红外探测器芯片高可靠性键合工艺研究
李峻光 王霄 乔俊 李 鹏
(沈阳化工大学信息工程学院 中国科学院沈阳自动化研究所 中国科学院光电信息处理重点实验室)
摘要:
金丝键合工艺广泛应用于红外探测器的封装环节。实验选用25μm 金丝,基于正交试验法,根据键合拉力值确定键合的最佳工艺参数。通过优化超声压力、超声功率、超声时间及接触力等工艺参数组合,改善了键合引线的电气连接性能和连接强度,从而提高芯片系统的信号传输质量。提出的引线键合工艺参数组合适用于红外探测芯片的键合。
0 引言
红外探测器在温度检测、环境监控、医学研究以及军事等领域有广泛应用,目前用于成像的探测器主要为焦平面[1]红外探测器,探测器的中间测试与封装均需要通过引线键合工艺来完成探测芯片与板级电路之间的信号连通。
引线键合技术根据键合方法可分为楔形键合和球形键合[2]。楔形键合的优势在于占用焊盘面积小,但该特点不适合于键合角度多样且四周面积较充分的红外焦平面探测器;球形键合方向灵活、可靠性高,因此本文采用球形键合开展研究。在探测器封装过程中,一根引线的失效都会影响整体系统的正常运行。相比于铂、银、铝、铜等材料,金的延展性最好[3],抗氧化能力强,在键合工艺过程中不需要保护气体,采用优化的超声压力、超声功率和超声时间的工艺参数组合,强化了键合引线的电气连接性能和连接强度。本文还研究了超声焊接之前的接触力对键合可靠性和推拉力的影响。本文采用25μm金丝引线,在先进引线平台对提出的差异化键合引线工艺参数组合方案进行实验验证。
1 探测器键合工艺
1.1 探测器封装过程
红外探测器根据探测的红外辐射波段可分为短波、中波和长波红外探测器[4]。高灵敏度的探测器是利用光电效应产生电子跃迁形成电流的光伏型焦平面器件。表1列出了不同波段焦平面的特征。焦平面器件需要与读出电路芯片经倒装焊互联、底部填充和背面减薄等工艺[5],然后将探测器读出电路芯片的焊盘键合到板级电路上实现信号传递。复杂的工艺流程是红外焦平面探测器高成本的主要原因。根据焦平面的特征进行有针对性的工艺参数组合调整,有助于获得最优的键合效果。常温工作的短波探测器可键合在FR-4材料PCB上,并采用金属管壳封装。中波和长波探测器则需要键合在导热性能更好的氧化铝或氮化铝陶瓷基板上,再封装在杜瓦中。键合是探测器封装的关键步骤,对探测器系统具有重要影响。
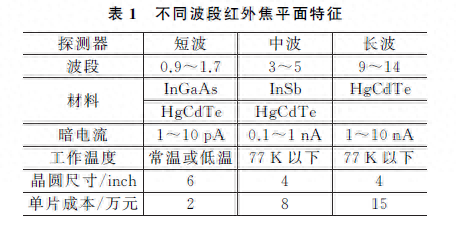
1.2 键合工艺流程
本文针对自研的短波红外探测器读出电路芯片的金丝键合工艺开展优化研究,芯片和PCB如图1所示,芯片焊盘规格为80μm×80μm,焊盘表面覆盖金属铜。PCB采用FR-4材料,焊盘表面覆盖化学镍钯金。引线键合的金线选择线径约25μm 的金丝。键合设备采用国产自动超声焊线机,除超声压力、超声功率、超声时间外,还可以精确控制超声焊接之前的接触力。球焊工艺选择BSOB模式,其工艺流程如图2所示。首先进行打火杆烧球,然后在第二焊点进行植球操作,完成植球后,在第一焊点开始键合,形成一道弧形的键合曲线,并键合到第二焊点。键合工艺参数优化分为两个方面:
