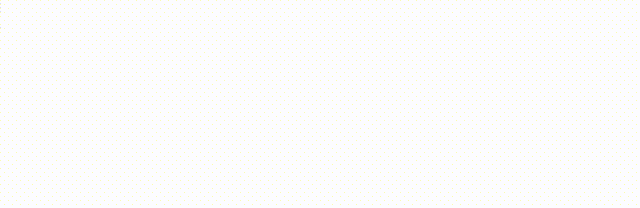
文|煮酒
编辑|煮酒
引言一直以来,铝基复合材料因其优异的力学性能和结构设计自由度,在轻量化和高性能结构方面展现出巨大应用前景,受到无数专业人士的关注。
在各类金属基复合材料中,铝基复合材料以其低密度、高比强度的特点,成为实现结构轻量化的重要材料之一。
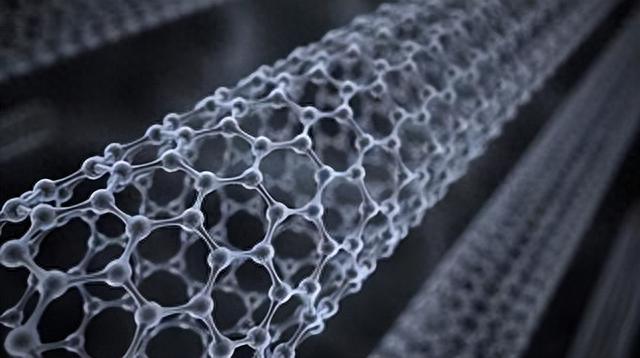
然而,界面的结合强度是制约铝基复合材料进一步推广应用的关键因素,进而使得其应用场景受到极大的限制。
近年来,轧粘技术作为一种新型铝基复合板材制备方法受到广泛关注。
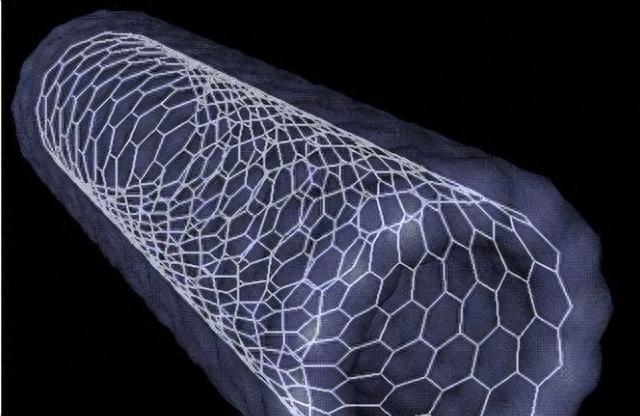
该技术可在较低温度下实现不同铝基材料的组合。研究表明,轧粘过程中,表面氧化物的破碎及残留会降低界面结合强度。此外,轧粘前的热处理虽可提高复合材料的界面强度,但其强化机制还不明确。
原料近表区显微组织探究在1℃下浸泡单侧加工的双辊铸造带产生的晶粒微观结构如图所示。
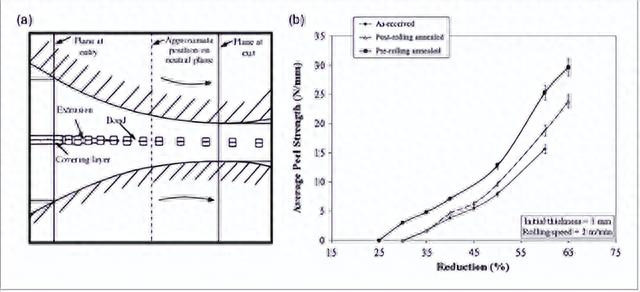
热处理导致近表区域(用黑色方块标记)出现可见的微观结构演变,但在中心区域则不然,这是双辊铸造材料的典型特征。与双辊铸造一样,带材中心的温度高于表面附近的区域,中心区域受到更强烈的压力。
而近表区域以相对较低的应变进行加工硬化,这表明这些区域的硬度较高。由于以低应变进行加工硬化,在随后的退火过程中,在表面附近形成了粗晶粒。
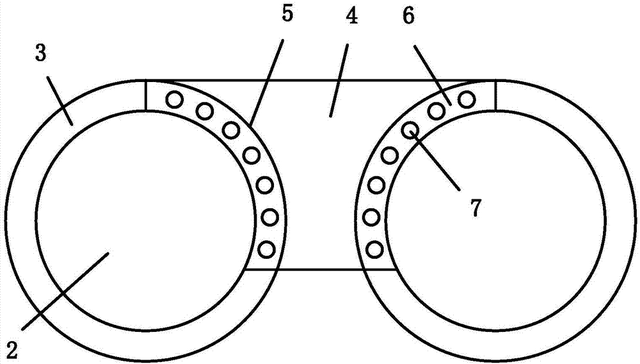
如果在热处理之前从两侧铣削加工硬化层,则会形成M2A400状态的细晶近表面区域。冷轧结合45℃浸泡400分钟,导致整个板材横截面在CRA400状态下重结晶。初始位错密度的不均匀分布(通过冷轧进一步增加)导致形成不同尺寸的晶粒。
