订单准时交付率是生产计划管理中一个非常重要的指标,这个指标的计算方法也是一个非常简单的数学运算,公式为:订单准时交付率 = (按时交付的订单数量 / 总订单数量) × 100%。这个指标直观反映了企业在生产计划执行方面的效率和能力。
一个高的准时交付率意味着工厂能够有效地管理供应链,减少生产延迟,从而提升客户满意度。反之,若准时交付率低下,则可能意味着存在生产计划不合理、物料供应不稳定等问题,需要工厂及时进行调整和改进。 因此,持续优化生产计划并提高订单准时交付率,是确保工厂稳定发展的关键要素。然而,值得注意的是,在追求这一目标的过程中,有时可能会矫枉过正。过度强调提升订单准时交付率,可能导致在一定程度上牺牲工厂管理的其他重要指标,其中尤为突出的就是库存周转率。这意味着,在寻求平衡与效率提升时,工厂应兼顾多个运营指标,实现综合优化,而非单纯片面地追求某一项指标的提升。
应当如何在确保订单准时交付的前提下,恰当地设定相关的库存指标呢?鉴于不同的工厂制造模式各异,下面将以离散型制造工厂为例,探讨一下适宜的库存设置策略。
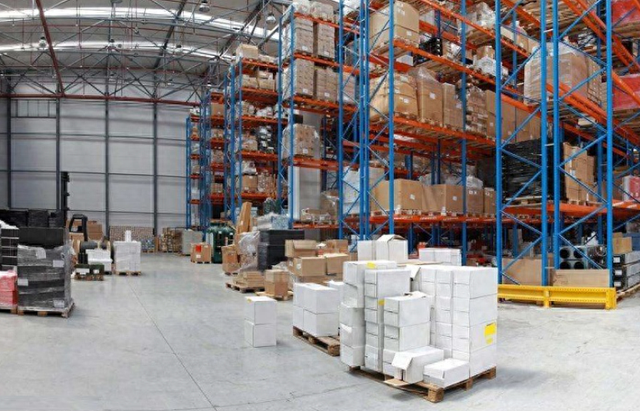
以工厂成品每月销售出库金额为基础来估算总体库存价值,这一计算方法涵盖了成品库存、半成品库存以及原料库存三个部分,尽管这种方法较为粗略,但它确立的目标直观明了。假定工厂在一个自然月内的成品销售总额为100万元,若按照库存控制要求维持45天的供应量,则对应的库存金额理论上应为150万元。也就是说,如果库存总金额超过了200万元,这就意味着物料的实际库存天数可能达到了大约60天。
这种方法的不足之处同样显著,因为它未能充分考量制造流程中的工艺限制和物料制约等因素。例如,由于生产工艺瓶颈的存在,可能导致需要提前准备一定的生产库存;另外,某些特定零部件的采购前置周期可能长达60天之久,也会造成库存增加。这些实际情况并未被该计算方法充分纳入考量范围。
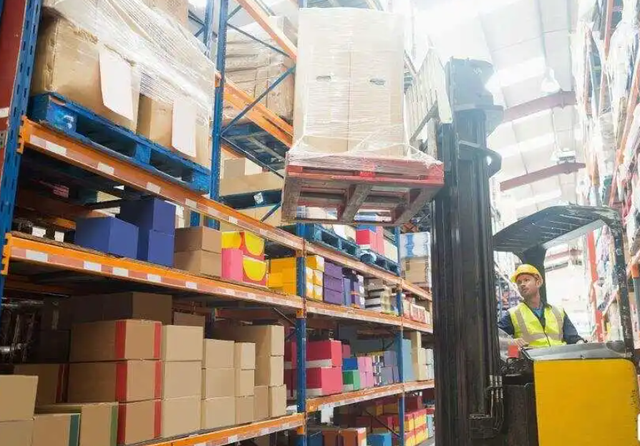
根据约束理论中对于瓶颈的观点:瓶颈被视为系统中限制整体性能的关键因素。系统的产出速度和产出量不是由所有环节的平均性能决定的,而是取决于这个瓶颈环节。因此,管理的重点应该放在寻找并消除这些瓶颈环节上,以实现系统的整体优化。
