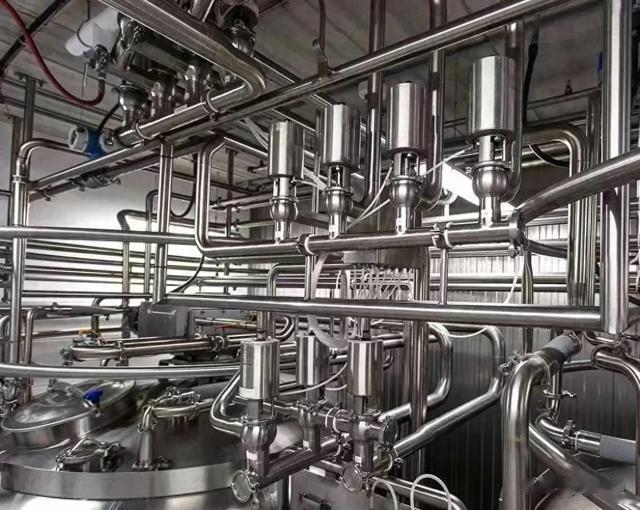
锂电池作为现代电子设备和电动汽车的“心脏”,其性能直接决定了设备的续航能力和使用寿命。而在锂电池制造中,注液工艺是决定电池性能的核心环节之一,尤其是电解液的浸润度,直接关系到电池的充放电效率、循环寿命甚至安全性。
1.电化学性能离子传导:电解液浸润度直接影响锂离子在电极材料中的传输效率。良好的浸润能确保电解液充分接触电极材料,降低内阻,提升电池的充放电性能。反应均匀性:浸润不足会导致电极表面反应不均匀,形成局部热点或死区,影响电池的容量和寿命。2.安全性热管理:浸润不良会导致局部电流密度过高,产生过多热量,增加热失控风险。枝晶生长:不均匀的浸润可能引发锂枝晶生长,刺穿隔膜,导致短路,甚至引发火灾或爆炸。3.循环寿命电极退化:浸润不足会加速电极材料的退化,导致容量衰减和循环寿命缩短。界面稳定性:良好的浸润有助于形成稳定的固体电解质界面(SEI)膜,减少副反应,延长电池寿命。4.制造工艺一致性:注液工艺要求电解液均匀分布,确保电池性能一致,避免批次差异。生产效率:浸润度影响注液速度和效率,良好的浸润能缩短注液时间,提高生产效率。5.成本控制材料利用率:良好的浸润能提高电解液利用率,减少浪费,降低生产成本。质量控制:浸润不良会增加废品率,提高质量成本。锂电池注液工艺的三大挑战与未来趋势一、注液工艺的三大核心挑战1. 精准控制注液量难点:注液量需与电极孔隙率、电解液粘度、电池设计容量严格匹配。过量会导致电解液溢出或界面副反应,不足则引发浸润不均。高能量密度电池(如高镍三元、硅基负极)对注液量的误差容忍度更低(通常要求误差<2%)。现有解决方案:采用高精度注液泵(如蠕动泵、伺服电机驱动),结合在线称重系统实时反馈。开发电解液动态分配算法,结合电极孔隙率建模优化注液量。未来方向:结合AI预测模型,通过电池设计参数(如电极厚度、压实密度)自动计算最优注液量。2. 多孔介质的复杂渗透难点:电极孔隙呈多尺度分布(纳米级活性颗粒孔隙+微米级涂层间隙),电解液需渗透至所有孔隙才能实现有效浸润。高镍正极表面高碱性易与电解液反应生成钝化层(如Li2CO3),阻碍渗透;硅基负极膨胀收缩导致孔隙动态变化。现有解决方案:优化电极结构:通过造孔剂或梯度涂层设计,提升孔隙连通性(如特斯拉的“干电极”技术)。低粘度电解液配方:添加氟代溶剂(如FEC)降低表面张力,增强毛细作用。未来方向:开发“自修复”电解液,动态填充硅基负极膨胀产生的孔隙。引入超临界CO2辅助注液技术,利用超临界流体高扩散性加速渗透。3. 工艺参数的精密调控难点:注液工艺需协同控制真空度(0.1-10 Pa)、温度(20-60°C)、压力(0.1-1 MPa)等多参数,非线性耦合关系复杂。固态电池注液需兼顾固态电解质与液态电解液的兼容性(如硫化物电解质对溶剂敏感)。现有解决方案:多物理场仿真(如COMSOL模拟电解液流动与电极浸润过程)。闭环控制系统:通过压力传感器、红外成像实时监控浸润状态,动态调整参数。未来方向:数字孪生技术:构建工艺参数与电池性能的映射模型,实现全流程虚拟调试。二、未来趋势:从“浸润度”到电池性能的闭环1. 材料体系升级带来的新需求高镍正极(NCM811/NCA):需匹配高浸润性、低阻抗电解液(如含LiPO2F2添加剂),抑制界面Ni/Li混排和氧气释放。硅基负极(SiOx/Si-C):体积膨胀(>300%)导致孔隙塌陷,要求电解液具备动态填充能力(如弹性粘结剂+柔性SEI膜)。2. 