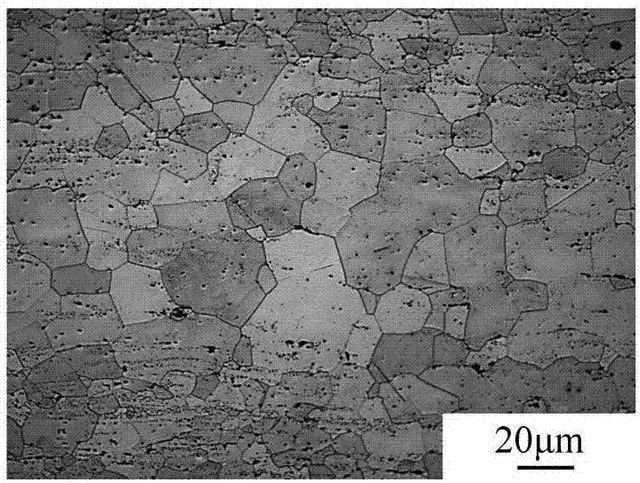
在近表区域可以看到更细的晶粒,因为那里较高的位错密度在重结晶过程中产生了许多新晶粒的原子核。
这些区域已经在双辊铸造过程中进行了加工硬化,这一观察结果与以前的研究相吻合。 较高的温度也增加了冷轧样品的平均晶粒尺寸,其中晶粒生长最强的是板芯。
相比之下,近表区域的微观结构几乎不受从400℃到520℃的温度升高的影响,表给出了所有样品近表区域平均晶粒尺寸的定量值。
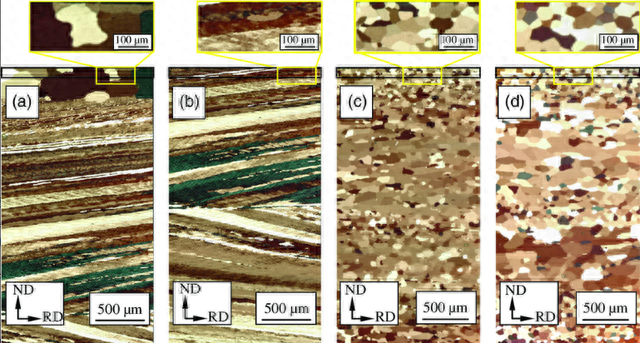
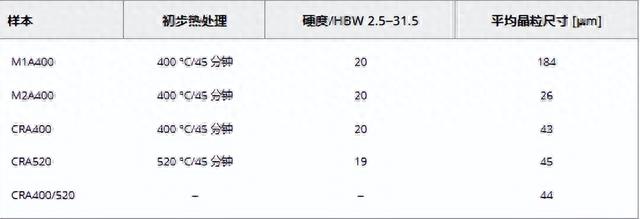
如上图所示,CRA400和CRA520状态的硬度和近表面晶粒尺寸值几乎相同;差异与所用实验方法的准确性相当。
出于这个原因,在近表区域分离了平均晶粒尺寸为400μm的附加熔融CRA520/44状态。此外,图显示了当原材料近表区域的晶粒尺寸增加时,温热的轧粘铝板的剥离强度如何变化。
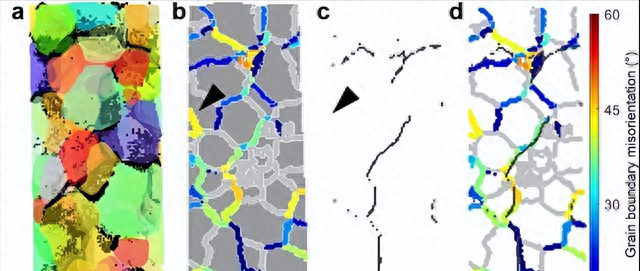
晶粒尺寸为26μm时,剥离强度为3.7nmm(M2A400-O)和5.3nmm(M2A400-W)适用于没有和有后热处理。通过将晶粒尺寸增加到44μm,包层的剥离强度提高到8.7nmm(CRA400/520-O)和12.6nmm((CRA400/520-W)。进一步粗化至184μm的晶粒导致剥离强度降低至6.9nmm不带后热处理(M1A400-O),增加到14.4nmm一个(M1A400–W)。
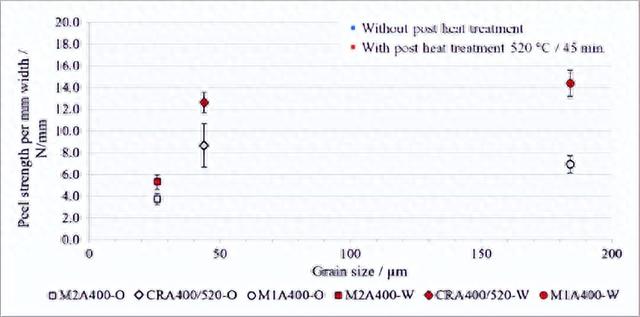
随着晶粒尺寸的增加,未经后热处理制造的样品的比分层能量上升到44μm的晶粒尺寸,之后减小。然而,在这种情况下,比分层能量非常低。
特别是晶粒尺寸为26μm时,复合材料在短时间加载后分层。由于包层界面区的晶粒较粗,粘结强度显著提高。例如,当晶粒尺寸从26μm变为44μm时,比分层能量从0.012增加到0.109Jmm无需后热处理。
