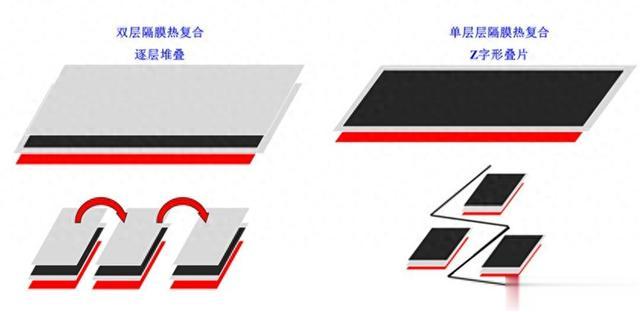
从“人”开始。操作人员在混浆、涂布、碾压、分条这些工序中的操作是否规范?有没有培训不足的情况?比如在混浆时搅拌速度或时间控制不当,导致浆料不均匀,或者涂布时涂布速度、厚度控制不好,可能会影响负极的附着力,导致掉粉。另外,操作人员是否按照SOP执行,是否存在疲劳或疏忽的情况?
然后是“机”方面。设备方面,混浆机的搅拌效率是否足够,有没有磨损或老化?涂布机的涂布头是否均匀,有没有堵塞或磨损导致涂布不均匀?碾压机的压力是否稳定,辊面是否平整,温度控制是否合适?分条机的刀具是否锋利,切割参数是否合理,是否会产生过多的粉尘?这些设备问题都可能导致负极材料的结构不稳定,容易掉粉。
接下来是“料”的因素。负极材料本身的质量如何?比如活性物质、导电剂、粘结剂的比例是否合适?特别是粘结剂的选择和用量是否足够,因为水系负极通常使用水溶性粘结剂,如果粘结剂分散不均匀或用量不足,会导致附着力差,容易掉粉。另外,浆料的粘度是否合适,搅拌后的浆料有没有充分分散,是否存在团聚现象?
“法”指的是工艺方法。混浆的工艺参数,比如搅拌时间、速度、顺序是否正确?涂布的干燥温度和时间是否合理,干燥不够会导致涂层内部有水分残留,影响粘结效果;干燥过度可能导致涂层开裂。碾压的压力和次数是否适当,过大的压力可能破坏涂层结构,过小则无法压实。分条的工艺参数,比如速度、张力控制是否合适,是否在分条过程中产生机械应力导致掉粉?
“测”方面,检测方法和标准是否合理?在制程中是否设置了适当的检测点,比如浆料的粘度、固含量测试,涂层的厚度、均匀性检测,碾压后的密度和孔隙率测试,分条后的尺寸和边缘质量检查?如果检测方法不准确或频率不够,可能无法及时发现掉粉问题。另外,检测设备的校准和维护是否到位,数据记录是否完整,是否有漏检的情况?
最后是“环”,环境因素。车间温湿度控制是否合适?水系负极对湿度比较敏感,湿度过高可能导致浆料吸水,影响粘结性能;温度波动是否会影响浆料的稳定性和干燥过程?车间的清洁度是否达标,是否有粉尘污染,导致掉粉问题加剧?静电控制措施是否到位,防止粉尘吸附?
现在需要把这些可能的因素系统地整理出来,并给出对应的改进建议。例如,在人的方面加强培训和操作监督;在设备方面进行维护和参数优化;在材料方面调整配方或供应商;在方法上优化工艺参数;在测量上增加检测点和频率;在环境上严格控制温湿度和清洁度。
可能还需要考虑各因素之间的相互作用。例如,如果环境湿度高,可能导致浆料粘度变化,进而影响涂布效果,导致掉粉。或者设备参数设置不当,加上材料粘结剂不足,共同导致问题加剧。因此,需要综合各方面的因素,逐一排查,找到根本原因。
有没有可能其他因素被忽略?例如,分条后的处理工序是否有问题?或者前段制程和后段之间的衔接是否有影响?不过用户已经明确问题出在前段的混浆、涂布、碾压、分条,所以可能不需要考虑后段工序。但可能需要确认是否在分条后存储或转运过程中出现问题,比如机械振动导致掉粉。
另外,关于水系负极,可能涉及到水作为溶剂的特性,比如干燥过程中的水分挥发是否彻底,残留水分是否在后续工序中导致问题。这可能与涂布和干燥工艺有关。
1. 人(Man)
可能原因:操作人员对水系负极工艺不熟悉(如搅拌速度、涂布参数设置错误)。SOP执行不到位(如未按标准控制干燥时间或碾压压力)。培训不足,缺乏对掉粉问题的敏感度。改进措施:加强工艺培训,重点强调水系负极粘结特性及关键参数控制。设立操作检查表,确保每个工序(如混浆粘度测试、涂布厚度调整)按SOP执行。引入技能认证机制,定期考核操作规范性。2. 机(Machine)
可能原因:混浆机搅拌桨磨损,导致浆料分散不均。涂布头堵塞或涂布辊磨损,导致涂层厚度波动。碾压机辊面不平整或压力不稳定,导致极片压实不均。分条刀具钝化或张力控制不当,造成边缘毛刺或机械应力。改进措施:定期维护设备(如搅拌桨更换、涂布头清洁、碾压辊校准)。引入自动涂布厚度监测系统,实时调整涂布参数。优化分条刀具材质(如金刚石涂层),减少切割粉尘。3. 料(Material)
