金丝楔形键合强度的影响规律分析
高依然 刘森 魏威 王冠 方志浩 韩健睿 刘亚泽
(华北光电技术研究所)
摘要:
金丝楔形键合是一种通过超声振动和键合力协同作用来实现芯片与电路引出互连的技术。现今,此引线键合技术是微电子封装领域最重要、应用最广泛的技术之一。引线键合互连的质量是影响红外探测器组件可靠性和可信性的重要因素。基于红外探测器组件,对金丝楔形键合强度的多维影响因素进行探究。从键合焊盘质量和金丝楔焊焊点形貌对键合强度的影响入手,开展了超声功率、键合压力及键合时间对金丝楔形键合强度的影响研究。根据金丝楔焊原理及工艺过程,选取红外探测器组件进行强度影响规律试验及分析,指导实际金丝楔焊工艺,并对最佳工艺参数下的金丝键合拉力均匀性进行探究,验证了金丝楔形键合强度工艺一致性。
0引言
微电子封装逐渐发展成当今微电子制造中影响生产效率和器件性能的关键技术。半导体制造行业的发展逐渐火热。其中,引线键合技术在各类封装中的地位愈发重要。由于优点多、成本低、易于在工艺中实现、封装形式的适用性高,该技术已逐渐发展为当前主流的半导体封装所采用的互连电学引出方式。尤其得益于近年来封装行业的高速发展与国家政策的大力支持,引线键合技术在未来十多年的发展前景十分广阔。
红外探测器组件是由采用引线键合互连的芯片控制的。芯片运行期间的可靠性依赖于引线键合互连的质量。引线键合质量差不仅对器件可靠性和可信性有显著影响,而且还会产生巨大的经济影响。因此,在红外探测器组件封装过程中确保引线键合的质量是极其重要的。本文基于红外探测器组件,从原理出发对影响金丝楔焊质量的因素展开研究,分析焊盘、焊点和楔焊工艺参数多重维度对键合强度的影响。
1超声楔焊简介
超声键合是一种固态金属结合方式。超声波能量和力传递到引线和焊盘上时,金属在接触面产生塑性变形,最终形成冶金学的键合。在金属引线与焊盘之间的键合界面上,两者之间的金属化层发生摩擦,形成剪切力并作用在接触界面的金属原子上,从而活化了接触的金属表面,并去除掉键合引线和焊盘结合面的污染物,最终得到了良好的键合效果。键合过程中需要施加一定的能量,其吸收的能量为

式中,E 代表键合吸收的总能量,ΔT 是键合前后的温度差值,k是影响因子,u是摩擦系数,F 是键合压力,A 是超声振幅,f 是超声频率,t是键合时间。
由式(1)可知,键合过程中的能量吸收变化与温度、时间、压力和功率均有关联。其中,键合温度选取室温,是固定工艺温度,不作为本文的研究内容。