(1)在符合GJB548B-2005(>3gf)拉力的条件下,分析焊线连接成功率达到100%情况下的最小接触力,以避免探测器焊盘有被击穿的风险为目标;
(2)在焊线连接成功率达到100%条件下,分析使得拉力测试达到最大情况下的合适接触力,并保证探测器正常电学连通,以实现高强度键合为目标。
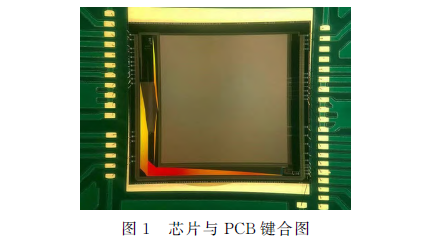
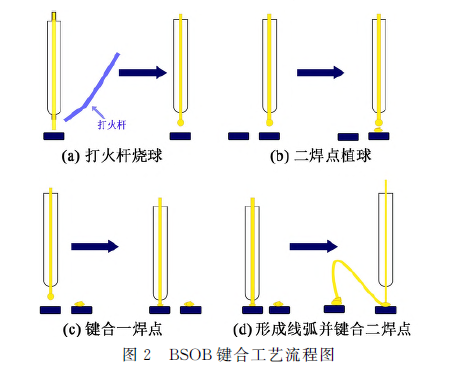
2 金丝键合工艺参数优化
超声波键合设备采用国产宁波尚进公司的BRT6000球焊机,用SPT 劈刀对纯度为99.99%的25μm 金丝进行键合,基板为FR-4的PCB板,镀层为2μm 厚度的化学沉金。在进行键合实验前,先用酒精进行清洁并确保其完全干燥,金丝键合如图3所示,以芯片上的焊盘点位作为第一焊点,引出金线,弧状焊接落点到介质基板的相应焊盘点位上。

键合质量受多种参数影响,而这些参数之间的关系并不明确[6-9]。基于预试验和实际的生产经验,实验选择了键合压力(F1)、超声功率(P )、键合时间(t)和接触力(F2)作为关键影响因素。其中,接触力是指劈刀与芯片在超声焊接之前的作用力,评估标准为引线的拉力值。首先要确保键合实验能够稳定成功,然后再进行拉力试验。键合实验时,尾丝的长度控制为0.2mm,跨丝长度控制为3mm。劈刀的安装高度保持统一,并确保第一焊点和第二焊点的参数设置相同[10]。
根据键合机出厂参考值和预实验得出的结果,表2列出了可能会影响键合的工艺参数及其参考值。主要的键合工艺参数为超声功率、超声时间、键合压力和接触力。
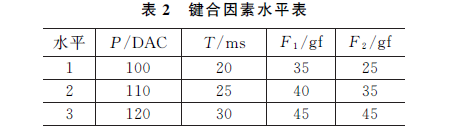
准备9组球焊键合的芯片样本,分别采用不同的键合工艺参数配置。构建L934 正交试验表,并对每个参数设定3个水平,详见表2。每种工艺参数进行30次键合实验后使用探测器电学测试检查芯片样品的键合是否达到预期效果。
正交试验结果如表3所示。正交实验表的特点是各列数据搭配均匀,因此各列之间的差异主要由该列的不同水平导致。其中,K1,K2,K3 代表水平1、水平2和水平3的平均值。通过观察各参数水平的极差R 可以评估各因素对键合效果的影响。极差越大,表示该因素对试验结果的影响也越大[11]。
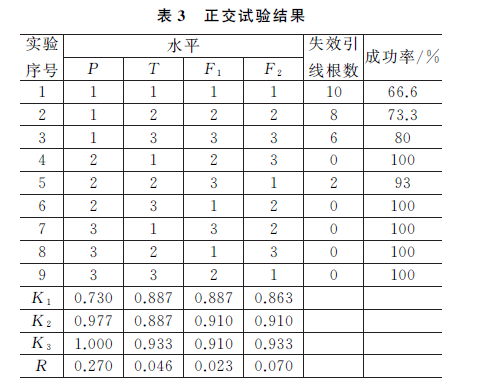
从结果来看,接触力和超声功率的影响明显大于键合压力和超声时间。这意味着在键合试验中,键合压力和超声时间对键合成功的影响相对较小。
针对接触力和超声功率进行深入分析。在试验中,当超声功率低于110DAC时,键合成功率显著降低,此时出现了键合点脱落、不完全断丝和烧球开路,工艺的稳定性大大降低,无法得出有效的实验数据。为了控制其他参数的影响,实验中将超声功率从110DAC开始增加,超声时间定为25ms,键合压力设置为40gf,研究超声功率和接触力对引线拉力的影响。为了确保试验的准确性,针对每种工艺参数都进行了30次键合实验,并用拉力机测定其断裂拉力[12]。如果在键合过程中出现脱粘或断丝现象,则将该次拉力值记录为0。
