据宝马集团10月29日消息,作为通往未来数字化工厂(iFACTORY)道路上的又一个里程碑,宝马集团德国雷根斯堡工厂正在推进其物流工作的数字化和自动化。据统计,每57秒就有一辆宝马新车在雷根斯堡工厂下线,每台宝马新车都是根据客户喜好和选择诞生的,并由数千个独立组件打造而成。每个工作日,多达1400台宝马X1和宝马X2在此下线并被发往世界各地的客户手中,包括传统内燃机、插电式混合动力以及纯电动车型。
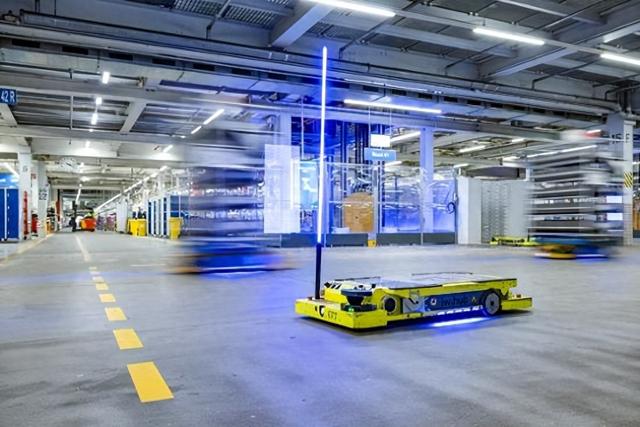
生产过程背后的物流工作十分复杂:生产所需的组件和单个零件必须始终在正确的时间出现在装配线上的正确位置,以便为不同客户打造独一无二的新车。
在雷根斯堡工厂,这一对高效生产至关重要的物流任务主要由无人驾驶、自动化或自主运输系统处理,这些系统通过被称为宝马自动运输服务(ATS)的云端交通控制系统智能连接。在某些情况下,运输车辆的装载和卸载也完全实现自动化。
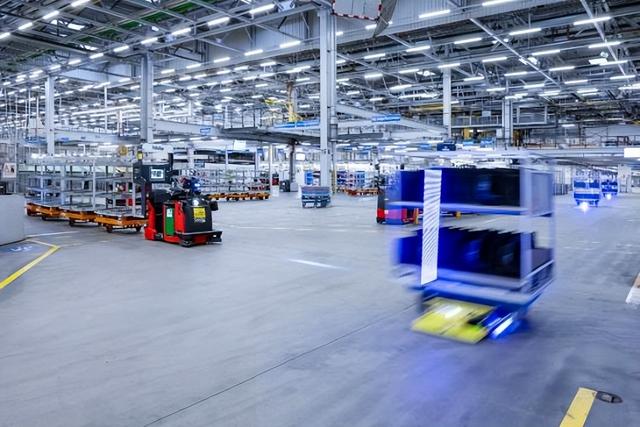
根据运输任务的不同,会使用不同类型的无人驾驶车辆。例如,自动牵引列车将小型部件从仓库运送到装配线,而重达一吨的大型部件则由智能运输机器人(STR)来处理。