微电子键合用复合微球制备技术与性能研究进展
张宁,王秀峰
(陕西科技大学材料科学与工程学院)
摘要:
多层多元复合微球具有硬度高、导电导热性好、可靠性高等优异性能,是解决三维高密度微电子产品在长期服役条件下互连可靠性问题的一类关键电子材料,其制备技术主要包括合金偏析(气体雾化技术、均匀液滴喷射技术、落管技术)和化学电镀。复合微球通常为多层多元核壳结构,核的主要成分为Cu、Al等高硬度、高熔点金属,用于提高微球稳定性;壳可为多层,主要成分为Sn、Sn-Ag、Sn-In、Sn-Bi、Sn-Ag-Cu等锡基合金,起键合作用。详细介绍了近年来微电子封装领域键合用核壳结构复合微球制备技术与性能研究进展,分析了复合微球应用中出现的问题,展望了复合微球制备技术的发展前景。
焊锡球是球栅阵列封装( Ball Grid Array, BGA) 、芯片级封装( Chip Scale Package, CSP) 等电子封装技术中的关键材料[1-3] , 替代了传统 IC 元件封装结构中的引脚, 起信号传输、电流承载、机械支撑等作用。焊锡球的性能在很大程度上决定着封装电子产品的质量[4-5] 。焊锡球热熔塌陷会造成电子元件短路, 导致产品失效[6-7] 。对于三维高密度微电子产品, 迫切需要解决长期服役条件下键合互连的可靠性问题。
微电子键合用复合微球是一种具有核-壳结构的多层多元焊锡球,具有硬度高、导电导热性好、可靠性高等特点,在高温、高应力环境下能够保持稳定的键合高度,可解决传统焊锡球塌陷造成的元件短路问题。
复合微球通常为多层多元核壳结构,尺寸范围在50~600μm之间,其结构如图1所示。核的主要成分为Cu、Al等高硬度、高熔点金属,用于提高微球稳定性,特别是保持服役过程中的键合高度;壳一般为多层(包含过渡层)多组分,主要成分为Sn、Sn-Ag、Sn-In、Sn-Bi、Sn-Ag-Cu等锡基合金,起键合作用。
本文详细介绍了近年来微电子封装领域键合用复合微球制备技术与性能研究进展,分析了复合微球应用中出现的问题,展望了复合微球制备技术的发展前景。
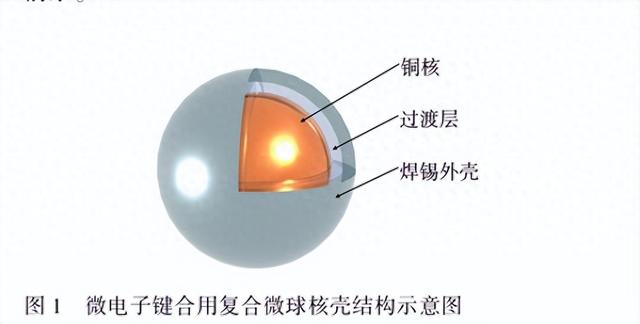
1 复合微球制备技术
多层多元复合微球制备技术主要有合金偏析( 气体雾化技术、 均匀液滴喷射技术、 落管技术) 和化学电镀两类, 制备技术原理与优缺点如表 1 所示。
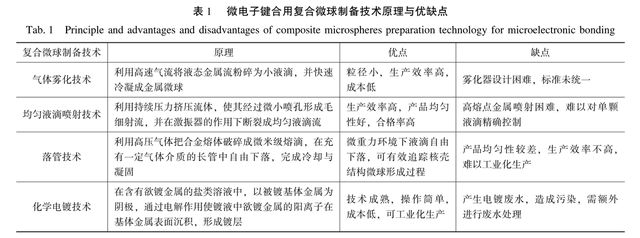
1. 1 合金偏析技术
偏晶合金相的组元分离特性为核壳结构复合微球的制备提供了新思路。 合金偏析技术利用偏晶合金熔体在冷却过程中发生液相分离, 在一定凝固条件下经过 Ostwald 粗化、 Stokes 运动和 Marangoni 迁移, 发生成分偏析和偏晶合金相组元分层现象, 最终形成上下分层结构或内外分层的核壳结构[8-10] 。 合金偏析技术制备复合微球的方法主要包括: 气体雾化技术[11-12] 、均匀液滴喷射技术[13-14] 和落管技术[15] 等。 合金偏析技术可同步制备出由高导电性材料构成的核以及由低熔点金属或合金构成的壳的复合微球。
相图中液相不混溶区内的熔体冷却后可得到偏晶合金相[16-17] 。 图 2 为 其 典 型 相 图, 当 温 度 降 低 至 Tm( 偏晶反应温度) 以下时, 发生偏晶反应 L1 → S1 + L2;继续降温, S1固相成分沿 Tm和 TE( 共晶反应温度) 之间的固相线变化, L2液相成分沿 Tm和 TE之间的液相线变化, 最后发生共晶反应 L→A+B。
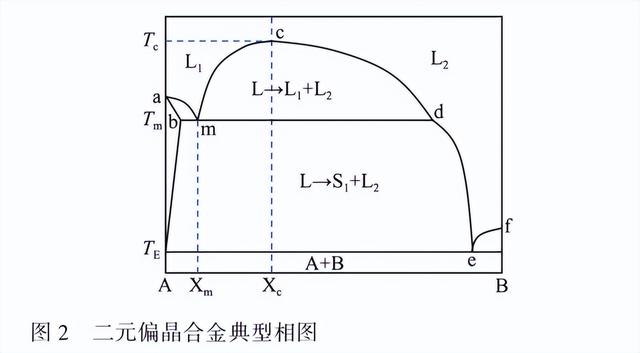