相比之下,经过额外热处理的样品的比分层能量从0.0825上升到0.214Jmm在晶粒尺寸为184μm时,比分层能量降低到0.031Jmm(M1A400-O)不进行后热处理,增加到0.281Jmm(M1A400-W)。
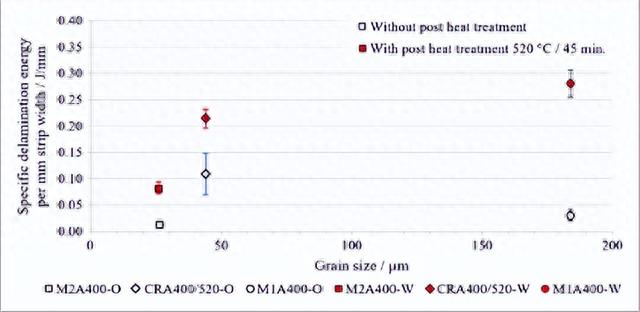
近表面晶粒从26μm扩大到44μm也增加了必要的最大剥离力,而进一步粗化到184μm的晶粒减小了剥离力。它们从13.8(M2A400-O)上升到35.4nmm(CRA400/520-O),然后下降到26.6nmm(M1A400-O)。
而后热处理将所需的最大剥离力值降低到11.7nmm(M2A400-W),27.1(CRA400/520-W)和24.9nmm(M1A400-W)。图表的所有值和偏差都列在表中。
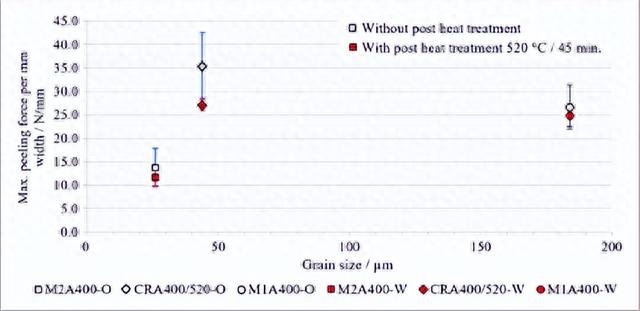
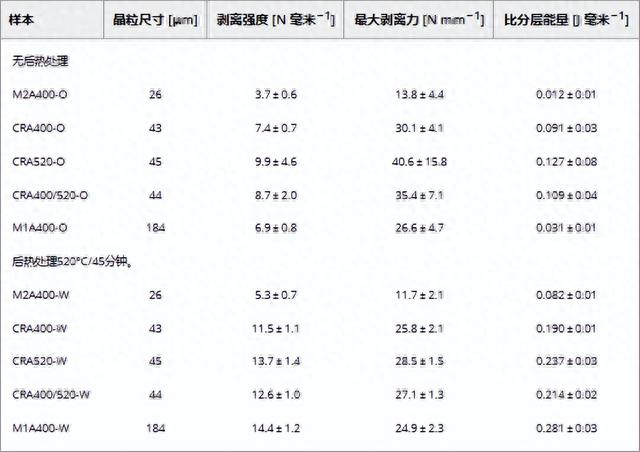
以下是CRA420和CRA520状态的比较。
尽管对原料初始状态的表征显示出很强的相似性,但对温轧粘合包层的分析显示其粘合强度存在明显差异。由于各种初步热处理,在CRA520状态的较高浸泡温度下,剥离强度值增加,其中近表面晶粒尺寸仅略有变化,比分层能量也显著增加,最大剥离力也显著增加。
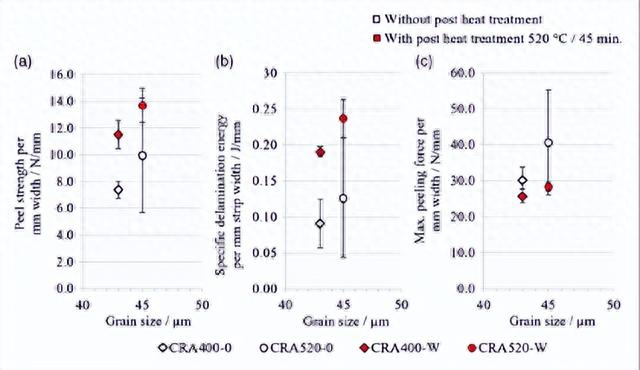
图显示了CRA400和CRA520状态下样品近表区域的相应FIB切片图像。重点是在白色圆圈标记的区域形成氧化铝层。应该注意的是,氧化层的厚度不同。由于材料表面的热负荷较高,CRA520状态比CRA400状态形成更厚且部分多孔的氧化层。近表区域的EDS证实了这一发现。
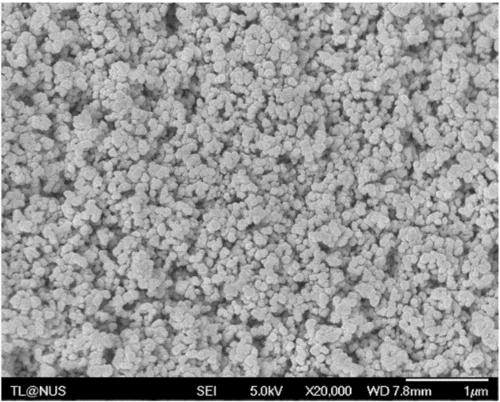
