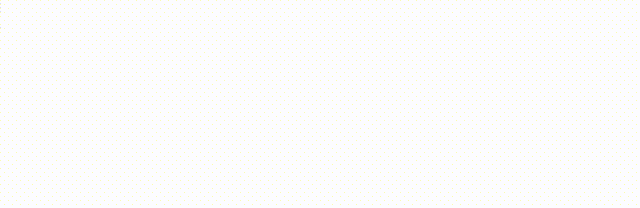
图|煮酒
编辑|煮酒
前言在钢铁冶金过程中,钢液与铸造用耐火材料发生复杂的界面反应,不仅影响产品质量,也导致过滤器寿命缩短。
当前关于钢液与碳结合氧化铝反应机理的研究结论存在分歧,而界面形成的原位氧化层对过滤性能产生重要影响的机理尚不明确。
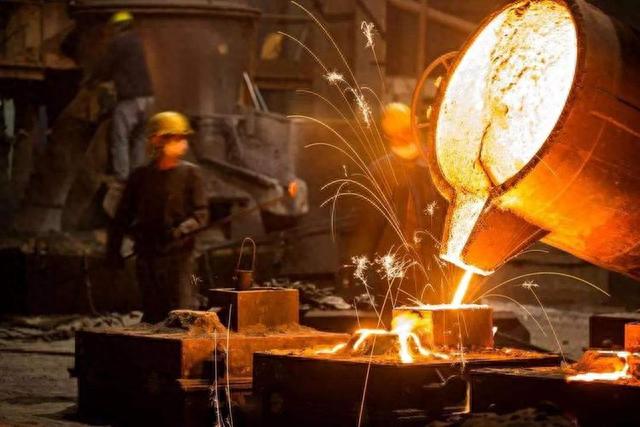
因此,开展关于钢液与碳氧化铝复合耐火材料间反应行为及生成氧化层微观机制的研究,对优化钢铁冶炼工艺具有重要意义。
钢坩埚系统氧化参比钢熔体的氧和碳含量的随时间变化如图所示。结果发现,熔体中的溶解氧量在70s内从30ppm减少到≈8300ppm。有趣的是,在4700ppm氧气下40s后形成平台≈2300s,然后氧含量进一步降低。

直到平台期,氧气损失率几乎恒定,每小时25ppm。在实验过程中,钢中的溶解碳量从1.46%减少到1.15%。可以假设一氧化碳是在实验过程中形成的,即使没有浸入碳键合耐火材料,也会不断离开系统。
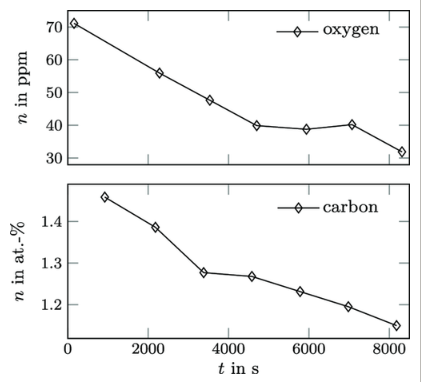
在浸入碳结合氧化铝样品的实验中,还观察到钢熔体氧含量的平台。因此,实验过程中钢液氧含量的总体趋势受SCS使用的实验装置的支配。
与参考实验相比,浸没实验的平均氧损失率略有降低,为每小时18ppm,直到达到氧含量平台。
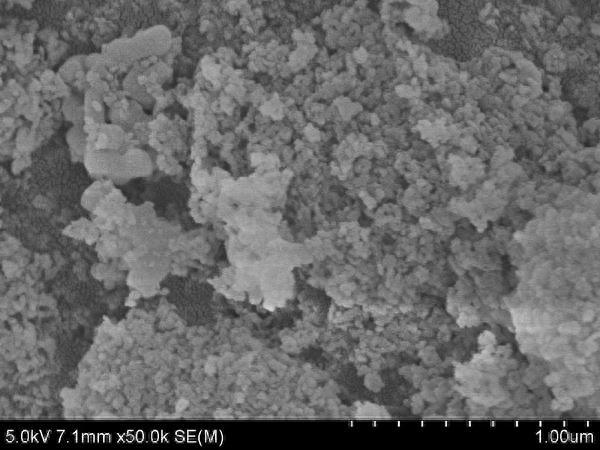
表明,取样会影响SCS内钢熔体的氧含量。在浸泡实验的情况下,与参考测量值相比,氧含量测量两次,而不是每20分钟仅测量一次。