2002 年, Wang 等[18] 利用 Cu -Sn -Bi 偏晶合金和Cu-Fe 偏晶合金的液相分离特性, 合成了以 Cu-Sn 合金为核、 以 Sn -Bi 低熔点合金为壳以及富 Cu 相包裹富 Fe 相的两种核壳结构的复合微球, 如图 3 所示。
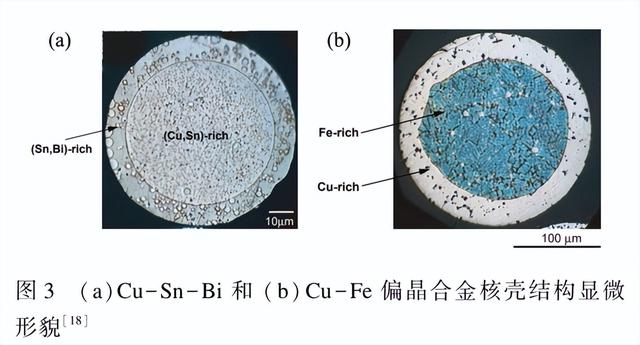
1. 1. 1 气体雾化技术
气体雾化技术( Gas Atomization Technique, GAT)是在高速气流下将液态金属雾化、 粉碎、 冷却并最终凝固形成球形微粒的过程[19] 。 该技术能够直接制备大量的粒径在 100 μm 以下的粒子, 生产效率高, 成本低, 是一种生产球形金属微粒的成熟方法。
Ohnuma 等[20] 研究具有偏晶合金相分离特性的 Cu-Al/Sn 和 Cu-Sn/Bi 合金的显微结构, 制备出了熔点温度分别为 230 ℃ 和 270 ℃ 的 Sn-Al-Cu 和 Bi-Cu-Sn偏晶合金新型 BGA 封装材料, 如图 4 所示。 分析图中核壳结构及两相形态特征, 可见气体雾化法制备的复合微球的显微组织演变过程。

He 等[21] 用高压(2 ~ 3 MPa) 氮气雾化合金熔体 20min, 得到直径为 20 ~ 280 μm 的富 Cu 相包裹富 Fe 相、具有核壳结构的 Cu60Fe40偏晶合金球。 研究 Cu(100-x) Fex(x = 15, 20, 30 和 40) 偏晶合金的凝固行为后发现液滴越小、 冷却速率越大、 过冷时间越长, 越容易产生液相分离, 形成核壳结构。
气体雾化技术制备的复合微球直径通常小于 200μm。 增大微球尺寸, 将会降低液滴的冷却速率。 李建强等[22] 通过 GAT 制备了 100 ~ 760 μm 的 Cu/Sn-Bi 偏晶合金复合微球, 在合金熔炼阶段加入适量稀土元素,提高了核壳结构的形成效率及完整性, 为大尺寸复合微球制备提供了新思路。
1. 1. 2 均匀液滴喷射技术
均匀液滴喷射( Uniform Droplet Spray, UDS) 技术基于射流不稳定性理论, 通过对射流熔体施加周期性扰动, 使流体成为分散液滴[23-4] 。 恒温控制熔化的合金在惰性气体压力下从坩埚底部的孔中喷射出来, 压电振动传感器诱导毛细管破裂, 使喷射出的熔体分离成大小均匀的球形液滴[25] 。 该方法制备的微球生产效率高、 产品合格率高。
张俊芳等[26] 使用 UDS 制备技术, 以 Al70 Bi11 Sn19偏晶合金为原料成功制备出 Al/Sn-Bi 复合微球。 由图5( a) 中可见 0. 7 mm 的 Al70 Bi11 Sn19 完美偏晶合金核壳结构, 但壳层 Sn -Bi 合金的 Bi 相显微组织呈现粗大化, 塑 性 变 差, 使 复 合 微 球 的 应 用 受 到 限 制。 而Al75Bi9Sn16合金中加入摩尔分数 5% Cu 元 素, 对 壳 层的 Sn-Bi 晶粒有一定的细化作用, 能有效改善 Al/Sn-Bi 核壳复合微球塑性变差问题[27] 。 向偏晶合金中尝试掺杂其他元素, 是改善核壳结构复合微球性能的有效手段之一。
Dai 等[28-30] 采 用 UDS 制 备 技 术 分 别 研 究 了Al-65. 5%Bi 和 Al/Sn-Bi 偏晶合金形成核壳结构的演变规律。 无论成分如何改变, Al - 65. 5% Bi 复合微球壳层总是由少数相( 富 Bi 相) 组成。 在自由落体距离为 30 mm、 熔体温度为 1410 K 条件下, 可以获得如图5( b) 所示的 Al-65. 5% Bi 完美核壳结构。 用于液滴凝固的硅油温度对 Al/Sn-Bi 偏晶合金核壳结构形成的影响如图5( c) 、 ( d) 所示。 随着硅油温度升高, Al/Sn -Bi 偏晶合金核壳结构球化的有效时间增加, 核心趋于圆润光滑。 均匀液滴喷射技术制备核壳结构复合微球过程中, 液滴冷却速率以及用于液滴凝固的硅油温度是影响核壳结构形成的重要因素。
