微电子封装低温Sn-xBi-yM 合金钎料研究
现状与展望
赵瑾 籍晓亮 贾强 王乙舒 郭福
(北京工业大学 北京联合大学)
摘要:
小型化、多功能电子产品的发展使器件在封装和组装过程中面临热损伤和基板翘曲等问题。为了减小电子封装和组装过程对芯片和器件的热影响,需要研究和开发低熔点的互连材料。锡铋(Sn-Bi)合金钎料由于低熔点、低成本、良好的润湿性和机械强度等特性受到了广泛关注,但是其中脆性Bi 相的偏析却不利于器件的长期服役可靠性。通过在Sn-Bi 钎料中添加合金元素构成Sn-xBi-yM 形式的合金钎料可以有效改善Sn-Bi 合金钎料及其焊点的服役可靠性。本文从钎料合金化的角度出发,分析并总结了不同合金元素对Sn-Bi 钎料的熔点、润湿性、微观组织、机械性能、界面反应及可靠性的影响。并根据现有的研究成果,展望了锡铋合金钎料未来的发展方向。
随着电子产品向高集成化、多功能化和多维化方向发展,电子封装用互连钎料面临了新的需求[1]。传统的电子封装钎料主要是锡铅共晶合金,其较低的熔点(183 ℃)、良好的润湿性和机械性能是其得以广泛应用的基础。21 世纪初由于铅元素所造成的环境和健康等问题,电子工业界开发了锡基无铅钎料并逐渐在消费电子封装领域取代了含铅钎料[2]。
近年来,微电子器件趋向小型化、多功能化发展,先进三维封装技术因此受到了广泛关注。在三维封装中,为实现高集成度的垂直互连,需要通过多次回流[3]。为了避免外层新一轮回流对内层已连接好的焊点产生热影响,内层连接使用的钎料熔点要高于外层互连使用的钎料。因此,需要研究和开发一系列不同熔点的钎料合金[4-5]。目前,高熔点的互连材料主要为高含铅量的95Pb-5Sn 合金(熔点为350 ℃),而广泛应用的Sn-Ag、Sn-Cu[6]、Sn-Ag-Cu[7]等无铅钎料的熔点居中(Sn-3.5Ag 共晶钎料熔点为230 ℃,Sn-3Ag-0.5Cu 钎料熔点为217 ℃[7])。低熔点无铅钎料主要有Sn-Bi[8]、Sn-Zn[9]和Sn-In[10]合金。Sn-Zn 共晶合金熔点199 ℃,微观组织与Sn-Pb 共晶合金类似,但抗腐蚀性差[11]。Sn-In[12] 钎料熔点更低(In-49Sn,120 ℃),塑性优良,但是强度低,而且昂贵的In 导致制造成本增加。
Sn-Bi 系钎料,具有相对较低的熔点(Sn-58Bi共晶合金,138 ℃),而且其具有和Sn-Pb 合金相近的微观组织、润湿性、机械强度和较低的价格,长期以来被大量研究[13]。但是Sn-Bi 合金钎料主要存在以下问题:(1)由于Bi 相是硬脆相,Sn-Bi 合金的塑性比Sn-Pb 合金差[14];(2)焊点热老化过程中,Bi 相偏聚在焊点界面处导致界面脆化[15],影响焊点的长期服役可靠性;(3)Sn-Bi 焊点的抗电迁移性能差[16]。为了解决上述问题,目前研究主要集中在降低钎料中Bi 含量,对钎料进行合金化,并将其定义为Sn-xBi-yM 合金钎料(其中x、y 为质量分数)。
本文从熔点、润湿性、微观组织、力学性能、界面反应、可靠性这5 个方面综述了Sn-xBi-yM 合金钎料的发展现状及研究成果,并据此展望了Sn-Bi基低温无铅钎料的未来发展方向。
1 Sn-xBi-yM 的熔点
在电子封装领域,熔点和熔化温度范围是选择互连钎料时考虑的首要特性。较低的熔点和较窄的熔化温度范围有利于回流。Bi 相的占比(x)和合金元素种类(M)均会影响Sn-Bi 合金的熔点和熔化温度范围。
