在当今全球制造业蓬勃发展的大背景下,设备的稳定运行对于企业的生产效率和经济效益起着至关重要的作用。然而,传统的设备维护模式正面临着前所未有的挑战,每年因设备突发故障导致的生产损失堪称天文数字。据数据显示,2023 年全球制造业因设备突发故障导致的生产损失达 1.2 万亿美元,这一数字令人触目惊心。例如,某汽车厂冲压机意外停机 3 小时,就造成了高达 800 万元的损失。如此巨大的损失,正倒逼整个行业进行技术革命,而设备预测性维护应运而生,成为解决这一难题的关键所在。

传统维护模式主要存在三大困局,严重制约着企业的发展。
被动响应陷阱。目前,70% 的企业仍在依赖 “坏了再修” 的模式,这种被动的维护方式使得企业在设备故障发生后才采取行动。平均故障修复时间(MTTR)长达 48 小时,在这漫长的时间里,生产停滞,企业的损失不断扩大。想象一下,一家工厂的核心生产设备突然出现故障,而维修人员只能在故障发生后才开始排查问题、寻找备件、进行修复,这期间生产线的停滞带来的不仅仅是产量的减少,还可能影响到订单交付,导致客户满意度下降,对企业声誉造成损害。
过度维护成本。为了确保设备的正常运行,许多企业选择定期检修的方式。然而,这种方式往往导致 30% 的备件浪费。以某石化企业为例,每年因此多支出 2000 万元。定期检修虽然在一定程度上降低了设备突发故障的概率,但却造成了资源的极大浪费。很多备件在被更换时,其实仍有相当长的使用寿命,这无疑增加了企业的运营成本。
经验依赖风险。随着老师傅退休潮的来临,企业面临着维护知识断层的严峻问题。新员工由于经验不足,误判率高达 40%。在设备维护领域,经验是非常宝贵的财富,老师傅们凭借多年积累的经验,能够快速准确地判断设备故障原因并采取有效的修复措施。然而,当他们离开岗位后,新员工往往难以迅速填补空缺,这不仅影响了设备维护的效率,还可能因为误判而导致更严重的设备故障。
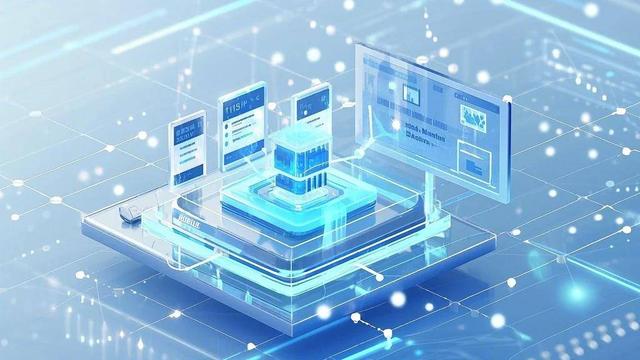
面对传统维护模式的困境,AI 预测模型技术架构的出现为设备维护带来了新的曙光。
多源感知层:敏锐捕捉设备细微变化
在多源感知层,各种先进的传感器发挥着重要作用。振动传感器能够捕捉 0.01mm 级位移变化,哪怕设备出现极其微小的振动异常,都能被及时察觉。红外热成像则可以检测 0.5℃温差异常,通过对设备温度的精准监测,发现潜在的故障隐患。声纹识别更是建立了 2000 + 种故障声学特征库,不同的设备故障往往会产生独特的声音特征,声纹识别技术能够通过对这些声音的分析,快速判断设备是否存在故障以及故障的类型。
智能边缘层:实现实时响应与高效数据传输
智能边缘层的嵌入式 AI 芯片实现了 10ms 级实时响应,这意味着设备一旦出现异常,系统能够在极短的时间内做出反应。同时,数据压缩技术的应用降低了 90% 传输带宽,大大提高了数据传输的效率,减少了数据传输过程中的延迟和成本。
云端大脑:强大的数据分析与决策能力
云端大脑采用混合模型架构,LSTM 捕捉时序特征,能够对设备运行数据的时间序列进行深入分析,发现其中的规律和趋势;XGBoost 处理结构化数据,对设备的各种参数进行综合评估。通过迁移学习,实现了跨设备知识共享,冷启动时间缩短 80%。这使得系统能够快速适应新设备的维护需求,无需长时间的初始化和数据积累就能准确进行故障预测。
关键技术突破:大幅提升故障预测准确率
故障特征解耦技术:精准分离故障特征
基于注意力机制的振动信号分解技术,成功地将轴承磨损与齿轮啮合异常等不同的故障特征分离出来。某风电企业应用这一技术后,早期故障检出率从 55% 提升至 89%。这意味着企业能够更早地发现设备故障隐患,及时采取措施进行修复,避免故障的进一步扩大。
多模态融合决策:提高预测准确性,降低误报率