在铝浓度较高的切割区域和氧含量较高的表面积之间,可以看到具有两种元素混合物包围的氧化层。
与CRA520状态相比,它在CRA400状态下更厚,并且在原料中含有更多的孔。沿白线进行的额外定量EDS测量支持了这一观察结果,CRA520样品层中的氧浓度为29.41%,而CRA11状态为37.400%。图a,b中图像下部显示的更清晰的层应理解为FIB过程中的沉积物。
SEM分形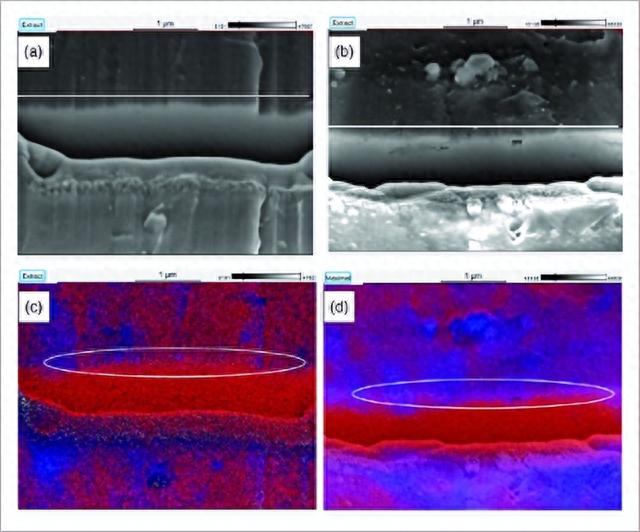
除了轧粘合的平坦区域外,分层表面的所有SEM芽在剥离方向上都显示出细长的凹凸和凹陷。凹凸和凹陷代表了包层之间以前的局部金属键区域。剥离导致铝包层出现许多内聚韧性断裂,在SEM图像上可见为明亮的高程(图b中的标记A)。
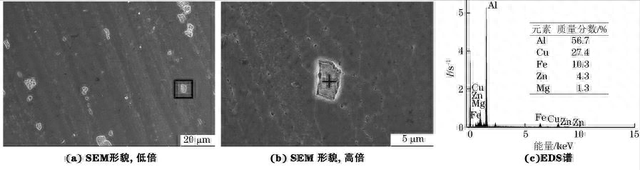
在与延性断裂相邻的平坦区域,铝层之间没有发生金属结合。图a,b显示了M2A400-O状态的断裂表面,其晶粒尺寸在辊合前最小,为26μm。图像显示了具有先前金属键的较大区域以及具有很少和弱形成连接的区。相比之下,近表面晶粒尺寸为400μm的CRA9-O状态具有均匀分布的图案特征,用于整个分离平面上的内聚性韧性断裂。
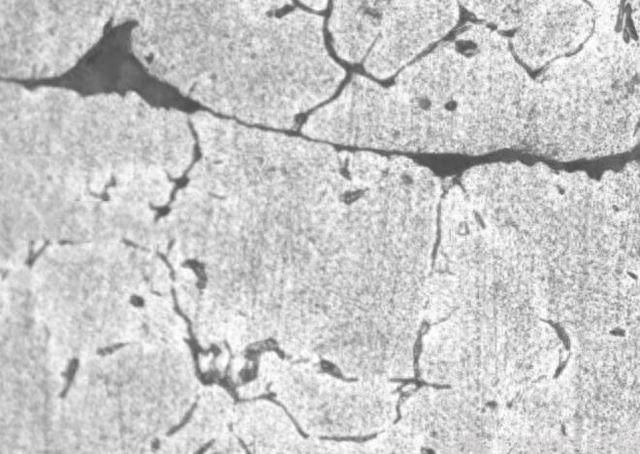
在CRA45-O状态的原料中晶粒尺寸稍大的520μm的前界面,确定了大塑性变形区域和其他较小变形区域之间的放大倍数。由于晶粒从26μm扩大到45μm,在轧粘过程中,表面上金属键的密度增加,到达到峰值。
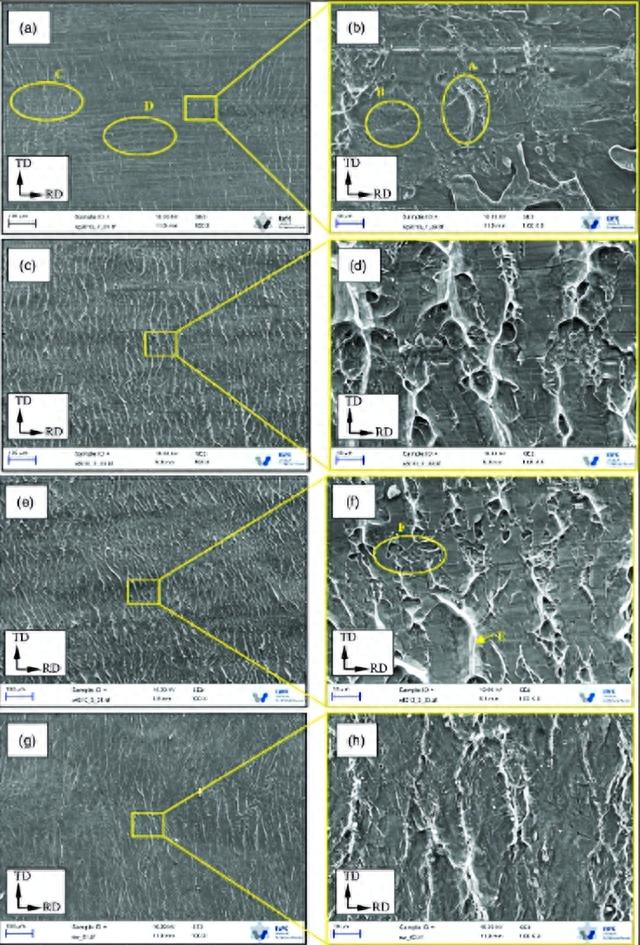
随后,进一步粗化至184μm的晶粒导致键变弱,如M1A400-O状态所示。与先前分层试样相比,退火后铝包层在相同的近表面晶粒尺寸下显示出更多的粘性韧性断裂区域。
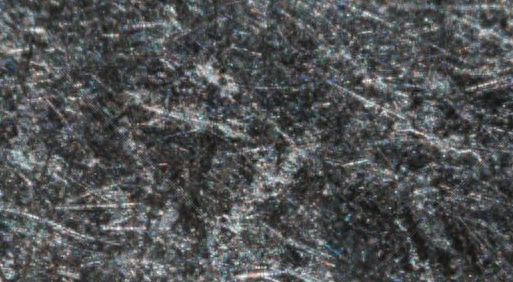