超细金属丝的超声楔形焊接过程如图1所示。键合时,金属丝穿过劈刀中心孔和背面通孔,与键合面(水平方向)的位置保持90°的夹角。在超声功率、压力和时间的共同作用下,金属丝线和焊盘金属的表面接触形成键合。楔形键合是指单一方向上的键合工艺技术,即第二焊点必须与第一焊点的方向保持一致。这会导致楔形键合的效率低于球形键合,但是其焊点、键合形成引线的弧高与弧长更小。由于弧高和弧长便于控制,楔形键合工艺简单便捷。
2焊盘及焊点形貌对金丝楔焊强度的影响
2.1 金丝基础拉力值测量
金丝工艺采用25 m金丝超声键合。为准确表征金丝楔焊强度影响规律,测试金丝的基础拉力值作为对照,判断金丝键合强度的优良。表1列出了试验所用金丝的基础材料参数。将金丝引线两端通过导电胶固定在两块塑料板之间,然后将两块塑料板垫高并将其两端用金属块固定,且留出缝隙便于测试拉力值(见图2)。表2列出了拉力测试仪的测试数据(断点均在引线中间)。
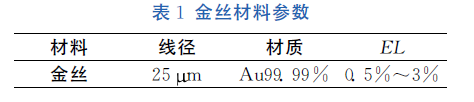
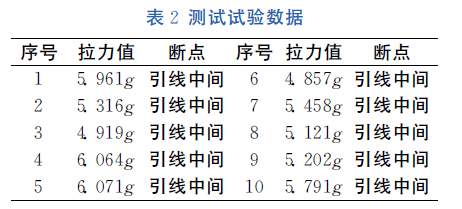
为更准确表示金丝线上受力,将金丝拉力值表达为

式中,F1为引线上的实际受力;F 是引线轴向拉力值;θ是引线与X轴的夹角。
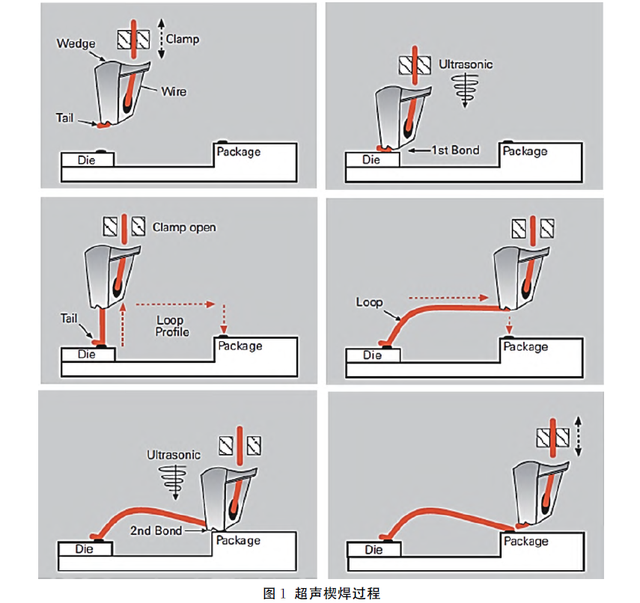
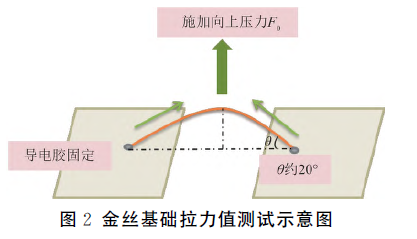
基础拉力值测试数据显示,金丝的平均拉力值为5.476g。该数据为轴向拉力,导线的弯曲角度θ为20°。由F0=Fsinθ可得:F(金丝)为16.001g。
2.2 焊盘对金丝楔焊强度的影响
在红外探测器组件中,金丝主要应用于芯片与陶瓷框架的连接。其中,焊盘质量会对金丝楔焊强度产生影响。芯片、框架上的焊盘可能出现镀层厚度不均匀、金层污染的问题,从而降低强度。芯片焊盘材质不同(铝、铝镀金),结合力也有所区别。本文主要对金焊盘进行探究。
2.2.1 陶瓷框架焊盘表面平整度探究
采用工具显微镜对框架焊盘进行Z向检测,即以陶瓷框架上表面作为基准来测量焊盘
不同位置到基板的高度,进而检验其焊盘表面均匀性。测试点位如图3所示。
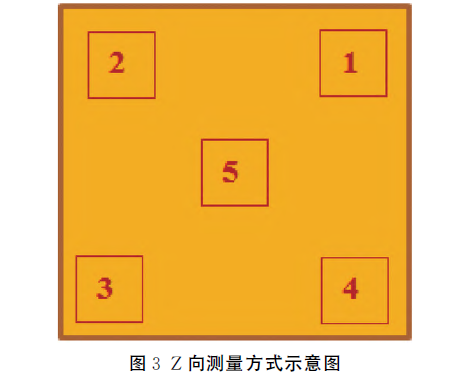
