浅谈陶瓷封装的平行缝焊工艺与技术
袁尔千,商登辉,阳永衡
贵州振华风光半导体股份有限公司
摘要:
在气密性集成电路封装中常用的封装工艺有平行缝焊、储能焊、玻璃融封和金锡融封,不同的封装工艺适用于不同的产品。其中,平行缝焊工艺具备易加工性、低温升、高可靠等性能,近年来被封装厂广泛应用,尤其在光电领域、集成电路领域有突出的应用价值。在多层陶瓷基体封装外壳中,平行缝焊工艺对外壳材料的冲击是工艺实施的重点、难点,对于如何在陶瓷基体封装外壳中实现最优的平行缝焊工艺,是本文研究的主要方向。
0引言
目前在气密性集成电路领域,与储能焊、激光焊相比,平行缝焊具有高可靠性、优越的密封性能、运行成本低及生产率高等特点,是微电子器件最常用的气密性封装工艺之一[1]。但陶瓷基体外壳平行缝焊工艺一旦控制不好,产品经常会出现以下不良问题:如打火、漏气、断焊、瓷裂等。本文将结合振华风光公司的生产经验,通过对平行缝焊工艺的全面分析,解剖每一个工艺手法,运用平行缝焊理论、工装夹具设计、电极轮设计等措施有效降低产品不良率,提升产品质量稳定性与工艺可靠性。
1平行缝焊的基本原理
平行缝焊属于电阻焊,缝焊时,用电极对被焊器件施加一定压力的同时断续通电,利用电极间的接触以及电阻产生的焦耳热使金属盖板与管壳镀层熔化结合,达成气密性焊接,确保了管芯和电路与外界环境的隔绝,避免外界有害气氛的侵袭,同时也限制了封装腔体内水汽含量和自由粒子等。
1.1 工艺主要实施过程
其工艺主要实施过程是两个圆锥形滚轮电极压住待封装的金属盖板和管壳上的金属框,焊接电流从变压器次级线圈一端,经其中一个锥形滚轮电极分为两股电流,一股电流流过盖板,另一股电流流过管壳,经另一锥形电极,回到变压器次级线圈的另一端。整个回路的高电阻在电极与盖板的接触处,由于脉冲电流产生大量的热,使接触处呈熔融状态,在滚轮电极的压力下,凝固后即形成一连串的焊点。这些焊点相互交叠,就形成了气密填装焊缝,对矩形管座而言,在焊接好的盖板的两条对边后,再将外壳相对电极旋转 90。后,在垂直方向上再焊两条对边,这样就形成了外壳的封装。
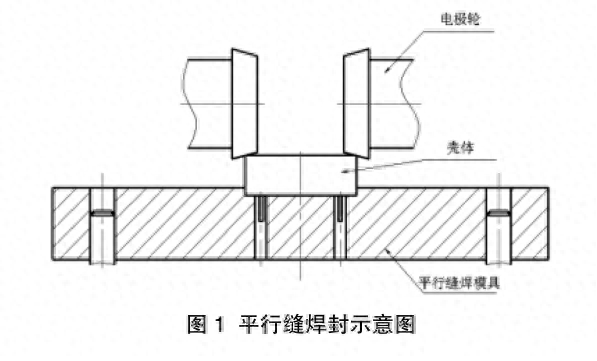
1.2 平行缝焊工艺的主要影响因素
在平行缝焊工艺中,影响其工艺实施好坏的因素有很多,每一个因素控制不当都将影响平行缝焊加工产品的质量可靠性,继而出现各种不良。本文将从人、机、料、法、环几个方面展开分析。
