耐湿试验中电子器件锈蚀行为研究耐湿试验中电子器件锈蚀行为研究
吕贤亮,侯小利,李旭
中国电子技术标准化研究院
摘要:
本文针对镀覆层为镀金材料的器件按照GJB 548C-2021方法1004规定进行耐湿试验后发生的锈蚀行为进行了深入研究,考察了器件镀覆层材料及镀层状态对器件锈蚀的影响,主要结合金属发生电化学锈蚀产生条件(电位差、锈蚀介质和锈蚀通道)的理论分析,通过试验对器件镀金和镀镍镀覆层材料与铁基材的电位差及器件平行缝焊部位镀层状态的锈蚀介质分析,揭示器件发生锈蚀的主要因素为器件的镀层材料,而在组装和检测过程中引入的镀层损伤也会加重其锈蚀。
0 引言
电子封装制造中,外壳的镀层工艺是一个十分重要的工艺过程,对于金属封装或陶瓷封装器件外壳,通常会有内镀层、中间镀层及外镀层,工艺目的是赋予封装优良的电性能、焊接性能、热性能、保护性能等,其外镀层材料通常为金、镍。一些产品或者是一些电子设备器件在贮存或者使用过程中,由于所处环境的温度、湿度、空气中的灰尘、锈蚀性气体、盐雾以及生产过程中附在器件表面上的污物等因素,都能够导致设备器件发生锈蚀,有时候微小的锈蚀就能导致器件的失效而使设备丧失使用功能。据一些研究统计,器件锈蚀是电子设备贮存失效的最主要原因之一[1],电子设备在使用或者贮存时器件的锈蚀成为近年来较受关注的一个问题[2]。
对于器件外壳镀层耐锈蚀能力的考核方法在一些标准中都有规定,主要有GJB 548C-2021《微电子器件试验方法和程序》中方法1004耐湿和方法1009盐雾试验[3];GJB 360B-2009《电子及电气元件试验方法》中方法101盐雾和106耐湿试验[4];GJB 128B-2021《半导体分立器件试验方法》中方法1021耐湿和方法1041盐雾试验[5]等。这些标准中对器件外壳的耐锈蚀能力进行了标准试验规定,在整体上试验方法与要求基本一致。
耐湿试验的目的是采用加速方式评定元器件及其所用材料在高湿和炎热(典型的热带环境)条件下抗退化效应的能力,试验提供一个凝露和干燥的交替过程,使锈蚀过程加速,使进入密封外壳内的水汽产生“呼吸”作用。大多数炎热条件下退化现象是直接或间接地由于有缺陷的绝缘材料吸附水蒸气和水膜,以及由于金属和绝缘材料表面变湿而引起的。这种现象会产生多种类型的退化,其中包括金属的锈蚀、材料成分的变化及电特性变化。湿度会对装备产生物理和化学影响,温湿度的变化可以导致装备内部出现凝露现象,与湿度有关的物理现象主要有凝露、吸附、吸收、扩散及呼吸。本文重点讨论器件外壳外镀层采用金或镍时,其耐湿能力的试验结果及分析。