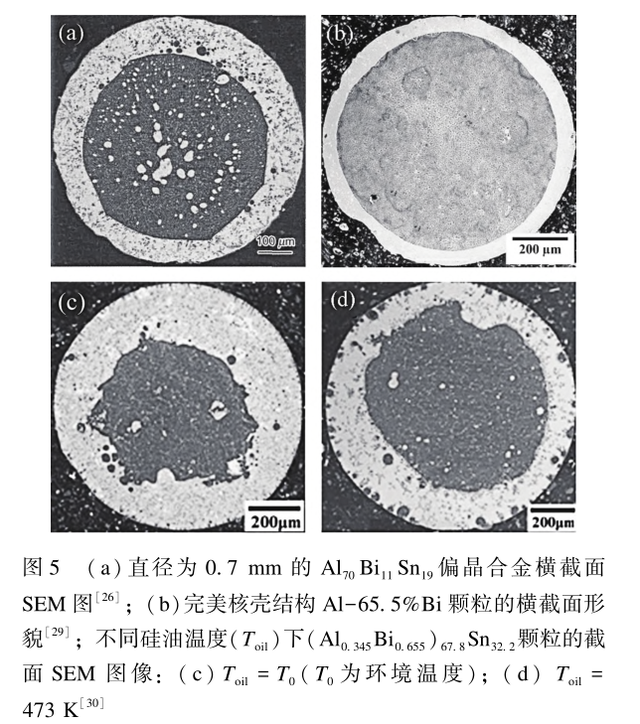
1. 1. 3 落管技术
落管技术( Drop Tube Technique, DTT) 的工艺流程为: 偏晶合金熔体经历过热和保温处理后, 从微孔喷射出, 分 散 成 若 干 小 液 滴, 然 后 在 充 有 高 纯 气 体( 通常是 Ar 气流) 的 5 ~ 50 m 降落管中自由下落, 迅速完成冷却与凝固, 最终在落管底部收集固体颗粒[31] 。该方法的主要特点是金属合金熔体可在落管过程中细分成非常小的液滴, 提高过冷水平, 更容易获得完整的核壳结构微球[15] 。
Jegede 等[32] 使用 6. 5 m 滴管装置研究 Co-Cu 偏晶合金的液相分离特性和核壳组织的形成规律。 在冷却速率超过 15000 K·s-1 时观察到大量的液相分离结构存在, 表明 Cu-Co 合金在形成稳定核壳结构时, 存在最佳冷却速率。 图 6 显示了 经 DTT 技 术 处 理 后 Cu -50%Co、 Cu - 68. 5% Co 和 Co - 76% Cu 合 金 的 核 壳 结构, 核始终是富 Co( 高熔点) 相, 外壳保持富 Cu 相不变。 说明两相分离的 Co-Cu 合金中, 两种液体的表面张力决定核心相的形成, 而不是体积含量, 可保证复合微球的金属核心为高熔点相。
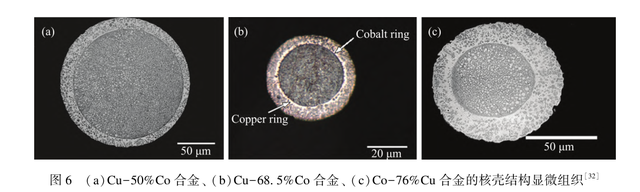
Wang 等[33-34] 采用 3 m 短滴管研究失重条件下 Cu-Pb 和 Fe-Sn 超偏晶合金双、 三层核壳组织的形成机理。 从图 7 可以看出, 双、 三层核壳结构偏晶合金中,壳层始终为暗相, 即富 Sn 或富 Pb 的低熔点相, 可见表面能较低的相趋向于形成壳层。 落管技术依赖于表面能的壳相选择特性, 在控制双层或三层核壳结构的形成中极为重要。
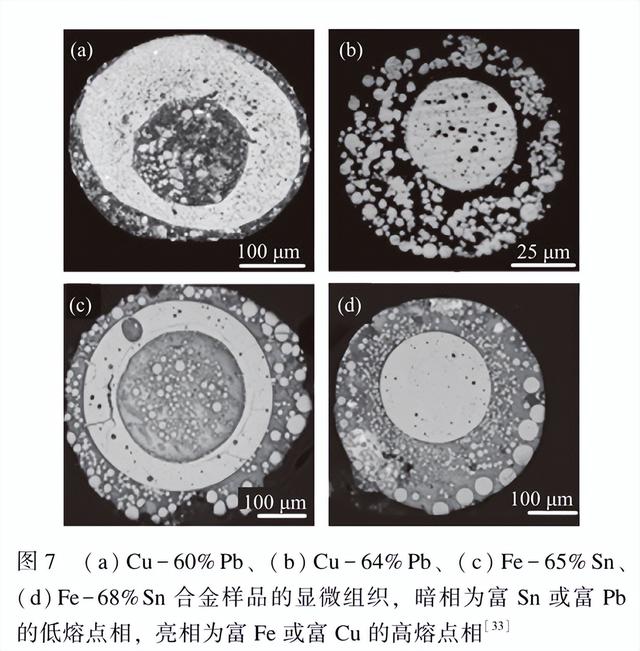
为了更方便、 有效地了解合金成分与合金凝固行为与组织的关系, Ma 等[35-36] 采用独特的常规铸造法将 Cu-Sn-Bi 和 Al -Sn -Bi 合金熔体铸入圆柱形铜模中, 分析圆柱形样品横切面的形貌。 如图 8 所示, 随着 Bi 含量的增加, Cu-Sn-Bi 合金首先形成富 Cu-Sn相包裹富 Bi 相的双层核壳结构, 之后形成富 Cu - Sn相的中间层, 富 Bi 相的核与壳层的三层核壳结构, 最后又形成富 Bi 相 包 裹 富 Cu - Sn 相 的 双 层 核 壳 结 构。Al-Sn-Bi 合金随着 Al 含量的变化也出现类似情况。初次相分离产生的适当体积的液滴和条件促进了双层核壳结构的形成, 二次相分离产生的适当体积的液滴和条件促进了三层核壳结构的形成。
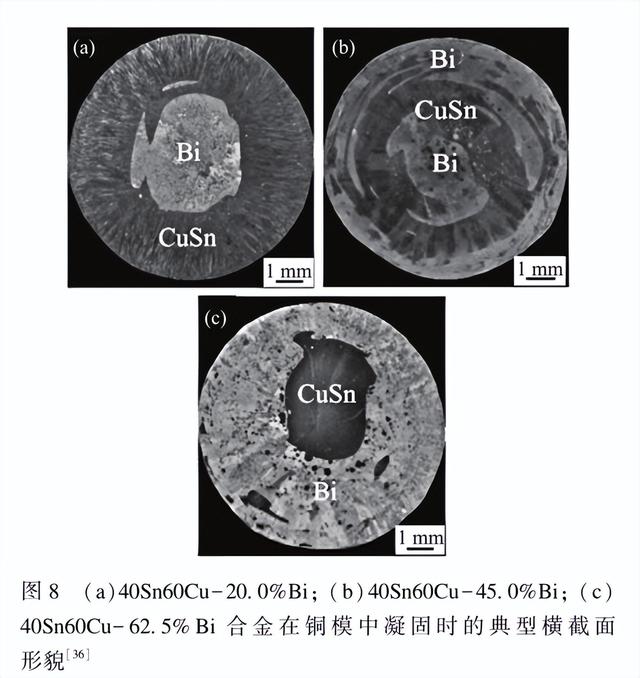
基于合金偏析技术制备多层多元复合微球实验研究中, 冷却速率、 用于液滴凝固的硅油温度、 液滴粒径、 不同相的体积分数、 表面张力和表面能等都是复合微球核壳结构形成的重要影响因素。 合金偏析技术制备微电子键合用复合微球工艺简单, 生产效率高,但微球样品粒径不够均匀, 真圆度较差等缺点仍有待改善。
