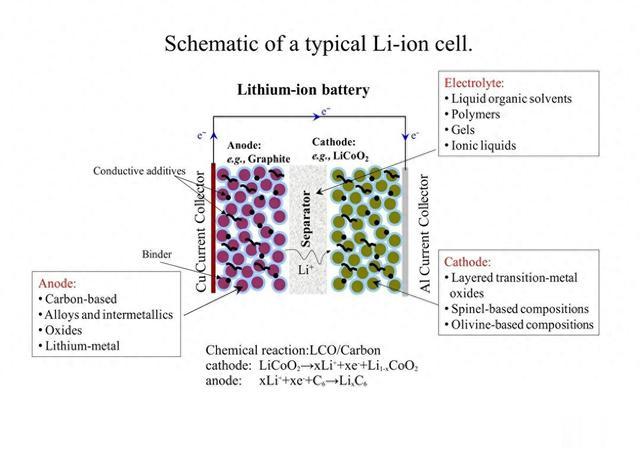
正极极片通常是在铝箔上涂布浆料,然后进行后续处理。但有些情况下,会在料区边缘涂3-5mm宽的陶瓷边,虽然增加了成本和工序,但好处显现。
首先,电池的安全性,锂电池在充放电过程中可能会有体积变化,或者温度变化导致材料膨胀收缩。边缘涂陶瓷可能起到支撑作用,防止极片边缘因为应力集中而破裂,从而避免内部短路或者陶瓷边可能具有更高的机械强度,防止极片在卷绕或叠片过程中边缘受损,导致活性材料脱落。
另外,陶瓷材料通常有较好的耐高温性能。在电池过热时,陶瓷边能提供额外的隔热保护,防止热失控蔓延。或者,陶瓷边是否有助于减少边缘的锂枝晶生长,因为边缘如果结构不够紧密,容易形成枝晶,导致短路,而陶瓷的硬度可能抑制枝晶穿透隔膜。
再者,涂陶瓷边是否与电解液的分布有关,在极片边缘,电解液容易积聚或分布不均,陶瓷涂层可能调整电解液的浸润性,确保更均匀的电流分布,减少极化现象。
还有,陶瓷边是否在电池组装过程中起到定位或对齐的作用。比如在卷绕时,帮助极片对齐,避免错位,从而提高电池的一致性和良品率。或者是在涂布过程中,陶瓷边作为边界标记,帮助后续的裁切或分条工序更精确,减少尺寸偏差。
另外,考虑生产过程中的问题。涂布浆料时,边缘可能容易出现厚度不均或开裂,陶瓷边可能作为加固层,防止涂布后的极片在干燥或辊压时边缘翘起或破损,从而提升整体极片的平整度和机械稳定性。
还有,陶瓷边是否影响电池的电化学性能。比如,边缘区域的电流密度可能较高,陶瓷涂层可能具有更高的导电性或绝缘性,调整电流分布,防止边缘过充或过放,延长循环寿命。或者相反,陶瓷是绝缘的,可以防止极片边缘与负极接触导致短路。
需要验证这些可能性。比如陶瓷材料的具体成分是什么?如果是氧化铝、氧化锆等,它们通常是绝缘的,但可能用于隔离。或者陶瓷涂层是否是多孔结构,允许离子通过但阻止电子传导?这可能防止边缘的微短路。
另外,涂陶瓷边可能减少极片在分切时的毛刺,因为陶瓷更坚硬,分切时边缘更整齐,减少金属颗粒或毛刺刺穿隔膜的风险,从而提高安全性。
再想,极片在卷绕或叠片时,边缘容易受到机械应力,陶瓷边提供额外的保护,减少破损,提高电池的耐久性。此外,如果电池在使用中受到冲击或振动,边缘加固可能防止内部结构损坏。
提高机械强度,防止边缘破损;抑制枝晶生长;改善电解液分布;提升安全性,防止短路;辅助对齐和裁切;减少毛刺;增强热稳定性等。这些优点可能带来的整体效益超过增加的成本和工序,比如提升电池寿命、安全性和一致性,减少故障率,因此在高端或高要求的电池应用中采用。
1. 提升机械稳定性与安全性抑制边缘破损与活性材料脱落:极片在卷绕、分切或电池循环过程中,边缘易受机械应力影响。陶瓷涂层(如氧化铝、氧化锆等)具有高硬度和耐磨性,可防止铝箔边缘开裂或活性材料脱落,减少内部短路风险。减少分切毛刺:陶瓷边的硬度高于铝箔,在分切工序中能形成更整齐的边缘,避免金属毛刺刺穿隔膜,降低微短路概率。2. 改善电化学性能均匀电流分布:极片边缘的电流密度通常较高,易引发局部过充或析锂。陶瓷层可通过调整边缘区域的导电性(如绝缘或梯度导电设计),抑制枝晶生长,延长循环寿命。优化电解液浸润:陶瓷的多孔结构可调节电解液在边缘的分布,避免局部干区或积液,提升充放电均匀性。3. 热管理与安全防护热稳定性增强:陶瓷材料耐高温(如氧化铝耐温>1500℃),在热失控时延缓热量扩散,为电池提供额外热缓冲,降低热蔓延风险。阻燃与隔热:部分陶瓷涂层具备阻燃特性,可抑制热失控链式反应,提升电池安全性。4. 工艺优化与一致性提升辅助对齐与定位:陶瓷边可作为卷绕或叠片时的视觉标记,提升极片对齐精度,减少因错位导致的性能波动。防止涂布缺陷扩散:在涂布工序中,边缘易出现浆料厚度不均或开裂。陶瓷层作为“屏障”,可限制缺陷向活性区延伸,提高极片良率。5. 成本效益权衡虽然涂陶瓷边增加了材料与工艺成本,但其带来的综合收益显著:
