宝马大圆柱电池VS比亚迪刀片电池:技术路线之争,谁在定义未来?
在动力电池领域,宝马与比亚迪正以截然不同的技术路径争夺话语权。前者即将量产的大圆柱电池与第六代eDrive技术剑指“电动时代的终极驾控”,后者则以刀片电池构筑起“安全即正义”的技术护城河。当德系豪华品牌的工程思维遇上中国品牌的场景创新,这场对决或将重塑全球动力电池的技术版图。

宝马选择46mm标准直径的大圆柱电芯,本质上是特斯拉4680电池的“德系升级版”。代表车:特斯拉cyberchuck,不过价格过高,因此暂时没有全面普及该品牌全部车型。
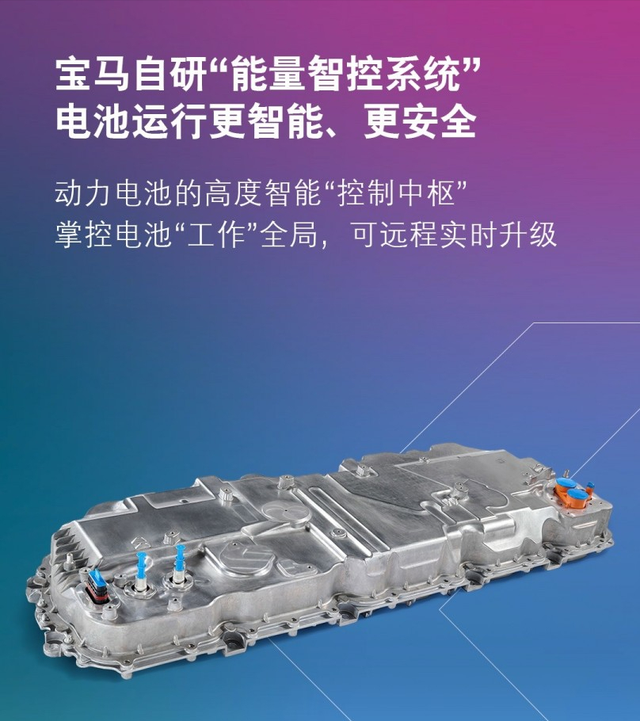
宝马大圆柱电芯通过高度定制化的95mm/120mm电芯设计,配合无模组(CTP)与电池车身一体化(CTB)技术,其电池包厚度减少15%,整车重心降低20mm,直接转化为更极致的操控体验。这种“自上而下”的工程逻辑,将电池作为底盘开发的核心要素,追求结构与性能的精密耦合。
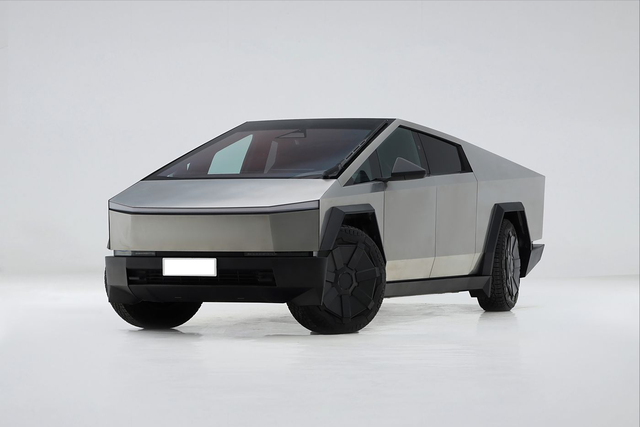
比亚迪刀片电池则开创了磷酸铁锂的形态革命。通过将电芯拉长至960mm并采用叠片工艺,电池包体积利用率提升50%以上。其本质是“以空间换性能”,在有限成本下实现续航与安全的平衡。这种“自下而上”的创新路径,更注重电池系统与整车空间的适配效率。
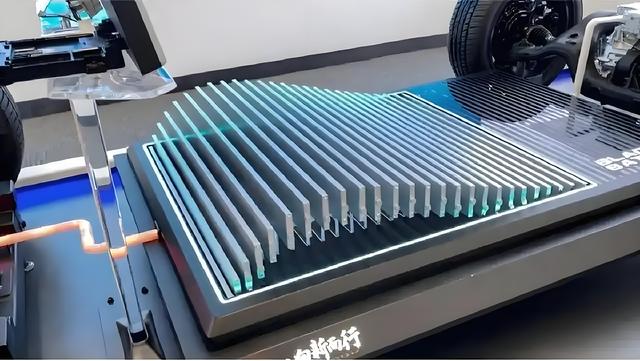