人:平行缝焊工艺实施前,技术人员应调试好设备及匹配好相应的工装夹具,并设置合理的工艺参数。如果设备与工装夹具失配,则可能出现漏焊、瓷裂、打火等不良现象。操作人员需要在加工过程对设备进行操作,将外壳管基、盖板一一对应对位放齐,启动平行缝焊系统进行加工。生产过程中,外壳管基放入工装夹具产品位的准确性和盖板与管基对准的准确性是影响产品合格率的主要因素,如以上操作出现问题则可能出现偏盖、漏焊等不良现象。
机:平行缝焊设备是工艺实施的必要条件,设备由逆变电源、电脑控制主机、显示器、设备运行主机、手套箱组成,每一个部分都是设备运行的关键部件,缺一不可。当设备波动时,可能对平行缝焊工序的运行产生影响。如:当手套箱气密性不足时,会对产品内部气氛控制产生负面影响;当逆变电源输入频率波动时,会对焊缝一致性产生影响;当运行主机伺服电机出现偏差时,会对电极轮压力施加产生负面影响。以上因素对产品质量都有不可忽视的影响,均可能引起产品缺陷率的增加。
料:原材料是影响平行缝焊加工产品性能的最直接因素。对于陶瓷基体的封装外壳来说,多层陶瓷的质量、金属封接环的平整度、关键密封区域材料一致性等都将直接影响产品加工的良率。使用合格的原材料才能生产出高质量的合格产品,所以,需要对原材料进行严格的入厂检验把控。
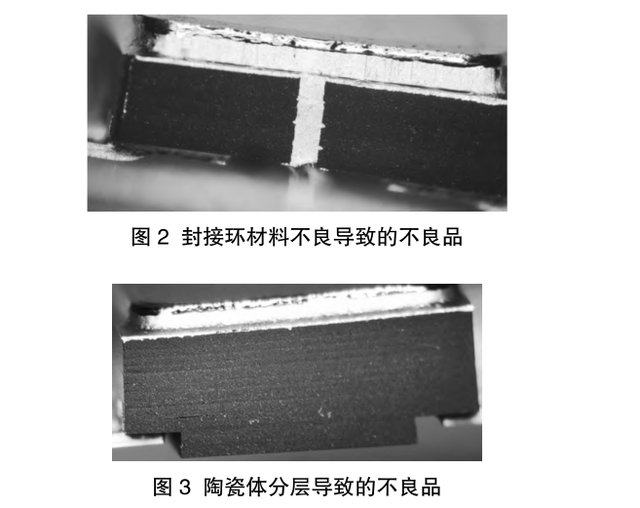
法:在平行缝焊工艺中,主要的封装参数有功率(P)、脉 冲(PW)、周 期(PRT)、速 度(S)、管 座 长 度(L)、工作电流(I)、等效电阻(R)等,其参数之间的关系有:
平行缝焊中的能量公式:

从公式中可以看出,周期和速度与总能量成正反比关系,脉冲、功率、长度与总能量呈正比关系。在实际工艺调整中,需要对合格影响参数进行配合才可得出可靠的缝焊工艺[2]。
环:环境是影响缝焊成品率的关键因素,在气密性集成电路中,对产品内部气氛含量的控制有着严格的要求。其内部水汽含量要求在 100℃下小于5000 ppm,氧气、氢气、二氧化碳对于高质量等级产品也有相应要求。因此,工艺加工一般是在密闭的手套箱中进行,并且在内部需填充 99.999%纯度的高纯氮气,以保证产品加工后内部的气氛含量。当环境不密闭或者氮气原气不纯净时,内部气氛含量将无法控制,焊缝边缘也极易变色,从而产生缺陷品。