1. 2 化学电镀技术
化学电镀技术又称电化学技术, 是将待包覆的导电核心材料作为阴极, 镀层金属作阳极, 溶液通电后镀层金属放电并在阴极上析出, 从而沉积在核心材料表面, 得到核壳结构复合微球。
浅田贤等[37] 选择 Cu、 Ni、 Fe、 Co 等导电性良好的金属单质或合金作为核心球, 将含 Sn 和 Ag 的甲磺酸溶液作为镀液, 电流密度 0. 15 A/dm2, 6 h 后在核心球表面制备出厚度 25 μm 的光滑 Sn - 3% Ag 镀层,得到如图 9 所示的真圆度较好的核壳结构复合微球,有效解决了一般电镀处理后镀锡层表面粗糙不平情况。

Kim 等[38] 在 直 径 为 300 μm 的 铜 球 上 电 镀 Sn -3. 0Ag 合金, 得到镀层均匀的 Cu/Sn-3. 0Ag 复合微球( 图 10) 。 Mizukami 等[39] 经过对镀液组成、 阳极、 电镀条件的反复试验, 在直径为 40 μm 的铜球表面得到厚度为 20 μm 的 Sn-Ag 镀层, 该复合微球与常规焊锡球有着同等的湿润性和稳定性。
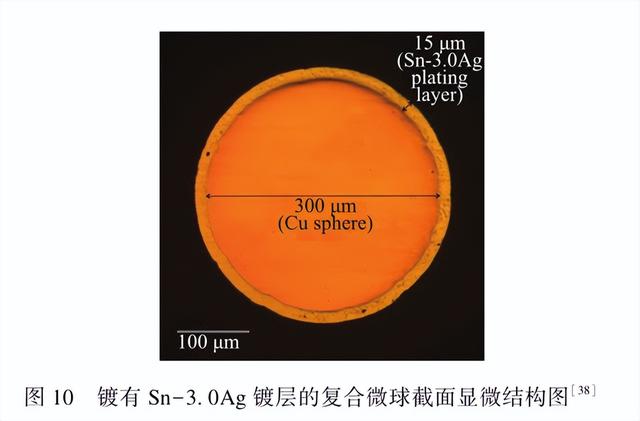
电镀法制备复合微球过程中, 如果铜球表面粗糙,容易导致镀层之间产生原子扩散, 形成金属间化合物,影响产品性能[40] 。 王梦茜等[41] 利用铜液在毛细管末端的表面张力下可自发形成规整球体的特性, 制备出真圆度较好的铜球, 同时在成型器具中充入氮气, 防止铜球在形成过程中被氧化, 得到高键合可靠性的铜芯复合微球。 赵兴科等[42] 用 Mo 球代替铜芯, 化学电镀制备锡镀层, 得到一种低热应力芯片封装用焊锡球,Mo 的热膨胀系数比 Cu 更低, 是 Sn 的四分之一, 有效削弱复合微球与硅芯片之间的热应力, 降低因热应力导致的器件故障率。
化学电镀技术制备多层多元复合微球可根据实际需要对微球尺寸、 镀层厚度、 成分进行精确控制, 技术成熟, 但其电镀液一般为硫脲、 甲磺酸等有毒、 强腐蚀性物质, 存在一定的危害。 用于复合微球镀层制备的新一代电镀液开发具有重要研究意义。
2 复合微球性能研究
2. 1 力学性能
多层多元复合微球的力学性能是满足微电子封装领域长期服役可靠性的根本。 Son 等[43] 使用倒装芯片键合器验证铜芯焊锡球( Cu-Core Solder Ball, CCSB)的力学性能优势。 在 175 ℃ 的压应力 条 件 下, CCSB没有发生变形, 20 s 内焊点高度一直保持在 180 μm,而相同测试条件下的 SAC 焊点高度降低约 50%, 见图11。 高温、 高压条件下, 复合微球比普通 SAC( Sn-Ag-Cu) 焊锡球能保持更稳定的键合高度。

Tanie 等[44-45] 结合裂纹扩展分析和冲击弯曲实验评估 CCSB 焊点的断裂寿命。 图 12 中 CCSB 焊点的非弹性应变分散程度较普通焊点高, 裂纹路径多而分散,裂纹总长度变长, 扩展速度降低, 焊点的断裂寿命比常规焊点更长。 在冲击弯曲实验中证实了 CCSB 的冲击强度与普通焊点相同或更高, 可在不降低冲击强度的情况下提高焊点断裂寿命。 Jeong 等[46] 通过模拟键合焊点低速剪切试验中的冯米塞斯( von Mises) 应力和等效塑性应变来测试 CCSB 的剪切强度和断裂能。 由图 13 可以看到 CCSB 焊点的最高冯米塞斯应力区位于铜芯的左下方, 最高塑性应变区集中在剪切前端和铜芯之间, CCSB 的模拟冯米塞斯应力和塑性应变最大值都高 于 SAC。 CCSB 的 抗 剪 强 度 和 断 裂 能 都 优 于SAC, 力学性能表现更优秀。