宝马大圆柱电池依托高镍三元体系,能量密度较前代方形电池提升20%,配合800V高压平台实现“充电10分钟补能300公里”的超充性能。其技术突破点在于:通过一体化压铸技术将电芯间距压缩至0.6mm,散热效率提升30%;智能温控系统可实时调节每个电芯的工作状态,确保性能输出的稳定性。
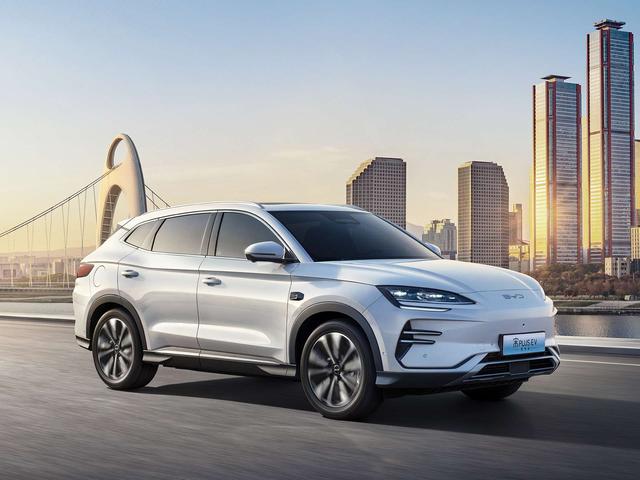
刀片电池则坚守磷酸铁锂路线,虽然单体能量密度(180Wh/kg)仍低于三元锂,但凭借独特的蜂窝状排列结构和全球首创的“电池包通过针刺测试”技术,将热失控风险降至最低。其核心优势在于:循环寿命突破4500次,全生命周期成本降低40%;通过结构创新弥补材料短板,实现“安全不妥协前提下的续航突围”。
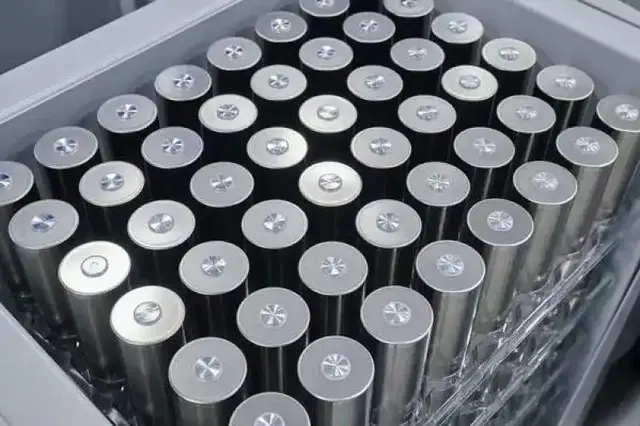
宝马大圆柱电池的生产链充满“德系精密制造”烙印:与宁德时代共同开发的激光焊接技术可将电芯装配精度控制在0.1mm级;兰茨胡特工厂的数字化产线实现每2秒下线一个电芯;沈阳基地的第六代产线整合了300个智能质检节点。这种高举高打的制造体系,瞄准的是豪华车市场对极致性能的溢价支付能力。
比亚迪则展现出中国制造的规模化优势。刀片电池产线通过独创的“六面体定位”技术,将生产节拍缩短至1.2秒/片;重庆“刀片电池超级工厂”的产能规划达135GWh,足够装备300万辆电动车。这种“技术普惠”路线,正推动磷酸铁锂电池在全球市场的份额从30%攀升至60%。
