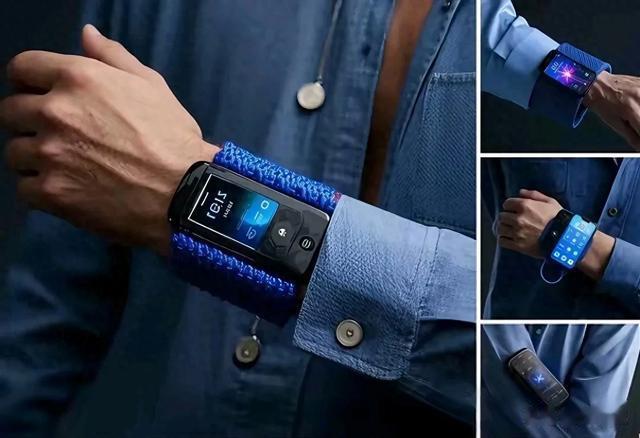
华为即将发布的新形态手机及其配套锂电池可能采用的新技术。包括铜箔、铝箔等材料,配方,能量密度,高电压和封装技术,硅基负极、高镍正极、电解质、隔膜等,比如更薄的集流体、复合集流体材料,或者柔性处理,以应对折叠屏手机的机械应力。
配方方面,之前讨论了电解液的添加剂组合、电极浆料的优化,可能需要进一步细化,比如具体的溶剂比例、新型导电剂的应用,以及如何通过配方调整来适应高电压和快充需求。
能量密度和高电压,比如通过高电压正极材料、硅基负极的使用,以及系统集成技术如CTP(Cell to Pack)或CTC(Cell to Chassis)的优化。
鸿蒙系统对电池管理的优化,比如软件定义电芯(SDC)、BMS的协同,以及AI在电源管理中的应用,这些都可能影响电池的设计和性能优化。特别是如何通过系统级优化来提升电池的效率和寿命。
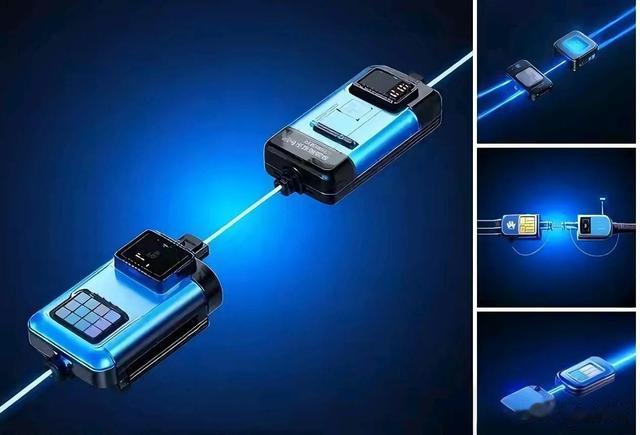
余承东透露的华为3月新机将搭载“新形态设计+原生鸿蒙系统”,这一组合对锂电池技术提出多维挑战:
形态适配性:折叠/卷轴屏需电池具备柔性、异形化设计能力;高能量密度:新硬件(如端侧AI芯片)功耗提升,要求电池容量与体积效率同步优化;快充与寿命平衡:4C以上快充需兼顾锂枝晶抑制与循环寿命;系统级协同:鸿蒙系统(HarmonyOS NEXT)通过AI调度与BMS深度融合,重新定义电池管理逻辑。二、材料创新:从集流体到活性材料的全面升级1.铜箔与铝箔:柔性化与高导电协同技术路径:超薄复合铜箔:采用PET/铜(6μm基材+3μm铜层)复合结构,厚度降至9μm(传统铜箔8μm),重量减轻40%,弯折寿命提升至10万次(传统铜箔≤5万次)。表面改性铝箔:通过等离子体处理(Plasma)在铝箔表面生成纳米级氧化层(Al₂O₃),提升耐腐蚀性,适配4.5V以上高压电解液。量产挑战:复合铜箔的激光焊接良率需从85%提升至95%以上;纳米氧化层均匀性控制(厚度偏差≤5nm)依赖高精度镀膜设备。2.正极材料:高电压与高镍并行技术路径:单晶高镍三元(NCM811):通过单晶化减少晶界裂纹,4.4V充电电压下循环寿命提升40%;高压钴酸锂(LCO):Al₂O₃+Li3PO4双包覆后电压提升至4.48V,能量密度突破750Wh/L;富锂锰基(LRMO):容量达250mAh/g,需固态电解质适配其高氧化性。量产挑战:单晶NCM811高温烧结(≥950℃)导致能耗成本增加30%;LRMO首效低(<85%)需预锂化补偿。3.负极材料:硅基体系与柔性集流体技术路径:硅碳复合负极(SiOx-C):硅含量提升至15%,比容量650mAh/g,搭配3D多孔铜箔(泡沫铜)缓解膨胀(膨胀率从300%降至120%);柔性石墨烯集流体:替代传统铜箔,厚度3μm,导电率1×10⁶ S/m,弯折半径≤1mm。量产挑战:硅颗粒纳米化(≤150nm)需高能球磨工艺;石墨烯集流体的规模化沉积成本(当前为铜箔的5倍)。4.电解质:高压适配与界面优化技术路径:双盐体系电解液:LiPF6+LiFSI(摩尔比1:1),耐压提升至4.5V,离子电导率1.2×10⁻² S/cm;局部固态化:正极侧涂覆Li6.75La3Zr1.75Ta0.25O12(LLZTO)固态电解质层,抑制界面副反应。量产挑战:LiFSI价格高昂(80万元/吨),需国产化降本(如新宙邦扩产);LLZTO涂覆厚度均匀性(±0.5μm)控制难度高。5.隔膜:耐高温与柔性化技术路径:复合涂层隔膜:PE基膜+勃姆石(Bohemite)+PVDF双层涂覆,耐热性从180℃提升至220℃,穿刺强度≥500gf;超薄柔性隔膜:厚度5μm(传统9μm),采用静电纺丝法制备PI纳米纤维隔膜,弯折10万次无裂纹。量产挑战:静电纺丝设备产能低(当前≤5米/分钟),需工艺优化。三、配方优化:高压、快充与寿命的平衡术1.电解液配方:添加剂协同增效组分设计:溶剂体系:EC:EMC:FEC =3:5:2(体积比),FEC提升硅负极SEI膜稳定性;添加剂组合:1% LiPO2F2(正极成膜)+1% DTD(抑制析锂)+0.5% TMSP(清除HF),4.5V循环100次容量保持率从70%提升至88%。