振动、温度、电流三模态融合模型的应用,使得误报率降低至 3.2%。以半导体蚀刻机为例,预测准确率高达 97.5%。通过综合分析多种设备运行数据,模型能够更加准确地判断设备的运行状态,避免了单一数据来源可能导致的误判。
数字孪生仿真:提前预演故障场景
建立 1:1 虚拟镜像,提前预演 2000 + 故障场景。某注塑机厂商通过这一技术实现了预测周期提前 30 天。在虚拟环境中,企业可以对设备可能出现的各种故障进行模拟和分析,提前制定应对策略,大大提高了设备维护的主动性和针对性。
行业落地范式:成功案例彰显显著成效
轨道交通轴承预警系统:保障地铁安全运行
地铁轴承故障可能导致全线停运的巨大风险。某轨道交通企业通过部署 500 + 智能传感节点,构建故障知识图谱,成功实现了提前 42 天预警,维护成本降低 65%。这一系统的应用,不仅保障了地铁的安全运行,还为企业节省了大量的维护成本。
炼化厂泵群健康管理:满足高危设备连续运行需求
炼化厂拥有 2000 + 高危设备,对连续运行的要求极高。该厂通过搭建 AIoT 平台,开发自适应阈值算法,非计划停机减少 80%,能效提升 12%。这一举措有效提高了设备的可靠性,降低了因设备故障导致的生产中断风险,同时还提高了能源利用效率。
数控机床寿命预测:摆脱对外方的维护依赖
对于价值千万的进口数控机床,以往维护依赖外方,成本高且效率低。某企业通过采集主轴电流谐波特征,建立剩余寿命模型,备件库存周转率提升 3 倍,精度保持周期延长 40%。这使得企业能够自主掌握设备的维护主动权,降低了维护成本,提高了设备的使用效率。
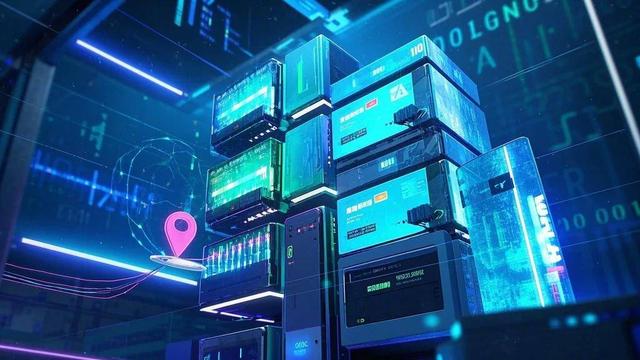
诊断评估阶段(1 - 2 月)
在这一阶段,企业需要进行设备关键性分析(FMEA),明确哪些设备对生产至关重要,以及这些设备可能出现的故障模式及其影响。同时,对数据可获取性进行评估,确保能够收集到足够的设备运行数据,为后续的故障预测提供数据支持。
试点验证阶段(3 - 6 月)
选择 3 - 5 台典型设备,构建最小可行性模型。通过对这些设备的实际运行数据进行分析和建模,验证预测模型的有效性和准确性。在这个阶段,可以对模型进行初步的优化和调整,为规模推广做好准备。
规模推广阶段(6 - 12 月)
部署工业级边缘计算网关,实现设备数据的实时采集和传输。建立模型迭代机制,随着数据的不断积累和设备运行情况的变化,及时对模型进行更新和优化,确保模型的预测准确性始终保持在较高水平。
持续优化阶段(12 月 +)
开发自学习系统,让模型能够自动学习设备运行的新知识和新规律。构建预测性维护知识库,将设备维护过程中的经验和知识进行整理和存储,为企业的设备维护提供更加全面和系统的支持。
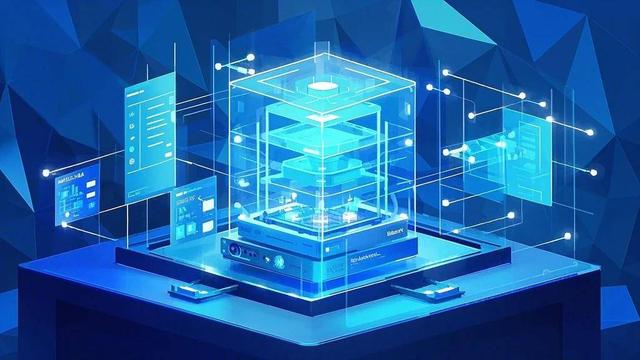
因果 AI 突破:深入挖掘故障根因
AI 取得突破,从目前的相关关系分析深入到故障根因追溯。这意味着企业能够更加准确地了解设备故障的根本原因,从而采取更加有效的预防措施,进一步降低设备故障的发生率。
自主维护系统:实现智能化运维
自主维护系统将成为现实,AI 能够直接下发工单并调度资源。设备一旦出现故障隐患,系统能够自动安排维修人员和备件,实现设备维护的智能化和自动化,大大提高维护效率。
维护即服务(MaaS):创新商业模式维护即服务(MaaS)将成为一种新型商业模式,企业按照预测准确率收费。这种模式将促使维护服务提供商不断提高故障预测的准确性,为客户提供更加优质的服务,同时也为企业降低维护成本提供了新的途径。
当某锂电池工厂通过 AI 预警避免价值 2 亿元的产线火灾时,我们深刻地认识到设备预测性维护的巨大价值。它不仅仅是一项技术革新,更是工业运维范式的根本转变。预测性维护正在重塑设备全生命周期价值曲线,在这场静默的革命中,提前布局的企业将赢得未来十年的竞争优势。让我们积极拥抱设备预测性维护,开启工业运维的新时代,为企业的可持续发展注入强大动力。