1.3 平行缝焊工艺几种主要不良品产生的原因
在我公司平行缝焊工艺加工的陶瓷基体的封装外壳中,打火、漏气、断焊、瓷裂是其主要的不良因素,接下来逐一进行分析。
1.3.1 打火不良
打火是平行缝焊工艺中常见的失效模式之一,该现象出现于电极轮放电过程时。打火主要有两种形式:中间打火和边角打火。通过观察,出现中间打火的产品易在电极轮行程过程中突然打火,通过分析,此类打火主要是因为压力不够或者电极轮与盖板接触面沾污导致。边角打火往往出现于电极轮接触产品的一刻和离开产品的一刻导致,此类打火主要是由于产品移动或者电极行程不够导致。
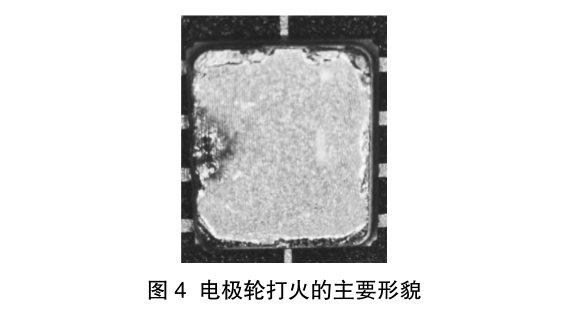
1.3.2 漏气不良
漏气主要是产品在密封加工后,经过氦质谱细检漏和氟油粗检漏发现的产品密封性不足的不良现象。GJB548-2005 标准要求,氦质谱细检漏中细漏率需≤5×10-3 Pa·cm3/s,粗检漏如观测到连续 3 个气泡,则密封性不合格[3]。
平行缝焊产品中,漏气主要有密封区域漏气和管壳基体漏气两个方面。密封区域漏气通常伴随着打火、漏焊等不良现象,管壳基体漏气主要伴随着瓷裂等不良现象。
1.3.3 断焊不良
断焊不良是影响集成电路外壳气密性和外观一致性的主要因素,我公司断焊不良品中,断焊位置主要位于焊边中部,造成此类不良的因素主要有电极轮状态差和夹具不匹配。当电极轮表面状态过差或者材料杂质过多时,在脉冲放电过程中会出现间歇性的放电不均匀和能力消散,导致多个焊点焊接失效。其表面状态过差如磨损严重、使用过久等也会改变电极轮的圆形度,使某一部分行程凹状结构在缝焊过程中无法有效缝焊。如果夹具设计不合理,产品在缝焊过程中发生晃动,也会影响到焊缝的行程造成断焊。
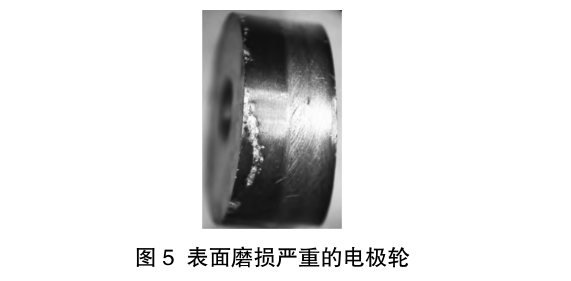
1.3.4 瓷裂不良
陶瓷基体破裂是一种严重的失效模式,通常在密封完成后经外检工序检验发现。造成陶瓷基体破裂的主要原因包括压力过大、能量过大和工装设计不合理等。陶瓷是一种脆性材料,其受力强度在350 MPa 左右,虽然其拥有良好的强度,但同时也有着脆性的特性。当压力过大时,陶瓷无法对承受的力进行有效的消散,从而导致陶瓷体内部过应力积累,继而出现陶瓷裂纹。