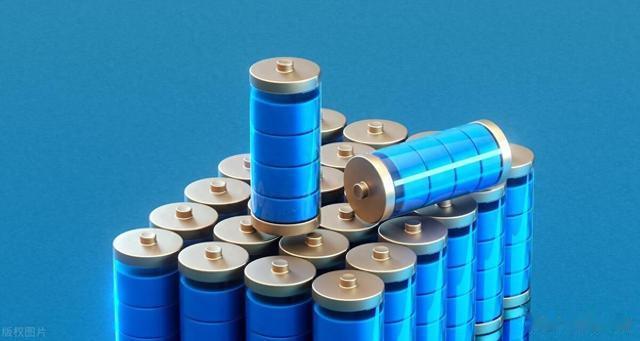
电芯部分出现低容问题。首先确认分容工艺是否设置错误(比如放电电流、充电时间、截止电压和分容温度是否有异常);①如果分容工步设置无问题,就需要更换测试点之后对电芯进行重新分容,查看是否为分容设备和通道出现了问题。②假设更换设备后分容数据没异常,那就是设备存在问题。③若复测之后依旧低容,那就可以确认低容问题真的存在了 。
1. 人(Man)可能原因:操作人员未按标准作业程序(SOP)操作,例如分容参数设置错误(如充电截止电压、电流设置偏低)。新员工培训不足,导致操作失误(如电池极性接反、夹具未压紧)。分容后电池静置时间不足,未充分释放极化电压。改进措施:复查SOP并强化操作培训,增加现场监督及考核。对异常批次的操作记录进行追溯,确认是否存在人为失误。引入防错机制(如扫码校验参数、设备自检报警)。2. 机(Machine)可能原因:分容设备(充放电柜)电流/电压精度偏差(未定期校准)。分容夹具接触不良,导致内阻升高或实际充放电电流不足。设备老化或散热不佳,导致测试过程中电流波动。改进措施:对分容设备进行全面校准,验证电流/电压的实际输出值。清洁或更换磨损的夹具触点,确保接触电阻<1mΩ。检查设备散热风扇及电源稳定性,排除环境干扰。3. 料(Material)可能原因:电芯原材料问题:正极材料克容量偏低(如LCO、NCM批次差异)、负极压实密度过高导致锂离子嵌入困难。电解液不足或浸润不充分,导致有效锂离子迁移率低。隔膜孔隙率异常或厚度不均,影响离子电导率。改进措施:对低容电芯拆解分析,检查极片涂布均匀性、电解液浸润状态。追溯异常批次材料的供应商数据(如正极材料ICP分析、隔膜孔径测试)。优化注液工艺,延长浸润时间或增加高温静置步骤。4. 法(Method)可能原因:分容工艺参数设置不当(如充电截止电压低于设计值、放电倍率过高导致容量未完全释放)。化成工艺异常(如SEI膜过厚消耗活性锂)。分容前未进行预充电或老化流程,导致容量测试不准确。改进措施:验证分容程序参数是否与设计规格一致(如4.2V截止电压)。对比低容电芯与正常电芯的化成曲线差异(如恒流/恒压阶段时间)。优化分容前的静置或老化条件(如25℃下静置24小时)。5. 测(Measurement)可能原因:分容设备数据采集系统误差(如电流传感器漂移)。测试环境温度波动(如低温下电池实际容量下降)。容量计算公式错误(如积分时间间隔设置不合理)。改进措施:将低容电芯在其他分容柜复测,排除设备单机故障。监控分容车间温度并确保恒温(25±2℃)。核对容量计算软件逻辑(如Ah积分算法)。6. 环(Environment)可能原因:分容车间温湿度过高或过低(如温度<15℃导致锂离子扩散速率下降)。车间洁净度不足,粉尘污染电池极耳或夹具。电池存储环境不当(如长期高温存放导致自放电加剧)。改进措施:加装温湿度监控及自动调控系统(推荐湿度<30%RH)。升级车间洁净度至万级,定期清洁分容柜内部。缩短电芯分容前存储时间(<7天),避免自放电累积。综合分析及验证建议:数据分层分析:统计低容电芯的分布规律(如设备编号、操作班次、材料批次),锁定共性因素。交叉实验:将异常电芯与正常电芯互换设备/工艺参数,验证问题复现性。拆解分析:对低容电芯进行拆解,检查极片、电解液、隔膜状态,确认是否存在微观缺陷(如析锂、枝晶)。通过以上系统性排查,可快速定位根本原因(如某批次正极材料克容量不足或设备电流漂移),并制定针对性纠正措施(如更换材料批次、校准设备)。
