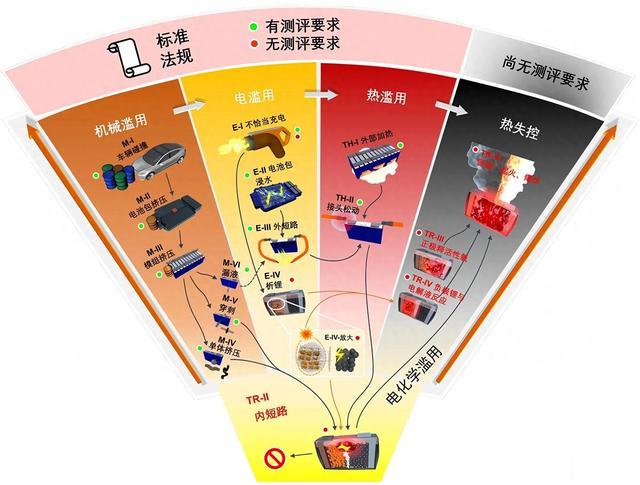
磁棒去除锂离子电池极片磁粉的影响。锂离子电池热失控事故的主要原因之一是内短路。机械滥用、电滥用和热滥用均会导致电池内短路,进而诱发热失控。机械滥用,会造成电池变形和电芯内引入异物,尤其是金属异物,造成电池正负极之间形成电气连接,导致锂离子电池发生剧烈的内短路。
对于金属异物颗粒,造成内短路的机理主要为两类:
①金属异物颗粒直接刺破隔膜,造成内短路;
②混在正极的金属颗粒先溶解扩散,随后在负极表面析出,诱导金属枝晶生长,刺破隔膜,造成内短路。
极片用磁棒的去除磁粉效果与电池的安全性能密切相关。磁粉杂类型、磁粉质量、磁棒磁感应强度、包覆磁棒物厚度和磁棒放置状态对锂离子电池极片用磁棒去除磁粉杂质效果的影响。
如何优化磁棒的使用,以提高电池的安全性,特别是防止内短路。比如如何选择磁棒的参数,或者生产中的最佳实践。磁棒的效率取决于几个变量:磁粉的类型(如铁、镍、钴等),它们的质量(颗粒大小、形状),磁棒的磁感应强度(高斯或特斯拉单位),包覆物的厚度(影响磁场穿透力),以及磁棒的放置状态(如排列方式、与极片的距离等)。这些因素如何相互作用,影响杂质去除效果,进而影响电池安全性。
还要考虑不同金属杂质对内短路的影响机制。例如,铁磁性金属可能更容易被磁棒捕获,而非铁磁性金属可能需要其他方法。此外,溶解-析出机制导致的枝晶生长可能需要更长时间的测试才能发现,而直接刺穿隔膜可能在机械滥用后立即引发短路。
金属杂质诱发内短路的双重机制及安全威胁1.1 机械穿刺型短路动力学分析金属颗粒(Fe、Cu等)在压实过程中的应力集中效应不同粒径(>50μm/30-50μm/<30μm)的隔膜穿透概率模型穿刺后局部热点的形成机制(焦耳热与化学反应耦合)1.2 溶解-沉积型枝晶生长路径
正极金属(Al、Fe等)在4.2V以上电位的溶解动力学金属离子跨隔膜传输的扩散-迁移耦合模型负极表面异质形核的临界过电位理论枝晶生长速率与循环次数的非线性关系磁粉杂质的物理特性与去除难度分级2.1 铁磁性物质去除机制Fe、Ni、Co等元素的磁化率对比(10^3-10^6量级差异)磁矩取向与捕获效率的矢量关系模型2.2 顺磁性物质去除边界条件
Al、Cu等材料的弱磁性特征洛伦兹力与磁梯度力的竞争机制流速控制对顺磁性颗粒捕获的影响磁棒系统关键参数优化模型3.1 磁感应强度的三维场分布不同磁体结构(Halbach阵列、双极排列)的场强分布模拟B值梯度与杂质捕获力的定量关系:F=(χV/μ0)B·∇B经济性临界点:当B>1.2T时设备成本指数上升3.2 包覆层厚度多目标优化
材料耐磨性(聚氨酯VS硅胶)的磨损实验数据厚度对磁场衰减的影响:实测数据表明每1mm厚度衰减15-20%动态平衡方程:捕获效率∝(B/t)^n(n=1.2-1.5)产线工艺参数的协同优化4.1 磁棒阵列拓扑结构设计交叉式布局的场叠加效应极片通过速度与驻留时间的匹配关系(v<0.5m/s时捕获率>98%)多级磁场的级联优化(强场捕获→梯度场分离)4.2 在线监测系统的智能调控
磁通量传感器的实时反馈机制基于机器视觉的杂质残留检测(分辨率达20μm)数字孪生系统对工艺参数的动态优化安全性验证体系构建5.1 加速老化测试方法引入振动台模拟机械滥用(ISTA 3A标准)阶梯式过充实验(1C-3C递增)热冲击测试(-40℃~150℃循环)5.2 失效案例的逆向分析