此外,表面显示出具有较大晶粒的包层之间金属键合的频率更高。即使在26μm的晶粒尺寸下,也可以看到更大面积的微观小金属键。在晶粒尺寸为43和45μm和184μm处发现粘性韧性断裂区域的数量最多。
对以上现象的思考与讨论剥离测试的评估显示,在拉动开始时剥离力强烈增加,当达到最大剥离力时,这导致包层的第一次微观分层。在测试中,测得的剥离力最大值总是比计算的剥离强度高出约2倍。
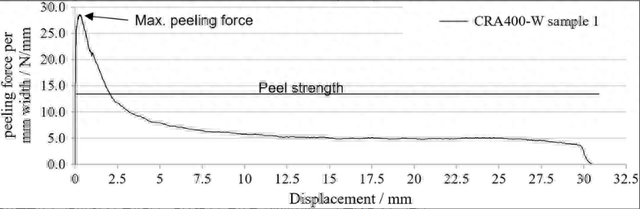
开始时,在包层的分离面中引起法向应力,使缺口变形,并导致裂纹尖端前方生长出塑性区域。开裂随之而来,剥离力降低。结果,它的峰值是短暂的时刻,就在粘合的第一次微观失效之前。因此,峰值取决于部件几何形状、缺口几何形状、应力状态和微观结构。
相比之下,剥离强度是整个样品长度上剥离力函数的平均值。在连续的裂纹扩展过程中,即塑性区域沿界面的运动直到复合层之间的粘合失败。
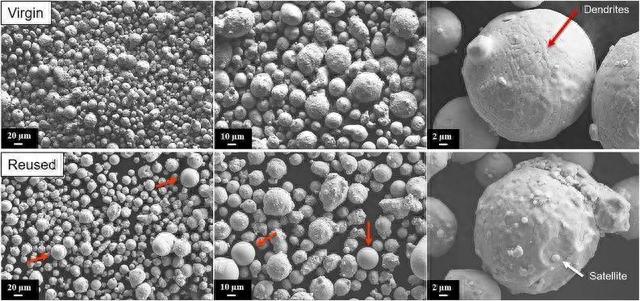
半成品的不同粒度对剥落测试有显著影响。剥离强度与晶粒尺寸类似地增加,直至缓慢减小。通过在热轧粘合之前将晶粒尺寸从26μm(M2A400-O状态)增加到44μm(CRA400/520-O状态),剥离强度增加,相当于增加约+135%。
晶粒尺寸最大为184μm的复合材料表现出倾斜剥离强度。这些结果包括未经过后热处理的样品。相应样品的断裂表面分析得出的结论是,近表面晶粒尺寸为26μm(M2A400–O)的样品比晶粒较粗的样品具有更少的微观金属键。
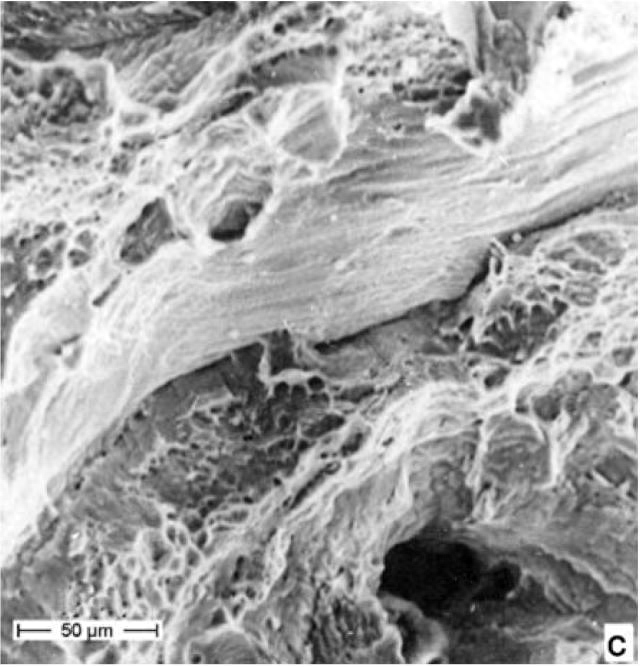
此外,还有更大的区域没有微连接。这些事实表明,对于晶粒为26μm的铝原料,在温轧粘合过程中界面氧化层中发生的裂纹较少,这对于幼年表面的产生是必要的。因此,金属键较少,导致M2A400-O状态的剥离强度较低。