当能量过大时,多余的能量通过封接环传递至陶瓷基体,高温升和能量的施加会导致陶瓷热应力积累,出现裂纹。当工装设计不合理时,将会导致在合适的工艺参数下,管壳不能将施加的应力进行快速的传递和消散,导致应力集中于管壳上的某一部分,使外壳分裂。除了上述常见的显性裂纹,陶瓷裂纹还会有隐性状态,其隐性裂纹出现在陶瓷体内部,通常很难在生产过程或封装工序一级检验中发现,但在后续的筛选检验过程中,裂纹生长会由隐性裂纹演变为显性裂纹,从而能被发现剔除。
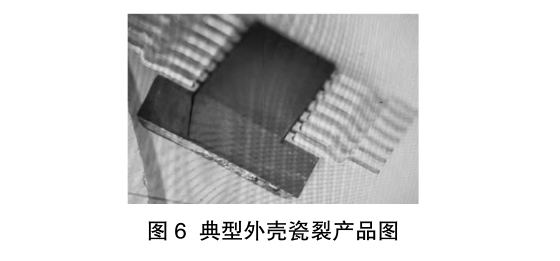
2针对不良的改进措施
2.1 打火不良的改进
通过分析,出现打火现象主要是因为压力不够或者电极轮与盖板接触面沾污导致。边角打火往往出现于电极轮接触产品的一刻和离开产品的一刻导致,此类打火主要是由于产品移动或者电极行程不满足要求而导致。
只有设置适宜的压力值,才能确保生产过程中不出现打火的不良情况,陶瓷基体封装外壳压力参数通常设置在 200 g~350 g 之间。另外,平行缝焊过程中有一个爬坡和下坡的动作,通过数据分析得知,出现边角打火的原因主要是工艺设置不当,没有考虑到外壳的部分离散情况。针对该问题,可以通过在工艺设置中调整延迟距离来解决,保证爬坡下坡过程的一致性。在原有设置中,延迟距离保持在设备默认状态,没有针对不同外壳进行特殊设置,导致部分外壳与初始设置匹配性差,从而引起打火。通过对边角打火率高的封装外壳进行针对性设置后,未发现边角打火情况,此措施有效。
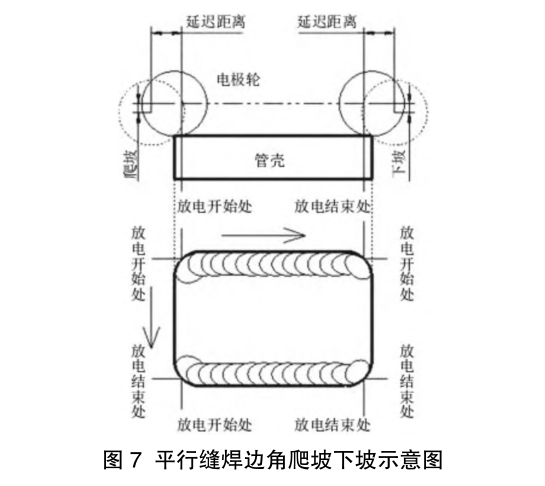
2.2 漏气、断焊不良的改进
漏气、断焊、瓷裂不良现象的产生存在相互交叉的影响因素,因此,接下来将统筹分析并提出改进措施。通过对工艺参数的符合性和产品加工完成后焊缝情况的质量分析,发现工艺参数设置在合理区间范围内,不存在过大或其它异常情况。通过分析,发现若是电极轮在使用过程中更换不及时,会导致在缝焊过后加工的产品,外观有毛刺、部分断焊的情况,因此判定导致断焊、漏气的主要因素是电极轮使用不合理。我公司对不同产品有不同类型的电极轮专门应用,根据材质、角度、缝焊宽度和应用范围等选择适用的电极轮。