量产挑战:FEC与TMSP兼容性需优化,防止凝胶化。2.电极浆料:高固含与高分散性技术路径:正极浆料:固含量72%(传统60%),采用BYK-2155分散剂,粘度控制在4000±500 mPa·s;负极浆料:CNT:SP =1:3复合导电剂,极片电阻降低30%。量产挑战:高固含浆料沉降问题需连续搅拌系统(如双螺杆挤出机)。四、能量密度跃升:材料与结构的双重突破1.电芯层级:高活性材料占比技术方案:硅碳负极(15% Si)搭配单晶NCM811,能量密度达320Wh/kg;富锂锰基+金属锂负极(半固态),能量密度突破400Wh/kg。量产难点:硅基负极膨胀导致极片翘曲,需预锂化与机械约束设计。2.系统层级:结构集成创新CTP 3.0进阶版:电芯直接集成至手机中框,空间利用率从55%提至70%;多极耳设计(6极耳)降低内阻20%,支持4C快充。分体式电池系统:折叠屏手机采用主副电芯(3000mAh+1000mAh),动态供电延长续航15%。五、高电压技术:突破4.5V天花板1.正极材料高压化表面包覆:单晶NCM811表面LiAlO₂包覆(2nm),4.5V循环寿命提升至800次;体相掺杂:Mg/Ti共掺杂稳定晶格结构,相变起始温度从210℃提至250℃。2.电解液高压适配新型锂盐:LiFSI占比提升至30%,耐压5.0V,搭配0.5% LiODFB抑制铝箔腐蚀。3.负极界面强化人工SEI膜:硅碳负极表面LiF-rich层(通过FEC分解生成),降低界面阻抗30%。六、封装技术:柔性化与异形化1.铝塑膜创新复合结构:外层PI膜(12μm)+铝层(40μm)+CPP层(30μm),弯折半径≤3mm;封装工艺:激光封边+热压强化,封装强度≥25N/15mm。2.异形电芯设计阶梯式电芯:针对折叠屏铰链区域,采用L型堆叠,空间利用率提升15%;可伸缩封装:卷轴屏电池采用滑轨式分段封装,电芯单元伸缩率≥30%。3.散热-封装一体化嵌入式VC均热板:将0.3mm超薄均热板嵌入电芯顶部,散热效率提升50%。七、鸿蒙系统协同:软件定义电池(SDC)1.BMS深度整合电芯级数据监控:实时读取膨胀应力、析锂状态,动态调整充电策略(如4C→2C);AI寿命预测:基于用户习惯预测电池衰减,误差率≤3%。2.跨设备能源管理车机-手机联动:低电量时调用车载电池无线反向充电(50W,效率≥75%);分布式储能调度:多鸿蒙设备协同供电,峰值负载分担30%。八、量产挑战与产业链机遇1.核心瓶颈硅基负极膨胀控制:需开发自修复粘结剂(如PAA-PEDOT:PSS );复合铜箔量产设备:进口激光焊接设备(如德国Manz)成本高昂,需国产替代。2.国产化机遇材料领域:贝特瑞硅碳负极(已量产第3代,硅含量12%);璞泰来复合铜箔或其它材料厂商(良率突破90%)。设备领域:先导智能柔性电芯叠片机或其它厂商(精度±0.1mm);赢合科技等其它高精度涂布机(面密度偏差≤1%)。九、结论:华为新机锂电池技术路线与产业建议1.技术路线总结材料体系:正极:单晶NCM811(4.4V)或改性LCO(4.48V);负极:硅碳复合(15% Si)+3D泡沫铜集流体;电解液:LiFSI基双盐体系+局部固态化。封装技术:PI基复合铝塑膜+异形阶梯式设计;系统集成:CTP 3.0进阶版(空间利用率70%)。2.性能指标能量密度:电芯级320-350Wh/kg,系统级提升25%;快充能力:4C有线快充(15分钟80%),50W无线快充;循环寿命:1200次(容量保持率≥80%)。3.对锂电从业者的战略建议短期聚焦(2024):攻关复合铜箔激光焊接工艺,良率提升至95%;与电解液厂商合作开发LiFSI降本方案(如回收提纯)。中期布局(2025-2026):推进硅基负极预锂化量产(连续式预锂化设备投入);参与鸿蒙BMS接口标准制定,抢占SDC协议话语权。长期规划(2027+):布局全固态电池核心专利(如硫化物电解质合成工艺);联合设备商开发异形电芯全自动产线。华为新机或成为锂电行业从“被动跟随”转向“主动定义”的关键转折点,柔性化、高压化、软件协同将成为下一代电池技术的三大核心壁垒。唯有深度融合材料创新、工艺革新与系统级设计,方能在这场变革中占据先机。
加油华为💪💪💪
除非是固态电池要不然没啥创新[得瑟]
奏折有了下一步应该是竹简形态了