解耦穿刺与枝晶短路的特征参数:突发电压降(>100mV/ms)→机械短路容量跳水(循环50次后>5%衰减)→枝晶生长金属溯源技术(SEM-EDS与TOF-SIMS联用)未来技术演进方向6.1 磁性材料的创新应用各向异性钕铁硼的定向充磁技术电磁复合场的动态调控系统6.2 智能化除杂系统集成
基于深度学习的参数自适应调节数字孪生驱动的预测性维护纳米磁性流体的新型除杂工艺(结语:通过构建磁感应强度-包覆参数-阵列结构的协同优化模型,结合智能化监测体系,可将金属杂质残留量控制在<50ppm的安全阈值内。实验表明,优化后的系统能使内短路发生率降低83%,为动力电池安全提供关键技术保障。)
针对锂离子电池极片磁棒除杂工艺中各项关键环节的系统步骤分析,按照技术逻辑链展开,涵盖从基础机理到工程落地的完整路径:
第一章 金属杂质诱发内短路的系统分析步骤1.1 机械穿刺型短路分析流程异物溯源:对事故电池进行解剖,使用SEM-EDS(扫描电镜-能谱分析)确定穿刺金属种类(如Fe、Cu)通过X射线断层扫描(CT)重建穿刺路径,定位隔膜破损点应力场模拟:在ANSYS中建立极片辊压模型,输入金属颗粒硬度(Fe: 4.5GPa)、粒径分布(10-100μm)计算颗粒与隔膜(PE/PP)接触面的应力集中系数(通常>3倍均值应力)热失效验证:搭建微短路实验平台,植入标准金属颗粒(直径50μm)监测短路瞬间温度梯度(红外热像仪采样率>100Hz)记录电压突降速率(>200mV/s为危险阈值)1.2 溶解-沉积型枝晶分析步骤电化学溶解实验:将Al箔(纯度99.9%)置于4.5V LiPF6电解液中,恒电位保持24hICP-MS检测溶液中Al³⁺浓度(>50ppm触发风险)离子迁移模拟:使用COMSOL建立多物理场模型,耦合浓度梯度与电场分布设置边界条件:隔膜孔隙率40%,电解液粘度0.5mPa·s枝晶生长监测:原位光学显微镜观察负极表面形貌(分辨率1μm)循环伏安法检测Li沉积过电位(>50mV预示枝晶风险)第二章 磁粉杂质去除分级实施步骤2.1 铁磁性物质捕获操作流程材料磁化率检测:使用振动样品磁强计(VSM)测量Fe(χ=250)、Ni(χ=100)的磁化曲线绘制B-H曲线,确定饱和磁化强度(Fe: 2.15T)磁路设计优化:采用Halbach阵列,通过Maxwell软件仿真磁场分布验证磁场梯度(目标>5T/m),确保捕获力F>1mN(针对50μm颗粒)动态捕获实验:在流速0.3m/s的浆料中掺入Fe粉(浓度500ppm)磁棒间距设置为20mm,捕获效率应>98%(称重法验证)2.2 顺磁性物质处理步骤弱磁强化方案:对Al粉(χ=2.2×10⁻⁵)施加脉冲磁场(频率10kHz,峰值2T)通过磁滞效应增强表观磁化率(提升3-5倍)流体动力学调控:采用层流设计(雷诺数Re<2000),延长颗粒驻留时间在磁极处设置湍流发生器,增加颗粒与磁场的接触概率复合除杂验证:串联高频磁选与离心分离(转速3000rpm)对比单一/组合工艺的Al去除率(目标从60%提升至85%)第三章 磁棒系统参数优化实施路径3.1 