因此,在库存设定方面,应以工艺路线为基础,识别并关注相关瓶颈环节,将瓶颈工序的库存作为核心KPI进行考核与管控。而对于非瓶颈物料,则应采取严格的库存限制措施,因为不必要的生产会导致库存积压,这正是精益生产理论中所指出的七大浪费现象之一——过量生产的典型表现。一旦生产出超过当前需求的产品,不仅会增加库存成本,还可能导致资源的无效利用,故应力求避免此类浪费的发生。
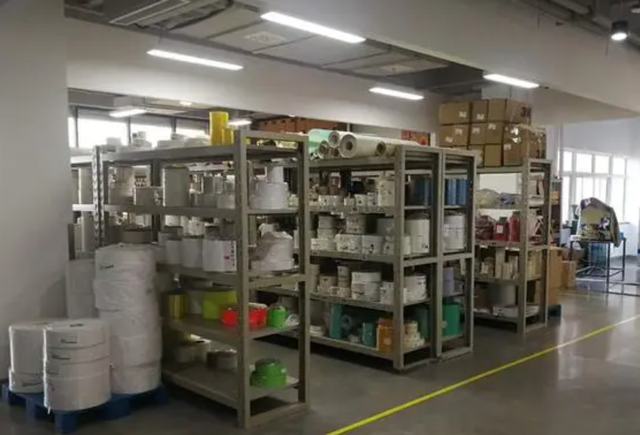
我们可以从信息化系统中获取过去12个月的库存周转天数以及各类产品、半成品和原料的平均月度库存金额,以此数据为基础来设定库存指标。在确定这些库存指标时,应采取系统数据与实际状况相结合的方式。这是因为,部分系统的库龄计算可能会因一些财务操作的影响而不完全准确,导致数据失真。特别是以下操作:
物料在不同的仓库之间频繁调拨;物料在月底集中不入库,月初集中入库;物料在某些时间点退库(退供应商、退车间再入库)仓库杂项进出,平账等操作;入库不及时等账务及时率问题;经过对历史数据的详尽分析与综合评估后,我们可以通过取历史数据中位值并乘以一定调整系数(例如1.2或1.3)的方式来制定库存指标。相较于上述两种方法,这种做法具有更显著的优势,因为它是在充分考虑现有状况的基础上,结合对未来目标的预期而做出的决策,更具备针对性和前瞻性。
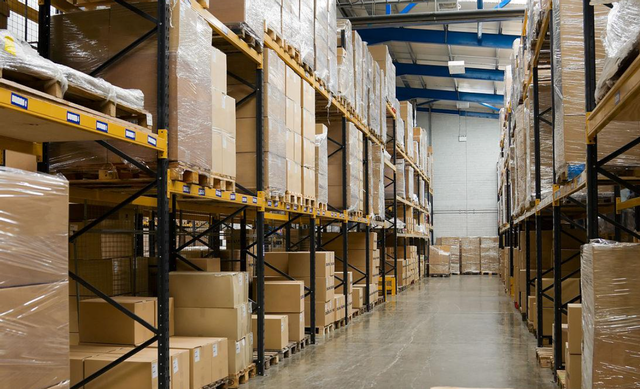
工厂不应仅将订单准时交付率视为唯一的绩效考核指标,过于侧重这一指标可能会导致虽然表面上完成了目标,但同时伴随着库存水平的攀升。一旦库存过高,后续的削减工作将变得尤为艰难,原因在于整个管理团队很可能已经适应了高库存运营模式,习惯了在生产制造过程中原料库存充足无虞的状态。在这种情况下,打破高库存的固有习惯并回归精益管理,无疑是一项颇具挑战的任务。
因此,在优先保证订单准时交付的核心原则下,工厂管理层应尽早与各个相关部门紧密合作,共同研讨并科学制定出一套符合实际生产情况且高效的库存控制标准。此举的长远目的是迅速且显著地优化整体工厂运营状态,包括但不限于生产节奏、物料流动性和资金利用率等方面。通过精细化管理库存,能够精准拿捏订单准时交付与合理库存控制之间的微妙关系,最终达成二者间的最佳协同效应,使工厂在市场竞争中取得高效、稳定且可持续的发展优势。
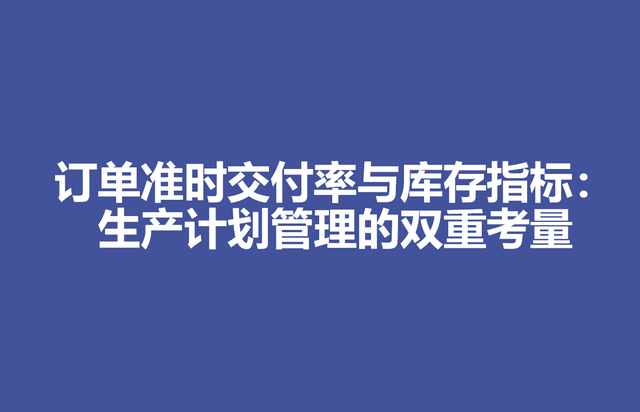
我是古哥计划,专注生产计划18年,头条号作者,职场问答专家,优质职场领域创作者。关注我,每天学习PMC相关知识。