由Sn-Bi 二元相图(图1 所示)可知,锡铋合金主要分为4 类:非共晶合金(Bi≤21%,质量分数, 下同)、共晶合金( Bi=58%)、亚共晶合金(21%<Bi<58%)与过共晶合金(58%<Bi<100%)。其中共晶合金的熔化温度范围最窄,这是Sn-58Bi共晶合金被研究最多的原因之一。当Bi 含量远离共晶点时,合金熔点开始升高。Dirasutisna 等人[17]用DSC 测量了Sn-xBi 系钎料(Sn-xBi-yM)的熔点(见表1),发现在共晶成分附近的合金熔点增幅较小(10 ℃以内)。这说明,在保证锡铋合金低熔点的前提下,可适当降低Bi 相含量以增强Sn-Bi 的塑性。
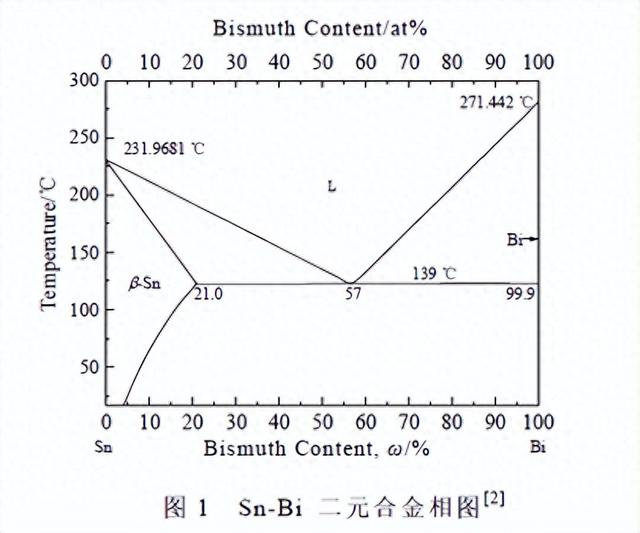
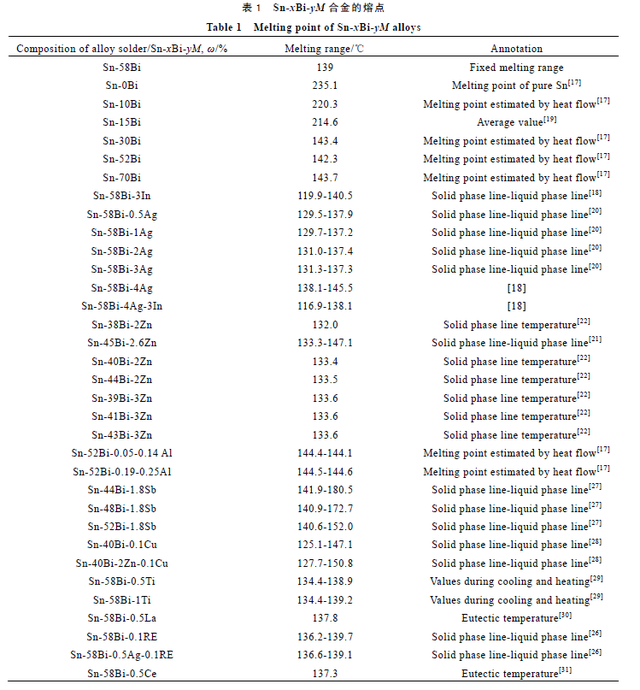
Sn-xBi-yM 合金钎料的熔点除受Bi 含量影响外,还受到合金元素M 种类的影响。添加的合金元素主要有:Ag、Zn、In、Al、RE 等。Wang 等人[18]发现,3% In 和4% Ag 复合添加到Sn-58Bi 中会降低其熔点,这主要是因为其中生成了Ag3Sn 金属间化合物(IMC)和In-Bi 相。类似地,Ding 等人[19]制备了Sn-15Bi-xAg 合金,DSC 曲线如图2 所示,峰的起始位置表示熔点大小。随着Ag 添加量的增多,合金熔点先升高后降低。以上现象主要因为:外来原子进入合金破坏原有金属键,生成Ag3Sn IMC,增加了合金内能,导致熔点下降。Yang 等人[20]研究了Sn-58Bi-xAg 的热性能,发现DSC 曲线上出现了明显的放热峰,表明Ag 的加入降低了熔点。他认为添加Ag 后生成的Ag3Sn IMC 可作为一种异质形核点,其破坏了Sn–Bi 共晶合金中的金属键,降低了过冷度(表现为一个放热峰),促进了合金的形核。
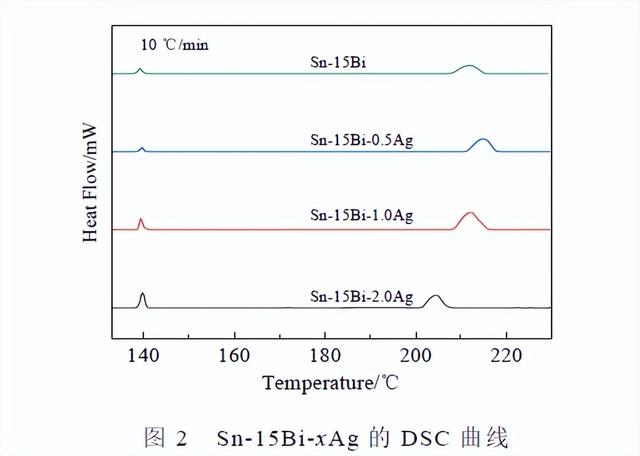
添加Zn 元素对Sn-Bi 合金的熔点几乎无影响。Zhou 等人[21]发现,添加Zn 并降低Bi 含量后合金的熔点波动较小。Chen 等人[22]研究了Sn-xBi-2Zn和Sn-xBi-3Zn 合金的热性能,发现少量Zn 加入后熔点略微升高(见表1)。这种微小的变化归因于Sn-Zn 之间的共晶反应影响了Sn-Bi 共晶,表现为DSC 曲线上随温度降低出现预共晶峰(如图3 所示)。无独有偶,Li 等人[23]对Sn-15Bi-xZn 的热性能研究结果表明,受到Sn-Zn 共晶的影响,出现了新的Sn-Bi-Zn 三元液相峰。因此,Li 的发现明确了Chen 等人提出的预共晶峰对应了Sn-Bi-Zn 三元相的生成。
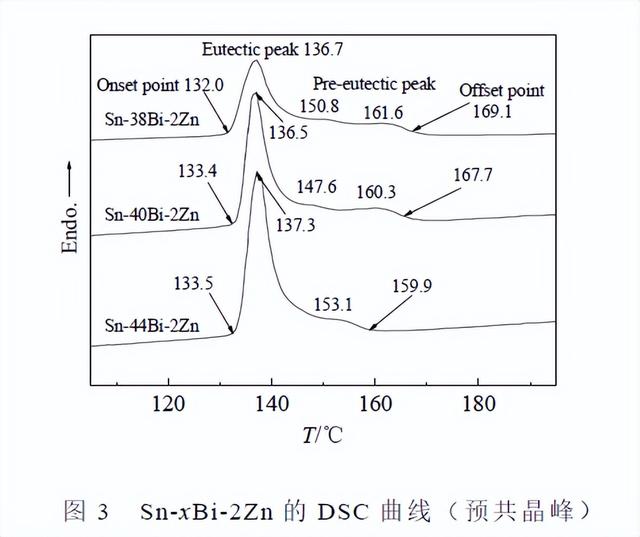
添加In 后,研究人员发现Sn-Bi 合金的熔点大幅度降低。Li 等人[24]对 Sn-Bi-In 的研究发现,在锡铋共晶峰前存在一个固相反应的小峰, 固相反应方程如下:

In 是少的能与Bi 形成IMC 的元素,但In-Bi相很难被观察到。这是因为随着温度升高,由In-Bi相分解出的In 固溶于β-Sn 相和Bi 相中。从图4 中可看出,InBi 相在不同Bi 含量的合金中都存在。因此, Sn-Bi 合金熔点降低归因于固相反应产生的InBi 相。
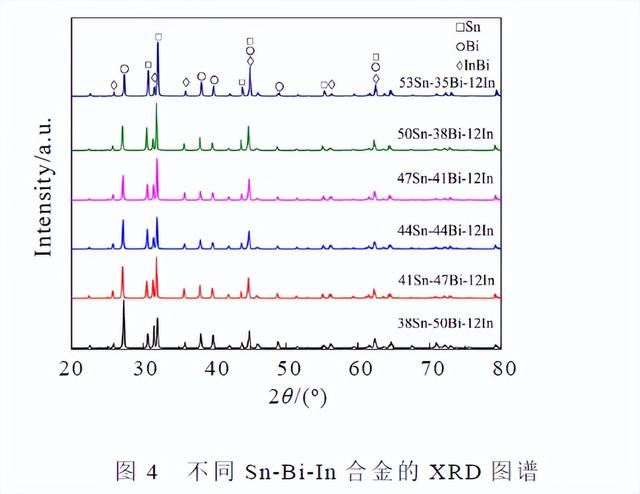
其他金属元素如Cu、Ti、Al、Ce、Re 对Sn-Bi合金熔点的影响见表1。例如,Sn-58Bi 在添加Cu后熔点先降后升,这与Cu 和Sn 生成复杂的IMC相有关[25]。添加少量Sb 则能大幅度提高Sn-Bi 的熔点,而添加微量稀土元素对熔点改变不大,主要对合金的组织性能有影响[26]。
将上述所涉及到的Sn-xBi-yM 复合钎料的熔点归纳总结,见表1。在Sn-xBi-yM 合金钎料中:
(1)合金的熔点主要受Sn、Bi 元素的占比影响,而且随Bi 含量的增加(x 值增大),熔点先降后升。