相比之下,在晶粒尺寸为44μm(CRA400/520-O状态)时,在分层表面上可以看到更具粘性的延性断裂区域,其宽度、分支和长度要大得多。
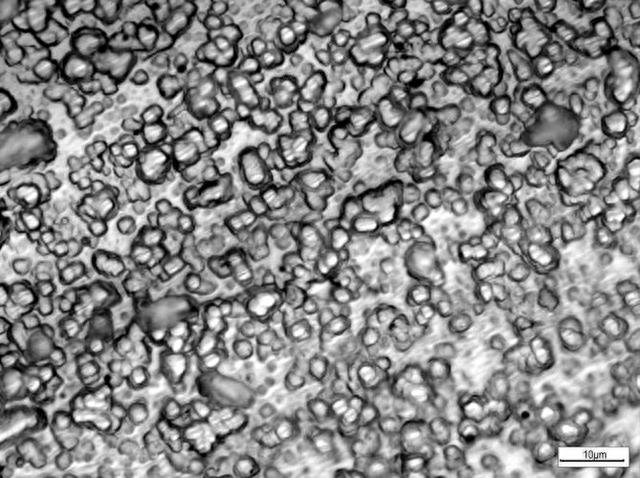
CRA400/520-O状态的剥离强度较高,这可以通过金属键数量的增加来解释。结果,最大剥离力随着晶粒尺寸的增加而增加,从而提高了复合材料的抗裂性。
与此同时研究还显示,就特定的分层能量而言,近表面晶粒尺寸达到峰值,因为它在M184A1-O状态的非常粗糙的400μm晶粒中下降。
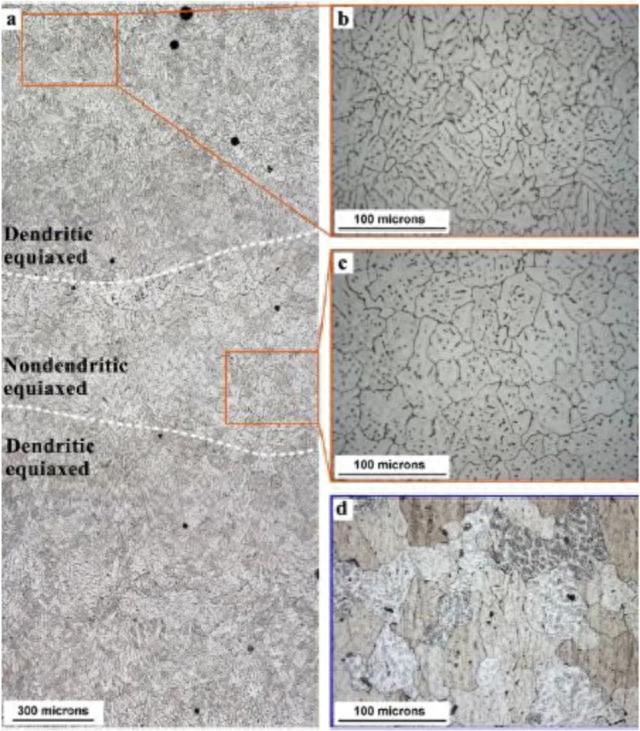
CRA520和CRA7状态的比较显示出非常不同的键强度,它们的晶粒尺寸差异为43和45μm,仅略有不同。
近表区域的FIB调查表明,CRA520状态表现出明显高于CRA400状态的剥离强度,在温轧粘合之前也具有更大的氧化铝层。
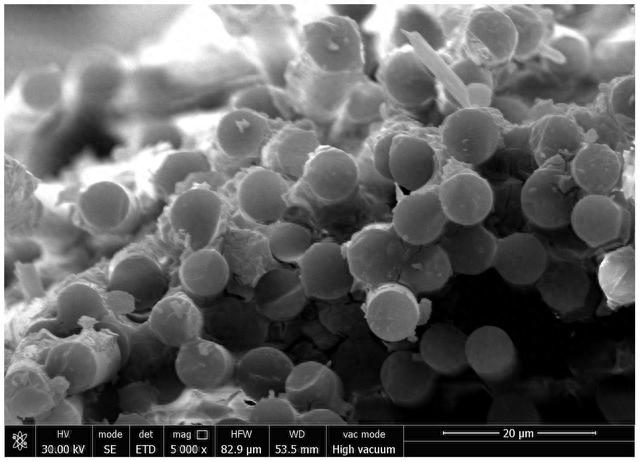
关于铝成型的文献描述了由于轧制力而导致较厚的氧化层开裂的敏感性更高。因此,在界面区域产生幼年表面和形成原子键具有有利条件。然而,在轧粘之前,界面上较厚的氧化层导致复合材料的剥离强度偏差更高,因为它从CRA400-O状态增加到CRA520-O状态。
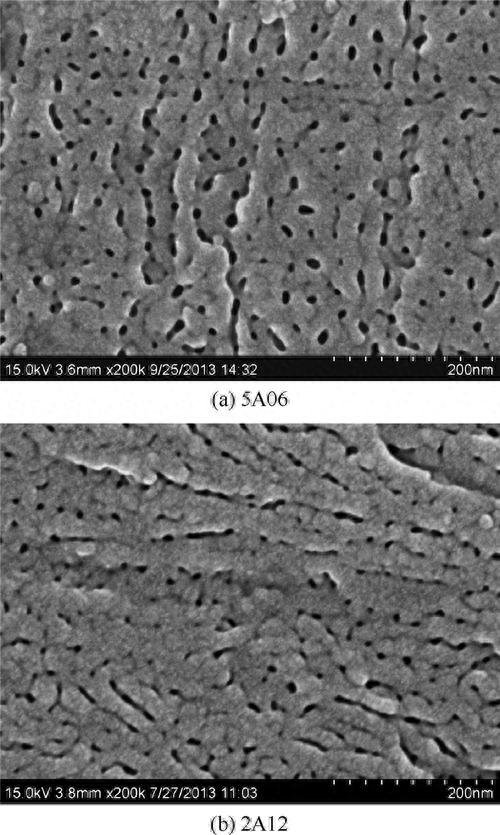
剥离测试后分离平面的破裂图证实,与CRA520-W状态相比,粗糙度和凹坑在CRA520-O样品的断裂表面上分布不均匀。这与较高的剥离强度偏差相关。
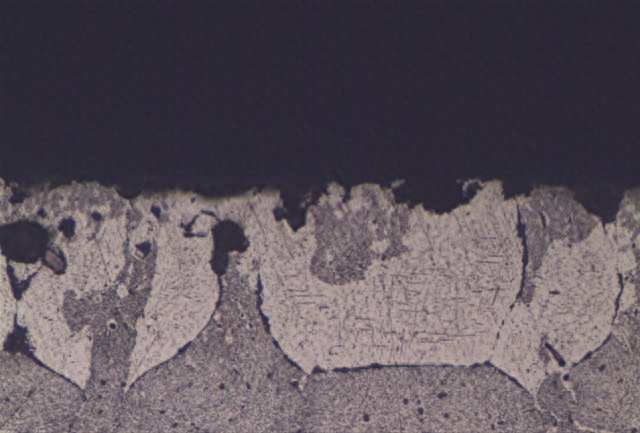
例如,对于26μm的近表面晶粒尺寸,剥离强度从M2A400-O状态增加到M2A400-W状态。比分层能量也从M2A400-O状态增加到M2A400-W状态。
对断裂表面的分析也证实了整个样品长度上粘合强度的显着增加。在M2A400–O状态下,仅发现细小且弥散分布的粘性韧性断裂区域,表明粘合较弱。