因此,浸没实验期间氧气损失率略有降低可能与氧传感器的额外浸入,耐火样品与钢液的化学反应或两者的组合有关。
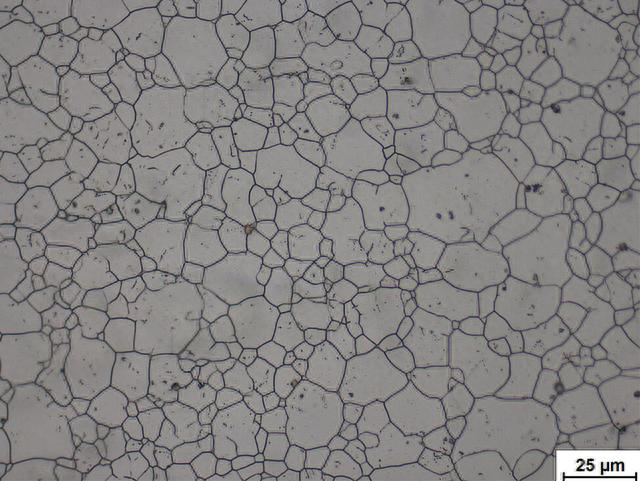
在耐火材料样品浸泡期间,在第一次接触钢熔体后,在耐火材料表面附近观察到强烈的气体产生约40秒。浸泡60s后未检测到进一步的气体鼓泡。在浸泡过程中,在耐火样品的浸没部分表面上形成均匀结构的氧化层。
从熔体中取出耐火样品后,原位成型层的某些部分剥落,从而可以查看基材。在图中,左侧可以看到黑色碳键合基材,右侧显示了形成的白色氧化层。通过表面高度的激光光学测量,发现所有样品中形成的层厚度为≈40-50μm。
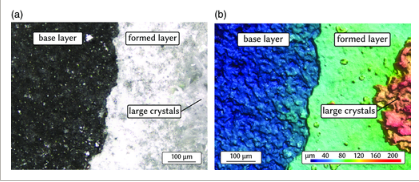
原位形成层的形态可以描述如下。所有样品的平均表面形态由小于5μm的晶体组成,大多数晶体尺寸低于1μm,较大的晶体,晶粒尺寸大于2μm,表现出六边形或三角形形态。
在晶体尺寸≈可能高于5μm的裂缝和晶体尺寸可能高于5μm的样品边缘发现晶体生长增加。在空腔中,经常观察到长度高达50μm的针状晶体形成。
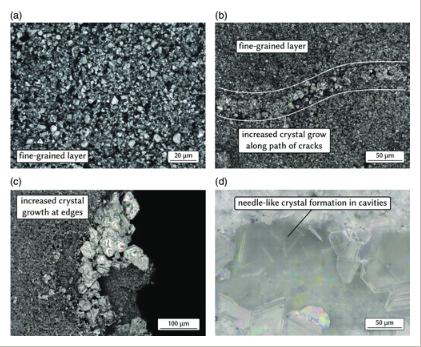
与裂纹无关的较大晶体浓度较高的区域,晶体尺寸高达≈30μm,不规则地分布在所有样品的表面上。所呈现结构的激光光学确定的高度如图所示。
大多数较大的板状和六边形晶体平行于平均小晶结构顶部的表面生长,达到离地面约10μm的高度。
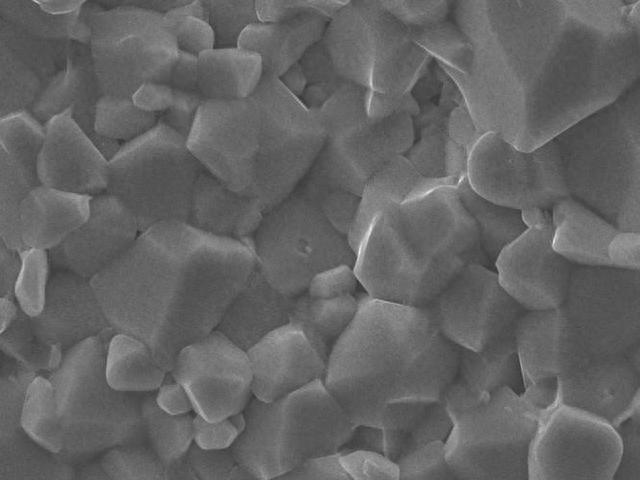