试验共选取13个焊盘测量。在点1清零,分别测试点2~5的Z向平均值,从而检验焊盘表面平整度。试验结果如图4所示。可以看出,焊盘Z向最大误差为3.6 m,平均误差为2.67 m,在合格范围内。但在实际焊接过程中,为避免焊盘表面不平整对结合力的影响,应尽量在焊盘中间区域进行焊接。
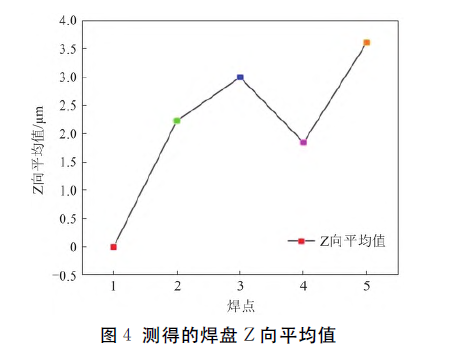
2.2.2 陶瓷框架焊盘表面形貌分析
焊盘表面形貌会对引线键合强度产生影响。图5所示为受污染的陶瓷框架金焊盘在扫描电子显微镜(Scanning Electron Microscope,SEM)下的形貌。可以看出,焊盘表面存在深、浅两种颜色(对其进行清理后仍存在此痕迹):浅色区域为100%的Au;深色区域不导电,其成分为陶瓷框架上的有机物介质层。
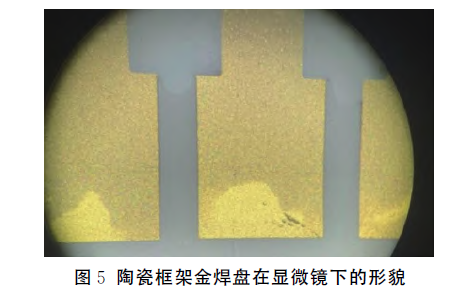
若焊接位置存在有机物,则会大大影响金丝引线的键合强度,从而出现引线断裂的情况。因此应加强对陶瓷框架加工质量的要求及检测,以免出现焊盘质量影响键合强度的情况。
2.3 金丝楔焊焊点形貌对键合强度的影响
根据GJB548C中关于引线键合的标准规定,芯片键合区上的超声楔形键合尺寸示意图如图6所示。其宽度(W)应大于引线直径(D)的1.2倍,且小于3倍。根据此标准,探究1.2~3倍范围内楔形键尺寸对键合强度的影响。
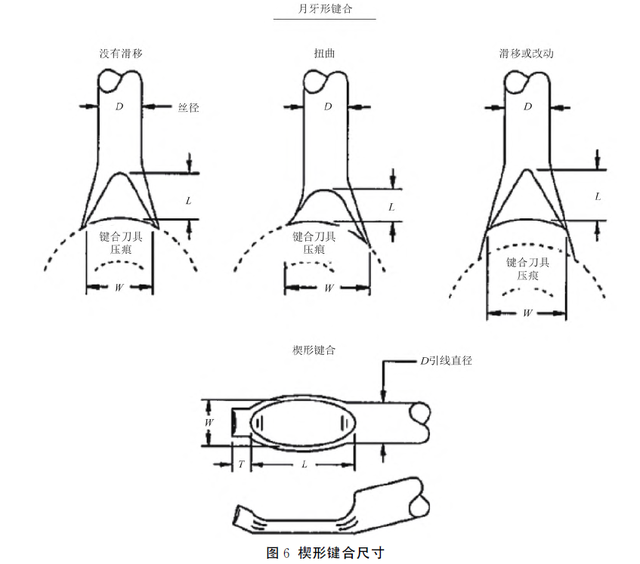
保持键合压力、键合时间和超声功率的工艺参数不变,改变楔形键合宽度,使其分别为引线直径的1.2、1.5、2、2.5、3倍。在不同的楔焊宽度参数下焊接金丝,测量金丝的拉力值,并通过SEM 对焊点形貌进行观察,确定最佳比例。金丝的材料参数如表1所示,试验结果如图7所示。为了更准确表示金丝线上的受力,通过式(2)计算金丝线上的拉力值。
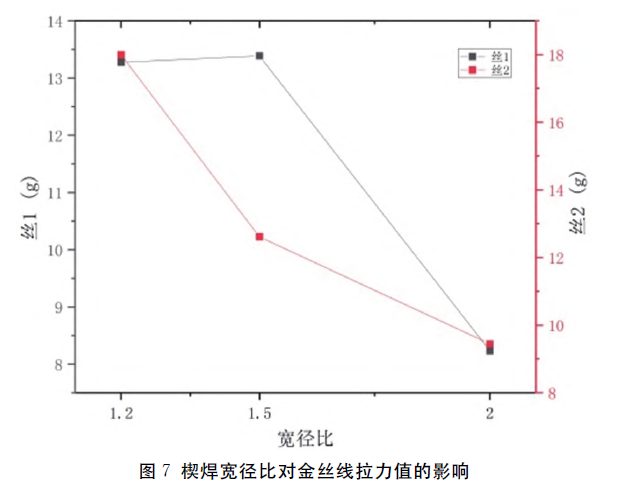
由试验结果可知,楔焊宽径比从1.2升至2后,金丝拉力值逐渐下降;当宽径比超过2后,无法完成金丝楔焊过程,也就没有金丝拉力值。因此,在宽径比为1.2的情况下,金丝拉力值最佳。金丝拉力值不能完全表征金丝楔焊强度的优良,还需要结合楔焊焊点形貌加以判断。图8~图10为金丝楔焊焊点的SEM图。
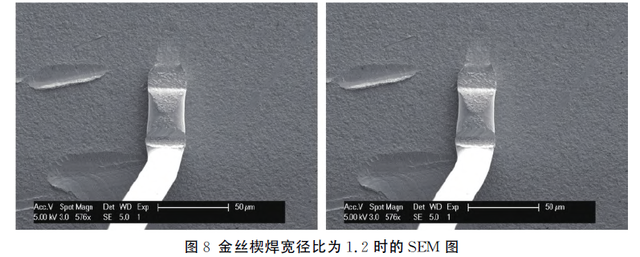