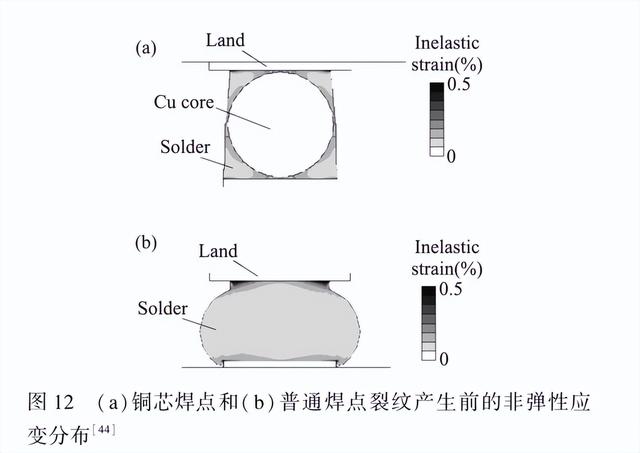
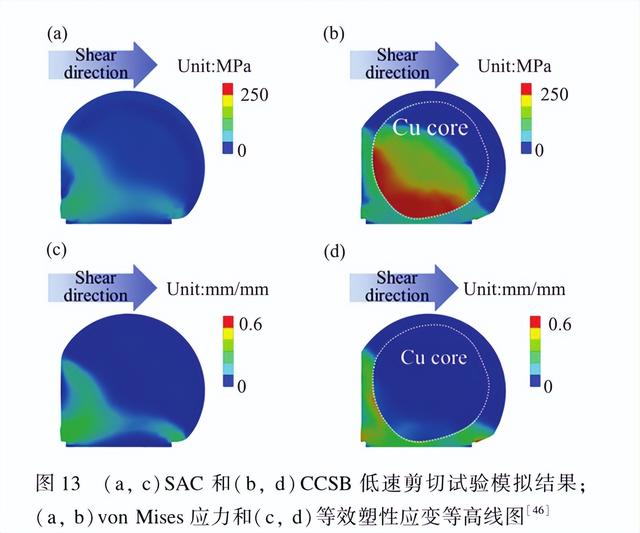
Kim 等[38] 通过推球试验和法向剪切测试研究不同镀层对铜芯复合微球的断裂强度和断裂模式的影响。铜芯与镀层界面处的上界面脆性断裂是 Sn - 3. 0Ag 复合微球焊点的主要失效模式, 而 Sn-1. 0In 复合微球焊点的上界 面 断 裂 率 仅 为 Sn - 3. 0Ag 焊 点 的 1/2。 Sn -1. 0In 镀层可以减少润湿时间, 增加润湿力, 改善铜芯和锡镀层之间的湿润性, 此外 Sn-1. 0In 镀层通过固体强化机制溶解并强化铜芯表面, 使复合微球的键合强度更大, 拥有更好的抗剪切性能。
铜芯复合微球力学性能分析集中于剪切性能方面,而复合微球在实际应用中也有可能受到拉伸力的作用。江山等[47] 就 CCSB 焊点和普通焊点的拉伸力学性能展开对比研究。 在图 14( a) 中普通焊点断口处观察到大量河流状花样、 撕裂棱和韧窝, 同时存在一定量的微孔, 在拉伸过程中容易造成应力集中, 产生裂纹, 降低焊点拉伸强度; 图 14( b) 的 CCSB 焊点断口处存在大量均匀分布的韧窝, 并夹杂微孔, 断裂模式接近韧性断裂, 焊点具有优异的抗拉伸性能, 使铜芯复合微球拥有更高的抗拉强度。
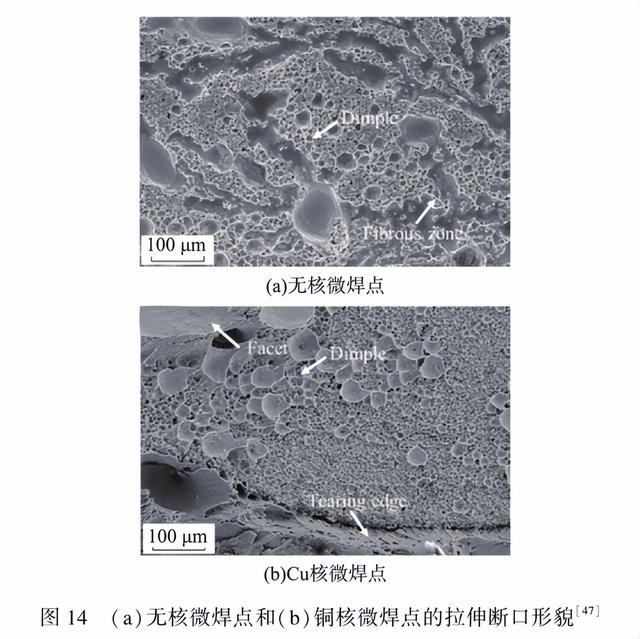
焊点尺寸效应关系到微电子键合结构可靠性[48] 。复 合 微 球 中 铜 芯 的 加 入 会 改 变 界 面 金 属 间 化 合 物( Intermetallic Compound, IMC) 的 形 貌 和 厚 度, 影 响焊点的力学性能[49] 。 Yao 等[50] 通过对比不同高度 Cu/SAC305 复合微球焊点的界面 IMC 微观结构演变和拉伸破坏行为, 研究复合微球焊点的尺寸效应[50] 。 铜芯复合微球的界面 IMC 厚度比 SAC305 更小, 且随着焊点高度的增加, 铜芯-镀层界面处的 IMC 厚度逐渐减小。 从图 15 可以看出随着 Cu/SAC305 镀层厚度的增加, 抗拉强度降至最低值 43. 66 MPa。 可见铜芯复合微球焊点的抗拉强度随焊点高度的增加而降低, 呈反比关系, 铜芯的加入可提高相同高度焊点的抗拉强度。Son 等[51] 研究不同厚度的 SAC305 镀层对 CCSB 剪切性能 的 影 响。 发 现 随 着 SAC305 镀 层 厚 度 的 增 加,CCSB 的剪切强度同样呈下降趋势, 但较厚的 SAC 镀层在球剪切试验中具有较稳定的延展性, 可完全覆盖在铜芯球顶部不坍塌, 表现出较稳定的性能。
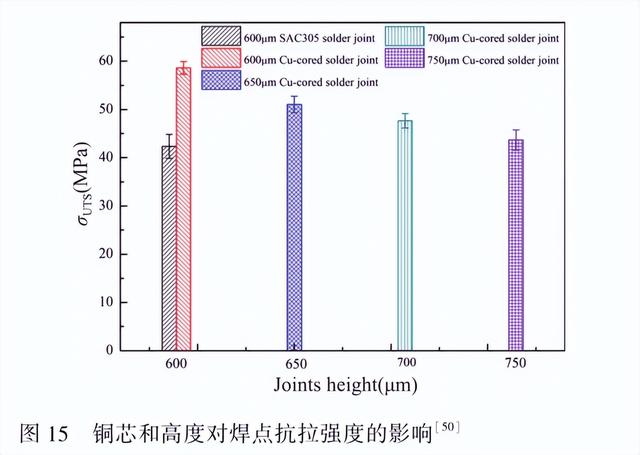
微电子键合用复合微球与传统焊锡球相比, 具有更优异的抗剪切、 拉伸力学性能。 复合微球的尺寸效应表现为: 剪切强度和抗拉强度随镀层厚度的增加呈下降趋势, 而镀层延展性和稳定性随厚度的增加表现更好。 因而以三维高密度微电子产品实际应用为前提,根据尺寸效应为复合微球设计合适的尺寸和镀层厚度范围来保证 复 合 微 球 长 期 服 役 可 靠 性, 有 待 进 一 步研究。
2. 2 电迁移行为
电迁移是指器件工作时, 金属互连线内有一定电流通过, 金属离子沿导体产生质量输运。 电子元件内部电流密度过大时, 发生电迁移, 致使器件的某些部位产生空洞或晶须( 小丘) , 出现短路、 断路、 参数退化问题, 称为电迁移失效现象[52-53] 。 在电子元件微型化的趋势下, 内部电流密度只会不断增加, 焊点的电迁移失效不可避免, 如何有效降低焊点的电迁移失效是焊锡球可靠性提高必须考虑的问题。