特别是在样品的小侧面区域发现了类似生长的晶体。在这里,几平方毫米的区域被连续的形态所覆盖。在图中,显示了只有几个不同的六边形晶体的典型示例。
仔细观察这些六边形晶体会发现晶体从平行于表面的初始原子核生长,直到达到几微米的一定尺寸。然后,这些晶体作为料斗晶体进一步生长。
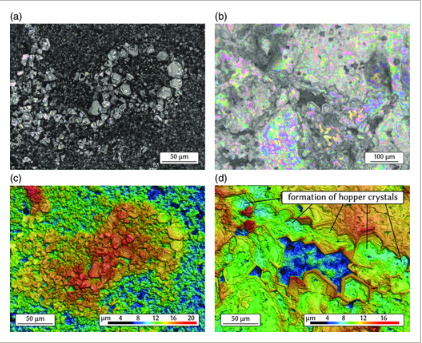
根据以上模型方案,上述晶体开始在过渡过饱和度以上生长形成一个平坦的表面,并在下面结束具有成型料斗晶体。必须说,图所示的大多数小晶体最终以料斗状结构生长。
通过比较观察到的晶粒尺寸和图中原位形成晶体的形态(板状和针状),可以得出结论,在浸泡过程中样品表面的过饱和度的局部值必须略有不同,因此熔体的相应局部化学成分也略有不同。
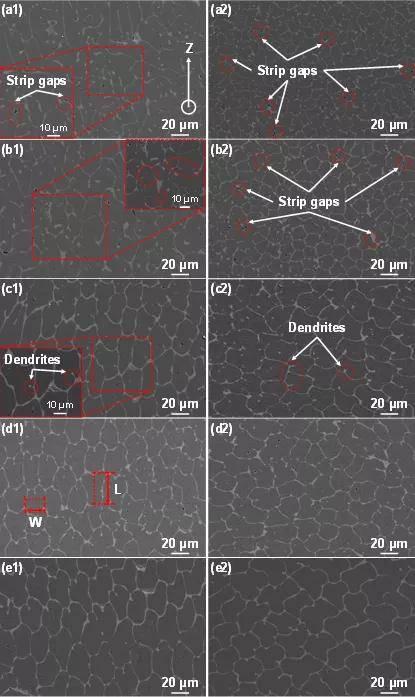
由于晶体形成是基于氧化铝、碳、钢熔体和形成气相之间的化学反应,因此可以假设晶体形成受到样品表面局部不均匀性的强烈影响,例如裂纹、空腔和样品边缘,这会影响靠近耐火表面的溶解元素的扩散动力学。因此,表面不均匀性很可能是原位形成的晶体的形态差异的原因。
相位分析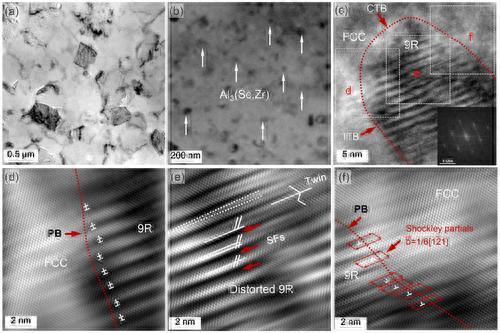
EBSD/EDS对原位形成的表面晶体的研究表明,形成了含(Al、Fe、Mg、Mn)的尖晶石,形成了上述料斗状结构。样品表面的SEM显微照片与尖晶石索引的EBSD图案一起显示。
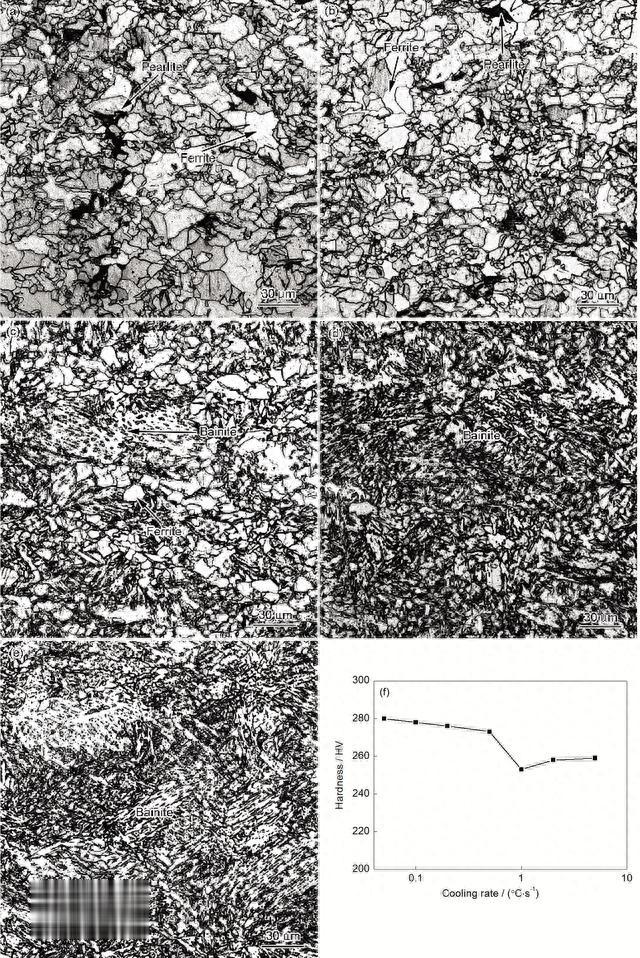