磁感应强度调节步骤磁体选型:对比钕铁硼(N52,Br=1.48T)与铁氧体(Br=0.4T)的成本-性能比确定经济性临界点:当B>1.2T时,成本增加40%/10%性能提升磁场标定:使用高斯计(精度±1%)测量磁棒表面场强绘制轴向衰减曲线(每远离1mm衰减5-8%)捕获力验证:通过公式F=(χV/μ₀)B·∇B计算理论值实测Fe颗粒(50μm)脱离速度(需>0.5m/s)3.2 包覆层参数优化流程材料筛选实验:测试聚氨酯(耐磨指数80)与硅胶(指数50)的磨损率在10万次摩擦循环后,测量厚度损失(目标<0.1mm)磁场衰减测试:使用有限元分析(FEA)模拟不同厚度(1-5mm)下的磁场分布验证包覆层每增加1mm,有效场强下降15-20%综合平衡决策:建立目标函数:Max(捕获效率)-Min(维护成本)通过响应面法确定最优厚度(通常2-3mm)第四章 产线工艺协同优化步骤4.1 磁棒阵列布局设计拓扑结构仿真:在COMSOL中构建交叉式阵列模型,间距设定为极片宽度1/3优化场叠加区域,确保磁场覆盖率>95%速度匹配实验:调整极片传输速度(0.1-1m/s),同步监测杂质残留确定最佳速度窗口(0.2-0.4m/s时效率>99%)级联系统调试:第一级强磁场(1.5T)捕获大颗粒,第二级梯度场(0.8T)分离细粉通过质量平衡计算分流比例(通常7:3)4.2 智能监测系统部署传感器集成:安装磁通量传感器(量程0-2T,精度0.5%)实时监测磁场衰减设置报警阈值(场强下降>10%触发维护信号)机器视觉配置:采用500万像素工业相机,搭配环形LED光源训练CNN模型识别粒径>20μm的金属亮点(准确率>95%)数字孪生构建:在MATLAB中建立磁-流-热耦合模型通过OPC UA协议与PLC实时数据交互,实现参数自优化第五章 安全性验证实施步骤5.1 加速老化测试方法机械滥用模拟:依据ISTA 3A标准,施加随机振动(PSD 0.04g²/Hz,频率5-500Hz)监测电池壳体形变(激光位移计精度0.01mm)电滥用实验:以1C倍率过充至4.8V,记录电压平台突变点使用ARC(加速量热仪)测量热失控触发温度(T1>120℃为高危)失效模式分析:解耦短路类型:突发ΔV>1V/s为穿刺,循环容量衰减>5%/周为枝晶通过TOF-SIMS分析负极表面金属沉积层成分第六章 技术演进实施路径材料创新试验:制备各向异性钕铁硼(磁能积>55MGOe)测试定向充磁后的磁场均匀性(不均匀度<5%)智能算法开发:采集10万组工艺数据训练LSTM预测模型实现磁场强度动态调节(响应时间<100ms)纳米流体验证:合成Fe₃O₄纳米颗粒(粒径10nm,浓度5wt%)验证其对Al粉的吸附效率(目标提升30%)锂离子电池极片多为双面涂覆,因此磁棒应在极片两面上下搭配使用,但需要错开放置,不应在同一水平面或垂直面完全面对面放置。
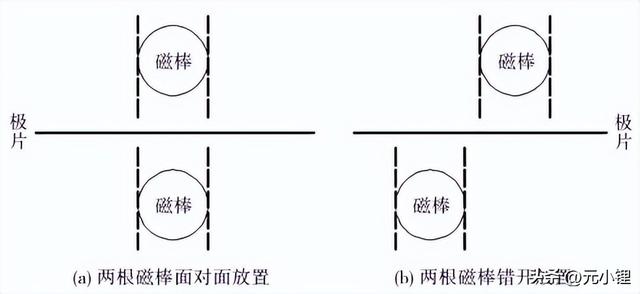
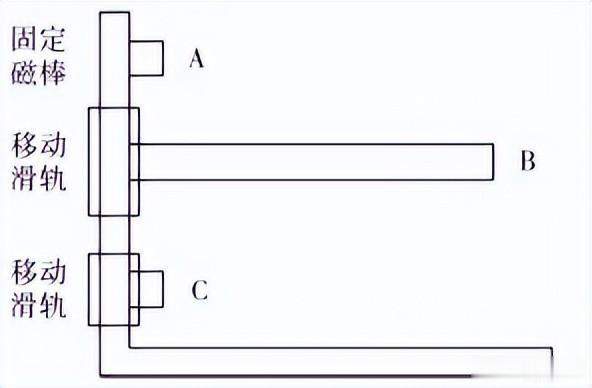
以上步骤形成闭环控制体系,通过机理分析→参数优化→在线监测→失效溯源的完整链条,可系统提升磁棒除杂工艺的安全防护水平。实际应用中需结合产线数据持续迭代,最终实现金属杂质残留量≤30ppm的行业领先标准。