Jeong 等[54] 研究高电流密度下 CCSB 焊点的电迁移行为, 采用三维有限元法确定 SAC 和 CCSB 焊点电迁移失效的位置。 从图 16 中观察到在靠近上下 Cu 电极的键合处出现电流拥挤, 图 16( a) 、 ( d) 显示 CCSB中电流通过铜芯, 不通过镀层, 因为铜的导电性高于SAC 焊点。 图 16( b) 、 ( e) 显示 CCSB 焊点的最大电流密度比 SAC 焊点低 10%。 图 16( c) 、 ( f) 表示 SAC 焊点的电流密度集中于键合面边缘处, 而 CCSB 焊点的电流密度偏向键合面中心。 CCSB 焊点内电流通过铜芯移动, 减弱电流拥挤效应, 空洞等缺陷形成时间比SAC 焊点晚, 电迁移可靠性优于 SAC 焊点。 Mu 等[55]为了研究 CCSB 焊点的电迁移失效行为, 通过三维有限元分析模拟 CCSB 焊点内的电流密度分布情况, 电流主要选择电阻率更低的铜芯作为流动路径。 CCSB的电流拥挤区从铜芯 -镀层界面向镀层中部移动, 而镀层中部的空洞形核与膨胀比镀层边缘更难, 因此电迁移失效发生率大大降低。
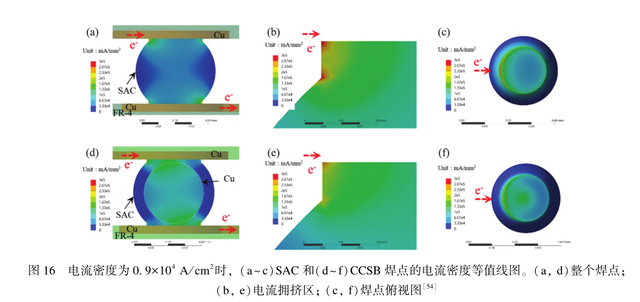
Sa 等[56-57] 研究在高温条件下, 特别是在高电流密度下电迁移行为对 CCSB 焊点显微组织演变情况的影响。 图 17( a) 中电流主要选择铜芯作为其电路, 电流拥挤明显发生在铜芯和镀层之间的区域。 Cu 原子随电流通量从阴极侧向阳极侧移动, 导致阴极侧出现空隙,而阳极侧界面 IMC 变厚, 图 17( b) 中可以看到电流应力 260 h 后, CCSB 出现很明显的裂纹扩展。
共晶 Sn-Bi 合金具有优异的机械强度、 较低的熔化温度和热膨胀系数等优点, 研究者将 Cu/Sn -Bi 复合微球作为电迁移失效研究对象, 分析其电流拥挤效应[58] 。 在图 18( a) 中, Sn 和 Bi 原子分别在铜芯两侧积累, 形成双面形貌。 图 18( b) 是 Sn 矩阵中 Bi 球的有限元分析模拟, 电阻性 Bi 原子趋向于从高电流密度区域 A、 B 处向低电流密度区域 C、 D 处迁移, 验证了复合微球 Sn-Bi 相边界处的电流密度重新分布的原因。 重新分布的 Sn-Bi 矩阵电阻降低, 和铜芯一起形成更通畅的电流流动路径, 显著提高 Cu/Sn -Bi 复合微球焊点的抗电迁移性能。
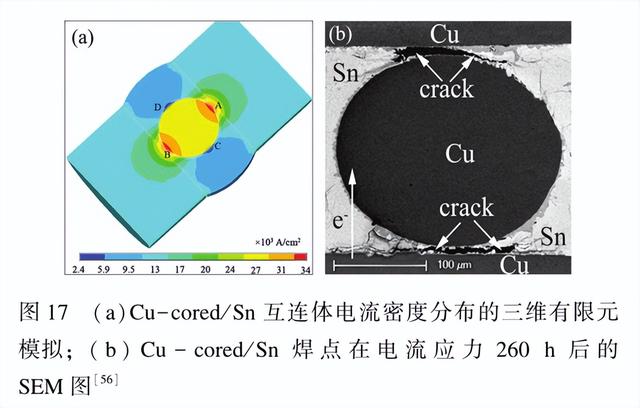
多层多元复合微球内部的高质量金属球具有优异的导电、 导热性, 可形成导电通路, 提供更通畅的电流流动路径, 在一定程度上减弱金属离子质量运输情况, 具有更好的抗电迁移能力, 是解决三维高密度微电子产品电迁移失效问题的有效方案。 在电迁移性能研究方面, 不同锡基合金镀层各有优势, 镀层的选择是否使复合微球电迁移失效产生差异, 这一问题也可以纳入以后的研究之中。
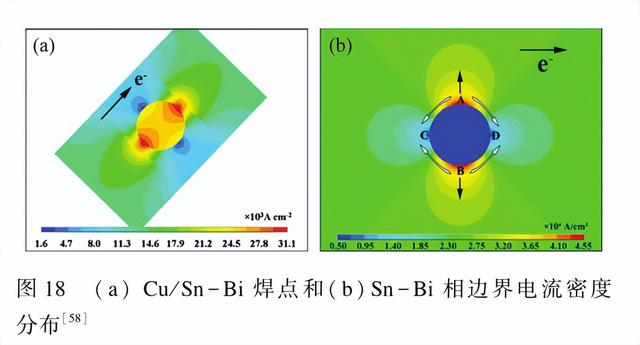
2. 3 热循环稳定性
热环 境 是 焊 点 可 靠 性 的 主 要 影 响 因 素。 Amagai等[59] 就 MLBGA( Multilayer Laminate Ball Grid Array)封装中温度循环频率对焊点疲劳寿命的影响展开研究,发现铜芯焊点的热循环电阻随铜芯尺寸的增大而增大。Terasaki 等[60] 基于裂纹扩展过程中的累积损伤, 利用有限元方法计算焊点的疲劳失效寿命, 在热循环试验中, 预测到球栅阵列封装中铜芯焊点比普通焊点的疲劳寿命更长。
