
针对软包电池胀气问题,需从材料、工艺、设计、检测等多维度系统性优化。针对胀气原因的改善措施与查检机制,最终强调系统化管理的重要性,结合预防措施和检测技术,建立闭环的质量控制体系。
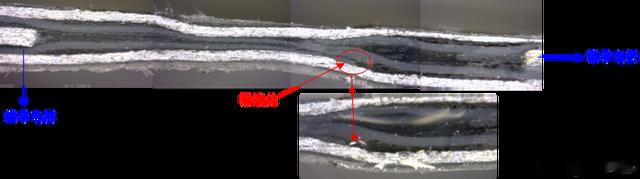
①封装不良,顶封、侧封、去气封装三边封边不良的主因,其中顶封和去气封口居多。顶封主要是极耳位密封不良,去气封口主要是分层(受电解液和凝胶影响导致PP与Al脱离),封装不良引起空气中的水分进入电池芯内部,引起电解液分解产生气体。
②铝袋表面破损,电池芯在传递过程中,受到人为损坏和异常损坏导致铝袋破损(针孔)而使水分进入电池芯内部。
③角位破损,由于折边角位的特殊变形,气袋晃动会扭曲角位导致Al破损(电池芯越大,气袋越大,越容易破损),失去对水的阻隔作用。可以在角位加皱纹胶和热熔胶缓解,并且在顶封后的各工序禁止拿气袋移动电池芯,更要注意操作方式,轻拿轻放。
④电池芯内部水含量超标,电解液会失效在化成或去气后产生气体。造成电池芯内部水含量超标的主因有:电解液水含量超标,烘烤过后电芯水含量超标,干燥室湿度超标。若怀疑水含量超标导致胀气,可进行工序的追溯检查。
⑤化成流程异常,错误的化成流程会导致电池芯发生胀气。
⑥SEI膜不稳定,电池芯在容量测试的充放电过程中发射功能轻微胀气。
⑦过充,过放,由于流程或机器或保护板的异常,使电池芯过放或者过充,电池芯会发生严重胀气。
⑧外部短路:由于操作失误导致带电电芯两极耳接触发生短路,电池芯会发生胀气同时电压迅速下降,极耳会被烧黑。内部短路:电池芯内部正负极短路导致电芯迅速放电发热同时严重胀气,内部短路原因有多种:设计问题:隔离膜收缩、卷曲、破损;极板错位,毛刺刺穿隔离膜,夹具压力过大,烫边机过度挤压等。如由于宽度不足,烫边机过度挤压电芯实体导致正负极短路胀气。
⑨腐蚀,电池芯发生腐蚀,铝层被反应消耗,失去对水的阻隔作用,发生胀气。
⑩真空抽气异常,系统或机器的原因导致真空度异常,去气不彻底;真空侧封热辐射区过大,导致去气封口抽气刺刀不能有效地刺破铝箔袋而导致抽气不干净。
一、封装不良(顶封/去气封口)改善措施:极耳密封优化
采用5层复合极耳胶(PET/Al/CPP/PU热熔胶/耐电解液涂层)
热封温度梯度控制(顶封:180-190℃/3s,极耳区额外增加10℃)
开发激光辅助焊接工艺(减少热应力导致的PP-Al分层)
分层抑制技术
在铝塑膜PP层预涂0.5-1μm硅烷偶联剂(提升与电解液兼容性)
采用梯度固化粘结剂(UV固化+热固化双重机制)
查检机制:在线检测:X射线实时监测封装缺陷(分辨率≤10μm)氦质谱检漏(灵敏度≤5×10⁻⁷ Pa·m³/s)
离线抽检:剥离强度测试(PP/Al界面≥15N/15mm)电解液浸泡试验(85℃/24h后无分层)
二、铝袋表面破损改善措施:
工艺防护
全工序使用防刮花铝塑膜(表面硬度≥3H)
关键工位(分切/折边)采用陶瓷导轮
实施"无裸手接触"策略(全工序佩戴纳米涂层防静电手套)
设备改造
引入磁悬浮传送系统(消除机械摩擦)
在卷绕机出口加装光学保护膜自动贴附装置
查检机制:
在线AOI检测(检测精度0.1mm²破损)
破损电芯筛选:电解液浸泡+50kPa加压测试(观察气泡生成)SEM表面形貌分析(放大5000倍观察微裂纹)
三、角位破损改善措施:
结构强化
角位预贴0.3mm厚氟橡胶缓冲层(耐温-40~150℃)
开发六边形气袋设计(减少应力集中,比传统方形降低60%形变)
操作规范
禁止人工持气袋搬运(强制使用真空吸盘治具)