可能原因:粘结剂(如CMC、SBR)比例不足或分散性差。浆料粘度不达标,导致涂布后附着力不足。活性物质(如石墨)与导电剂比例失衡,影响结构稳定性。改进措施:优化浆料配方,增加粘结剂比例或改用高粘结性材料(如PAA)。加强来料检验,确保活性物质粒径分布和导电剂分散性。在混浆后增加浆料粘度及固含量测试,确保一致性。4. 法(Method)
可能原因:混浆工艺参数(搅拌速度、时间)不当,导致浆料团聚。涂布干燥温度过高或时间不足,导致涂层开裂或水分残留。碾压压力过大,破坏极片结构;分条速度过快,产生机械应力。改进措施:通过DOE实验优化混浆、涂布、碾压参数(如梯度干燥工艺)。引入慢速分条工艺,减少切割振动对极片边缘的影响。在碾压后增加极片密度和孔隙率检测,确保压实均匀。5. 测(Measurement)
可能原因:检测频次不足(如涂布厚度仅抽检,未全检)。检测设备未校准(如粘度计、厚度仪误差大)。缺乏对掉粉的量化评估(如未定义单位面积粉尘量标准)。改进措施:在涂布、分条后增设全自动在线检测(如AI视觉检测掉粉区域)。制定粉尘收集量化标准(如用胶带法测试掉粉率)。定期校准测量设备,并保留数据追溯记录。6. 环(Environment)
可能原因:车间湿度过高,导致浆料吸潮或干燥不彻底。温度波动大,影响浆料流平性和粘结剂固化。洁净度不足,环境粉尘污染极片表面。改进措施:控制车间湿度在30%-50%,温度在25±2℃(需根据粘结剂特性调整)。在涂布和分条区域增加局部除尘装置(如离子风机)。定期监测车间洁净度(如ISO 14644标准),避免交叉污染。综合改进方向
跨工序协同优化:例如调整涂布干燥曲线与碾压压力的匹配性。根本原因验证:通过SEM分析掉粉区域微观结构,确认是粘结失效还是机械损伤。快速响应机制:建立前段制程异常与电池压降的关联数据库,实现问题闭环管理。通过系统排查5M1E各环节,可逐步锁定关键因子并制定针对性措施,最终提升负极极片良率,解决电池压降问题。
系统性排查步骤建议
需要考虑如何将每个因素转化为具体的行动步骤。比如,对于“人”,可能需要检查培训记录和操作规范性;“机”可能需要设备维护记录和参数校准;“料”涉及材料检验和配方验证等等。同时,需要结合用户的实际工作环境,步骤要具体可行,可能需要分阶段,比如初步排查、详细分析、根本原因确认、措施实施和预防机制建立。
还要注意逻辑顺序,可能从最可能的原因开始,或者按照生产流程顺序排查。另外,用户可能需要一些工具或方法,比如检查表、数据收集表格、实验设计(DOE)等,来辅助排查过程。需要确保步骤之间有衔接,每个步骤的输出作为下一步的输入,最终形成闭环。
可能还需要考虑时间因素,如何高效地完成排查,避免影响生产进度。同时,要建议用户记录每一步的结果,以便追溯和分析。最后,可能需要综合各步骤的发现,找到根本原因,并制定改进措施,然后验证效果,形成预防机制,防止问题再次发生。
需要注意的是数据采集、现场观察、实验验证、团队协作等内容。此外,要确保建议的步骤符合行业标准和最佳实践,比如ISO标准、SPC控制等。
总结一下,需要构建一个分阶段的系统性排查步骤,覆盖5M1E各个因素,结合生产流程,使用合适的工具和方法,确保全面性和可行性,最终有效解决问题。
以下是针对水系负极掉粉导致电池压降问题的系统性排查步骤建议,结合方法分阶段推进,确保问题彻底闭环:
第一阶段:问题确认与数据收集
1. 现象确认
o 明确掉粉现象的具体表现(如掉粉位置、形态、粉尘量)。
o 关联电池压降不良的具体数据(如电压降幅、发生批次、电芯位置分布)。
2. 初步数据收集
o 收集异常批次的工艺参数记录(混浆时间、涂布速度、碾压压力等)。
o 调取前段制程的检测数据(浆料粘度、涂布厚度、极片密度等)。
o 统计掉粉问题发生的频率(如每卷极片的掉粉点数)。
3. 快速围堵措施