为测试复合微球在汽车/航空航天工业中微电子元件经常遇到的极端热循环条件下的性能, Kim 等[61] 研究 Sn-3. 0Ag 和 Sn-1. 0In 两种不同镀层铜芯焊点与基准 SAC305 焊点, 在-55 ~ 150 ℃ 温度范围内每 15 min一次循环的热疲劳试验的失败率。 图 19 中 Sn-3. 0Ag和 Sn - 1. 0In 铜芯焊点都显示出 比 基 线 SAC305 焊 点(1444 周期) 更高的特征寿命值, 且 Sn-3. 0Ag 铜芯焊点的 特 征 寿 命 ( 1690 周 期) 高 于 Sn - 1. 0In 铜 芯 焊 点(1563 周期) 。 Jeong 等[62] 在 40 ~ 125 ℃ 的温度范围内进行热冲击试验, 研究 CCSB 焊点的热冲击可 靠 性。CCSB 焊点的界面 IMC 层厚度较 SAC 焊点更小, 平均热冲击循环次数明显大于 SAC 焊点。 铜芯复合微球与SAC305 焊锡球相比更能抵抗苛刻的温度循环引起的热应力, 热循环性能更好。
张焱 等[63] 研 究 不 同 热 时 效 时 间 下 SAC 焊 点 和CCSB 焊点的力学性能表现。 焊点的界面 IMC 厚度均随着热 时 效 时 间 的 增 加 而 增 加, CCSB 焊 点 的 界 面IMC 增长速率更慢, 且铜芯 -镀层界面 IMC 层厚度比衬底-镀层界面略薄, 表明添加铜芯可减缓焊点界面IMC 层的生长速率。 由应力 -应变曲线( 图 20) 可知,随着热时效时间的增加, 两种焊点的抗拉强度都出现下降, 但 CCSB 焊点的抗拉强度始终高于 SAC 焊点。CCSB 焊点中主要组分为高质量铜芯, 内部缺陷减少,且铜芯与镀层之间形成了致密的( Cux Ni1-x ) 6 Sn5 界面化合物, 抗拉强度增加, 在热时效处理试验中表现出更优异的互连可靠性。


多层多元复合微球内部金属球尺寸、 镀层成分和界面 IMC 厚度都会对其热循环性能和失效机制产生影响。 复合微球在一系列热冲击、 热时效实验下的热循环性能表现为: 铜芯的加入使复合微球在回流过程中保持稳定高度, 具有更低的热膨胀系数, 热循环稳定性优于传统焊锡球。 多层多元复合微球是微电子产品在长期服役条件下互连可靠性问题的优秀解决方案。对于复合微球的广泛实际应用具有重要意义。
3 复合微球应用问题
Hayashi[64] 使用复合微球应用于芯片和基底的互连键合, 有效提高集成电路键合点的封装稳定性。 Son等[65] 在一种 RDL( Redistribution Layer) 基晶片级插接封装 PoP( Package on Package) 工艺中使用 CCSB 代替垂直互连的电镀铜柱, 顺利解决电镀铜柱在装配过程中无法提供坚固性的问题。 微电子键合用复合微球凭借其优良特性进入应用阶段的同时, 一些应用问题也随之出现, 例如复合微球界面 IMC 导致的力学性能变差, 铜芯的偏心现象导致封装精度下降, 刚性铜球的存在降低焊锡球跌落可靠性等。
3. 1 金属间化合物
目前铜芯复合微球焊点中的界面 IMC 通常为( Ni, Cu) 3 Sn4。 Ni3 Sn4 晶 粒 在 有 限 空 间 的 撞 击 可 能 导 致Ni3Sn4基 IMC 产生明显空隙, 降低力学强度[66-67] 。 针对上述问题, Song 等[68] 提出一种新的加压键合方法,在焊接过程中施加机械压力以改变焊点的晶粒和相结构, 可保持 Ni3Sn4基 IMC 的细小晶粒结构, 在不形成空隙的情况下具有较高的断裂韧性, 从图 21 中可以看到使用 34. 7 MPa 压力键合的铜芯焊点中, ( Ni, Cu) 3Sn4由于加压键合而获得明显的完整性和致密性, 在铜芯与镀层之间几乎看不到空洞和缺陷。 ( Ni, Cu) 3 Sn4内部散发的白点为 Ag3 Sn, Ag3 Sn 极高的断裂韧性和高弹性强化加压铜芯焊点, 使铜芯复合微球焊点具有优异的机械强度和电迁移阻力。
