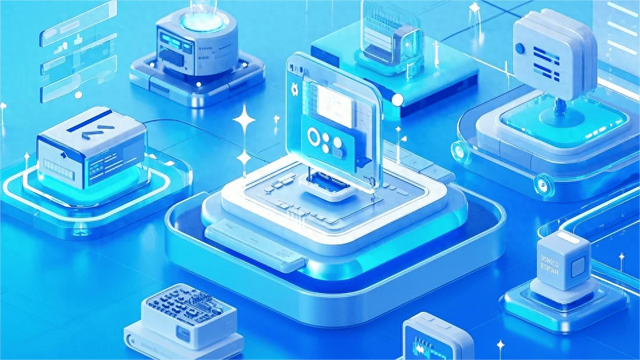
在工业制造领域,设备管理是企业运营的核心环节。然而,许多企业仍沿用传统管理模式,导致效率低下、成本高企。本文将从手工记录维修历史、备件浪费、部门数据孤岛等七大痛点切入,结合EAM(企业资产管理)系统的解决方案,揭示数字化转型如何帮助企业突破管理瓶颈,并通过实际案例展现转型成效。

1. 手工记录维修历史:信息滞后与误差频发
传统设备管理依赖纸质或Excel表格记录维修信息,不仅效率低,还容易因人为疏忽导致数据错误。例如,某企业设备部门需每月制定维护计划,但手工记录难以实时更新设备状态,导致计划与实际需求脱节:设备可能在计划检修前突发故障,或状态良好却被迫进行冗余维护。这种“盲人摸象”式的管理,使得设备故障率居高不下。
2. 备件浪费:库存积压与短缺并存
备件管理是传统模式的另一大难题。企业常因缺乏数据支持而盲目采购,导致库存积压或紧急缺货。某制造企业每月需提交备件采购计划,但主管因无法判断需求合理性,只能“照单全收”,最终造成资金占用和资源浪费7。据统计,过度库存可占用企业20%以上的流动资金。
3. 部门数据孤岛:协同效率低下
设备管理涉及生产、维修、采购等多个部门,但传统模式下数据分散,信息无法共享。例如,维修部门无法实时获取设备运行状态,采购部门难以及时响应备件需求。这种“各自为战”的格局,导致决策滞后和资源内耗。
4. 设备寿命短:缺乏科学维护策略
许多企业采用“坏了再修”的被动维护模式,忽视预防性维护。例如,两家使用同型号设备的企业,因维护策略不同,设备寿命差异显著:一家通过定期保养延长设备使用周期,另一家则因频繁故障被迫提前报废。
5. 合规性风险:记录缺失与追溯困难
传统管理模式下,设备维护记录分散且不完整,难以满足行业监管要求。例如,某化工企业因无法提供完整的设备检修记录,面临巨额罚款。
6. 资源利用率低:设备闲置与超负荷并存
缺乏实时监控导致设备使用不均衡。某钢铁企业部分设备长期闲置,而核心设备却因超负荷运行频繁故障,整体利用率不足60%。
7. 决策依赖经验:缺乏数据支撑
管理人员多凭经验制定维护计划,忽视设备实际运行数据。例如,某电力公司因未分析设备历史故障规律,导致重复性故障频发,每年损失超百万元。
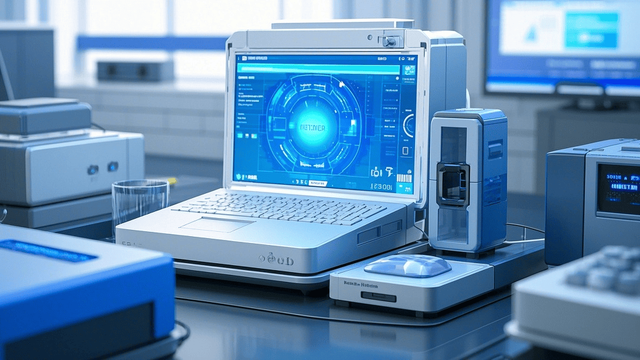
1. 标准化流程:从“人治”到“数治”
EAM系统通过工单管理、预防性维护、预测性维护三大核心功能,重构设备管理流程:
工单自动化:系统自动生成维护计划,并实时跟踪执行进度,减少人为干预。
预防性维护:基于设备运行时间或使用周期,制定标准化保养计划,避免突发故障。
预测性维护:通过物联网传感器采集数据,结合AI算法预测故障,实现“精准维修”。
2. 数据整合:打破信息孤岛
EAM系统集成设备台账、运行监控、备件库存等模块,构建统一数据平台:
实时监控:通过2.5D/3D可视化界面,直观展示设备状态,支持跨部门协同。
全生命周期管理:从采购到报废,所有数据集中存储,便于追溯与分析。
KPI与OEE分析:量化设备综合效率(OEE),为决策提供科学依据。
3. 智能优化:降本增效的实践路径
备件库存优化:系统根据维护计划自动生成备件需求,结合安全库存模型,减少资金占用。
资源调度优化:通过分析设备利用率,动态调整生产计划,避免闲置与超负荷。
合规性保障:自动生成合规报告,满足ISO 55000等资产管理标准。
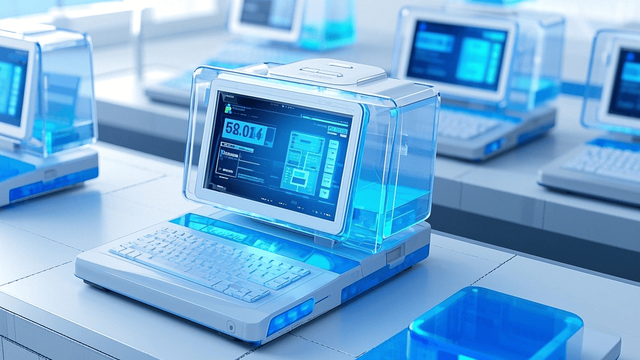
随着 AI 与物联网技术深度融合,设备管理正迈向 "三自" 新境界:
自感知:通过边缘计算实现设备状态实时诊断自决策:AI 算法自动生成优化方案自执行:机器人系统完成自主维护