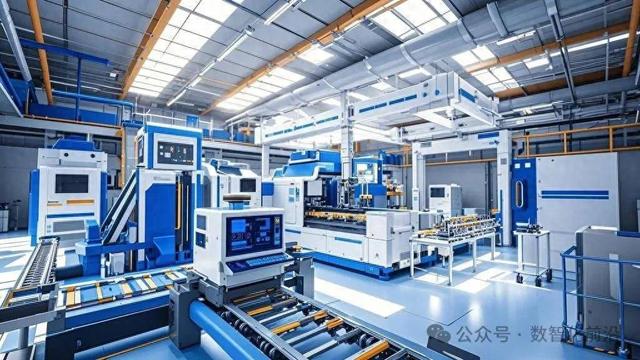
在工业领域,设备就如同企业的 “心脏”,设备的稳定运行关乎企业的生产效率与经济效益。传统的设备维护方式,往往是在故障发生后才进行维修,这就好比人得了病才去治疗,不仅会导致生产中断,还可能造成巨大的经济损失。而设备预测性维护,就像是给设备做 “体检”,提前发现潜在问题,将故障消灭在萌芽状态,实现从 “被动维修” 到 “主动预警” 的转变。今天,我们就来深入探讨设备预测性维护从数据采集到故障预警的完整链路。
数智科技说 |公众号
↑↑↑欢迎关注新号↑↑↑
数据采集:收集设备的 “健康信息”
数据采集是预测性维护的基础,就如同医生诊断病情需要先了解患者的各项身体指标一样。在设备预测性维护中,我们依靠各类传感器来收集设备的运行数据,这些传感器就像是设备的 “听诊器” 和 “体温计”。
常见的传感器有振动传感器、温度传感器、压力传感器等。振动传感器能实时监测设备运行时的振动情况,一旦设备出现异常振动,很可能意味着内部零部件出现了磨损或松动。温度传感器则能精确测量设备关键部位的温度,过高的温度往往是设备故障的前兆。例如,在一台大型电机上安装振动和温度传感器,通过持续收集电机运行时的振动幅度、频率以及温度数据,我们就能初步掌握电机的运行状态。
除了这些物理量的监测,数据采集还涵盖设备的运行时间、负荷等信息。这些数据就像设备的 “健康档案”,为后续的分析提供了丰富的素材。需要强调的是,数据的准确性和完整性至关重要,只有高质量的数据,才能为后续的分析和决策提供可靠依据。
数据传输与整合:搭建数据 “高速公路”
采集到的数据需要及时、准确地传输到分析系统中,这就涉及到数据传输环节。目前,数据传输主要有有线和无线两种方式。有线传输稳定性高,适合对数据传输可靠性要求较高的场景,如工厂内部的设备数据传输。而无线传输则更加灵活,便于在一些难以布线的场所使用,像风力发电厂的风机数据采集,通过无线传输就能轻松将风机上的传感器数据发送到控制中心。
在传输过程中,不同的设备和系统可能采用不同的传输协议,如常见的 Modbus、MQTT 等。为了确保数据能够顺利传输和被识别,需要统一或转换这些协议。当数据从各个传感器传输到数据中心后,由于来源多样,数据格式和类型也各不相同,这就需要进行数据整合。数据整合就像是把来自不同地方的拼图碎片拼在一起,形成一幅完整的图像。通过建立统一的数据标准和数据仓库,将多源异构的数据整合到一起,消除数据孤岛,为后续的数据分析提供一个统一、规范的数据平台。

数据分析与建模:挖掘数据背后的 “秘密”
有了丰富的数据之后,接下来就是要通过数据分析和建模来挖掘这些数据背后隐藏的信息,找出设备运行的规律和潜在的故障模式。
在数据分析中,机器学习和深度学习等先进算法发挥着重要作用。机器学习算法可以对大量的历史数据进行学习和训练,从而建立起设备的运行模型。例如,通过分析设备过去正常运行和发生故障时的各种数据特征,训练出一个能够识别设备健康状态的分类模型。当新的数据输入时,模型就能根据已学习到的特征判断设备当前处于正常运行状态还是存在故障风险。
深度学习算法则更擅长处理复杂的数据模式,特别是在图像、语音等非结构化数据处理方面有独特优势。在设备预测性维护中,如果涉及到设备内部结构的图像分析,如通过 X 光或红外成像检测设备内部的磨损情况,深度学习算法就可以对这些图像数据进行分析,准确识别出设备的缺陷和故障隐患。