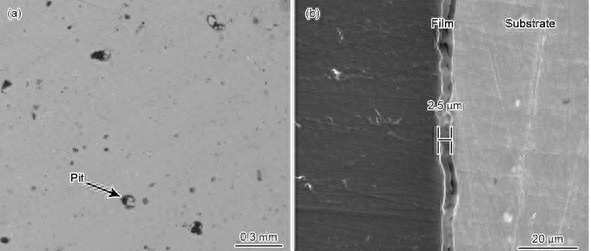
另一方面,后处理样品M2A400-W显示出更高的粘性断裂区密度,这与更高的比分层能和剥离强度相对应。这表明有更强的结合。
将原料的晶粒扩大到44μm,使得未退火和后热处理样品之间的剥离强度增加更大,因为它从CRA400/520-O状态增加到CRA400/520-W状态。
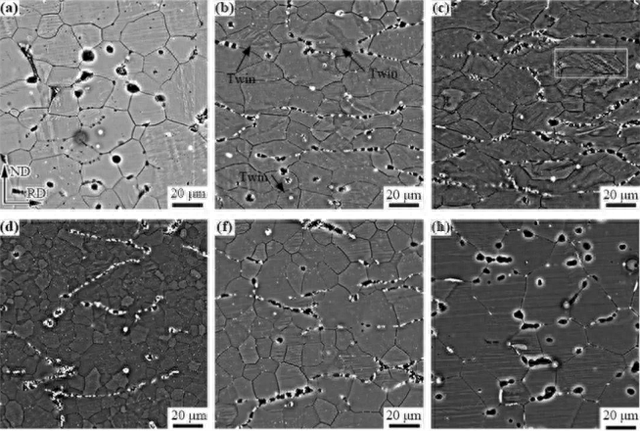
这是由于界面上具有更多幼年表面的扩散条件得到改善。然而,对于最初最粗糙的近表面晶粒为184μm的样品,剥离强度和比分层能量的增加最高。前者从M109A1-O增加到M400A1-W增加了+400%。因此,后热处理后,具有最粗糙的近表面组织温轧键具有最佳的剥离强度和比分层能。
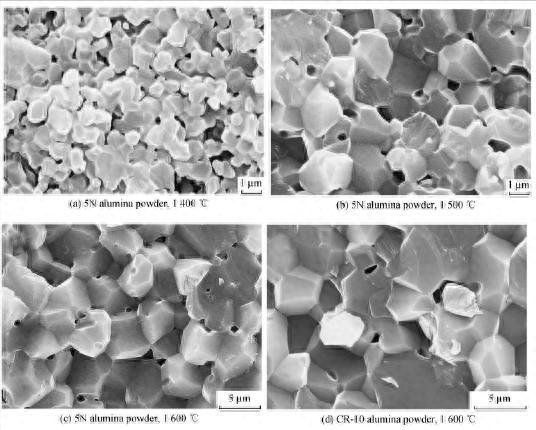
与剥离强度和特定分层能量相反,后热处理降低了最大剥离力,这也降低了材料强度。这导致应力强度因子的阈值较低,表明裂纹萌生。
较粗的近表面键的剥离强度增加到一定点的假设原因是晶粒旋转增强。众所周知,材料的延展性取决于它们的晶粒尺寸。颗粒较粗的那些通常具有较低的延展性。这是因为与晶粒尺寸较小的材料相比,具有较粗晶粒的材料不太可能具有位错滑移平面有利于剪切应力的晶粒。
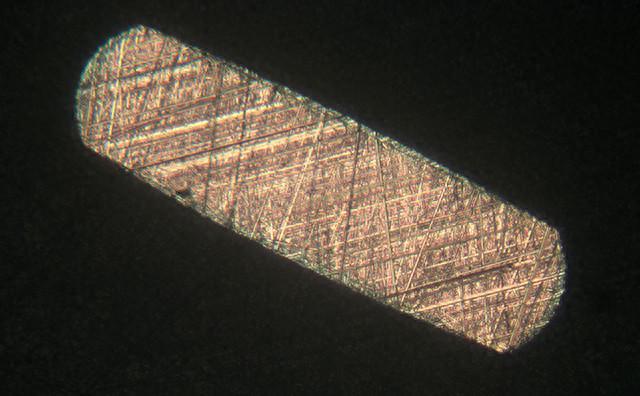
因此,在加载过程中可以激活的滑动平面较少,导致较大的晶粒旋转,直到它们对位错滑动有利。这表明在轧粘过程中,较粗的晶粒对铝原料界面处的氧化层损伤更大,因为晶粒旋转的概率更高。
随后,铝可以流入裂缝中,这增加了包层之间的金属键的数量。然而,必须考虑晶粒尺寸峰值,超过该峰值,晶粒进一步粗化会导致粘结强度减弱。
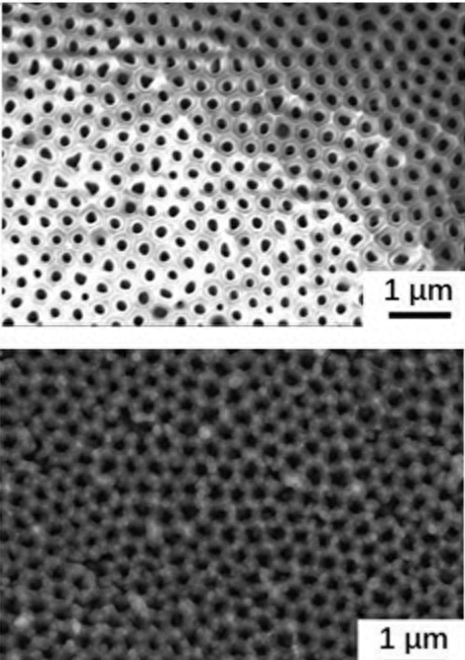
