导语:在工业4.0浪潮下,制造业智能化转型已成必然趋势。但对于中小制造企业而言,动辄百万级的MES系统(制造执行系统)投入令人望而却步。如何用最小成本撬动最大效益?本文提供一套可落地的MES推进策略,破解中小企业数字化转型困局。
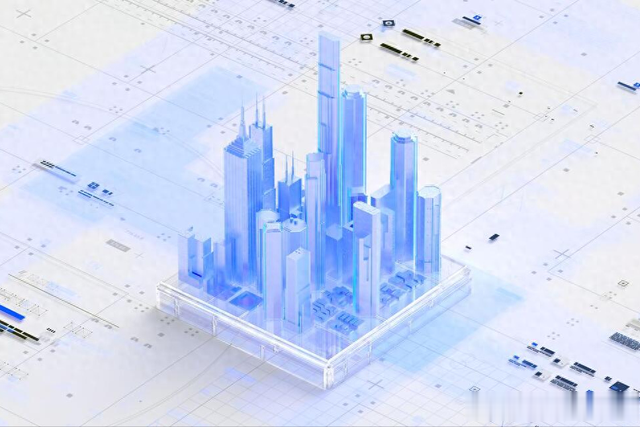
为什么中小企业更需要MES?
传统生产模式正面临三大致命伤:
数据黑箱:人工记录易出错,质量问题追溯难如"大海捞针";效率瓶颈:设备空转率达30%,订单交付周期超同业20%;成本失控:库存积压与缺料停工并存,每年浪费超百万。MES系统通过实时数据采集、生产调度优化、质量全程追溯,可帮助中小企业实现**效率提升15%+、不良率降低40%**的跃迁。
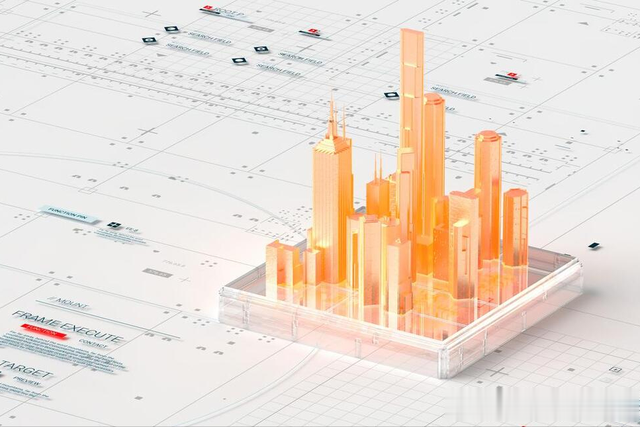
三步走战略:小步快跑实现MES落地第一步:精准定位需求,避免"大而全"陷阱痛点诊断:先做价值流分析,锁定车间最痛的3个环节(如物料齐套率、设备OEE、首检合格率)场景验证:选择1条产线试点,用轻量化模块(如Andon系统、电子工单)快速见效案例参考:某汽配企业通过设备联网模块,3个月将OEE从68%提升至82%第二步:选型避坑指南——不选贵的,只选对的成本控制:✓ 避免定制化开发,根据核心需求问题点优选标准模块✓ 选择可扩展的模块化系统✓ 利用政府补贴(多地提供数字化改造专项补助)供应商筛选:✓ 必须有同行业实施案例✓ 提供3个月免费试运行✓ 承诺不达标可退款第三步:柔性推进策略——先人后系统人员赋能:▸ 培养内部"数字种子"(选拔车间骨干参与实施)▸ 设计激励机制(如节省工时兑换奖金)流程再造:▸ 固化3项核心标准作业流程▸ 建立数据日清机制(晨会10分钟看板分析)迭代升级:每季度评估1次系统效益,滚动追加功能模块
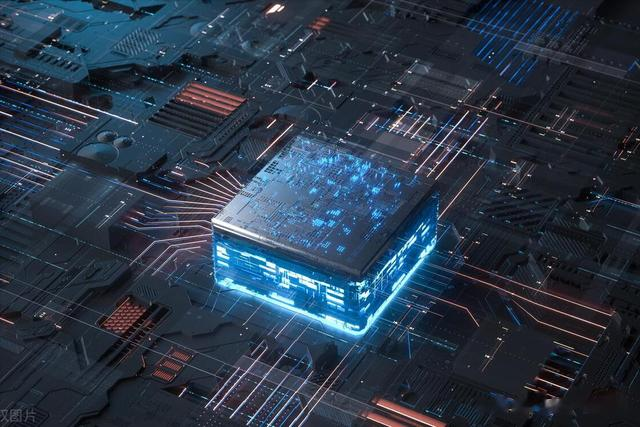
避开这3大雷区,成功率提升80%盲目对标大厂:砍掉AGV、数字孪生等"炫技"功能,聚焦基础数据打通忽视数据治理:先规范物料编码、工艺参数等基础数据,避免"垃圾进垃圾出"强推系统上线:用"试点产线VS传统产线"的对比数据说服管理层成功案例:30人小厂的逆袭之路
浙江某电子元件厂投资28万元实施MES:
订单交付周期从15天→8天质量追溯时间从4小时→10分钟人均产值提升2.3倍关键动作:聚焦电子看板、生产报工、设备监控三大模块,用三个月完成产线数字化改造。
结语:MES不是大企业的专属玩具。通过精准定位、分步实施、持续迭代,中小企业完全可以用一套"组合拳"打开智能制造的大门。记住:数字化转型不是选择题,而是生存战!立即行动的企业,将在新一轮行业洗牌中抢占先机。