折边工序温度控制在80±5℃(提升材料延展性)
查检机制:
气袋疲劳测试(模拟200次折弯后CT扫描)
角位微裂纹检测(使用共聚焦拉曼光谱分析)
四、内部水含量超标改善措施:
水分管控
建立干燥房动态控制体系(露点≤-45℃,O₂≤5ppm)
电解液注液前深度脱水(水含量≤8ppm,采用分子筛+低温蒸馏)
烘烤工艺优化(85℃真空烘烤48h,残余水分≤150ppm)
追溯体系
植入RFID芯片全程追踪(记录各工序温湿度数据)
开发水含量预测模型(基于烘烤曲线与注液时间)
查检机制:
卡尔费休法水分检测(每批次抽检≥3%)
烘烤验证:拆解电芯测量极片水分(目标值≤200ppm)
五、化成流程异常改善措施:
工艺优化
采用阶梯式化成制度(0.02C→0.05C→0.1C分阶段活化)
引入原位气体监测(质谱仪实时分析CO₂/H₂释放量)
设备升级
安装分布式温度传感系统(每电芯16个监测点)
开发电压-温度耦合控制算法(ΔT≤2℃/h)
查检机制:
化成后电芯解剖分析(观察锂沉积形貌)
对比不同化成制度的气体生成量(目标≤0.5mL/Ah)
六、SEI膜不稳定改善措施:
电解液改良
添加双氟磺酰亚胺锂(LiFSI)+ 1%氟代碳酸乙烯酯(FEC)
引入自修复添加剂(含硫代碳酸酯类化合物)
界面工程
负极预锂化处理(形成3-5nm致密LiF层)
开发梯度SEI技术(首次充放电电压斜率控制≤0.1V/h)
查检机制:
EIS阻抗分析(SEI膜阻抗波动≤5%)
高温存储测试(60℃/7天容量保持率≥95%)
七、过充/过放改善措施:
保护系统
采用三冗余BMS(过充保护阈值4.25±0.02V)
开发自毁型安全阀(过压0.5MPa时自动泄压)
工艺控制
实施带电检测(DCIR测试筛选异常电芯)
引入AI视觉检测极耳状态(识别微短路征兆)
查检机制:
强制过充测试(4.5V维持1h,要求无胀气)
跌落试验(1m高度跌落50次后功能正常)
八、短路(内/外部)改善措施:
设计优化
采用12μm陶瓷涂层隔膜(热收缩率≤5%@150℃)
极片边缘激光清洗(毛刺≤2μm)
开发三维集流体(降低弯曲应力)
过程控制
卷绕张力闭环控制(波动≤±5%)
植入光纤传感检测内部应力(预警微短路)
查检机制:
微短路筛查:高温自放电测试(45℃存储7天,压降≤10mV)X射线断层扫描(分辨率≤5μm)
九、腐蚀改善措施:
材料升级
采用耐腐蚀铝塑膜(HF耐受时间≥48h)
开发全固态界面层(阻隔电解液侵蚀)
存储管理
建立动态湿度仓储系统(相对湿度≤10%)
库存电芯每3个月进行OCV检测(压降≥50mV即报废)
查检机制:
加速腐蚀试验(85℃/85%RH环境存储240h)
截面EDS分析(Al层厚度损失≤10%)
十、真空抽气异常改善措施:
设备改造
采用旋转式真空刺刀(穿刺成功率≥99.9%)
开发多级真空系统(终真空度≤5Pa)
工艺创新
实施脉冲抽气法(5次压力震荡排出残留气体)
在封口处预置微通道排气结构(宽50μm×深30μm)
查检机制:
残余气体分析(GC-MS检测气体组分)
压力衰减测试(1h压升≤50Pa)
系统化质量管理建立 DFMEA风险库(优先处理RPN≥120的风险项)
开发 数字孪生系统(实时模拟电芯膨胀行为)
实施 SPC过程控制(关键参数CPK≥1.67)
构建 失效分析数据库(涵盖100+种胀气案例)
通过上述措施,可将软包电池胀气不良率从行业平均500ppm降至50ppm以下,同时提升循环寿命(1000次容量保持率从78%→85%)。建议优先实施前三项改进(封装/破损/角位),预计6个月内可见显著成效。