这些平板运输机器人由宝马集团与德国弗劳恩霍夫物流研究院(IML)合作开发,并在大约十年前研制成功,如今能够使用专用的AI人工智能模块自主运行。依靠传感器和软件,这些设备能够识别周围环境,甚至能够识别环境、绕过障碍物独立行驶。
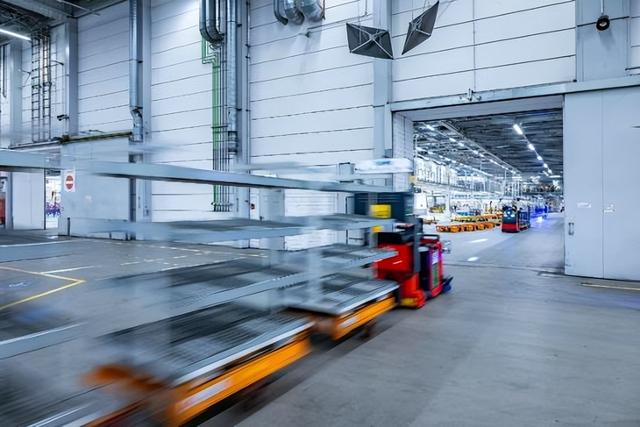
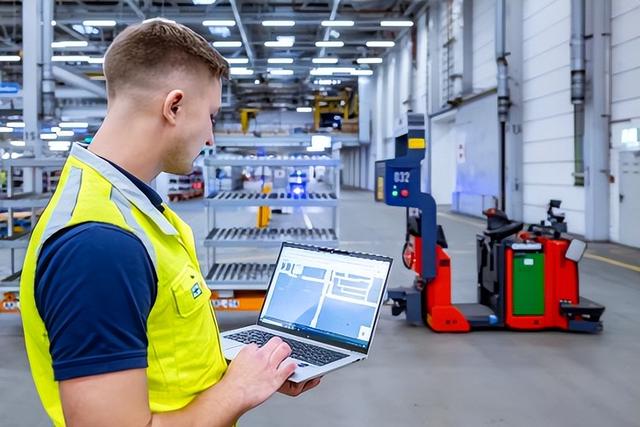
运输设备通过中央云端宝马交通控制系统进行管理。当需要补充物料时,装配线上的员工会转动装有空零件容器的更换框,并用它来操作所谓的回收摇杆。然后,控制系统就会接收到需要运送新零件的信号。通过这种方式,控制系统可以顺利、准确地按时交付材料,并保持装配车间内的智能交通流。此外,该系统还能根据交付的优先级别提供蕞佳路线指引,并确保运输设备合理停放和电池充足充电。
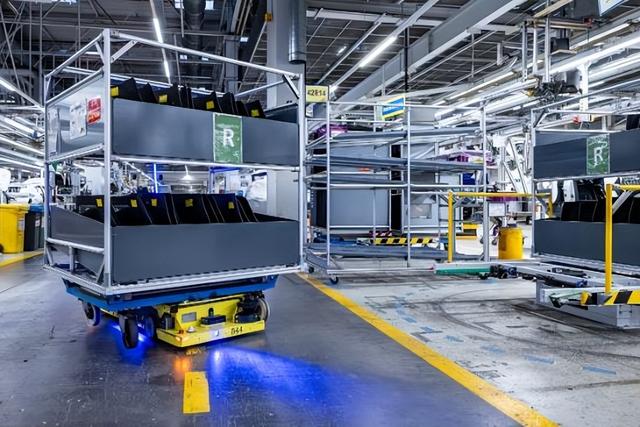
目前,宝马集团雷根斯堡工厂通过ATS控制系统实现了近50台自动牵引列车和140多个智能运输机器人之间的智能连接。车队由来自不同制造商的自动化和自主设备组成,每个工作日处理约10000次零件交付。此外,近期在雷根斯堡工厂的冲压车间投入使用了一台具有55吨载重能力的自动运输车。
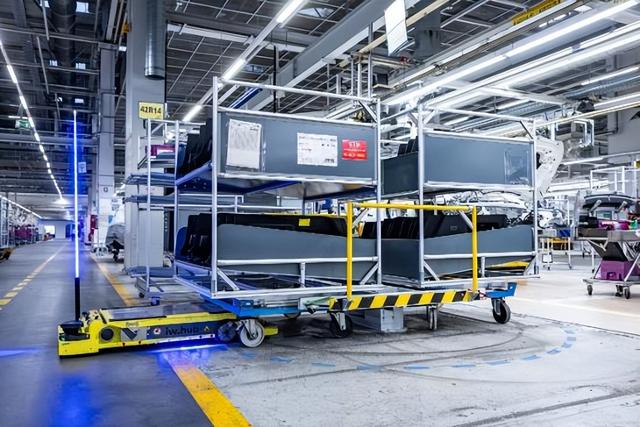