半导体芯片切割加工品质的评价方法
方素平 小森雅晴 赵宇 植山知树 广恒辉夫 梅雪松
(西安交通大学 机械制造系统国家重点实验室 日本京都大学 工学院精密
工学系 ∙陕西省计量科学研究院 日本 TOWA 株式会社)
摘要:
在对日本一些著名半导体生产企业实际生产中所用的质量控制方法和企业生产规范进行认真分析的基础上提出了一组具有代表性的主要检测项目和相应的检测方法。设计了一组芯片切割实验方案并进行了切割实验对所提出的检测项目及要求逐项进行了检测。明确了在正常切割条件下各项指标出现不合格品可能性的大小证明了所提出的检测项目和检测方法对于控制芯片切割品质的有效性。研究成果对于芯片切割加工品质评价方法的规范化和标准化对于高速切割机的设计和切割工艺的制定等均具有重要的参考价值。
0 引言
随着半导体制造技术的进步大规模集成电路的集成度越来越高除 CPU 芯片和大规模存储器芯片等少数芯片外在笔记本计算机、液晶显示器、数码相机、手机及各种随身携带的视频与音像制品中大量使用的 IC 芯片其成品的外形尺寸已经变得非常小。
本文主要就采用高速切割机切割半导体芯片切割品质的评价方法进行探讨。在对国际上的现行评价方法进行充分分析之后进行了大量的切割实验并对实验结果进行了分析和对比在此基础上提出了一套可以有效控制半导体芯片切割质量的实用性评价方法及其相应的评价指标。
1 芯片切割加工品质的现行评价方法
目前国际上对芯片切割加工品质的评价指标有很多没有形成统一的标准世界著名企业都有自
己的质量控制方法或生产规范[1-2] 较小的企业则参考著名企业的做法制定出自己的检测项目。在这些企业自定的质量控制和评价指标中有些项目是一致的但具体指标值也有所不同而有些项目则完全因企业而异。从日本几家著名半导体制造企业实施的检测项目中可以找出一些具有代表性的主要检测项目将其列于表1中[1-2] 。按照检测方法的不同这些主要检测项目可以分为芯片总体外观的观测项目和芯片切断面形状尺寸的检测项目两大类。
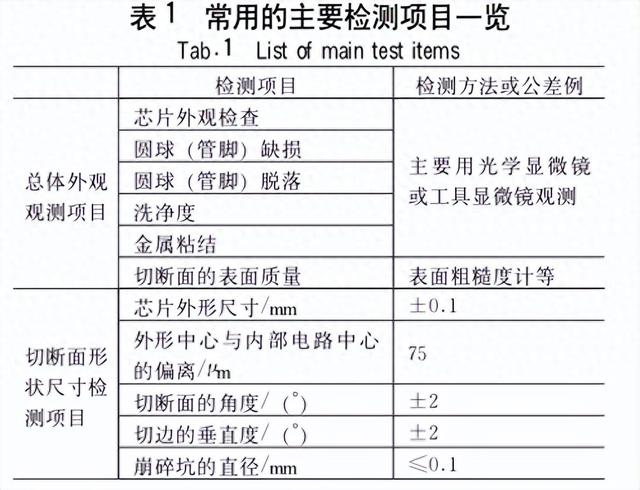
芯片总体外观的观测检查被认为是非常重要的它可以给发生故障或出现某种问题的产品提供很多有益的信息以帮助查明原因。对于刚切割成片的芯片其主要检查项目有:芯片外观检查、管脚缺损、管脚脱落、芯片的洗净度、断面上的金属粘结、切断面的表面质量等。这些项目一般采用光学显微镜或工具显微镜人为地进行观察和测量因为现行的检查方法中大多没有规定具体的判断指标值观察和测量的结果受人为因素的影响较大。但切断面的表面质量一般参照机械制造行业粗糙度的定义和检测方法给出较为具体的指标值检测时也用表面粗糙度计进行精确测量。
芯片切断面的形状和尺寸的检测项目主要有:芯片外形尺寸、切断面的角度、芯片外形中心与内部电路中心的偏离、切边的垂直度、崩碎坑的大小等 (见 图 1)。其 中芯 片 外 形 尺 寸 A、 B、C、 D 的公差一般参照机械制造行业长度量的公差给出如±0∙1mm 等;断面的角度在每个断面上各有2个如图1 (a) 中的 E、 F 和 G、 H;切边的垂直度指芯片正面相邻2边的垂直度误差;芯片外形中心与内部电路中心的偏离用从芯片断面到四个角上的小球中心的尺寸之差来衡量如图1 (b)中的 I、 J、 K、L;崩碎坑系指断面上的树脂在切割过程中出现崩碎而形成的坑目前一般仅用崩碎坑的直径 L 来衡量其大小并进行判断 (见图2)。