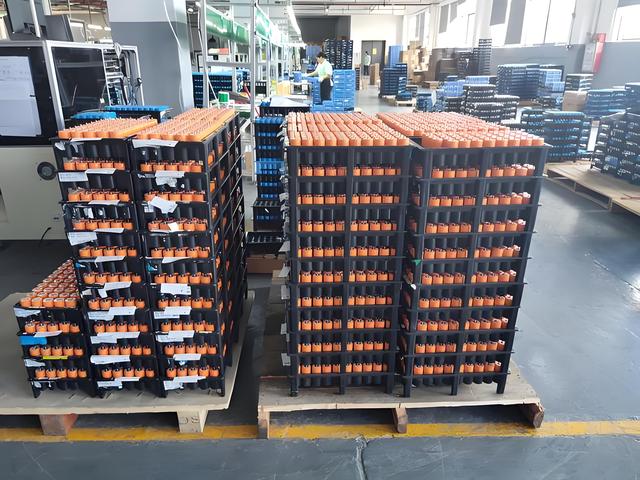
宝马大圆柱电池的创新属于“系统级突破”:
机械结构重构:电池包与车身的深度集成,使底盘刚度提升40%;能量管理跃迁:BMW能量智控系统可同时调度高压电池与低压电气网络,能耗管理精度达毫秒级;材料工艺革新:新型硅碳负极使电芯膨胀率降低70%,支持更高倍率充电。
比亚迪刀片电池则实现了“基础材料突破”:
磷酸铁锂性能天花板突破:通过纳米涂层技术将导电率提升5倍;制造工艺革命:全球首创的“高速叠片”技术,将生产效率提升200%;全场景适配:从A0级海鸥到豪华腾势D9,单一电池形态覆盖全品类车型。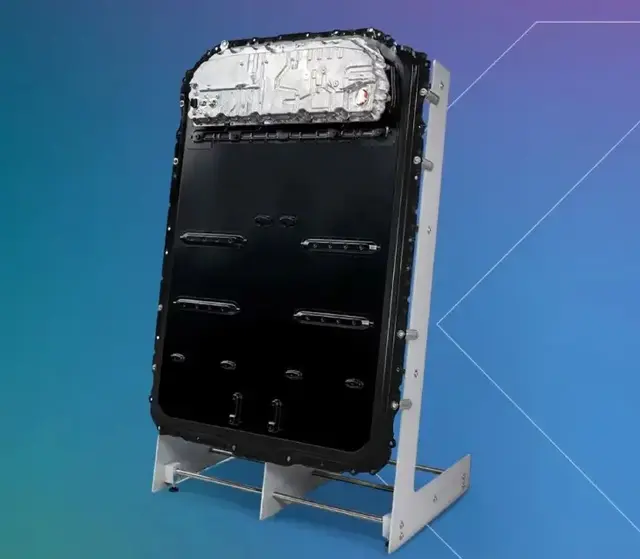
这场对决本质上反映了电动化浪潮下的技术分化:宝马选择用“性能升维”捍卫豪华品牌溢价,其大圆柱电池在能量密度(260Wh/kg)、快充功率(350kW)等硬指标上确实领先;比亚迪则通过刀片电池证明,在主流市场“安全+成本”才是真正的核心竞争力。值得关注的是,宝马已启动磷酸铁锂技术储备,而比亚迪也在研发高镍三元电池——两条技术路线终将走向融合。
在动力电池的竞技场上,没有绝对的胜利者。宝马大圆柱电池重新定义了豪华电动车的工程标准,而比亚迪刀片电池则改写了动力电池的经济学公式。当技术创新从单点突破转向系统竞合,这场“圆柱与刀片”的对话,或许正在孕育下一代动力电池的终极形态。