去年秋天,我受邀参观一家小家电工厂。走进车间,原本想象中的轰鸣机器和忙碌工人不见了,取而代之的是安静运转的机械臂、闪烁的电子看板,以及几位工程师在平板电脑前轻点屏幕。厂长余崇威指着一条电源线生产线告诉我:“以前这里需要 10 个人盯着,现在 1 个人就能管整条线,产能还提升了 28%。” 这就是数字工厂的魅力 —— 它不是科幻电影里的未来场景,而是正在重塑制造业的现实。

数字工厂的本质,是给工厂装上 “数字大脑”。就像某科技企业为某制造集团打造的数字工厂操作系统,通过云边协同技术,将分布在全球的生产数据实时汇聚到云端,再通过 AI 算法优化排产、预测设备故障。这种 “虚实融合” 的模式,让工厂的每个环节都能在虚拟世界中提前演练。比如某航天企业的火箭制造车间,焊接机器人在正式作业前,会在数字孪生系统中模拟焊接路径,确保每一道焊缝都精准无误,生产效率提升了 2.5 倍。
与传统工厂相比,数字工厂最大的突破在于数据驱动。在某智能车间里,每台设备都连接着 BI 系统,4000 多张实时报表让管理者能一眼看穿生产瓶颈。曾经需要人工统计的良品率、能耗等数据,现在系统自动生成分析报告,甚至能预测未来三天的产能波动。这种 “用数据说话” 的方式,彻底改变了工厂的决策逻辑。
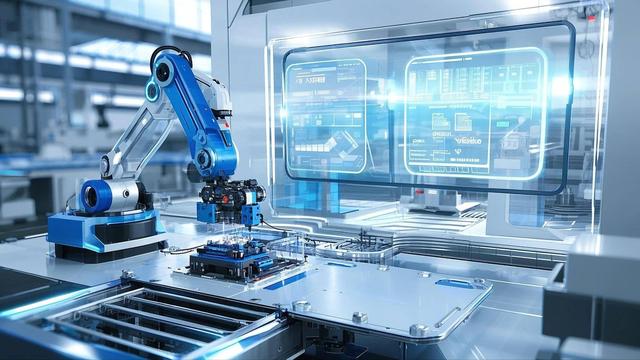
在参观某工业互联网企业服务的半导体面板工厂时,我深刻体会到了这种代际差距。传统工厂的设备数据分散在各个孤岛,工程师需要在不同系统间切换,效率低下且容易出错。而数字工厂通过统一的平台,将生产管理、品质分析、设备运维等系统整合在一起,实现了 “一个屏幕管全厂”。这种整合带来的不仅是效率提升,更重要的是决策模式的升级:当某条产线良率下降时,系统会自动关联到设备参数、原材料批次等 12 个维度的数据,10 分钟内给出优化建议,而传统工厂可能需要工程师花半天时间排查。
另一个显著区别在于灵活性。某家电企业的工业 4.0 示范工厂,能根据消费者的个性化需求定制冰箱。从外观设计到功能配置,数据直接驱动生产线切换模具,实现 “千台千面” 的柔性生产。这种能力在传统工厂几乎不可想象 —— 它们往往需要停工数周来调整产线。
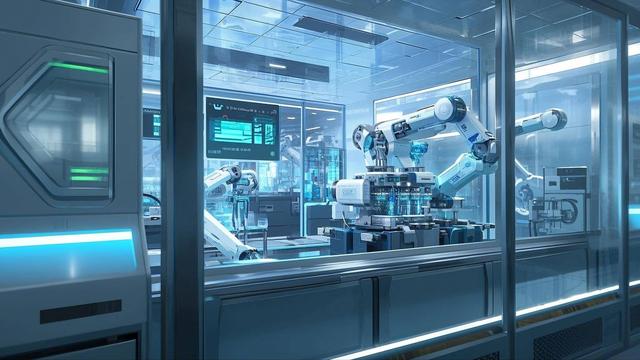
物联网与边缘计算
某电子企业的电源线生产线上,6 个检测工位全部实现 “机器换人”,传感器每秒采集 1000 组数据,实时反馈给中央系统。这些数据不仅用于质量控制,还能预测设备寿命,将故障率降低 70%。
数字孪生与仿真技术
某跨国企业的工厂数字孪生系统,能模拟每一个生产环节。新产品研发时,工程师先在虚拟环境中测试工艺,将研发周期缩短 50%。这种 “先试后产” 的模式,避免了传统工厂因设计缺陷导致的返工浪费。
工业软件自主可控
在半导体行业,某企业自研的 CIM 系统成功替代了国外软件,实现了从设备控制到生产调度的全流程国产化。这不仅打破了技术封锁,还让系统支持二次开发,更贴合本土企业的需求。
人机协同的新生态
在某航天企业的车间里,工人不再是 “操作机器的人”,而是 “训练机器的人”。他们通过 AR 眼镜接收操作指令,利用大数据分析优化工艺参数,将经验转化为可复制的算法模型。
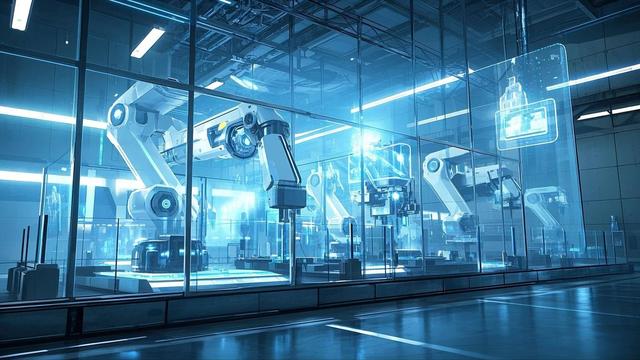
从某地的小家电到工业互联网总部基地,数字工厂正在中国大地落地生根。相关报告显示,55.4% 的工业企业倾向于选择整体解决方案服务商,而非单点改造。这种趋势背后,是企业对 “降本增效” 的迫切需求 —— 某数字工厂操作系统,帮助客户降低制造成本 10%-20%,提升生产效率 20%-30%。
作为观察者,我常常思考:数字工厂的价值究竟是什么?它不仅是技术的升级,更是一场关于 “人” 的革命。当机器承担了重复劳动,人类得以解放双手去创新;当数据取代经验成为决策依据,工厂的竞争力将不再依赖规模,而是智能化水平。这或许就是制造业的未来 —— 不是冰冷的机器统治,而是数字与人性的深度融合。