原位形成的晶体的横截面图如图b所示。在碳结合氧化铝基材的顶部,EDS鉴定了一层带有小钢陷阱的氧化铝。样品表面由尖晶石晶体形成,经EDS测定的溶解度为≈32–35%AL、≈6%Mg,以及较小的Mn和Fe溶解度,它们合计为≈1.5–2%。
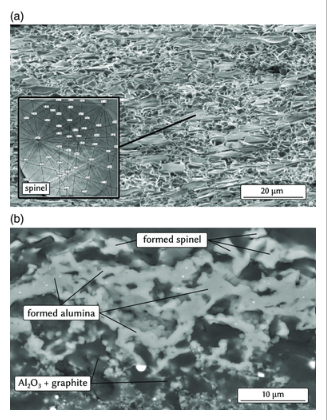
如图所示,平坦表面的GIXD测量结果证实了观察到的相位组合。
没有石墨反射表明观察到的氧化铝反射与基材无关,并且氧化铝和尖晶石两种相都是在碳键合氧化铝耐火材料顶部原位形成的。应该提到的是,在钢的原始成分中没有发现镁。
然而,一个2O3–镁铝2O4制造坩埚用于熔化钢的实验。因此,镁很可能溶解在钢液中,并在耐火样品表面引发尖晶石形成。

从图可以看出,尖晶石晶格参数随着熔体的氧含量而增加。使用相关系数对包括样本I1-I7和初步测试结果(样本P1-P5)在内的总数据集进行了相关分析。
分析得出的相关系数为0.91,p 值为3×10−5.这表明尖晶石晶格参数与钢熔体氧含量之间的关系具有显著而强烈的线性。
由于锰和铁溶解在这些尖晶石中,可以假设它们各自的离子可以改变它们的氧状态以及它们在四面体和八面体尖晶石位置的占用,具体取决于氧分压。由此,可以预期晶格和结构参数的变化。
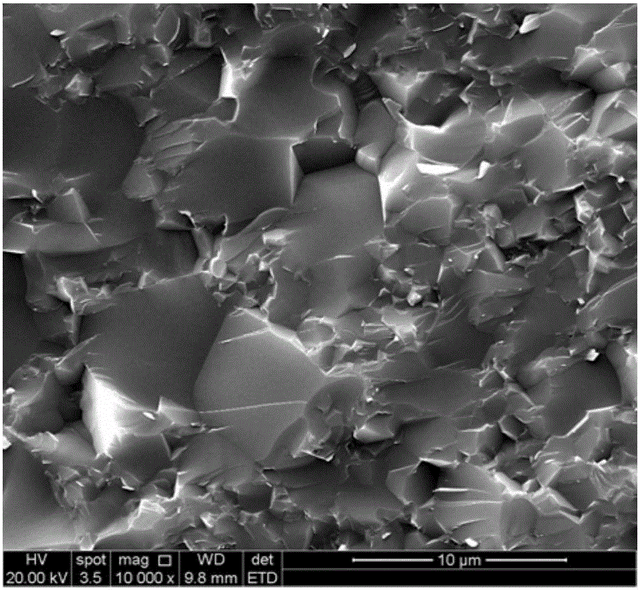
从热力学的角度来看,尖晶石成分与钢熔体/耐火材料界面处的氧分压密切相关。因此,在所研究的体系中,形成的(Al,Mg,Fe,Mn)尖晶石的结构特性可用于评估耐火材料浸泡时钢熔体的氧含量。