表4显示键合引线的拉力测试结果,结果显示各组平均拉力值遵循统计学的分布规律。所有测试的金丝拉力都符合GJB548B—2005的剪切试验标准(即大于3gf),表明金丝键合的质量都达到了较高的水平。
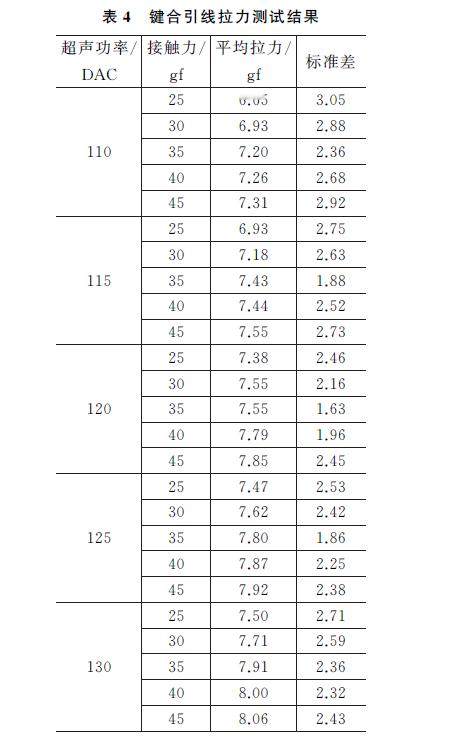
图4(a)、(b)分别为超声功率与平均拉力的关系图和超声功率与标准差的关系图。控制超声功率在110~120DAC 范围内,观察到平均拉力提升10%,而标准差下降20%,表明在该功率范围内,提高超声功率有助于加强键合强度并提高工艺的稳定性[13-15]。继续增加超声功率达到120DAC,平均拉力出现拐点,同时标准差也达到了最小值。当超声功率超过120DAC后,平均拉力的增长速度明显变慢,标准差开始变大,说明工艺稳定性开始下降。一般情况下,过高的超声功率会导致键合处形态发生过度变形,从而使键合塌陷,进一步引发键合不良的问题。
图5(a)、(b)分别为接触力与平均拉力关系图和接触力与标准差关系图。控制接触力范围在25~35gf,观察到平均拉力增大7%,而其标准差减小18%。表明在该范围内,提高接触力可以增强键合的稳固性。继续增加接触力到35gf,平均拉力和标准差均出现拐点。当接触力超过35gf后,平均拉力的增长放缓,标准差逐渐变大,这表明其对键合抗拉力的影响逐渐减少,且工艺的稳定性开始下降。一般情况下接触力过大容易导致劈刀击穿芯片管脚,从而出现损伤芯片的不良后果。
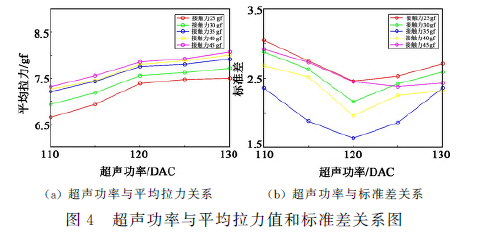
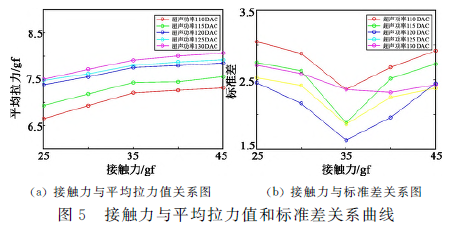
将键合后的芯片接入探测器电学测试系统进行测试,结果显示键合引线具有较好的电学连接性能,如图6所示。
实验结果指出,在对25μm 金丝进行键合的过程中,接触力的影响仅次于超声功率而远大于超声时间和键合压力,是一个不可忽视的关键因素。实验中发现,超声功率达到120DAC以及接触力达到35gf时,拉力值和标准差都出现明显拐点。尽管继续提高超声功率和接触力会增加键合强度,但可能因为接触力过大而导致劈刀击穿芯片管脚,从而造成损伤芯片等不良后果。
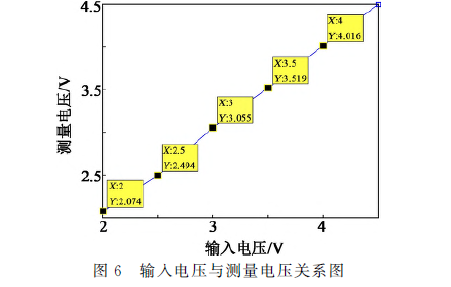
3 结束语
通过设计正交试验,确定适当的键合参数来减少探测器焊盘被击穿的风险。经过实验分析发现接触力在键合过程中的影响仅次于超声功率,远高于键合时间和键合压力。反复实验后得到稳定的键合参数:超声功率为120DAC,接触力为35gf,键合时间为25ms,以及键合压力为40gf。优化的键合工艺参数组合能够显著提高探测器芯片引线的强度和电气连通性能,进而提高探测器芯片封装的可靠性。