技术路径突破固态电池注液工艺:半固态电池需精准控制液态电解液与固态电解质的比例(如QuantumScape的“混合润湿”技术)。全固态电池可能转向“干法电极+原位固化”工艺,减少液态注液依赖。智能闭环控制:通过电化学阻抗谱(EIS)实时监测浸润状态,反馈调节注液参数。数据驱动工艺优化:利用机器学习分析生产数据,预测最优注液策略。3. 行业竞争的关键指标(2030年展望)精度:注液量控制误差需<1%,电极浸润均匀性>99%。效率:注液时间压缩至10秒/电芯以内(当前平均30-60秒)。兼容性:支持从液态到半固态电解液的多场景工艺切换。三、应对策略与技术创新方向设备升级:开发多自由度注液机器人,支持复杂电池结构(如叠片、刀片电池)的定向渗透。材料创新:设计“自适应电解液”(如含纳米SiO2的剪切增稠电解液),动态匹配电极体积变化。工艺融合:预锂化技术与注液工艺结合,补偿硅基负极首次循环的锂损耗。总结未来锂电池注液工艺的核心矛盾在于:如何在高精度、高效率的前提下,满足多孔介质动态渗透与复杂界面稳定性的双重需求。突破方向将围绕“材料-工艺-设备”协同创新展开,最终实现从“浸润度达标”到“电池性能可控”的闭环升级。到2030年,注液工艺的智能化与柔性化能力,或将成为企业能否在固态电池时代占据技术高地的关键分水岭。
系统性实施步骤建议
1.前期准备材料选择:选择高纯度、低粘度的电解液,确保其具有良好的浸润性和化学稳定性。设备检查:确保注液设备(如注液机、真空系统、烘箱等)处于良好状态,定期维护和校准。环境控制:在干燥间或手套箱中进行注液,控制湿度(通常低于1% RH)和温度(通常为20-25°C)。2.电极预处理干燥处理:在注液前对电极进行真空干燥,去除水分和挥发性有机物,通常干燥温度为80-120°C,时间为12-24小时。表面处理:对电极表面进行等离子处理或化学处理,提高表面能,增强电解液的浸润性。3.注液工艺真空注液:将电池放入真空注液机中,抽真空至一定压力(通常为0.1-1 Pa),然后注入电解液。真空注液有助于排除电极孔隙中的空气,提高浸润度。分步注液:采用分步注液法,先注入少量电解液,静置一段时间(如10-30分钟),再进行二次注液,确保电解液充分浸润。加压注液:在注液过程中施加一定压力(如0.1-0.5 MPa),促进电解液快速渗透到电极孔隙中。4.浸润过程静置浸润:注液后,将电池在室温下静置一段时间(如4-12小时),使电解液自然浸润电极材料。加热浸润:在静置后进行加热处理(如40-60°C,2-6小时),加速电解液的扩散和浸润。5.化成工艺预充放电:进行小电流充放电(如0.02-0.1 C),形成稳定的固体电解质界面(SEI)膜,确保电池的初始性能。老化处理:在化成后进行老化处理(如25°C,7天),进一步稳定电池性能。6.质量检测浸润度检测:通过扫描电子显微镜(SEM)或X射线断层扫描(CT)检测电极的浸润情况,确保电解液均匀分布。电性能测试:进行内阻测试、容量测试和循环性能测试,评估电池的电化学性能。安全测试:进行过充、过放、短路和热冲击等安全测试,确保电池的安全性。7.数据记录与分析过程记录:详细记录注液工艺参数(如真空度、注液量、静置时间等)和检测结果。数据分析:对记录的数据进行分析,优化工艺参数,提高生产一致性和产品质量。8.持续改进反馈机制:建立反馈机制,根据检测结果和客户反馈,持续改进注液工艺。技术创新:关注行业最新技术,引入新材料、新设备和新工艺,提升生产效率和产品质量。总结通过以上系统性实施步骤,可以有效提高锂电池注液工艺的电解液浸润度,确保电池的性能、安全性和一致性。同时,持续改进和技术创新是保持竞争力的关键。