表面形貌的表征从Sdr=0.90对于示例1,Sdr样本1的值几乎恒定地增加到2.4,样本1的值进一步跃升至68.6,样本2的值为34.7。
这些值表明,与未反应的样品表面相比,反应后样品的有效表面积大两到三倍。另一方面,峰的密度Sdr与未反应的样品相比,浸入样品的样品减少,如图所示。
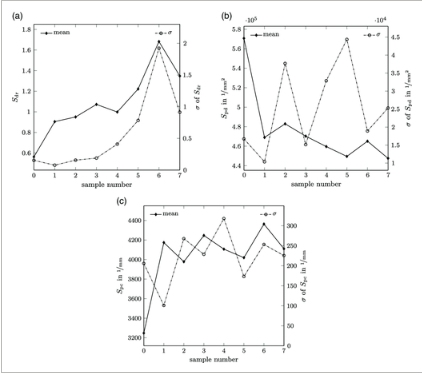
从570000个峰值mm开始−2浸泡前,Sdr480000–450000峰值mm−2确定样品1-7的趋势略有下降。
确定的算术平均峰值曲率Sdr对于未反应的样品为3250mm,而Sdr浸入样品的值在4000到4400mm之间−1,这些值对应于未反应样品和浸没样品的线轮廓峰的曲率半径分别为0.31和0.25–0.23μm。
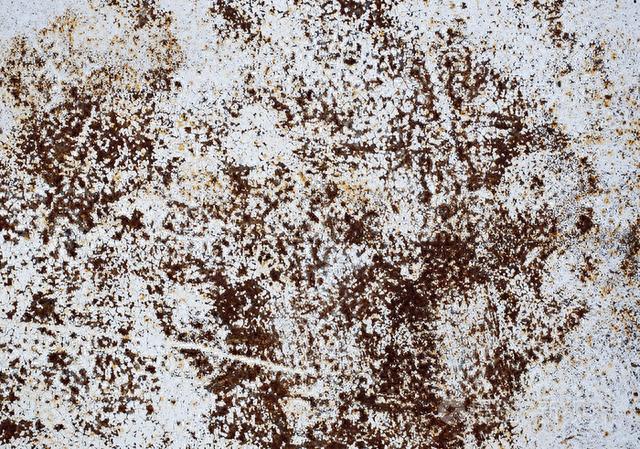
所有样品的表面特征相对于样品的高度和宽度几乎是各向同性的分布,因为它可以从确定的纹理纵横比值中推断出来STR,介于0.8和0.9之间,接近单位(完全各向同性)。
但是,在样本1-4的趋势和样本5-7的趋势中可以看到细微的差异。第一组有STR值介于0.86和0.9之间,略高于起始值0.83。
示例5–7显示STR值介于0.8和0.84之间,这意味着这些表面的各向异性略高于样本1-4的表面。
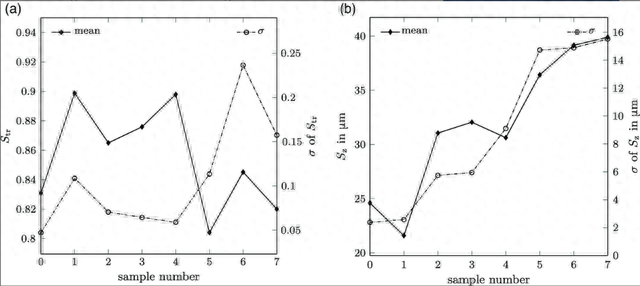
最后确定的基于ISO的值是最大高度Sz,但它的价值需要谨慎解释。
如前所述,在本例中,与ISO相关的高度值不能与样品表面相关。然而,作为Sz表示最小值和最大值之间的差异,如果假设最小值是从基底Al开始的孔,它可以对应于形成的氧化层的厚度2O3–C材料。