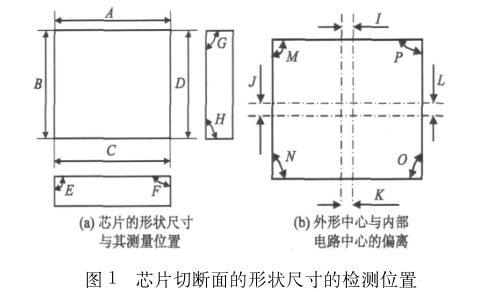

上述切断面的形状尺寸的检测项目多用工具显微镜来检测和观察有条件的企业也用三坐标测量机等精度更高的检测设备来测量。
2 芯片切割实验的条件和实施方法
为了对芯片在不同的切割条件下的切割品质进行分析和评价从中找出一些具有普遍意义的规律对实用中的评价方法进行修改提出一套适用的评价方法设计了一组切割实验。芯片切割实验的切削条件如表2所示所用的砂轮为一种圆型薄片砂轮砂轮的安装位置为其外圈最低处低于被切割基板的底边0∙1mm以保证将被切割基板切断[3]。
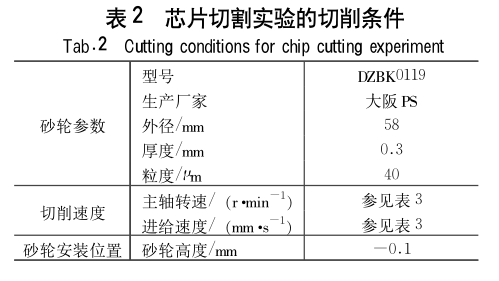
切割时所用的主轴转速 v轴 和进给速度如表3所示。由于所用切割机的最高转速为30000r/min实验时所用的转速不能超过这个值。常见的芯片基板有有机材料基板和铜板基板两种对于有机材料基板其进给速度 v有机板可以高一些目前生产中常用50~80mm/s实验时最高 做 到 了310mm/s;对于铜板材料基板其进给速度 v铜板 要低一些生 产 中 常 用20~30mm/s实 验 时 最 高 做 到 了200mm/s。将表3中的主轴转速和进给速度进行排列组合分别进行切割实验并对切割完的芯片逐项进行检测和分析。
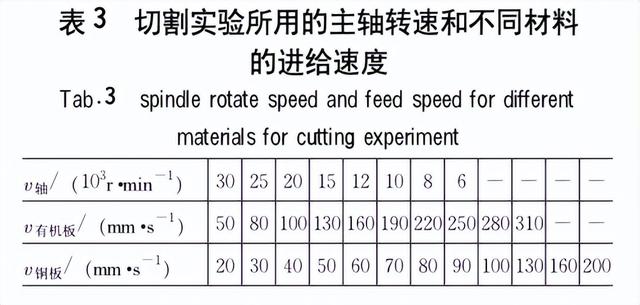
3 芯片切割实验的结果及其分析
3∙1 芯片总体外观的观测结果
在工具显微镜下对上述实验中切割出来的各种不同芯片进行观测得到的结果如下:
3∙1∙1 芯片外观检查
外观检查的项目主要有:芯片有无破损、有无发生变色、有无出现剥离、有无裂纹及其大小等。检查结果表明在正常的切割条件下出现上述明显缺陷的可能性极小。但对于重要的芯片应该特别注意裂纹的检查因为裂纹比较难以发现而常常出现遗漏而裂纹中容易渗入湿气和其他杂质是导致芯片出现故障的重要原因。国外常用荧光液渗透法来查微小的裂纹效果比较好[1] 。
3∙1∙2 管脚缺损或脱落
这类芯片的管脚以小圆球形居多如图3所示。检查结果表明没有发现管脚脱落或较为明显的缺损发现个别芯片上的管脚有少许轻微的机械性损伤认为是由其他原因所致而非由切割所引起。说明正常切割情况下由切割致伤管脚的可能性极小。
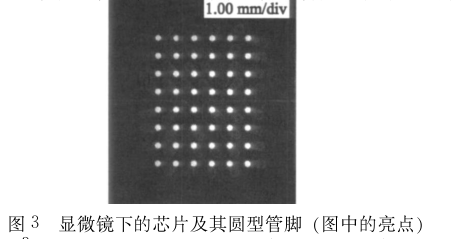
3∙1∙3 洗净度
洗净度主要检查以下项目:高速切断时所产生的树脂粉末、水分、油脂成分及其他残渣异物有无附着在管脚等处因为这些绝缘性材料如果附着在管脚等处将直接影响到芯片的正常工作。检查结果表明在正常洗净工艺下几乎没有发现明显的上述附着物说明切割本身并不会导致更难洗净但如果在切割时采用胶带纸来粘贴固定芯片则应特别注意胶带纸的残留。
3∙1∙4 金属粘结
