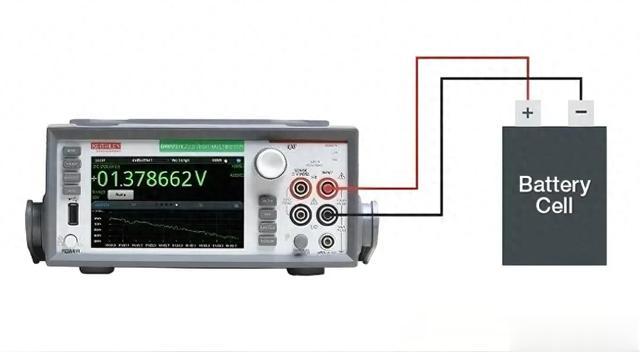
锂电池的电压监测是确保其安全与性能的核心环节,其重要性体现在对电池状态的精准把控和潜在风险的提前预警。
一、电压监测的关键目的
(一)安全防护
1. 过充/过放防护:锂电池因化学特性存在特定工作电压窗口,例如三元锂电为2.5V - 4.2V,磷酸铁锂为2.5V - 3.65V 。过充可能致使正极材料结构崩塌、电解液氧化分解,释放诸如CO₂、O₂等热量和气体,甚至引发热失控;过放会造成负极铜集流体溶解,生成枝晶引发短路。电压监测通过实时对比预设阈值(如±50mV冗余设计),触发电池管理系统(BMS)切断充放电回路。
2. 热失控预警:电压的异常波动(如突降)可能预示着电池内部微短路或固体电解质界面膜(SEI膜)破裂,结合温度数据能够提前预警热失控风险。
(二)性能优化
1. 荷电状态(SOC)估算:电压与SOC呈非线性关系,以磷酸铁锂为例,其平台区较为平坦。需结合开路电压(OCV)模型或混合算法(如扩展卡尔曼滤波)来提升估算精度,将误差控制在<3% 。
2. 健康状态(SOH)评估:电池老化后,满电电压下降、内阻上升,通过循环中电压曲线的偏移量(如满电电压降低50mV对应约10%容量衰减)可间接评估其健康状态。
3. 均衡管理:电池组内单体电压差异若>50mV需进行被动均衡,>100mV则需主动均衡,该差异直接影响电池组的可用容量。监测数据可驱动均衡电路工作,延长电池组使用寿命。
二、电压监测的技术要点
(一)高精度采集
1. 模拟 - 数字转换器(ADC)选择:至少应具备12位分辨率(最低有效位LSB<1mV),采样率≥1kHz以捕捉瞬态波动。例如,特斯拉BMS采用16位ADC实现了±2mV的精度。
2. 抗干扰设计:采用差分测量、屏蔽线缆及数字滤波(如移动平均、有限脉冲响应FIR)等方法抑制共模噪声,在高压电池包(如800V平台)中尤为重要。
(二)动态阈值管理
1. 温度补偿:在低温环境(-20℃)下,电压平台会下移,需动态调整截止电压(如充电上限从4.2V降至4.0V),防止锂析出。
2. 工况自适应:大电流充放电时,欧姆极化会导致电压瞬时偏移(如1C放电瞬间压降约0.3V),BMS需区分暂态与稳态电压,避免误触发保护。
(三)多参数融合分析
1. 内阻计算:通过脉冲测试(ΔV/ΔI)获取直流内阻(DCR),结合电压变化可诊断接触不良或电池老化情况。
2. 一致性监测:统计电池组内单体电压标准差(如>30mV为异常),能够定位故障单体(如自放电率异常)。
三、深度分析:技术挑战与前沿方向
(一)挑战
1. 平台区精度困境:磷酸铁锂在20% - 80% SOC区间电压变化仅约30mV,传统OCV法误差较大,需引入混合动力脉冲特性(HPPC)测试或弛豫电压分析。
2. 多尺度耦合效应:快充(如4C)会导致浓差极化与电化学极化叠加,使电压信号呈现复杂非线性,需建立多物理场模型(如P2D模型)辅助解析。
(二)前沿技术
1. 人工智能(AI)驱动预测:利用长短期记忆网络(LSTM)学习电压时序特征,预测微短路趋势,如蔚来电池云系统。
2. 阻抗谱分析(EIS):通过宽频带交流激励获取频域阻抗,解析SEI膜增长、锂沉积等老化机制,与静态电压数据互补。
四、实践
(一)BMS设计
采用分布式拓扑(每个模组独立ADC),减少长线缆干扰。
(二)校准策略
定期静置(>2小时)获取OCV,修正SOC模型漂移。
(三)失效模式覆盖
设计冗余通道(如双ADC采样),防止单点故障。
电压监测如同锂电池的“神经末梢”,其技术深度贯穿电化学机理与系统工程。未来随着固态电池等高电压体系(>5V)的普及,对监测精度与响应速度的需求将进一步提升,推动电压传感技术向高集成度、多维度感知方向演进。