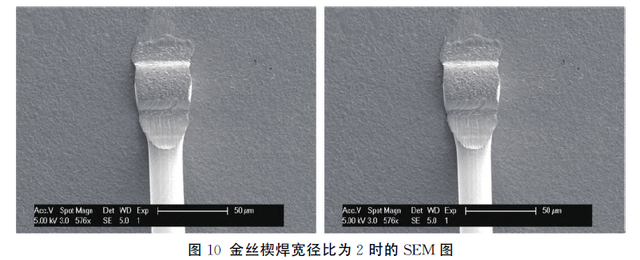
通过SEM图可以观察到,当楔焊宽径比为1.2时,焊点变形情况最好,金丝与楔形键连接颈部宽度、长度大小适宜,且楔形键及引线颈部无缺陷;当楔焊宽径比增至1.5和2时,焊点变形过大,金丝与楔形键连接颈部宽度、长度加大,导致颈部薄弱,容易断裂。结合金丝拉力值,楔焊宽径比为1.2时拉力值最大;随着楔焊宽径比的增大,拉力值降低,与SEM图规律一致。综上所述,楔形键合宽度与引线直径的最佳比例为1.2∶1。
2.4 小结
从上述试验可以得出焊盘表面平整度、表面状态以及楔焊焊点形貌对金丝楔焊强度的影响规律。在焊接过程中,应保证焊盘金层尽量平整且不能有污染和杂质。此外,金丝楔焊焊点的宽度与引线直径的比值会影响引线键合的强度。当两者的比值为1.2时,金丝拉力值与SEM焊点形貌最佳。
3键合参数对金丝楔焊强度的影响
3.1 金丝楔焊第一焊点最佳参数探究
进行金丝楔形键合时,键合温度选取室温。键合压力、键合时间和超声功率对金丝键合强度的影响具有协同作用。试验选用红外探测器组件A进行金丝焊接,键合丝采用25 m金丝(材料参数见表1)。
金丝楔焊工艺中第一、第二焊点所采取的工艺参数不同。在红外探测器组件中,第一焊点在芯片焊盘上,第二焊点在陶瓷框架上。由于在室温下进行楔形键合,金丝与键合焊盘金层之间的焊接面没有冶金学的反应,故第二焊点所需要的能量大于第一焊点,工艺参数不同。表3列出了金丝楔焊的原始工艺参数。

试验中,首先改变第一焊点(芯片端)的工艺参数,论证其对金丝楔焊强度的影响。保持第二焊点的原始工艺参数不变。设置第一焊点原始工艺参数为参照组,改变功率、压力、时间等参数值。
超声时间是指在键合点上施加超声功率和键合压力的时间。只有在合适的超声时间范围内才能形成良好的键合。过短的时间会导致剥离,而过长则会导致颈部断裂的现象。因此,控制超声时间的本质就是控制超声能量的输入。故首先探究压力与时间的最佳比例。试验结果如图11所示。

图11(a)所示为原始工艺参数减半条件下增大压力(即减小时间与压力的比值)时的引线拉力值规律。可以看出,金丝拉力值明显降低。图11(b)所示为原始工艺参数条件下增大压力时的引线拉力值规律。将参数恢复正常后增压,验证上述的结论。与原始参数相比,金丝拉力值明显降低。当键合压力过大时,金丝吸收到的能量增大,使得金丝变形严重。发生过键合造成焊点底部引线的键合强度降低,导致金丝在拉弧过程中就发生断裂(故无拉力值)。