(2)能与Sn-Bi 合金反应的合金元素都能一定程度上影响合金熔点。
(3)除了Sb 和In 外,其他元素并不会大幅度改变Sn-Bi 合金的熔点。
2 Sn-xBi-yM 的润湿性
作为微电子封装用钎料,Sn-xBi-yM 合金钎料的可焊性(润湿性)也是需要考虑的主要性质之一。钎料的润湿行为主要为液态钎料在固态基板表面的铺展现象,润湿性越好则润湿角越小、铺展面积越大、速度越快。因此评估钎料润湿性的参数为:接触角、界面张力和铺展面积[32]。
液态钎料的润湿过程如图5 所示,图中三界面间的界面张力可用下列杨氏方程来描述[33]:
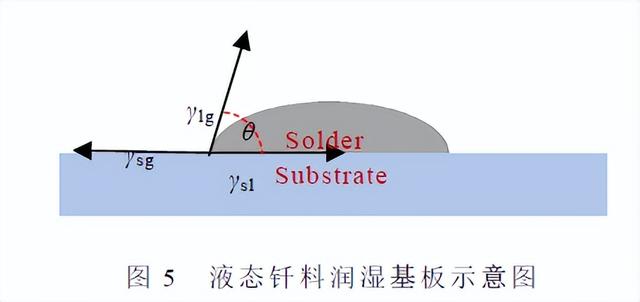
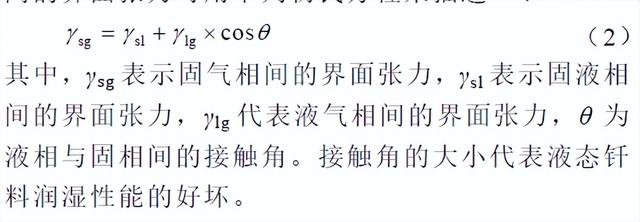
除了Sn 和Cu 之间的冶金反应生成Cu6Sn5 和CuSn3 促进润湿外,Sn 基钎料与电子封装常用的Cu基板之间润湿的驱动力也依靠下列反应[34]:

上式说明Sn 基钎料和Cu 基板间的化学反应能够去除Cu 板表面的氧化层,促进润湿。
在Sn-Bi 钎料中,仅有Sn 能与Cu 发生化学反应润湿,但钎料润湿性并不是随Sn 含量增多而升高的。如图6 所示,Sn 含量低于50%时,钎料的铺展面积随Sn 含量的升高而变大,因为焊接过程中Cu 基板中原子会向钎料基体扩散, 在界面与Sn 反应成Cu6Sn5,形成冶金结合,促进了化学润湿。但当Sn含量超过50%时,因Sn 和Cu 原子之间强烈的界面反应,反而阻碍了钎料的铺展[30]。
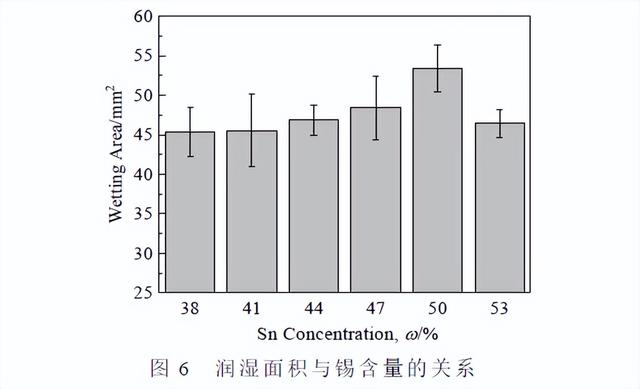
Sn-15Bi 合金作为与锡铅合金润湿性和熔点最接近的钎料,曾被大量研究[35]。Wang 等人[35]对比研究了Sn-15Bi 和Sn-40Pb 钎料的润湿性,结果如图7。在相同条件下,Sn-15Bi 的润湿力比Sn-40Pb小、润湿时间比Sn-40Pb 长,说明Sn-15Bi 的润湿性能仍不及锡铅合金。
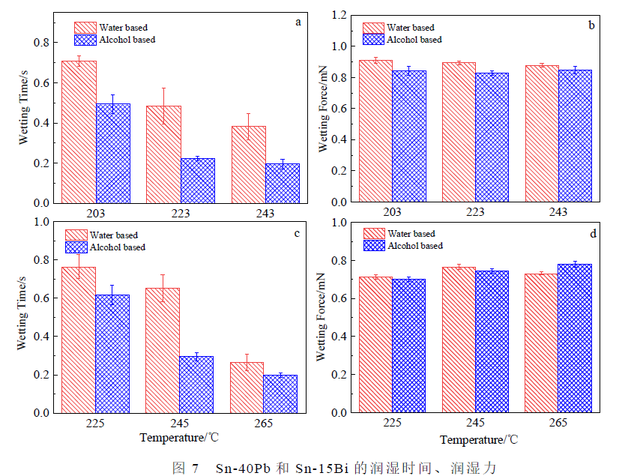
改善钎料润湿性的途径主要有:改变钎料性质、选择合适的焊接工艺、调控基板材料的表面状态等。其中改变钎料性质主要为钎料合金化( 如Sn-xBi-yM 合金钎料),润湿性主要取决于钎料基体Sn-Bi 和合金元素M 的种类。
首先合金元素会改变液态钎料的表面张力。Yang等人[33]发现在Sn-20Bi-xAl 钎料中,Al 游离在钎料表面并被氧化成膜增大了钎料的表面张力(γlg),降低了润湿性。Ding 等人[19]发现,在Sn-15Bi 中添加Ag后,由于Ag3Sn 的生成,钎料润湿性能提高。对于钎料的润湿性能的定量表征,除接触角外,还有“平衡接触扩散率”。由Shen 等人在研究Sn-40Bi-Zn-Cu 钎料时提出。平衡接触扩散率由下列公式定义[36]:

式中,S 代表扩散率,D 是熔融焊料球的直径,H是熔融焊料的高度。
相较于用凸点测量钎料的润湿角θ,平衡接触扩散率S 更多地用于表征焊球的润湿性。Shen 等人[36]用上述公式计算得出:单独添加Cu 促进铺展,Zn则相反,同时添加Cu、Zn 则阻碍铺展。这要归因于Cu、Zn 同时加入形成的Cu5Zn8 改变了钎料表面张力γlg。但Zn 元素单独加入则易被氧化成膜(类似添加Al),增大了γlg。Zn 与Cu 生成的IMC 虽促进了化学润湿,但是阻碍了Sn 与Cu 的化学反应。
与其他金属元素不同,稀土元素对润湿性改善显著。Dong 等人[26]发现在Sn-58Bi-RE 中,由于RE元素的表面活性作用,其聚集在液态钎料表面,降低了表面张力γlg 和固液界面张力γsl。但是应控制稀土元素的添加量,Zhang 等人[27]发现Sn-58Bi-Sb 铺展面积随Sb 的添加量先增后减。这是因为少量Sb可以降低界面张力,但过量添加后Sb 易与Cu 反应,进而阻碍Sn 基体的铺展。