o 隔离异常批次极片,避免流入后续工序。
o 临时增加涂布后目检或胶带法测试,监控掉粉趋势。
第二阶段:分层排查(按5M1E展开)
1. 人(Man)
排查内容:检查操作人员的培训记录及上岗认证状态。现场观察操作是否符合SOP(如混浆加料顺序、涂布参数设置)。确认交接班记录是否存在参数波动或异常调整。工具:操作录像回放、SOP符合性检查表。2. 机(Machine)
排查内容:检查混浆机搅拌桨磨损情况,确认转速稳定性(通过电流曲线分析)。涂布头清洁记录及涂布辊磨损量测数据(如辊面跳动检测)。碾压机压力传感器校准记录及辊面平整度(用塞尺测量间隙)。分条刀具磨损状态及张力控制精度(如张力计实测值 vs 设定值)。工具:设备点检表、维护日志、传感器数据导出分析。3. 料(Material)
排查内容:核对异常批次材料清单(如粘结剂型号、活性物质批次)。复测浆料关键指标:粘度(旋转粘度计)、固含量(烘箱法)。对比正常/异常批次材料微观结构(SEM观察浆料分散性)。工具:来料检验报告、浆料测试记录、第三方材料分析。4. 法(Method)
排查内容:混浆工艺参数是否与配方匹配(如搅拌速度与浆料剪切力关系)。涂布干燥曲线合理性(如温度梯度是否导致表面快速结皮)。碾压压力设定是否超出材料承受极限(通过极片回弹率验证)。分条速度与刀具匹配性(高速分条是否引发边缘应力集中)。工具:DOE实验设计、工艺参数趋势图、极片机械性能测试(如剥离力)。5. 测(Measurement)
排查内容:确认检测设备校准状态(如涂布测厚仪、粘度计)。复核异常批次检测数据(如涂布厚度CPK是否达标)。评估现有检测方法的灵敏度(如目检能否发现微米级掉粉)。工具:MSA(测量系统分析)、第三方设备比对、AI视觉缺陷检测试点。6. 环(Environment)
排查内容:监测车间温湿度记录(是否在粘结剂要求的范围内)。评估涂布/分条区域洁净度(粒子计数器检测粉尘浓度)。检查设备周边振动源(如空压机、风机是否导致极片微裂纹)。工具:温湿度记录仪、洁净度检测报告、振动频谱分析。第三阶段:根因验证与措施制定
1. 关键因子锁定
o 通过鱼骨图/Pareto分析,筛选出前3项潜在主因(如粘结剂比例不足、涂布干燥过快、碾压压力过高)。
2. 实验验证
o 设计小批量验证实验(如调整粘结剂比例±5%、梯度干燥工艺优化)。
o 对比实验组/对照组的掉粉率(胶带法测试)及电池压降数据。
3. 根本原因确认
o 通过SEM观察极片表面形貌,确认掉粉是粘结失效(界面剥离)还是机械损伤(裂纹导致)。
o 结合实验数据,确定主因(如干燥过快导致内应力开裂)。
第四阶段:措施实施与效果监控
1. 短期对策
o 调整关键参数(如降低涂布干燥温度、增加碾压压力分段控制)。
o 在分条工序增加毛刷清洁工位,减少粉尘附着。
2. 长期对策
o 优化浆料配方(引入交联型粘结剂提升附着力)。
o 升级涂布机干燥系统,实现温湿度闭环控制。
3. 效果监控
o 连续跟踪3批次极片掉粉率(目标:≤0.1%)。
o 监控电池压降不良率趋势(SPC控制图)。
第五阶段:标准化与预防
1. 文件更新
o 修订SOP(如明确混浆分散时间、涂布干燥梯度)。
o 将掉粉检测纳入IPQC巡检项目(如每2小时胶带法抽检)。
2. 防错机制
o 在MES系统中设置参数互锁(如涂布速度与干燥温度关联控制)。
o 关键设备加装传感器报警(如混浆机电流超限自动停机)。
3. 经验固化
o 将案例纳入FMEA库,更新潜在失效模式风险系数(RPN)。
o 开展跨部门分享会,提升团队对前段工艺-电池性能关联的认知。
排查工具推荐
数据分析:Minitab(CPK/DOE分析)、Python(工艺参数趋势预测)。微观检测:SEM/EDS(极片表面成分分析)、XRD(晶体结构验证)。在线监控:AI视觉检测系统(实时识别掉粉缺陷)。通过以上系统性排查,可逐步缩小问题范围,精准定位根因,最终实现工艺稳定性提升和电池压降问题的根治。