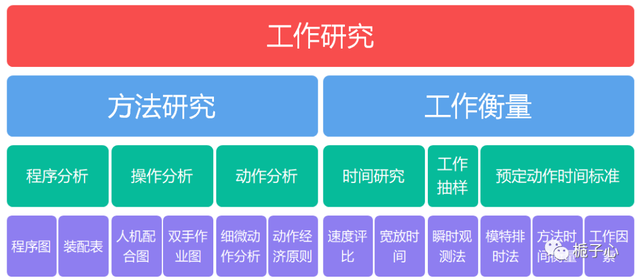
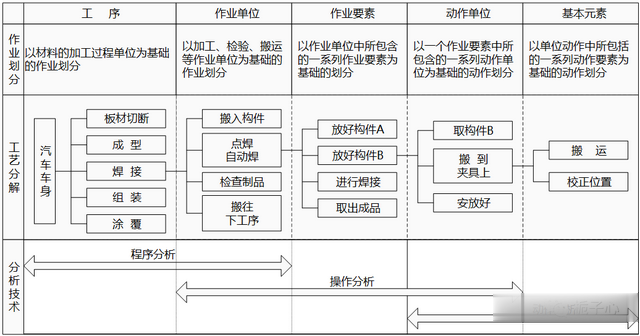
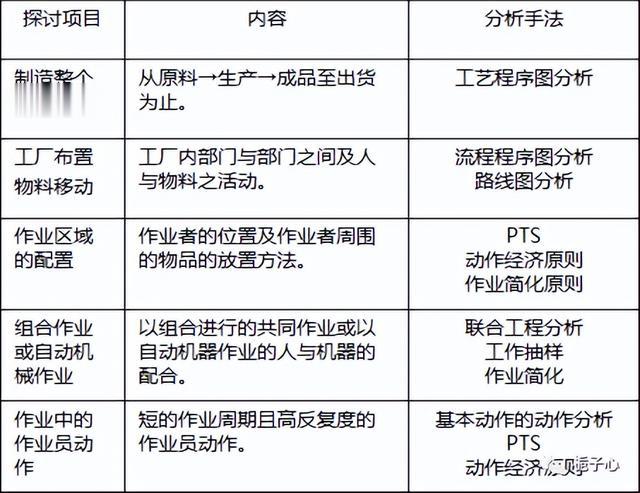
人机作业分析
在机器的工作过程中,调查、了解在操作周期(加工完一个零件的整个过程称为一个操作周期或周程)内机器操作与工人操作的相互关系,以充分利用机器与工人的能量及平衡操作。
利用人机操作图,可将生产过程中,工人操作的手动时间和机器的机动时间清楚地表现出来
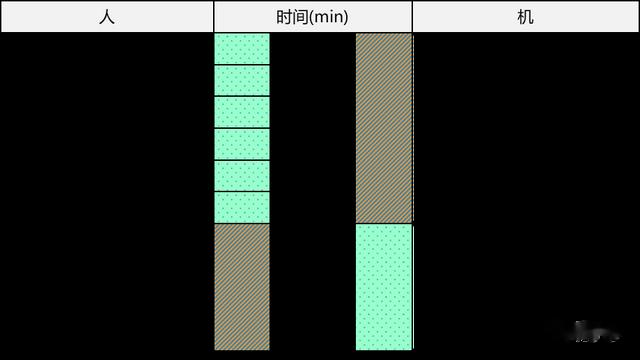
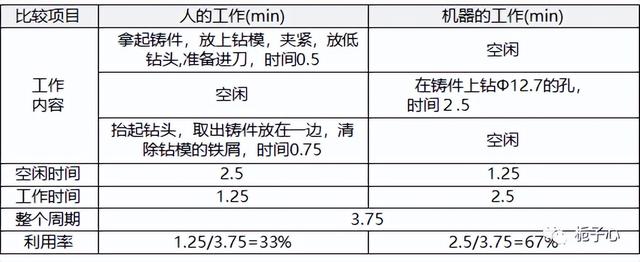
时间分析
标准时间的概念来源于泰勒的企业科学管理:“公平的一天工作量”(a fair day’s work)理论。
标准时间的定义是:“在适宜的操作条件下,用最合适的方法,以普通熟练工人的正常速度完成标准作业所需的劳动时间。”
•客观性—对应于某一标准化的作业操作(通过方法研究),标准时间是不以人们的意志而转移的客观存在的一个量值。
•可测性—只要将作业标准化了,就可以用科学的方法对操作进行测定(如秒表时间研究、工作抽样、PTS技术等),以确定标准时间的量值。
•适用性—标准时间是普通工人以正常速度能完成某项作业的劳动标准时间,不强调过分先进或十分敏捷的动作完成某项操作,所以它应该是易于被大多数人接受。