总之,在一系列的Sn-xBi-yM 钎料中,依据Bi含量和添加M 的不同,其对润湿性的影响主要可以归结为以下几点:
(1)Sn 与Cu 间的化学反应润湿对锡铋合金整体润湿性起主导作用,但Sn 含量超过50%后钎料的润湿性会恶化。
(2)除Al、Zn 等易被氧化元素外,其他金属元素尤其是稀土元素,在少量添加时均会改善润湿性。
3 Sn-xBi-yM 合金的微观组织和机械性能
3.1 微观组织
合金的组织和结构决定了其性能,故合金元素会通过改变Sn-Bi 合金的微观组织进而影响其服役性能。首先,Sn-Bi 合金中的锡(β-Sn 四方结构)和铋(六方)在回流温度范围内都以单相存在(即无相变),其组织根据图1 的二元相图可分为以下3类:共晶组织、β-Sn 固溶体、富Bi 相。
Sn-xBi-yM 合金钎料中不同Bi 含量对应的组织也不同。非共晶的锡铋合金组织:主要由β-Sn 枝晶(灰色基体)和双相的共晶(网状组织)组成,其中灰色为Sn 相,白色为Bi 相[19],如图8 所示。
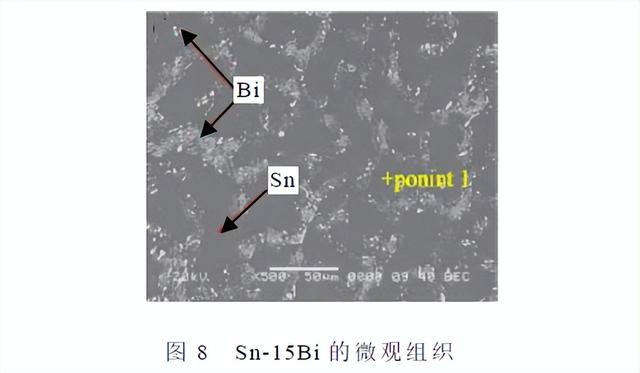
图9 为Sn-58Bi 共晶合金组织,黑色的Sn 相和白色的富Bi 相交替成网层状组织,部分Sn 相因非平衡凝固偏析形成一次枝晶[37]。由于Sn 与Bi 相金属性及相生长动力学机理上的差异,Sn-Bi 共晶通常呈现无规则状共晶组织。
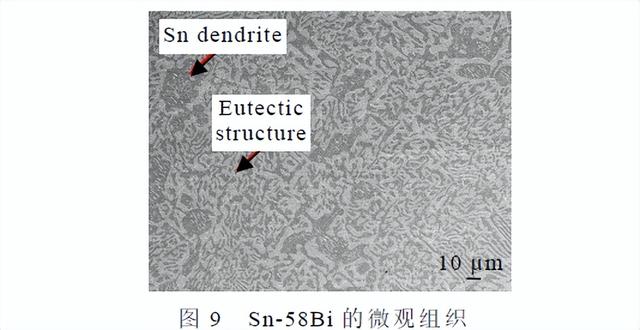
图10a 为Sn-90Bi 过共晶组织[34]。此时Bi 含量很高,已观察不到共晶组织。图中的灰色相为Sn相,白色Bi 相弥散其中。图10c 为Sn-30Bi 亚共晶组织,视野左下为先析出的β-Sn,基体组成分别为脱溶析出的富Bi 相和共晶组织。相较于非共晶成分,此时Bi 相含量明显变多。
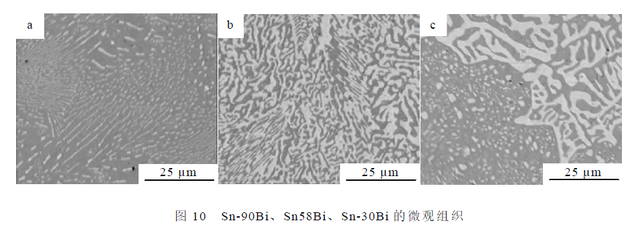
总之,在上述不同成分的合金中,共晶合金分布相较于其他成分更均匀、细小。但其中硬脆的富Bi相会危害焊点的机械性能和服役可靠性[38],所以,对于Sn58Bi 合金来说,其中Bi 相的组织形态是关键。
由霍尔-佩奇公式可知,金属中更细的晶粒尺寸可获得更高的屈服强度,因此钎料合金都期望获得细小和均匀的组织。对于合金组织细化方法主要可分为:快速凝固[39]、冷加工变形处理[40]、外加电场[41]、磁场[42]、超声波场[43]及其复合场[44]等物理方法。其中冷变形处理法主要用于存在多个固态相变的金属(例如,铁-碳合金),外加场则多运用于镁铝合金。对于熔点和强度低得多的钎料合金,主要的细化方式还是化学细化法:最典型的就是添加形核剂,利用颗粒的异质形核达到细化作用。对Sn-Bi 钎料进行合金化,其对微观组织的影响机理类似于化学细化法[45]。
合金元素对Sn-Bi 共晶组织的细化效果明显。Zhou 等人[37]向Sn-58Bi 中分别添加了In 和In+Zn,发现In 单独添加减少了共晶组织,增加了先共晶Sn 枝晶。In+Zn 复合添加则能细化共晶组织,归因于针状薄片Zn 相的异质形核作用。更显著是,Mokhtari 等人[46]发现向Sn-58Bi 中添加少量Ni 后共晶组织细化并变为规则共晶,如图11 所示。
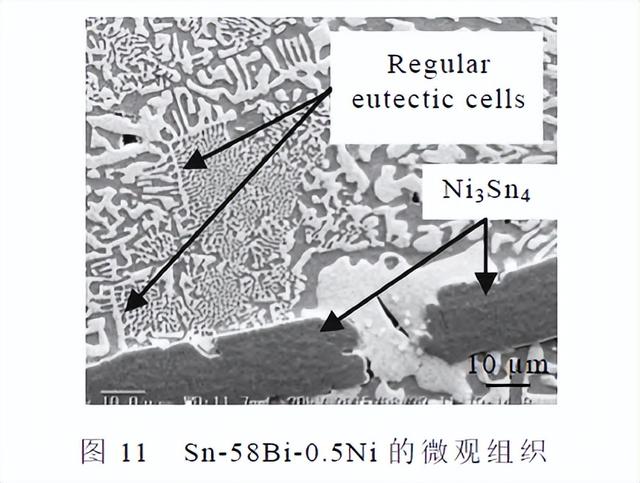