在我公司的生产过程中,电极轮寿命为 800 只 /次,更换要求标准为:表面粗糙即可更换。但在实际生产过程中,每天的产量要求为 1200 只 / 天,在高强度的生产中操作人员难以记住生产产品数量和无法准确判断电极轮的表面状态,导致生产中无意地使用表面状态不良的电极轮继续生产。根据上述情况,从程序上进行优化改机,通过软件控制编程,加入了 Electrode Life protection 功能,使电极轮每加工一次移动 0.2 mm 距离,总共移动 2 mm 距离,扩展了电极轮的利用率,使一副电极轮使用寿命提升了5倍,规避了电极轮粗糙继续使用的问题。
2.3 漏气、瓷裂不良的改进
瓷裂产品主要出现在 XXX 产品中,瓷裂图如图8所示,通过观察,此类封装在结构中,瓷裂位置刚好和基体结构拐角处重合。在平行缝焊中,电极轮给管壳施加的是由上而下的力,此类夹具在底部由于管脚的翼型结构呈现悬空状态,观察此类产品工装发现,此类工装没有对于管基悬空部分进行衬底考虑。通过受力分析,当管基受到自上而下的力时,力的作用不能通过外壳直接传导,只能通过外引脚进行力的释放,因此在拐角处可能会出现应力集中,导致瓷体开裂。
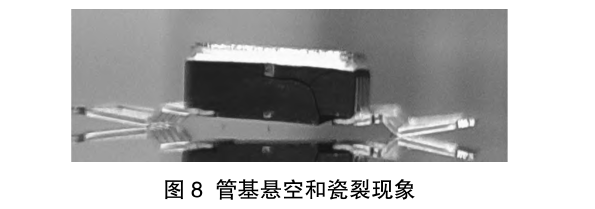
针对瓷裂不良的问题,着重在工装夹具上进行改进和优化,通过对产品的力学设计,对悬空部分增加衬底,保证了垂直力的施加能够通过衬底直接进行释放。通过三维建模,设计出适用的夹具,新夹具应用后,新生产的产品中没有出现类似瓷裂的现象,措施有效。
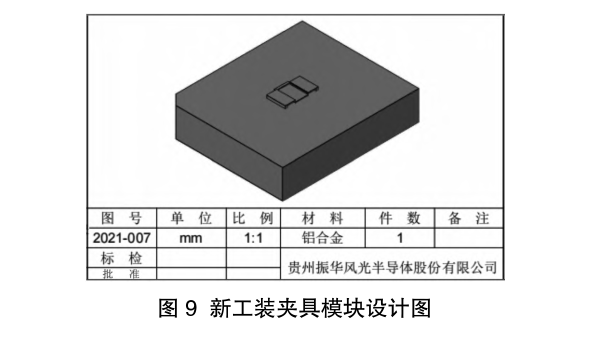
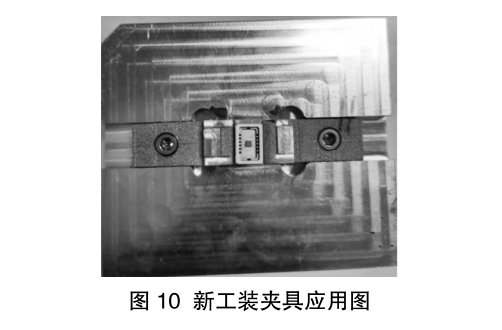
3优化前后对比验证
对打火、漏气、断焊、瓷裂等不良现象进行工艺优化改进后,对 2021 年优化前后的生产情况进行了统计验证,对于期间生产的陶瓷基体平行缝焊工艺封装产品,打火、漏气、断焊、瓷裂等不良现象已不是导致产品失效的主要因素。
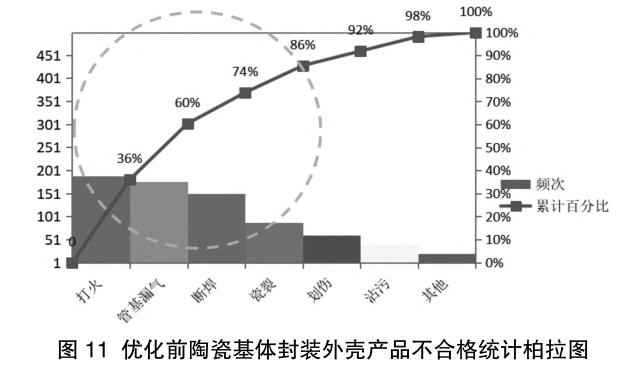
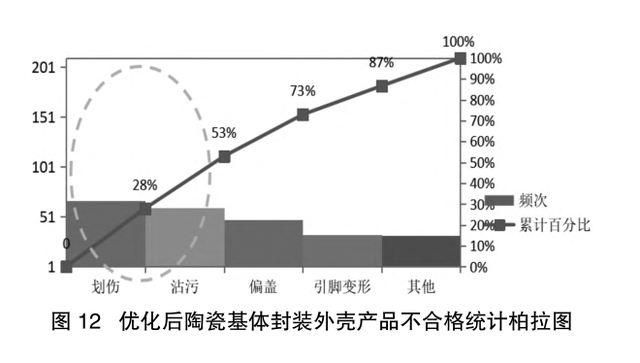
4结束语
通过对陶瓷基体平行缝焊工艺封装工艺的分析,针对打火、漏气、断焊、瓷裂等主要不良影响因素进行工艺优化改进,通过采取电极轮延迟距离的设置、电极轮使用及工装夹具的优化等措施,提升了产品质量与可靠性。