降低故障率:减少短路、热失控等事故,延长电池寿命,降低售后维护成本。适配高能量密度设计:在追求轻薄化、高镍/硅碳体系的电池中,陶瓷边对安全性的提升至关重要。满足高端市场需求:如电动汽车、储能系统对电池可靠性的严苛要求,陶瓷边成为差异化竞争的关键技术。总结涂陶瓷边通过增强机械强度、优化电化学性能、提升热安全性和工艺一致性,有效平衡了高能量密度与安全性的矛盾。尽管成本增加,但其在延长电池寿命、降低故障率及满足高端应用需求方面的价值,使其成为高可靠性锂电池设计的重要策略。
系统性实施步骤
在锂电池正极极片边缘涂覆陶瓷边的系统性实施需要从材料选择、工艺设计、设备适配到质量控制的全流程规划。以下是分阶段实施的详细步骤:
一、前期评估与方案设计1. 需求分析与目标定义明确应用场景:根据电池类型(动力电池、储能电池、消费类电池)和性能要求(高能量密度、高安全性),确定是否需要涂陶瓷边及其优先级。确定技术指标:设定陶瓷边的宽度(3-5mm)、厚度(通常1-5μm)、附着力(≥0.5N/cm)等关键参数。2. 材料选型与配方开发陶瓷材料选择:对比氧化铝(Al₂O₃)、氧化锆(ZrO₂)、勃姆石(AlOOH)等材料的硬度、导热性、绝缘性,结合成本选择最优方案。浆料配方设计:开发陶瓷浆料配方(陶瓷颗粒、粘结剂、溶剂比例),确保分散均匀性、粘度(建议2000-5000 mPa·s)及与铝箔的兼容性。3. 工艺路线规划涂覆方式选择:同步涂布:在主浆料涂布设备上集成陶瓷边涂布模块,实现一次成型。分步涂布:单独设置陶瓷边涂布工位,与主涂布工序分开(需平衡效率与精度)。干燥与固化方案:设计陶瓷浆料的干燥条件(温度、时间),避免与主浆料干燥工艺冲突。二、设备改造与工艺集成1. 涂布设备适配涂布头定制:采用狭缝挤压式或微凹版涂布头,确保陶瓷边宽度精确控制(±0.2mm误差)。定位系统升级:加装高精度视觉定位或激光对位系统,保证陶瓷边与活性区的对齐精度(偏差<0.5mm)。2. 工艺参数优化涂布速度与压力:根据浆料流变特性调整涂布速度(建议10-30m/min),避免边缘流延或断带。干燥条件匹配:主浆料与陶瓷边的干燥温度需分层控制(例如主浆料80-120℃,陶瓷边100-150℃)。3. 边缘宽度与位置设计卷绕电池:陶瓷边宽度需覆盖卷芯最内层与最外层极片边缘,防止卷绕应力集中。叠片电池:陶瓷边位置需与隔膜对齐,避免叠片错位导致毛刺风险。三、工艺验证与质量控制1. 小试与中试验证DOE实验设计:通过正交实验优化陶瓷浆料固含量、涂布厚度、干燥温度等参数组合。性能测试:验证涂陶瓷边对极片柔韧性(180°弯曲无裂纹)、循环寿命(500周容量保持率≥80%)的影响。2. 在线检测系统部署实时监测项:陶瓷边宽度(机器视觉检测);涂层均匀性(β射线测厚仪或红外成像);边缘毛刺(高倍显微镜或激光扫描)。缺陷自动剔除:联动涂布机与分切机,对边缘缺陷极片自动标记并分选。3. 离线检测标准建立附着力测试:使用百格刀法或拉力试验机评估陶瓷层与铝箔结合强度。电化学分析:通过局部电化学阻抗谱(EIS)验证边缘电流分布均匀性。四、量产阶段优化1. 工艺稳定性监控SPC(统计过程控制):对涂布速度、浆料粘度、干燥温度等关键参数进行CPK(过程能力指数)分析,确保CPK>1.33。定期维护:清洁涂布头与干燥箱,避免陶瓷颗粒堵塞或结焦。2. 成本控制策略浆料回收利用:设计陶瓷浆料循环系统,回收涂布头两侧溢流浆料。薄层化技术:在满足性能前提下,通过纳米陶瓷粉体降低涂层厚度(如1μm以下)。3. 持续改进失效模式分析(FMEA):针对陶瓷边开裂、脱落等问题,制定预防措施(如优化粘结剂比例)。新材料迭代:探索复合陶瓷(如Al₂O₃+SiO₂)或柔性陶瓷涂层,平衡硬度与韧性。五、应用场景差异化策略动力电池:优先陶瓷边的热稳定性与防短路能力,宽度可增至5mm。储能电池:侧重成本控制,采用低固含量浆料或局部点涂。消费类电池:通过陶瓷边辅助卷绕定位,提升轻薄化设计精度。总结系统性实施涂陶瓷边需以“需求定义-工艺开发-设备适配-质量控制”为主线,结合实验验证与量产反馈持续优化。其核心在于通过精准的工艺控制与材料创新,在成本可控的前提下,最大化陶瓷边对电池安全性、寿命及一致性的提升价值。