通过建立物理模型或数学模型,我们可以模拟设备在不同工况下的运行状态,预测设备性能随着时间的变化趋势。例如,利用热传导模型来预测设备在长时间运行后的温度分布,或者通过机械动力学模型来分析设备零部件的受力情况,提前发现可能出现疲劳损坏的部位。
故障预测与预警:为设备故障拉响 “警报”
基于数据分析和建模的结果,我们就可以进行故障预测和预警了。这一步就像是给设备安装了一个 “智能报警器”,一旦发现设备可能出现故障,就会及时发出警报。
首先,需要根据设备的历史数据和运行特性,设定合理的预警阈值。这些阈值是判断设备是否正常运行的重要依据。例如,对于一台压缩机的振动值,经过大量历史数据的分析,确定当振动幅度超过某个特定值时,设备出现故障的概率会显著增加,那么这个值就是振动预警的阈值。
当设备的实时运行数据超过预警阈值时,故障预警系统就会立即启动。预警方式多种多样,常见的有系统界面弹窗,提醒运维人员设备出现异常;短信和邮件通知则能让相关人员在第一时间得知设备情况,即使不在电脑前也能及时做出响应。例如,某工厂的设备预测性维护系统在检测到一台关键设备的温度超过预警阈值时,立即向设备管理员的手机发送了短信提醒,管理员收到短信后迅速安排维修人员对设备进行检查和维护,避免了设备故障的进一步扩大。

实战案例见证实力
设备预测性维护在众多行业已经得到了广泛应用,并取得了显著成效。
在一家汽车制造工厂,通过实施设备预测性维护系统,对生产线上的机器人、冲压机等关键设备进行实时监测和数据分析。在过去,这些设备由于突发故障导致生产线停机的情况时有发生,每次停机都会造成大量的生产损失。引入预测性维护后,通过提前预测设备故障并及时进行维护,生产线的停机时间降低了 30% 以上,生产效率大幅提高,同时维修成本也因为减少了不必要的维修和零部件更换而降低了 20% 左右。
在电力行业,某发电厂利用设备预测性维护技术对发电机组进行状态监测。通过对发电机的振动、温度、电气参数等数据的实时分析,成功预测并避免了多次潜在的设备故障。例如,在一次监测中,系统发现一台发电机的转子振动出现异常变化,通过进一步分析预测到转子可能存在不平衡问题。维修人员在接到预警后,及时安排停机检修,更换了受损的零部件,避免了因转子故障导致的发电机损坏,保障了电力的稳定供应。
挑战与展望:探索前行的方向
尽管设备预测性维护前景广阔,但在实际实施过程中也面临着一些挑战。首先是数据安全问题,设备运行数据包含了企业的核心生产信息,一旦泄露可能会给企业带来严重损失。因此,需要建立完善的数据安全防护体系,确保数据在采集、传输、存储和使用过程中的安全性。
其次,人才短缺也是一个制约因素。设备预测性维护涉及到数据分析、机器学习、设备工程等多个领域的知识,需要既懂技术又懂设备的复合型人才。企业需要加强相关人才的培养和引进,以满足实施预测性维护的需求。
展望未来,设备预测性维护将朝着更加智能化的方向发展。随着人工智能技术的不断进步,预测模型的准确性和可靠性将进一步提高,能够更精准地预测设备故障。同时,设备预测性维护将与物联网、大数据、云计算等技术深度融合,实现设备的远程监控和管理,让设备维护更加高效便捷。
结语:开启设备维护新时代
设备预测性维护从数据采集到故障预警的完整链路,为企业提供了一种全新的设备维护理念和方法。通过这一技术,企业能够提前预知设备故障,降低生产风险,提高生产效率,实现降本增效的目标。在竞争日益激烈的市场环境下,采用先进的设备预测性维护技术,将成为企业提升核心竞争力的关键因素之一。让我们一起积极拥抱这一技术变革,开启设备维护的新时代。