系统性排查
阶段一:快速数据收集与问题定位数据分层统计设备维度:统计低容电芯的分布是否集中在特定分容柜(如设备A出现30%低容,其他设备正常)。时间维度:分析低容电芯的生产日期/班次,是否与某次换班、参数变更或材料切换时间重合。材料批次:核查低容电芯是否来自同一批正极材料、电解液或隔膜供应商批次。操作人员:确认低容电芯是否由同一班组或新员工操作。横向对比分析选取正常电芯与低容电芯,对比以下数据:分容充放电曲线(恒流/恒压阶段时间、电压平台差异)。内阻、开路电压(OCV)、自放电率(K值)。极耳焊接电阻(若差异显著,可能为接触问题)。阶段二:分步排查与验证设备与参数验证设备校准:对分容柜进行电流/电压精度校准(例如用标准电阻和万用表验证实际输出与设定值是否一致)。夹具检查:测量夹具接触电阻(目标<1mΩ),清洁氧化层或更换磨损触点。环境监控:记录分容车间温湿度数据(目标25±2℃、湿度<30%RH),排除低温导致容量衰减。材料追溯与验证材料批次核查:调取低容电芯对应的正极材料ICP成分分析报告(如Ni/Co/Mn比例是否偏离规格)。电解液浸润检查:拆解低容电芯,观察极片和隔膜的浸润状态(若局部干燥,需优化注液工艺)。隔膜孔隙率测试:对异常批次隔膜进行SEM扫描或Gurley测试,确认孔隙率是否达标。工艺与操作复查SOP符合性检查:现场观察操作人员是否按标准设置分容参数(如充电截止电压4.2V、静置时间≥2h)。化成工艺复盘:检查低容电芯的化成曲线,确认SEI膜形成是否异常(如恒流时间过短导致活性锂损失)。静置时间验证:延长分容前静置时间至24小时,观察容量是否恢复(排除极化电压影响)。阶段三:交叉实验与根因确认复测与交叉实验设备互换:将低容电芯转移到其他分容柜复测,若容量正常,则原设备存在硬件故障。参数对比:在同一设备上分别运行标准参数和调整参数(如降低放电倍率),验证容量差异。材料替换实验:使用已知合格材料替换疑似异常批次材料,重新生产电芯并测试容量。拆解分析(破坏性检测)极片分析:测量低容电芯正/负极涂布面密度(如正极面密度偏低导致克容量不足)。SEM/EDS检测:观察正极材料颗粒形貌及元素分布(如材料团聚或杂质导致锂离子迁移受阻)。电解液成分检测:通过GC-MS分析电解液分解产物(如过量LiPF6分解消耗活性锂)。阶段四:闭环验证与标准化根本原因确认通过上述实验锁定关键因素(例如某批次正极材料克容量偏低、分容柜电流传感器漂移)。验证改进措施有效性(如更换材料后低容率从5%降至0.3%)。预防措施与标准化更新控制计划(如增加正极材料入厂克容量抽检比例)。建立设备定期校准制度(如每周用标准电池校验分容柜)。优化工艺参数(如延长电解液浸润时间至48小时)。排查工具推荐统计分析:使用Minitab进行柏拉图(Pareto)分析,识别主要低容贡献因素。DOE实验设计:针对多变量交互影响(如温度+静置时间),设计正交实验优化参数。8D报告:记录排查过程并形成闭环报告,避免问题复发。通过以上系统性排查,可高效定位问题根源(如材料批次异常或设备精度失控),并推动长期改进。