1 试验
1.1 试样
选取基材为铁的某款器件作为试验对象,为验证镀层材料对器件耐湿性能的影响,分别采用外镀层为镀金的镀层结构和镀镍的镀层结构进行试验,试样外观形貌见图1、图2。
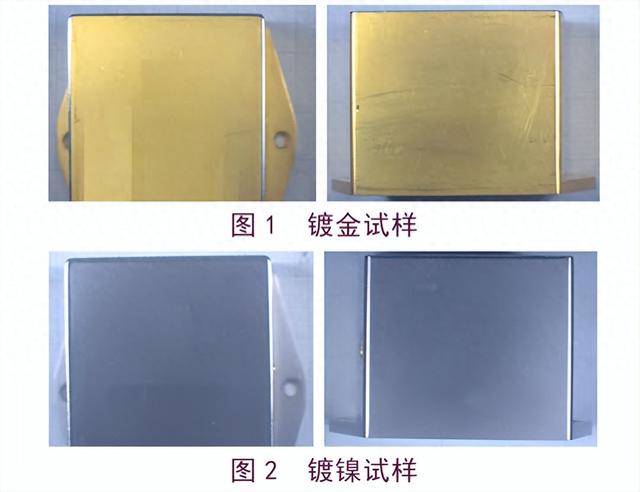
1.2 试验方法
按照GJB 548C-2021中方法1004的规定进行耐湿试验[3],进行10次24h连续循环(见图3)。试验后对其外观进行检查。

1.3 试验结果
镀金试样耐湿试验后试验的外观形貌如图4所示。从图中可以明显看出镀金试样耐湿试验后锈蚀较为严重,特别是封口处锈蚀尤其严重。
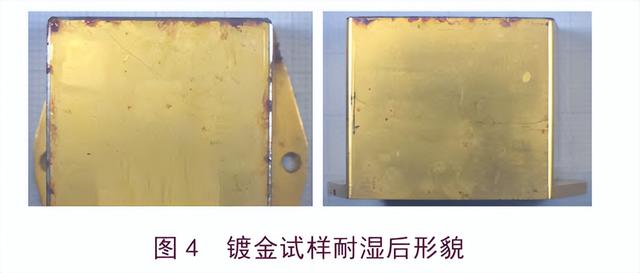
2 试验结果分析
造成器件表面出现锈蚀的原因,主要有以下两种:(1)组装或检测环节控制不当;(2)镀覆层耐湿能力不足,其故障树如图5所示。
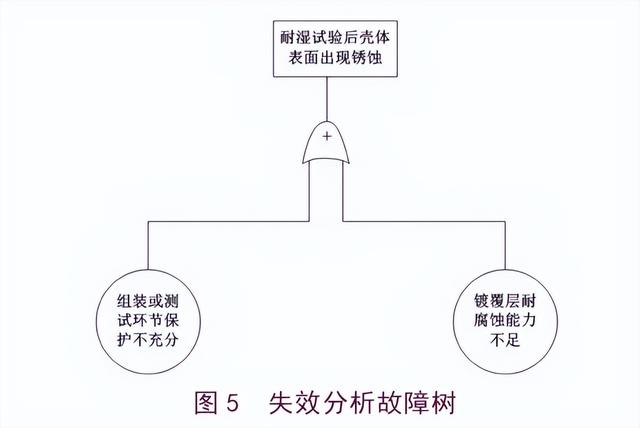
2.1 镀覆层耐锈蚀能力不足
金属外壳镀覆的镀金层为纯金(俗称“软金”),金的含量达99.9%以上。高纯镀金层具
有优良的可焊性和可键合性等组装性能,但软金也有不足,金层硬度低,努氏硬度HK25≤90,金层不耐磨,在装配或试验过程中与工装夹具等稍微摩擦或擦刮,镀层表面轻则留下划痕,稍重镀层可能减薄,如果遇到尖锐物体擦刮,可能 漏 出 底 镀 层 镍 。 镀 金 层 本身 比 较薄 , 约1μm~1.25μm,受外力摩擦,无论擦刮多少,镀金层的破坏会减弱对底镀层及基体的保护。
金属发生电化学锈蚀产生的条件包括电位差、锈蚀介质和锈蚀通道。电位差条件具备,而且电位差非常大,一般来说电位差越大锈蚀动力越足。金属管壳采用的是铁基材表面镀镍镀金,属于阴极性镀层,仅仅起到机械防护作用,不能起到电化学保护作用。镀层中金的标准电极电位为E0Au+/Au=1.68V,E0Fe3+/Fe=-0.036V,E 0Fe2+/Fe=- 0 . 4 4 V , 金 与 铁 之 间 电 位 差 达 到2.12V[6],镀层和基材之间存在较大的电位差,基体金属将作为锈蚀电池的阳极,加速了基体金属的锈蚀。
