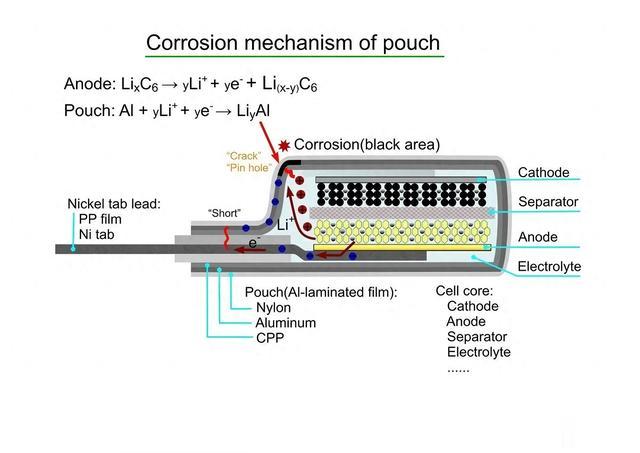
引起电芯腐蚀必须具备两个短路的通道:
①离子短路通道,即包装铝箔铝层与阳极发生离子短路
铝箔的结构:内部为绝缘 PP,PP的一个作用就是绝缘,将电解液环境与铝层隔离,保护铝层,发生离子短路是由于PP发生破损致使电解液渗透将铝层与阳极导通,因此腐蚀均发生在 PP破损部位。
②电子短路通道,即包装铝箔铝层与阳极发生电子短路
导体在阳极和铝层(PP破损处)间能够导通电子或阳极通过Nitab直接与铝层短路导通电子。
这样包装铝箔的铝层就与阳极形成一个短路的回路,阳极即为电芯负极,处于低电势的部分,一旦与铝接触会通过电导率较高的电解液引起电化学反应,化学反应,导致铝层的不断被消耗。空气中水分会进入电芯内部导致进一步反应产生大量气体。这两种短路是电芯发生腐蚀的必要条件,两者缺一不可。
一、铝塑膜腐蚀问题的工程背景1.1 软包电池封装体系特征
典型结构:尼龙外层(12-25μm)/铝箔层(40-60μm)/CPP层(30-50μm)
铝层功能:阻隔水氧(透湿率<0.1g/m²·day)、电磁屏蔽、结构支撑
失效阈值:铝层腐蚀深度>5μm时阻隔性能下降90%
1.2 腐蚀现象表征
宏观表现:电解液渗透→铝层白斑→封装鼓胀(体积膨胀>5%)
微观特征:Al→Al³+氧化(电位差>1.5V vs Li+/Li)
电性能劣化:自放电率>3%/月,DCR上升>20%
二、离子短路通道形成机制2.1 铝/负极界面电化学体系
电解液浸润路径:CPP层结晶缺陷(尺寸>0.5μm)→Al层暴露
腐蚀反应链式过程:Al + 3LiPF6 → Al(PF6)3 + 3Li+ + 3e- (ΔG=-217kJ/mol)Al³+ + e- → Al²+ (E=1.66V vs SHE)
离子迁移特征:Li+通量密度>10^-5 mol/(cm²·s)

2.2 腐蚀产物输运模型
多孔介质效应:Al2O3钝化膜孔隙率>30%时形成导通路径
浓差极化:界面Cl⁻浓度梯度>0.1mol/L/cm
SEI膜破坏:腐蚀产物嵌入导致膜阻抗上升>200Ω·cm²

三、电子短路通道演化过程3.1 机械失效诱因
折叠应力:曲率半径<5mm时Al层裂纹扩展速率>0.1μm/cycle
热膨胀失配:ΔT=50℃时界面剪切应力>50MPa
枝晶穿刺:Li枝晶生长速率>1μm/h穿透CPP层
3.2 电子传导路径构建
金属间接触:Al/石墨直接接触面积>0.1mm²
隧穿效应:界面间距<5nm时量子隧穿概率>10^-3
微电弧放电:局部电流密度>10A/cm²诱发热点(T>300℃)
四、双通道耦合效应分析4.1 交互作用动力学
离子/电子传导协同系数K=σ_ion·σ_elec/(σ_ion+σ_elec)
腐蚀扩展速率:初期以离子通道主导(v≈1μm/day),后期电子通道加速(v>10μm/day)
热失控临界点:双通道并联电阻<100Ω·cm²时Q=10^6J/m³
4.2 失效模式转变
阶段I:点蚀引发离子泄漏(循环50周内)
阶段II:裂纹扩展形成电子通路(循环50-200周)
阶段III:双通道并联引发热失控(循环200周后)
五、防护技术体系构建5.1 材料改性方案
阳极侧:开发AlF3涂层(厚度2-3μm,击穿电压>10V)
电解液:添加0.5wt% LiBOB缓蚀剂(腐蚀电流降低80%)
封装层:三层共挤CPP(结晶度>65%,针孔密度<5个/m²)
5.2 工艺控制要点
化成工艺:预钝化处理(0.1C恒流至3.8V维持24h)
封装参数:热封温度185±5℃,压力0.4MPa,时间8s
环境控制:注液房露点<-40℃,O₂<10ppm
六、检测与评估方法6.1 在线监测技术
电化学噪声检测:电流波动>10nA/√Hz判定微短路
红外热成像:温差>2℃定位腐蚀热点
超声扫描:分辨率10μm检测层间剥离
6.2 加速老化模型
湿热循环:85℃/85%RH条件下腐蚀速率加速系数K=15
电化学加速:施加1.5V偏压时失效时间缩短至1/20
机械振动:10-2000Hz扫频测试封装结构完整性
结论:
通过构建铝塑膜腐蚀的双通道理论模型,从材料界面工程、电化学体系优化、制造过程控制三个维度建立防护体系,可将软包电池循环寿命提升至2000周以上,年失效率控制在0.5%以内。