金属粘结主要是芯片机体内的铜丝在切断过程中发生的由于铜的韧性很好一般都会不同程度地发生粘连需要对断面中铜丝的粘连程度进行检查。由于粘连情况的复杂性目前也没能像机械制造行业那样给出具体的数字来进行判断检查时仍有赖于人的经验判断。检查结果表明在主轴转速较高时发生粘连的程度较轻难以看到有明显的粘连 (见图4 (a))基本上属于正常的范围之内但转速较低时应引起注意[3] 。

3∙1∙5 切断面的表面质量
切断面的表面质量指的是其表面粗糙度但由于芯片的切断面不同于机械零件的表面没有配合、接触、承受载荷等方面的要求实际给出的粗糙度值都非常低。实验结果表明采用高速切割法切断的芯片其断面比较光滑 (见图4 (b))实测的粗糙度值一般都小于有关厂家所提出的值。因此正常切割时实际上没有必要采用粗糙度计来监测。但在主轴转速较低时其表面粗糙度较差 (如图2所示)有可能出现不合格品[3] 。
3∙2 芯片切断面的形状和尺寸的检测结果
芯片切断面的形状和尺寸的检测也在工具显微镜上进行检测结果如下:
3∙2∙1 芯片外形尺寸
实际切割出来的芯片有可能出现倾斜的情况。因此检测时芯片外形的长和宽均采取在两端分别进行检测的方法将同一芯片两端的尺寸都检测出来如图1 (a) 中的 A 和 C 及 B 和 D。判断时不仅要对单个尺寸的检测结果进行判断还要算出两端尺寸之差根据差值判断是否被切成了喇叭口形等。检测结果表明以通常的速度进行切割时芯片的外形尺寸精度都能满足要求但在主轴转速较低特别是进给速度较快时会出现少量的尺寸不合格品[4-6] 。
3∙2∙2 切边的垂直度
检测结果表明以通常的切割速度进行切割时芯片四边的垂直度一般均能满足要求但在主轴转速较低和 (或) 进给速度较快时会出现个别不合格品。
3∙2∙3 切断面的角度
检测结果表明用现行的切割速度即主轴转速为30000r/min有 机 材 料 基 板 的 进 给 速 度 为50~80mm/s铜 板 材 料 基 板 的 进 给 速 度 为20~30mm/s进行切割时切断面的角度误差一般均在精度要求的范围 (±2°) 之内但随着主轴转速的降低和 (或) 进给速度的加快出现的不合格品数将增多 (见图4 (c))切削速度对切断面角度误差的影响较为显著[4-6] 。
3∙2∙4 外形中心与内部电路中心的偏离
检测结果表明此项误差相对较小在正常切割的情况下一般均能满足要求说明所用的切割机具有较高的定位精度。
3∙2∙5 崩碎坑的大小
检测结果表明用现行的切割速度进行切割时崩碎坑 (见图2) 一般较小除个别之外绝大多数均能满足要求但随着主轴转速的降低和(或) 进给速度的加快不合格品将显著地增加切削速度对崩碎坑的影响很大[4-6] 。
4 结语
通过大量的芯片切割实验并对实验中切割出来的大量芯片按所提出的评价指标和检测方法逐项进行了检测证明所提出的检测项目和检测方法对于控制半导体芯片的切割质量是有效的和可行的。指出了在正常切割条件下切断面的直角度和崩碎坑两项指标出现不合格品的可能性较大在主轴转速较低或进给速度较快时这两项指标出现不合格品的可能性将进一步增大。研究成果对于半导体芯片切割加工品质的评价方法的规范化和标准化具有一定的指导意义对于相关企业的质量控制具有一定的实用价值对于切割机的设计和切割工艺的制定具有重要的参考价值。