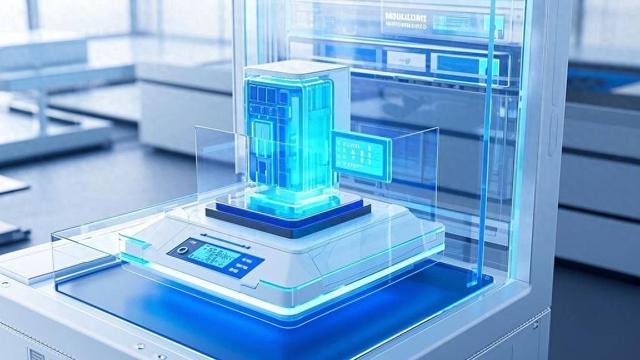
一、从台账管理到智能中枢的范式迁移
工业革命的历史本质上是一部设备管理技术的演进史。从蒸汽机时代的机械维护手册,到电气时代的预防性维保体系,再到数字时代的预测性维护系统,设备管理始终是生产效能的基石。当前,随着工业4.0与智能制造战略的推进,设备管理系统(Equipment Management System, EMS)正经历着从单一功能工具向智能中枢的质变。
根据Gartner 2023年工业物联网报告显示,全球85%的制造企业已部署或正在升级智能设备管理系统,其中62%的企业将系统升级与数字化转型战略深度绑定。这种变革不仅体现在技术架构层面,更引发了企业组织架构、运维模式的深层重构。
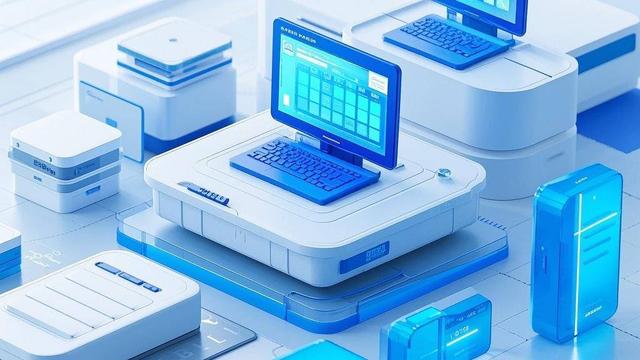
二、技术驱动的系统功能革命
1.IoT与5G赋能的实时感知网络
现代EMS通过工业物联网传感器集群实现设备状态全维度采集,某汽车零部件工厂部署的振动监测系统,将数据采集频率从传统人工巡检的4次/天提升至每秒2000次,异常识别准确率提高40%。5G+TSN(时间敏感网络)技术则解决了海量数据传输的时延问题,在半导体行业,晶圆加工设备的控制指令传输时延已压缩至1毫秒级。
2.AI算法重构决策逻辑
深度学习模型正在改变传统维护策略,某风电集团采用设备寿命预测算法后,叶片故障预警提前期从72小时延伸至30天,运维成本下降28%。更值得关注的是强化学习在参数优化中的应用,某化工厂通过实时工艺参数动态调整,使反应釜能效提升12%,每年减少碳排放1500吨。
3.数字孪生构建闭环管理体系
数字孪生体(Digital Twin)实现了物理设备与虚拟模型的实时映射,波音公司为飞机引擎构建的孪生模型,可同步模拟3.5万个零部件的磨损状态。这种虚实交互使设备管理从被动响应转向主动优化,某智能电网企业通过数字孪生仿真,将变电站故障处置效率提升60%。

三、行业级应用图谱分析
1.离散制造场景的柔性适配
在汽车制造领域,EMS与MES系统的深度集成催生出新型管理模式。特斯拉柏林工厂的设备管理系统可动态调整焊接机器人工作参数,支持8款车型的混线生产,产线切换时间缩短至22分钟,设备综合效率(OEE)达到92%的行业标杆水平。
2.流程工业的能效革命