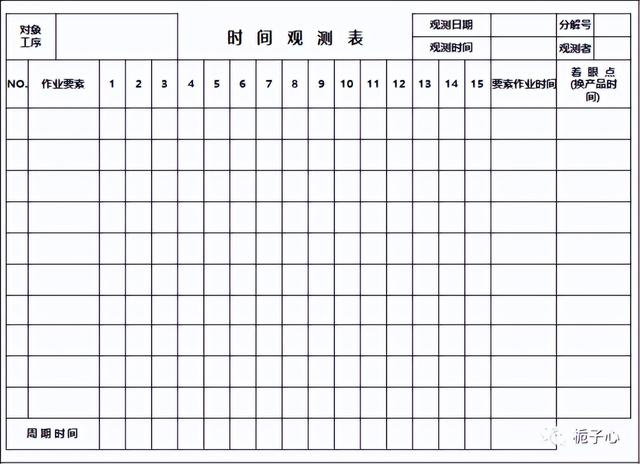
流程分析
过程流程图是利用一定的符号将实际的流程以图形方式表现出来,以便于确定可能的变量的形式。
它可以对要改进的过程有一个全面的,统一的了解;帮助项目团队确定过程中的一切可控与不可控的一切变量以及可能出现的缺陷。
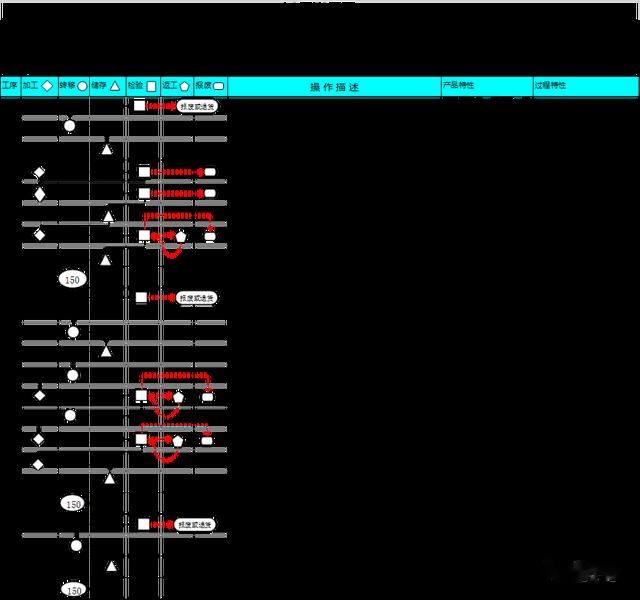
价值流图
价值流程图(Value Stream Mapping,VSM)是丰田精益制造(Lean Manufacturing)生产系统框架下的一种用来描述物流和信息流的形象化工具。VSM可以作为管理人员、工程师、生产制造人员、流程规划人员、供应商以及顾客发现浪费、寻找浪费根源的起点。
1. 组成工作小组并明确职责
2. 选择要研究的产品族
3. 了解客户需求
4. 画出工艺流程图
5. 画出物流
6. 画出信息流
7. 定义并收集相关数据
8. 绘制当前价值流图
9. 计算产品生产周期及增值比
10.找出当前价值流图中的各种浪费
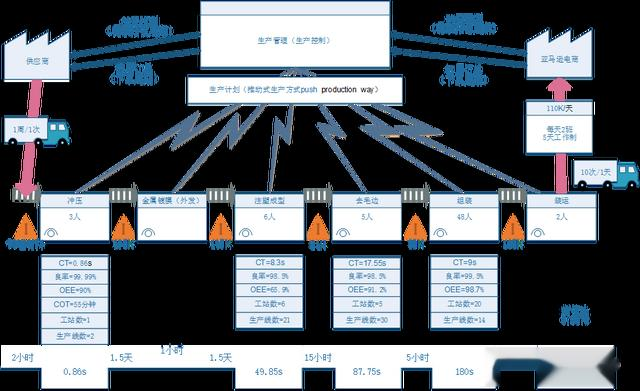
复杂性价值流图
描绘并且量化复杂性的影响,借助复杂性价值流图以及对复杂性方程的应用来找出并量化各种机遇,从而构建上述这些战略分析

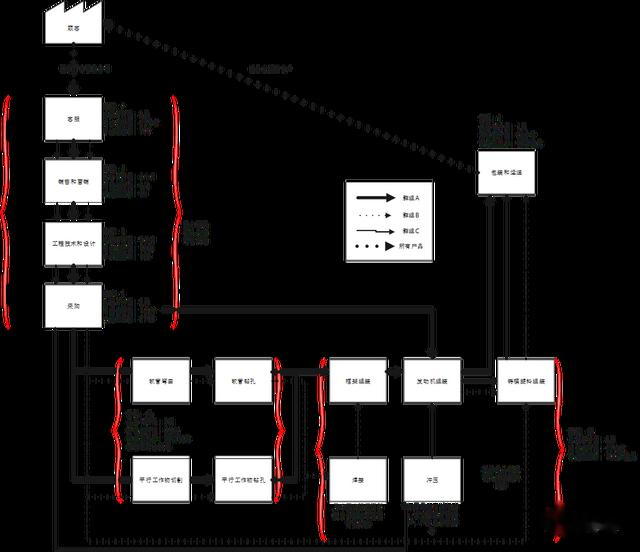