添加Cr 后也获得了规则共晶组织,如图12 所示。Sn-58Bi-yCr 的显微组织显示出了逐渐细化且明显的“规则共晶”(图中白圈标识)结构[47]。这要归因于生成的CrSn2 相IMC,其消耗了钎料中的Sn导致Bi 浓度升高,最终形成了此结构。并且,得益于CrSn2 的异质形核作用,共晶组织得到细化。
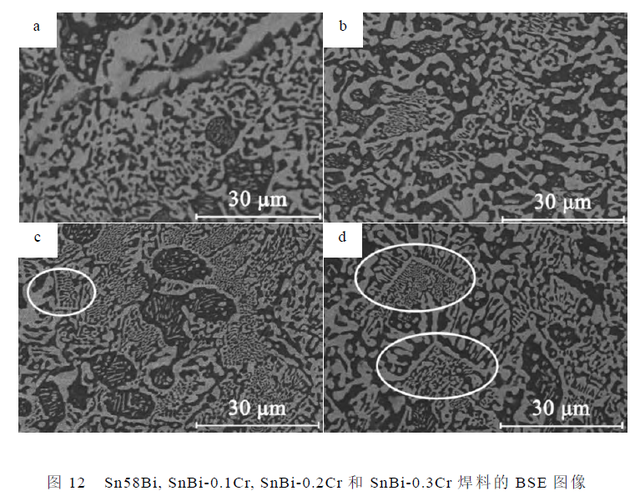
以上研究表明,能与基体反应生成IMC 的合金元素能够显著改变Sn-Bi 合金的组织。例如,向Sn-58Bi 合金中添加能与Sn 反应的合金元素Ag 和Cu 后,共晶组织出现鱼骨状规则化转变[48]。同时,Yang 等人[20]研究Sn-58Bi-Ag 钎料时发现共晶间距获得了细化。不同的Ag 添加量影响了生成的Ag3Sn的形态。如图13 所示,添加1% Ag 时,ε-Ag3Sn 相的尺寸约为1 μm,分布于Sn 相中;添加3%时,IMC 尺寸约为50 μm,分布于共晶组织中。在进一步测量IMC 和β-Sn 的相对取向关系后,发现细化原因为ε-Ag3Sn 作为了异质形核点,与规则组织相竞争。IMC 在低Ag 添加量中并不明显。不过随Ag 添加量增加,IMC 浮现,“鱼骨”结构被破坏。
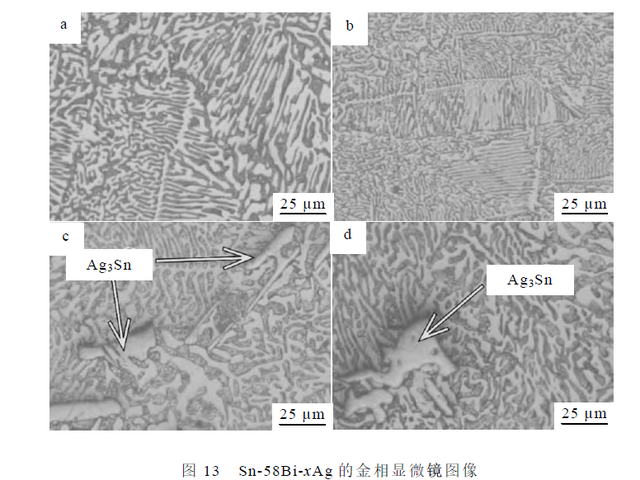
综上,合金元素对组织的影响取决于该金属是否能与Sn-Bi 基体发生反应。
(1)反应型元素加入后消耗Sn 生成IMC,影响扩散形成规则共晶结构(Ni、Ag、Cr、Cu 等元素),同时因IMC 的异质形核作用,组织得到细化。
(2)不发生反应也不固溶的元素(Sb、Zn)也通过异质形核作用细化共晶组织。
(3)In 能与Sn 反应,但多固溶于Sn-Bi 双相中导致其无细化效果。
为了产生最佳的组织细化效果,合金元素的添加量都小于1%。合金元素与对Sn-Bi 组织的影响总结如表2 所示。
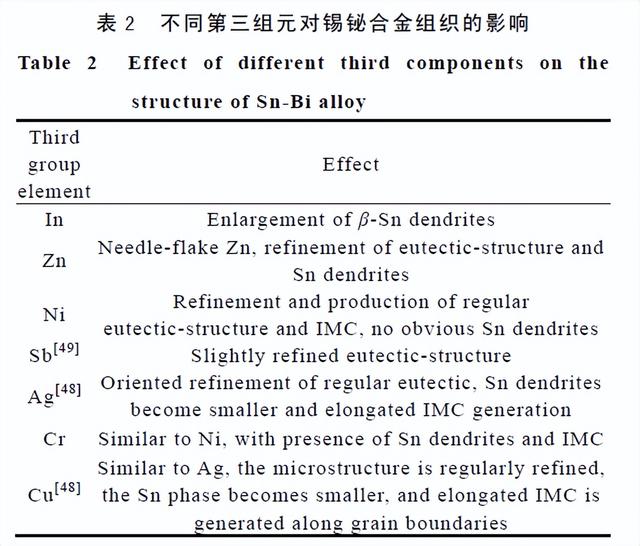
3.2 机械性能
Sn-Bi 合金钎料的强度高,但Bi 相的脆性大[49]、导致合金的塑性差[15]。添加合金元素后的Sn-xBi-yM合金组织发生了变化,其必然会对性能产生影响,本节从Sn-xBi-yM 合金组织和性能的关联出发,综述了合金元素对锡铋钎料机械性能的影响。
Sn-Bi 合金钎料中硬脆的Bi 相导致两相间结合力弱,结果钎料的塑性差和抗跌落性能差。Sliva等人[50]发现向Sn-34Bi 中添加Cu 元素后,合金的断裂模式由脆性断裂转变为韧性断裂。类似地,In和Ag 同时添加到Sn-58Bi 中后其钎料的抗跌落性能变好,归因于In 的增塑作用和Ag3Sn 的细化效果[51]。
依据霍尔-佩奇公式,前文中具有细化效果的元素都能增加合金钎料的强度,但对塑性的改善却不一致。Mokhtari 等人[52]发现Sn58Bi-Ni 的断裂伸长率较未添加降低一半,而Sn58Bi-In 的断后伸长率却提高了1 倍。与此不同的是,Sn58Bi-Cr 中的“规则状”共晶组织可牺牲强度来换取塑性(如图14所示)。这得益于细化的组织具有更多的相界,其能在变形过程中容纳更多的位错,减少应力集中,增加变形能力[47]。
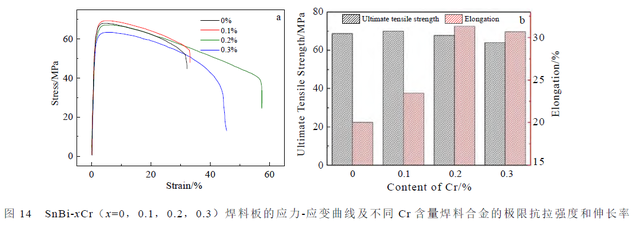
由于Sn 的滑移系比Bi 多,位错更易在Sn 相中滑移。Sn 相和Bi 相间力学性能的差异导致位错在二者之间传递时发生困难,位错因此会堆积在相界处。Cu、Cr 等元素细化了Sn-Bi 合金的共晶组织,产生了更多的相界,进而容纳了更多的位错,因此改善了合金的塑性[53]。