石油炼化企业通过设备管理系统实现能源流全景监控,中石化某炼厂将加热炉热效率从89%提升至93%,相当于年节省标准煤1.2万吨。系统集成的APC(先进过程控制)模块,使催化裂化装置产品收率波动范围收窄至±0.15%。
3.医疗设备的精准运维
三级医院设备管理系统已集成AIoT技术,某三甲医院的MRI设备通过振动频谱分析,提前37天预警冷却系统故障,避免价值千万的设备损坏。系统自动生成的PM(预防性维护)工单执行率达到98%,较传统模式提升45%。
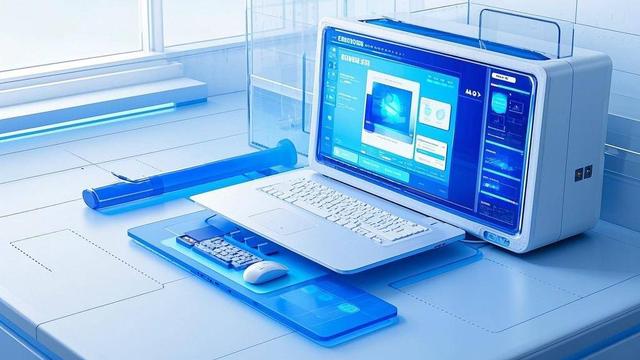
四、实施过程中的关键挑战
1.数据治理的复杂性
工业设备产生的多源异构数据(时序数据、图像、音频等)对系统提出新要求,某钢铁集团设备管理系统初期因数据标准不统一,导致20%的传感器数据无法有效利用。建立符合ISO 55000标准的数据治理体系成为必要基础。
2.组织变革的阵痛期
传统"设备科-生产部"的条块分割模式难以适应智能系统需求,某家电企业实施EMS时遭遇部门数据壁垒,通过设立CDO(首席数据官)岗位,构建跨部门设备数据中台,才实现系统价值释放。
3.安全防护的升级压力
工业设备联网率提升带来新的攻击面,某水厂SCADA系统曾因PLC漏洞导致停产事故。当前领先的EMS已集成零信任架构,采用设备指纹识别、流量基线分析等技术,将安全事件响应时间压缩至8分钟内。

五、下一代系统演进方向
1.自主决策系统(ADS)的突破
边缘计算与联邦学习的结合,推动设备管理向自主决策演进。西门子正在测试的自主维护机器人,可在本地完成98%的故障诊断决策,仅将关键数据回传云端,实现"决策下沉"。
2.生态化服务平台崛起
设备制造商、系统开发商、运维服务商正在构建价值网络,三一重工的根云平台已接入68万台高价值设备,形成从设备监控到备件供应链的完整生态,客户设备利用率提升30%。
3.可持续性成为核心指标
新一代EMS开始集成碳足迹追踪模块,施耐德电气的EcoStruxure系统可自动计算设备能耗碳排,并给出能效优化方案,助力企业达成ESG目标。
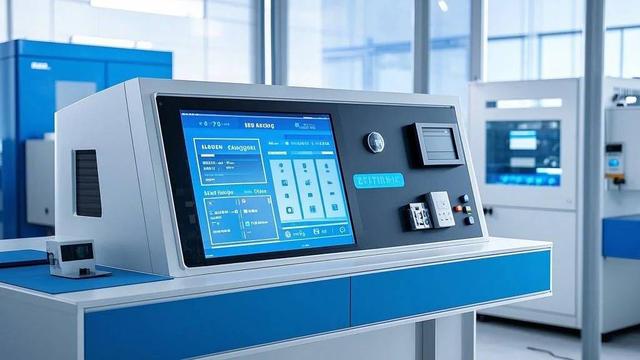
六、结语
设备管理系统的进化折射出工业文明的升级路径。当管理系统从辅助工具进化为生产力核心要素时,企业需要以战略视角重构设备管理体系。未来的竞争,本质上是设备管理能力的竞争——这不仅关乎效率提升,更是智能制造时代的生存法则。那些率先完成设备管理系统智能化转型的企业,将在新一轮工业革命中掌握价值创造的密钥。