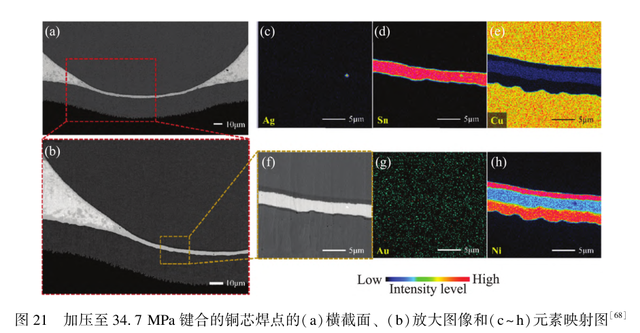
3. 2 封装精度
铜芯复合微球集中应用于三维高密度封装领域,表现出的独特键合行为不同于传统焊锡球。 Kawasaki等[69] 分析研究了铜芯焊锡球的键合步骤和键合行为,铜芯焊 锡 球 回 流 后 铜 芯 大 多 偏 心 位 于 凸 点 之 中 ( 图22) , 影响微电子产品封装精度。 总结回流曲线与凸点位置的关系后, 发现键合点附近的加热速率是造成偏心现象的主要因素, 较慢的锡镀层熔化过程会使铜芯保持中心位置, 有效提高铜芯焊锡球的键合精度,持续优化三维高密度封装精度问题。
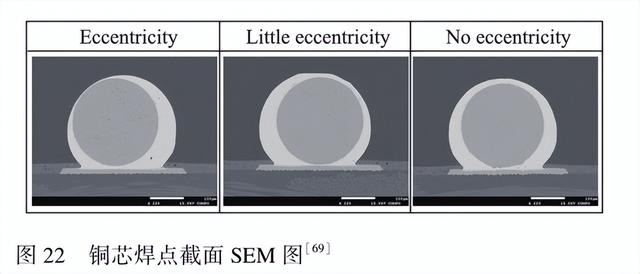
3. 3 跌落可靠性
电子产品的使用中, 跌落冲击引起的故障最常见。冲击可通过支撑电路板结构传递到产品内部的晶圆级封装上, 使焊点中的累积塑性变形超过焊锡球断裂韧性, 导致焊点开裂。 Pin 等[70] 对晶圆级封装用焊锡球的跌落冲击可靠性进行测试, 表 2 是每种焊锡球的首次失效结果, 铜芯复合微球内部存在刚性铜球, 能够吸收跌落冲击和应力的焊锡量较少, 跌落性能表现最差。 而聚合物芯复合微球由于内部低杨氏模量聚合物的存在, 可降低复合微球硬度, 减轻复合微球上的应力, 在跌落试验过程中获得最优的跌落试验性能, 该测试结果为具有特殊抗跌落冲击性能需要的微电子键合用复合微球开发提供有效解决方案。
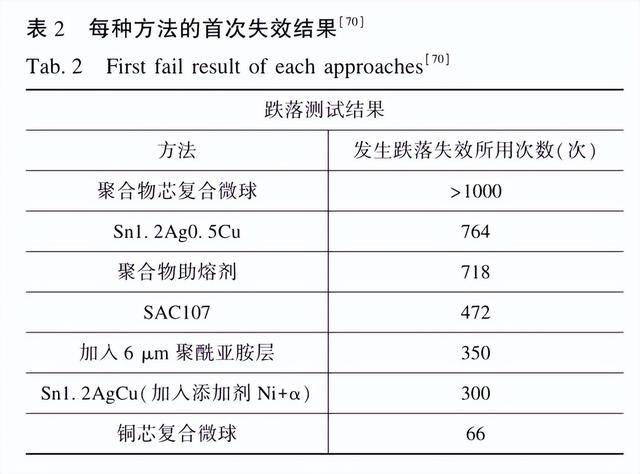
4 结论与展望
目前微电子键合用复合微球制备技术主要有: 气体雾化技术、 均匀液滴喷射技术、 落管技术等合金偏析技术和化学电镀技术。 合金偏析技术可一步直接合成核壳结构复合微球, 工艺简单。 化学电镀技术需提前准备高硬度、 高熔点金属球, 之后化学电镀制备核壳结构复合微球, 可精确控制微球尺寸, 技术成熟。剪切-拉伸力学性能、 抗电迁移失效能力以及热循环稳定性等是复合微球性能的主要研究热点。 此外, 研究者们分别采用加压键合、 降低镀层熔化速率以及使用聚合物芯等措施成功解决复合微球应用方面问题。尽管复合微球已经被微电子封装领域认可和关注, 但以下方面仍需进一步研究:
(1) 多层多元复合微球锡基合金镀层体系有二元合金 Sn-Ag、 Sn-Cu、 Sn -Bi、 Sn -Sb, 三元合金 Sn -Ag-Cu、 Sn -Ag -Bi 等, 不同锡基合金性能特点各有优势。 针对不同熔点、 不同应用领域需求来研究选择适宜的锡基合金镀层对复合微球的广泛应用意义重大。
(2) 多层多元复合微球制备技术众多, 相关技术也较为成熟, 但仍存在不少问题, 如环境污染、 工艺复杂、 成品效果差等。 离子溅射法可精确控制溅射镀膜过程, 易获得均匀、 致密、 附着性好的镀层, 可大批量、 高效率工业化生产, 该方法有可能成为核壳结构复合微球的有效制备技术。
微电子键合用复合微球由于铜芯的存在可保持封装空间稳定, 已经成为三维高密度微电子产品最佳的封装材料之一。 复合微球优异的力学性能、 抗电迁移失效性和热循环稳定性让众多研究者看到其广阔应用市场, 相信复合微球也会因新材料、 新制备技术的开发展现出更大的应用优势。