在正常参数下增大时间与压力的比值,试验结果如图12所示。图12(a)、图12(b)所示分别为减小压力、增大时间时的引线拉力值变化规律。可以看出,与原始参数相比,增大比值后金丝拉力值明显提高;当继续增大比值时,金丝的拉力值迅速降低。因此,增大时间与压力的比值能够提升金丝引线的键合强度,且最佳的时间压力比为4∶1。这是由于在超声楔形键合时,压住金线需要施加压力。若键合压力高,则金会被向外挤出,较高的键合力会导致焊盘露底、变形或损伤;当压力继续降低时,金丝吸收到的能量不足,焊点与基板之间的连接不牢固,焊点的面积和深度不够,无法产生合格的键合力。随着键合时间的延长,金丝键合时吸收的能量逐渐增多,金丝与焊盘之间形成的焊点尺寸就越大,焊点与焊盘结合面的强度增加,而金丝与焊点间连接处(即“颈部”)的强度会随之降低。所以过长的键合时间导致焊点过大甚至超出焊盘范围,并且空洞、裂纹等缺陷形成的概率增大。
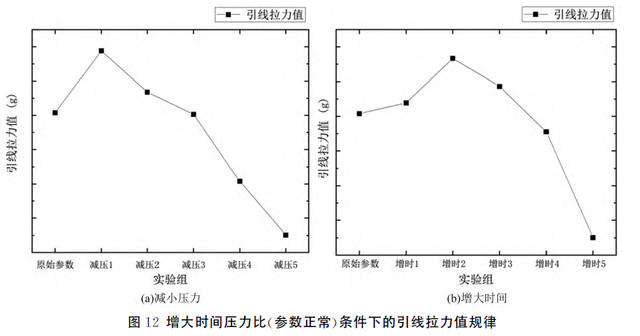
上述试验表明,当增大时间或者减小压力至二者比值为4∶1时,金丝楔焊的结合力均可提高。为进一步确定金丝引线焊接第一焊点的最佳工艺参数,对两组比值为4∶1的工艺参数进行对比,试验结果如图13所示。参数1为增大时间条件下的金丝拉力值;参数2为减小压力条件下的金丝拉力值。结果表明,通过减小压力来增大比值时,金丝引线楔焊的金丝拉力值更佳。因此,当时间压力比为4∶1时,金丝楔焊键合力最佳。合适的键合压力和键合时间可以使键合强度足够大。当时间增加时,过大的键合能量会将已形成的键合强度破坏而造成过键合,使其出现剥离和无连接。
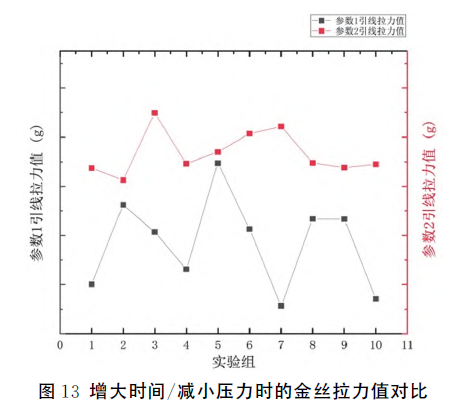
3.2 金丝引线第二焊点最佳参数探究
由上述试验可以得到金丝内引线第一焊点的最佳参数。固定第一焊点参数,对第二焊点参数进行探究。设置第二焊点原始工艺参数为参照组,改变功率、压力、时间参数值,根据第一焊点试验结果规律,论证减小压力对键合强度的影响。
选用与上述试验相同的组件进行金丝楔焊试验,测量金丝拉力值,探究第二焊点最佳工艺参数。试验参数及结果如图14所示。可以看出,第二焊点的参数规律与第一焊点一致。当减小压力(即增大时间压力比)时,金丝拉力值明显提升。当压力继续减小后,金丝拉力值会随之迅速下降。