众所周知,沿晶界的扩散比通过晶粒的扩散要快得多。因此,随着晶粒的进一步粗化,沿界面的晶界数量变小,扩散效果降低。这导致剥离强度在近表面晶粒尺寸的阈值以上确定下降。
为了在辊压键合层之间实现最佳粘合强度,必须考虑促进氧化层破裂和增加扩散路径数量的两种效应之间的相互作用。后者还受到额外热处理的青睐,这导致具有最粗糙近表面晶粒的双辊浇注原料具有更高的剥离强度和特定的分层能量。
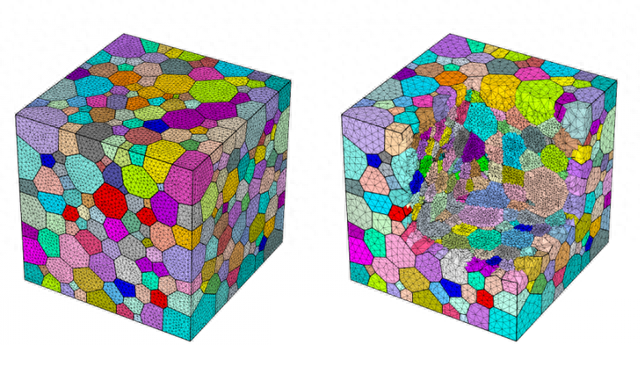
综上所述,本研究系统地研究了原材料近表面区域的微观结构对铝基复合材料界面结合强度的影响规律。研究结果表明:原材料的晶粒尺寸和表面氧化层对复合材料的剥离强度和断裂能量有显著影响。初始晶粒尺寸为44μm时出现剥离强度峰值。
进行复合材料制备后的热处理可明显提升界面结合强度,这是由于热处理促进了扩散效应、再结晶和晶粒生长所致。与无热处理组相比,热处理组的剥离强度提高了43%~109%。
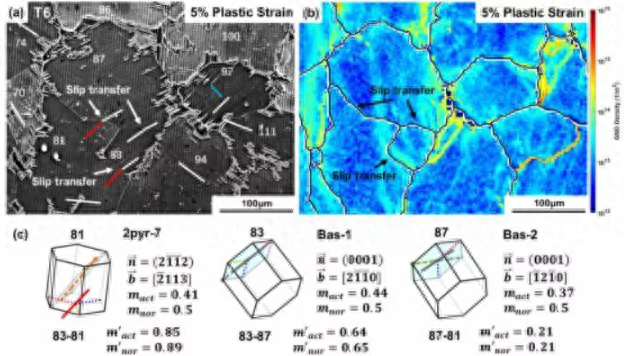
原材料表面氧化程度越深,也有利于提高复合材料的界面结合力。这可能是氧化层的机械扣锁作用所致。
综合两方面因素分析,初始晶粒较粗大的原材料经复合制备后进行热处理,可获得界面结合强度最高的复合材料。
参考文献:1C. Schlögl, C. Planitzer, O. Harrer, B. Buchmayr, Berg- Huettenmaenn. Monatsh. 2011, 156, 249–254.
2L. Long, K. Nagai, F. Yin, Sci. Technol. Adv. Mater. 2008, 9, 23001.
3I. Kaur, Y. Mishin, W. Gust, Fundamentals of Grain and Interphase Boundary Diffusion, Vol. 3, Wiley, Chichester 1995, pp. 32–34.