除了细化Sn-Bi 合金的组织之外,研究人员还提出了其他改善Sn-Bi 合金塑性的方法。例如,加In 后合金的共晶组织略微粗化,但仍具有塑性改善效果。Zhou 等人[37]提出了“固溶软化”来解释这一现象。他们发现In+Zn 复合添加到Sn58Bi 合金中相比单独添加Zn,合金的塑性得到了改善。这要归因于Zn 细化共晶组织和In 的固溶软化效果。当添加量较少时,In 不与钎料基体反应成IMC,而是固溶在Sn 相中。这种固溶行为减少了Bi 在Sn 中的固溶度,并降低了β-Sn 的键能,使得位错更易发生滑移,故称作“固溶软化”效应。
此外,改善Sn-Bi 合金塑性的方法改善Sn-Bi合金塑性的方法还有诱发Bi 相生成晶内孪晶[54]。
如图15 所示,当向Sn-58Bi 中添加Te 后,降低了Bi 的堆垛层错能,因此脆性的六方Bi 相容易产生变形孪晶。形成孪晶的过程一方面能承载少量的变形,另一方面可提高Bi 相中的施密特因子,激活Bi 中更多的滑移系。
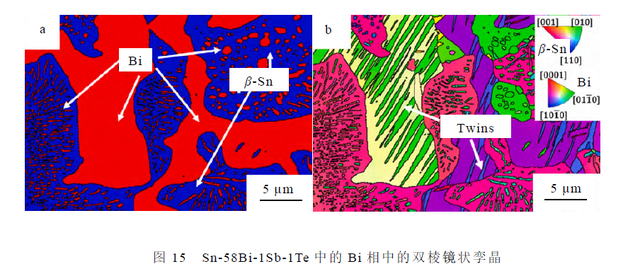
综上所述,在Sn-xBi-yM 钎料合金中,合金元素改善Sn-Bi 塑性的机理主要为:
(1)组织细化增加相界面,界面容纳更多位错;
(2)In 的“固溶软化”效应,软化Sn 相;
(3)Te 诱发Bi 相产生孪晶,增加变形量。
4 Sn-xBi-yM 焊点的界面反应
Sn-xBi-yM 合金钎料的应用性能不仅与钎料本身有关,而且与其焊接后产生的焊点也有关。焊点的界面反应是决定性能的关键。这是因为微子元件的失效多数发生在焊点[55]。根据前文,钎料在基板上的润湿主要分为物理润湿和化学润湿。界面IMC不仅可增加钎料的化学润湿,而且可以实现冶金结合增加焊点强度。因此,界面反应生成的IMC 的种类、形貌和厚度与该界面的性能和可靠性紧密相关。
在常见的Sn-xBi/Cu 焊点中,界面IMC 主要为Cu6Sn5 和Cu3Sn,其化学反应方程如下[56],首先钎料中的Sn 原子直接与基板中的Cu 原子反应生成Cu6Sn5:

Cu6Sn5 不稳定,随着回流温度的上升或回流时间的延长,其会由“贝壳状”向“层状”转变。组成上Cu 原子向Cu6Sn5 中扩散导致Cu3Sn 在靠近Cu基板侧形成,这降低了界面可靠性和机械性[57]。反应方程为:

随温度继续上升,2 种界面IMC 厚度增加。Bi不与Cu 反应,在上述反应后,剩余的Bi 会在界面处偏聚,阻碍Cu3Sn 的生成从而使得Cu6Sn5 层变厚[58]。Cu6Sn5 层导致界面脆化, 降低了接头机械性能[ 5 9 ]。
界面性能主要与存在的几种界面缺陷有关。在Sn58Bi/Cu 界面中,主要存在Cu3Sn、空洞和偏聚的Bi 相[60]。Hu 等人[60]指出空洞的产生是因为温度升高和焊接时间延长导致更充分的界面反应。此外,Bi 的偏析主要有2 个原因:(1)温度上升后Bi 原子扩散加快,从钎料扩散至Cu6Sn5,饱和后再扩散至Cu3Sn 中,最终因Bi 与Cu 不互溶而停止。(2)Bi 在Cu6Sn5 中的溶解度大于Cu3Sn,Cu3Sn 的生成消耗了Cu6Sn5,导致之前溶解的Bi 脱溶偏聚[61]。
对于Sn-xBi-yM/Cu 焊点,界面结构受到合金元素M 的影响。Gain 等人[62]研究了Sn-58Bi-0.5Ni(nano)/Cu 的界面, 发现在长时间回流后Cu3Sn 的生成被抑制,如图16 所示。添加Ni 的焊点中生成了比Cu6Sn5 更稳定的(Cu, Ni)-SnIMC,这阻碍了反应(6)的发生。和Ni 的效果类似,在Sn-32Bi-6Ga/Cu 焊点界面中,Cu 更易与Ga 反应, 故在回流初期只生成CuGa2 而没有Cu6Sn5[63]。
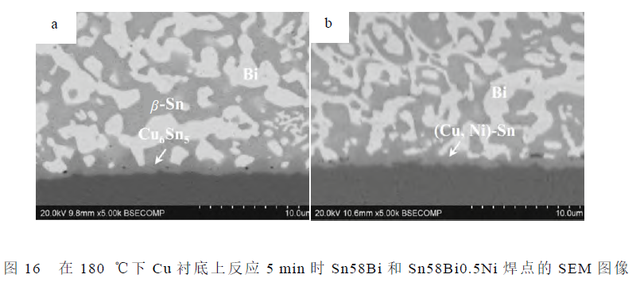