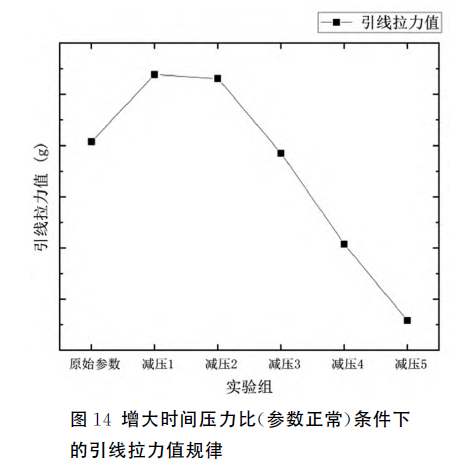
3.3 小结
从上述试验可以得出金丝超声楔形键合工艺参数对键合强度的影响规律。在进行金丝键合时,减小键合压力至时间压力比为4∶1时,对增大键合强度有促进作用。
4最佳参数下引线拉力均匀性探究
由上述试验可以得出金丝楔焊第一、第二焊点的最佳工艺参数。根据此参数进行样本均匀性试验,即在此参数下焊接引线200根,并分别测试金丝拉力值。拉力值分布直方图及拟合曲线如图15所示。结果表明,样本的方差为0.48,标准差为0.69。标准偏差越小,分布曲线越瘦高,随机变量的分散度就越小,拉力值越接近平均值(即精度高);反之,标准偏差越大,分布曲线越扁平,随机变量的分散度就越大,拉力值分布越离散(即精度低)。拉力值曲线接近正态分布,表示拉力值集中在样本平均值附近,样本间差异不大。因此在最佳参数下焊接的金丝拉力值较为均匀。
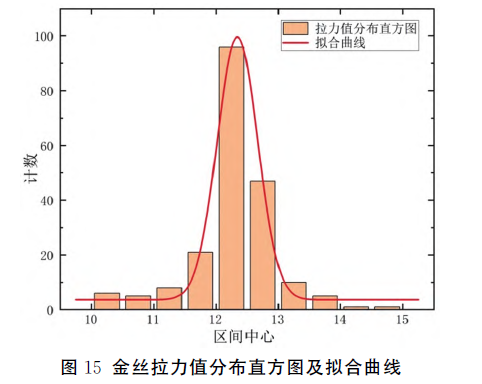
为了更加严谨地探究引线键合强度的优良,通过SEM观察焊点及断点形貌。图16为最佳工艺参数下金丝楔焊测量拉力后的焊点及断点表面形貌SEM图(左侧所示为焊点形貌)。可以看出,此参数下焊点变形良好,楔焊焊点宽度与引线直径的比值满足1.2倍的要求,焊点及断点表面平整、断口整齐,且表面没有明显缺陷。综上述,此参数下的金丝引线楔焊的键合强度最佳。
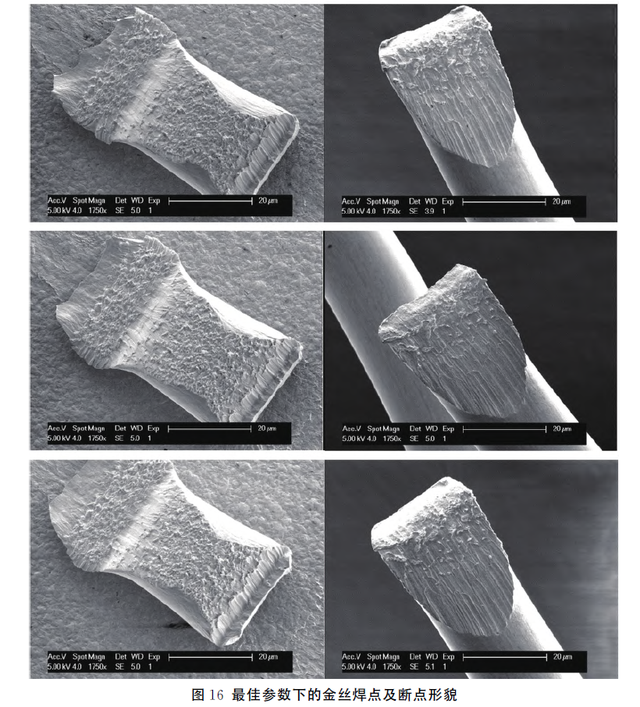
5结束语
金丝楔形键合在红外探测器组件中的应用十分广泛。提升金丝键合强度可以保证红外探测器的可靠性。本文基于红外探测器组件,对影响金丝楔焊质量的因素进行了分析论证,得到了以下结论:
(1)通过对焊盘表面平整度、表面状态的分析可知,其质量对金丝楔焊强度有影响。在焊接过程中,应保证焊盘金层尽量平整,并且不能有污染和杂质。
(2)金丝楔焊焊点的宽度与引线直径的比值为1.2时,金丝拉力值与SEM 焊点形貌最佳。在该参数下,焊接可以提升金丝键合强度。
(3)减小金丝超声楔形键合工艺参数中的键合压力对提高键合强度有促进作用。
(4)在最佳参数下,金丝焊线质量均匀,其规律符合正态分布,焊点及断点表面形貌符合国军标要求。
本文主要针对工艺参数展开研究,后续可以在工艺基础上进行仿真,进一步分析薄弱点,并针对结构性设计展开论证来指导实际应用。