
在工业4.0与智能制造浪潮下,设备管理正从传统的“故障后响应”模式向“全生命周期主动管控”跃迁。借助扫码上云与数字孪生技术,设备管理的边界被重新定义——从设计、生产到运维、退役,每一个环节都能通过数据驱动实现效率跃升。本文结合中设智控等企业的实践案例,探讨这两大技术如何赋能设备管理系统的智能化升级。

1. 传统管理模式的痛点
数据孤岛:设备信息分散于采购、运维、财务等系统,缺乏统一视图;响应滞后:依赖人工巡检和经验判断,故障预测能力弱;成本高企:维护成本占设备总成本的30%以上,且资源调配效率低。2. 技术破局:扫码上云+数字孪生的协同效应
扫码上云:通过二维码/RFID快速绑定设备身份,实现“一物一码”数据上云,打通设备全链条信息流;数字孪生:构建物理设备的虚拟镜像,实时映射运行状态,支持仿真优化与预测性维护。协同价值:扫码技术解决数据入口问题,数字孪生提供动态分析能力,两者结合形成“感知-建模-决策”闭环。
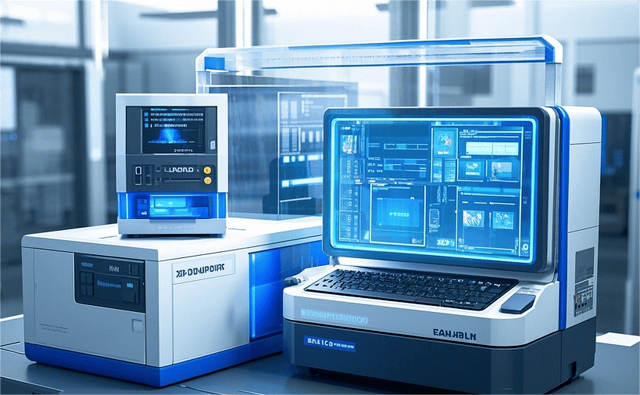
1. 技术架构与应用场景
设备身份数字化:扫码绑定设备唯一ID,集成出厂参数、维修记录等静态数据;实时状态监控:结合IoT传感器,云端同步振动、温度、能耗等动态指标;移动化运维:通过APP扫码快速调取设备档案,实现工单派发、备件申领等操作。2. 中设智控的实践:比亚迪设备资产数字化升级
在比亚迪项目中,中设智控通过扫码技术将设备资产与SAP、OA等系统打通,实现全生命周期数据集成。例如:
采购验收:扫码录入设备规格、供应商信息,自动生成电子台账;维修管理:故障扫码触发工单,关联历史维修记录与备件库存;成本分析:自动汇总维修费用、能耗数据,生成设备TCO(总拥有成本)报表。成效:设备利用率提升15%,故障停机率降低22%。
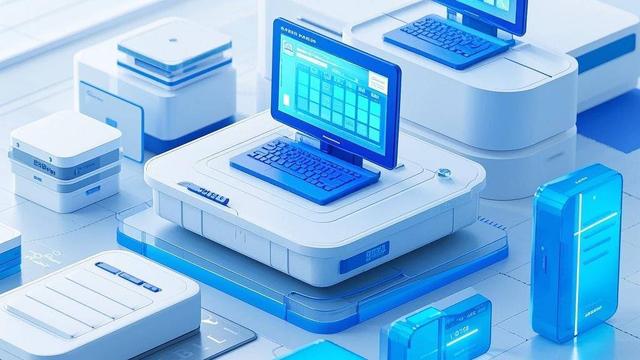
1. 技术深度解析
多维度建模:融合几何、物理、行为模型,例如NXP在电机控制中构建的“电气-机械-热学-算法”四维孪生体系;动态仿真:通过参数自适应算法,实时校准模型精度(如电机转速误差从8.7%降至1.2%);预测性维护:基于历史数据与机器学习,预测故障概率并优化维护计划。2. 应用案例:涪陵制药厂的智能化转型
中设智控为太极集团涪陵制药厂设计的设备管理系统,将数字孪生技术融入提取车间管理:
虚拟调试:在投产前模拟设备运行,优化工艺参数;故障预测:通过温升、压力等孪生数据,提前预警关键设备异常;能效优化:分析虚拟模型中的能耗热点,制定节能方案。成果:设备综合效率(OEE)提升18%,维护成本下降30%。
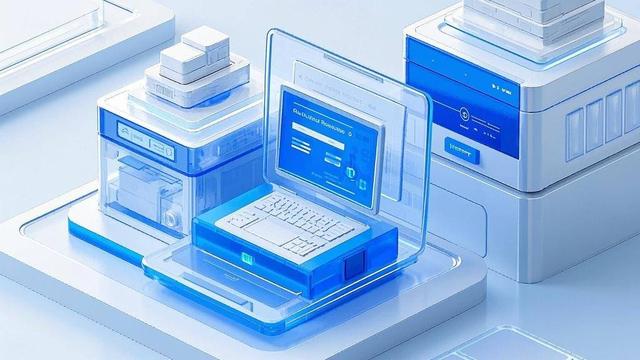
1. 设计制造阶段
虚拟验证:通过数字孪生仿真设备性能,减少物理样机迭代成本;质量追溯:扫码记录零部件来源,实现制造过程透明化。2. 运维阶段
智能诊断:结合扫码数据与孪生模型,定位故障根源(如轴承磨损或电路老化);资源调度:云端分析设备负载,动态分配维修人员与备件。3. 退役回收阶段
残值评估:基于孪生模型中的磨损数据,测算设备剩余价值;绿色回收:扫码追踪设备材料成分,优化拆解与再利用流程。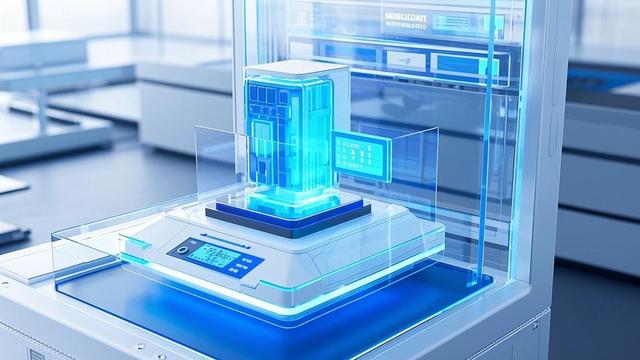
1.技术趋势:
5G+边缘计算:提升孪生模型实时性,支持毫秒级响应;AI大模型:实现更精准的故障归因与自主决策。2.生态延伸:
产业链协同:上下游企业共享孪生数据,优化供应链与产能配置;碳足迹管理:通过全生命周期数据分析,助力企业达成“双碳”目标。
扫码上云与数字孪生技术的结合,不仅让设备管理从“黑箱”走向“透明”,更推动了制造业向“数据驱动”的深刻转型。中设智控在比亚迪、涪陵制药厂等项目的成功实践,印证了这一路径的可行性。未来,随着技术成熟与生态完善,设备全生命周期管理将成为智能制造的核心竞争力之一。