阻碍界面元素的扩撒。Hu 等人[64] 发现在Sn58Bi4Ag/Cu 焊点中,Ag 会扩散到Cu 基板表面形成Cu-Ag 层。这阻碍了Bi 向Cu 及IMC 层的扩散,降低了IMC 层厚度并改善了界面脆性。类似地,Song 等人[65]发现,Cr 加入后也具有阻碍Bi 扩散的效果。
Sn-xBi-yM 焊点界面的改性不仅能通过合金化钎料来实现,而且也可以通过改变基板来实现。例如,可在合金化钎料的同时也对基板进行处理,构成Sn-xBi-yM/Cu(N)焊点,其中N 代表对基板进行的特定处理。这种处理主要为基板表面处理, 如Zhang 等人[66]对Sn58Bi/Cu 中的Cu 板进行了表面洁净和镀金,得到了均匀分布的IMC 层(AuSnBi)和较少的空洞率。鉴于合金元素的改善效果,Hu等人[67]对基板进行了镀镍处理(Sn58Bi/Cu-xNi 焊点),他们发现镀Ni 后界面无Cu3Sn,且原有的IMC形貌被优化。利用Cu 基板结构和形态对界面的影
响,Shang 等人[68]实现了对于Cu 基板的单晶和多晶形态的调控,发现Cu3Sn 在多晶Cu 基板上比在单晶Cu 上生长更快。Ma 等人[69]提出,通过在基板上预置含Sn 的单晶IMC 形核剂可调控上方钎料中Sn 晶粒的c 轴取向。
综上,利用钎料合金化和基板表面处理可以有效地解决Sn-Bi/Cu 焊点界面中存在的Bi 扩散和界面IMC 粗化问题:
(1)合金元素取代原Cu6Sn5 中的Sn,抑制了Cu3Sn 的生成,降低了IMC 层厚度。
(2)合金元素阻碍Bi 的扩散,减少了界面的Bi 富集。
(3)基板表面处理,通过抑制Cu3Sn 的生成和阻碍界面元素扩散等多种方式改善界面性能。
上述Sn-xBi-yM/Cu(zN)焊点的界面IMC 组成及形貌差异如表3。
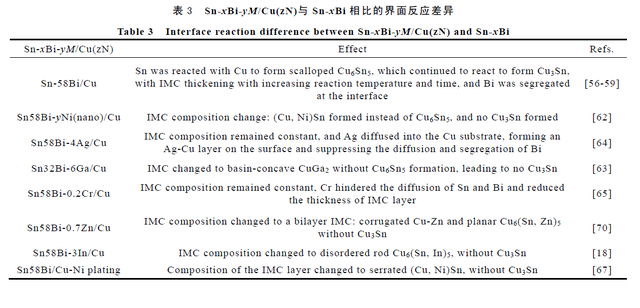
5 Sn-xBi-yM 焊点的热可靠性
在微电子器件的服役过程中电流作用下焊点内产生焦耳热,因此焊点会长期经历热环境[23]。同时在间歇开关使用的器件中,整个焊点还会经历热循环[71]。Sn58Bi 比广泛使用的Sn-3Ag-0.5Cu 钎料具有更好的热循环可靠性[72]。但是,热老化过程中硬脆Bi 相在界面处的偏析和粗化导致焊点的长期服役可靠性降低[73-74]。
热老化可以分为等温老化和变温老化,不同环境下接头界面形貌演变有所区别。图17 揭示了整个Sn-58Bi/Cu 界面在等温热老化过程中的演变[18]。首先,如图17a 所示,焊后界面处仅有一层薄的扇贝状Cu6Sn5,此时既无Cu3Sn 层,也未见Bi 偏析。随老热化时间延长,Cu6Sn5 从扇贝状转变为层状,出现双相粗化和薄Cu3Sn 层(图17b)。继续热老化,界面几乎无变化。当老化到21 天(图17d),Cu3Sn/Cu 的界面开始出现Bi 偏析和空洞。如图17e 中箭头所示,当老化时间到28 天时,Bi 偏析更明显。最终,钎料的粗化不明显,但连续的富Bi 相形成脆化了界面。
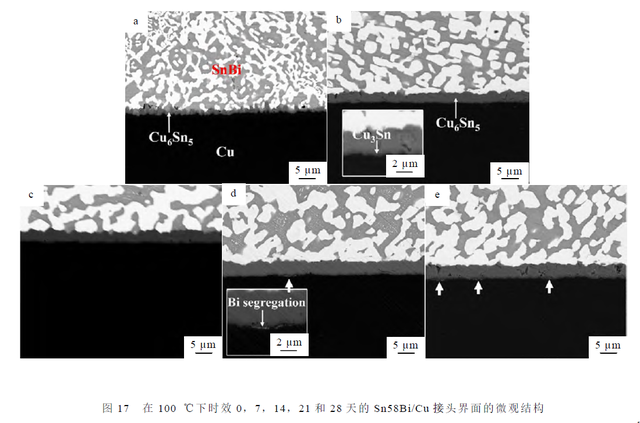
与等温老化不同的是,在变温老化(接头中存在温度梯度)中,Bi 偏析和粗化现象将更加严重。Liang 等人[14]通过相场模拟得出,在温度梯度下,Bi 原子会沿热流方向迁移,其会在冷端形成富Bi相偏析层,在热端余留下富Sn 相。这导致了严重的相分离现象,恶化了焊点可靠性。而且,Wu 等人[75]通过对Cu/Sn-58Bi/Cu 接头进行变温老化,发现Bi 会向冷端迁移,是主要的热迁移元素。
在热老化下锡铋焊点中的Bi 偏析和粗化的机理主要有以下两点:(1)Bi 相热导率小于Sn 相,这导致Bi 相内产生较大的温度梯度。在热差驱动下Bi 相扩散更快,表现为冷端的Bi 偏析,偏析长期积累后表现为粗化。(2)热驱动下焊点中的Cu 扩散更快,引发界面反应消耗Sn,加剧了Bi 在界面的富集。
