近日,由中石化石油化工科学研究院有限公司炼油工艺与催化剂国家工程研究中心研发的“助力双氧水绿色安全大型化生产的新一代蒽醌载体设计”项目获第四届中央企业熠星创新创意大赛二等奖。该技术通过设计新型蒽醌载体,“治愈”了传统生产工艺蒽醌产品稳定性差、依赖碱消除降解物的顽疾,有望让双氧水生产彻底摆脱碱的“束缚”,从源头铲除相关事故发生的可能。
该项目由中国石化首席专家、中国石化流化床蒽醌法制备双氧水成套技术首席宗保宁教授团队研发。

宗保宁教授团队用9年时间画出一道改变全球化工史的分子式——当新型蒽醌载体的稳定性测试数据定格在传统产品的18.7倍时,宣告着中国双氧水产业终于挣脱了困扰行业70年的“碱透析”枷锁。这场静默的技术突围,不仅让每年10万吨的废碱液固废成为历史,更将全球双氧水装置单套产能上限从20万吨/年暴力拉升到50万吨级,而成本却直降30%。
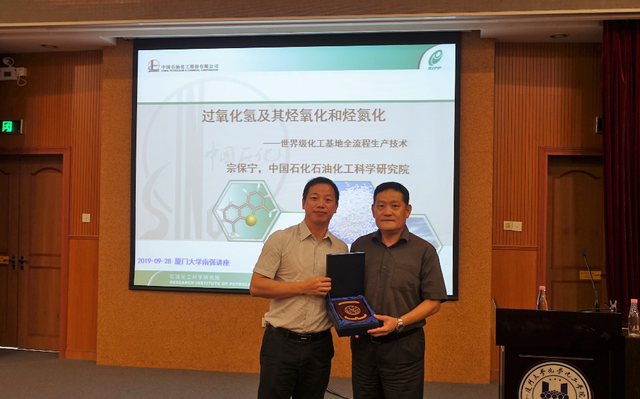
把时间倒回2015年的江苏某双氧水厂,刺鼻的碱液气味弥漫车间,工人们每72小时就要对蒽醌载体做一次“血液透析”——这是行业对付降解物堆积的无奈之举。传统乙基蒽醌就像脆弱的“载氢红细胞”,在氢化-氧化循环中不断衰亡,产生的四氢蒽醌等降解物如同血管里的血栓,逼着企业用强碱清洗系统。仅山东某龙头企业,每年因此产生的废碱渣就达3800吨,处理费用超2000万元,更别提那些因碱液与双氧水意外接触引发的闪爆事故。
宗保宁团队的手术刀精准切入分子层面:他们在蒽醌骨架上嫁接特殊烷基链,如同给载体装上“防降解装甲”。在沧州中试基地,搭载新载体的反应器连续运转180天未停机,降解物生成量较传统工艺锐减92%。更颠覆的是,团队独创的活性氧催化氧化技术,让烷基蒽转化率飙至99.8%,将原本需要5道工序的流程压缩到2步。这套组合拳直接改写了产业经济学——当德国同行还在为30万吨级装置的天价投资发愁时,中国技术已实现50万吨级产线设备国产化,建设成本比进口线低55%。
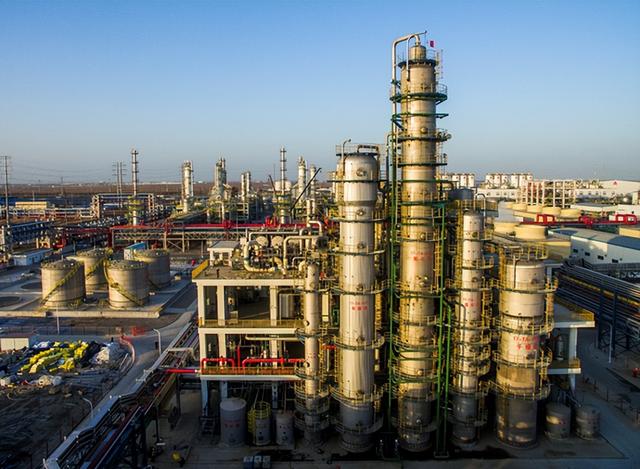
在福建古雷半岛,全球首套新一代双氧水装置正吐出雪白的工业级产品。这里看不到碱再生车间的刺眼蒸汽,闻不到苯酐法生产的刺鼻气味,监控屏上跳动的“零固废”指示灯宣告着新时代的来临。下游光伏企业测算,因双氧水纯度提升至电子级,硅片清洗损耗率下降0.8%,单条产线年省成本超千万。而更深远的影响在于,这项技术让中国手握双氧水领域首个自主知识产权体系,从催化剂到工艺包全部国产化,全球200亿美元双氧水市场的话语权正在发生不可逆的东移。