锈蚀介质同样具备,金属外壳在装配和试验过程中,被污染物污染,常见的污染物有无机污染物和有机污染物,无机污染物如常见的NaCl、KF、MgSO4、CaF2等,有机污染物如常见的有机敖酸(RCOOH),无论是无机污染物还是有机污染物,在潮湿的空气中吸附水汽潮解,形成Na+、K+、Ca2+、Mg2+、Cl-、F-、S-、SO42-以及COO-等阴、阳离子,水解后的阴、阳离子活性高,既是导电介质也是锈蚀介质,通过导电介质传送电子,为锈蚀创造条件,在空气中氧的作用下,加速锈蚀。金属和大气中的氧反应,典型的锈蚀电极反应如下[7]:
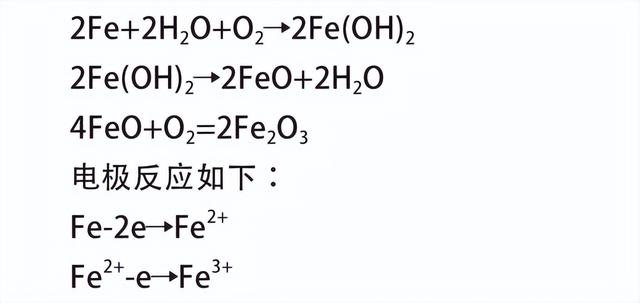
锈蚀生成物可能为FeO或Fe2O3,或者是FeO和Fe2O3的混合物,无论生成哪种锈蚀产物,锈蚀反应均发生。最终管壳在耐湿试验高湿炎热条件下,金属管壳表面发生原电池锈蚀,产生锈蚀点。
2.2 组装或检测环节保护不充分
该试样采用平行缝焊工艺封口,平行缝焊是一种电阻焊,利用两个圆锥形滚轮电极压住待封装的金属盖板和管壳上的金属框,焊接电流从变压器次级线圈流经锥形滚轮电极,电流经过盖板,流过管壳,进行电阻焊接。在焊接过程中,工艺参数不合适,脉冲电流过大,可能会导致局部镀覆层受损。
外壳在装配或检测过程中与工装夹具等稍微摩擦或擦刮,保护不充分可导致表面局部镀层受损。组装或检测环节保护不当可能会减弱镀层对基体材料表面及底面的保护,影响其抗锈蚀能力。
从图3中可以明显看出试样平行缝焊的封口处锈蚀最为严重,平行缝焊破坏了镀覆层,且平行缝焊处平滑性更差,并且在组装和检测过程中更易被划伤而残留污染物,形成锈蚀介质,导致锈蚀。
3 比对分析验证
为了证实上述的分析判断,将采用镀镍层的试样进行同样的耐湿试验。耐湿试验后,试验的外观形貌如图6所示。试验后试样表面完整,没有任何锈蚀现象。根据金属发生电化学锈蚀产生的条件的电位差理论,镀层中镍的标准电极电位为E0Ni2+/Ni=0.25V,镍与铁之间电位差达到0.69V,相对于金镀层的电位差相差3倍多,因而采用镀镍层可极大提高器件的抗锈蚀能力。镀层电位差的降低可以有效提升器件的抗耐湿锈蚀能力。
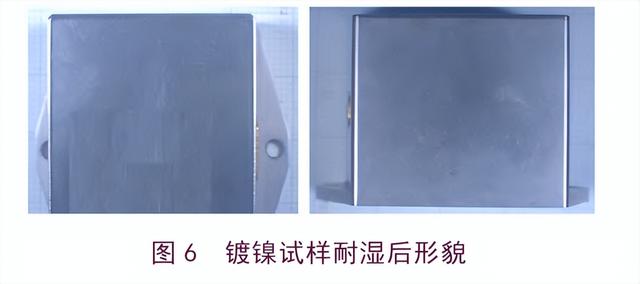
4 结语
本文重点对器件不同镀层材料的抗锈蚀能力及锈蚀产生的原因进行了具体研究,从器件的镀层材料及器件的镀层状态方面开展分析,并进行了比对分析验证。根据试验和理论分析,在常规情况下引起器件锈蚀的主要因素以器件镀层材料为主,而在组装和检测过程中引入的镀层损伤也会加重其锈蚀。