Sn58Bi 钎料因为熔点低,在室温下就会发生热老化。如图18,在室温老化后白色Bi 相明显粗化,更长时间老化后(图18c、18d)枝晶和共晶中的Bi 相开始重溶到Sn 相中,同时粗化现象加剧。最终在室温老化263 天后基本观察不到共晶结构[76]。Wang 等人[76]对钎料进行了纳米压痕测试,发现Bi固溶后的Sn 相硬度上升并超过富Bi 相,说明热老化后钎料塑性降低的主要原因为:( 1) 硬脆Bi 相的粗化。( 2)Bi 固溶后Sn 相硬度上升,Sn相塑性恶化。
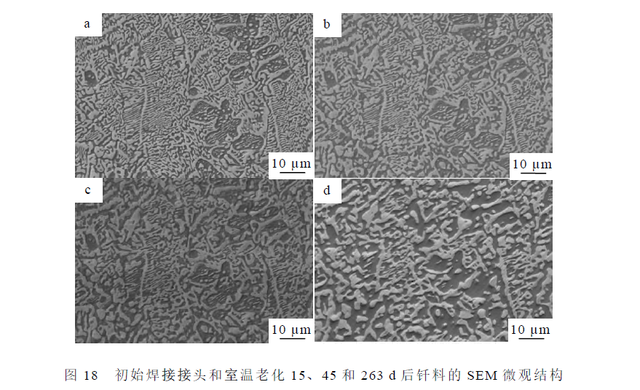
Sn-xBi-yM 合金钎料中的部分合金元素可以改善Sn-Bi/Cu 焊点的热老化可靠性。Nishikawa 等人[73]的研究发现,当Zn+In 混合添加后,其会抑制界面Bi的粗化,同时抑制IMC 层的生长。类似地,Hirata等人[77]对Sn-45Bi-2.6Zn-0.5In 和Sn-45Bi-2.6Zn-1In焊点研究后发现,由于Zn 在相界偏析阻碍Bi 和Cu的扩散,以及In 固溶于Sn 相导致的软化,焊点在老化过程中保留了Sn 枝晶,阻碍Bi 扩散,从而改善了界面性能。
根据研究,In 对Sn-Bi 合金钎料的机械性能改善效果较好,但改善效果与加入量有关。Mokhtari等人[52]研究了Sn-58Bi-(0.5, 1.0)In/Cu 的界面热老化性能,发现添加量为1%时,界面IMC 的形貌和成分被改变。但In 添加过量时会大幅度降低焊点的抗拉强度[18]。因此需要避免In 的过量添加,其他合金元素也是如此[19,78]。当合金元素的添加量非常多时,可能形成高熵合金,高熵合金被认为具有较好的塑性[79]。Liu 等人[80]制备了原子比为1:1:1:1 的SnBiInZn 高熵合金,他们发现其不仅熔点低,而且界面反应极慢,这归因于高熵导致的较低的IMC 生长驱动力。同时在高In 添加量后,出现了大量稳定的InBi 相。此外,Fe 基共晶高熵合金的出现也为开发研究Sn-Bi 共晶高熵合金提供了思路[81-82]。
综上,在Sn-Bi/Cu 焊点的热老化过程中,Bi是主要的热扩散元素,Cu 则控制IMC 的生成。添加合金元素能阻碍Bi 和Cu 的热扩散,改善焊点的热老化性能。因此, 钎料合金化+ 基板合金化(Sn-xBi-yM/Cu-zN)可充分利用合金元素的抑制扩散的效果来提升接头的热老化可靠性。
6 总结与展望
近年来在微电子封装领域,锡铋合金钎料因其类似锡铅合金的组织、较低的熔点、良好的润湿性和机械强度,其受到了大量的研究。这些研究都期求解决Sn-Bi 钎料中的硬脆Bi 相偏析后导致的服役可靠性问题。
本文综述了锡铋合金近年以来的发展现状及研究成果, 发现解决Sn-Bi 钎料长期服役可靠性问题的主要途径为添加合金元素构成Sn-xBi-yM合金钎料。合金元素可增加钎料润湿性、改善共晶组织、软化焊点界面、提高焊点的抗热老化性能。
为了解决Sn-Bi 钎料在应用中出现的问题,本文认为未来可在以下3 个方面进行研究:
1)添加合适的合金化元素:挑选出与 Sn 和Bi 都能形成IMC 的元素,例如In,Mn,Ga 等元素,在消耗Bi 阻碍Bi 扩散的同时,可以获得冶金结合。
2)高熵合金:鉴于共晶高熵合金的特殊性能,未来可利用Sn/B/In 体系来制备Sn-Bi 共晶高熵合金。利用高熵效应阻碍IMC 生长和高熵合金塑性好的特点,解决Sn-Bi 合金的长期服役可靠性恶化问题。
3)籽晶层:回流焊前在基板上添加一层组织均匀细化的Sn-Bi 籽晶层,利用籽晶层控制后续钎料的凝固,获得与籽晶层相似的组织,从而达到改善锡铋合金钎料性能的目的。