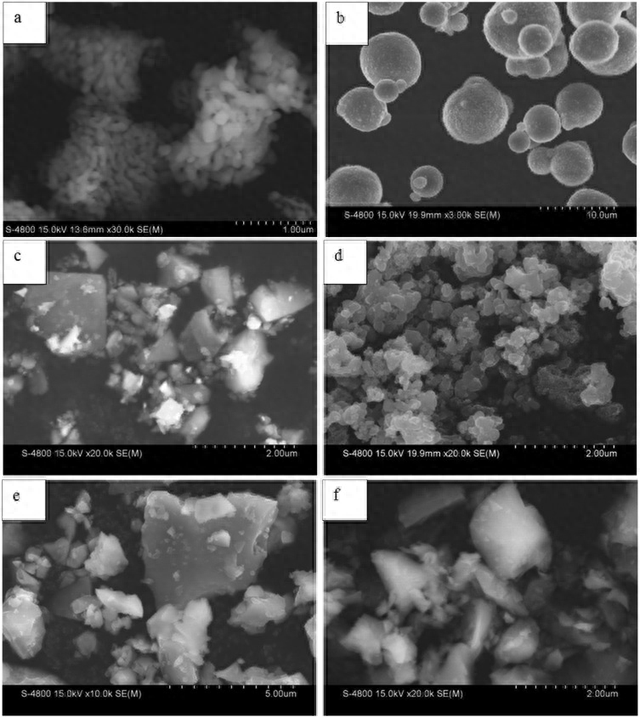
如图 所示,Sz值从样品22–0的1μm增加到样品40的7μm。对于样本2-4,值相对恒定,为Sz=32 Sm.这些数字可以解释为层厚度增加,也可能意味着后一个样品的形成层密度较低,这将增加在测量中击中深孔的机会。
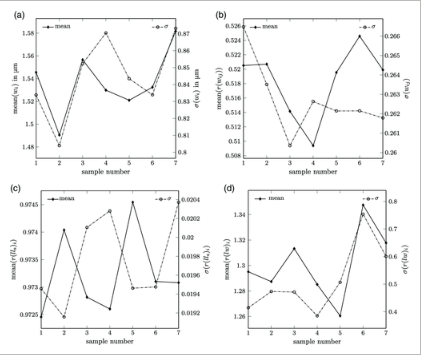
上述五个参数代表了表面形态的一般统计特征。此外,公式定义的参数可用于表征所形成晶体的形貌。截面宽度WI样品在≈1.52μm的范围内,如图所示。
该值与从图a估计的平均晶体尺寸非常吻合。小节宽度的比率R适用于所有样品≈0.52,这意味着对于大多数晶体,一个小节宽度是另一个小节宽度的两倍。
这一观察可以解释如下。如果相对平坦的晶体(相对于样品平面)垂直于样品表面倾斜,则会导致定义的截面基元的子截面宽度又大又短。这种观点也符合观察到的表面晶体的形态。
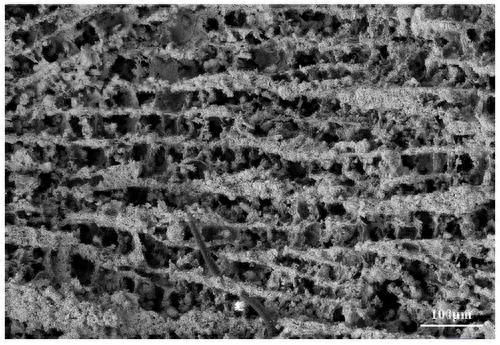
直晶表面的存在也得到了确定值的支持R(USs)我如图所示。对于所有样品,这些值≈0.97,因此非常接近单位,这意味着最小值和最大点之间的矢量长度几乎与沿晶体表面测量的矢量长度相同。
根据大值SPC,晶体表面的斜率,表示为R(LW),显示≈1.3μmμm−1对于所有浸入的样品来说,也是一个很大的值。
统计分析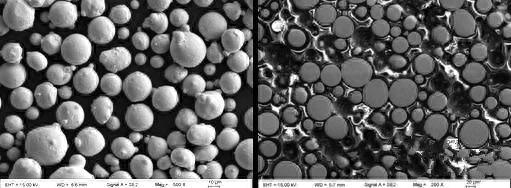
样品I1–I7表面形貌的演变可能受到钢熔体氧含量的影响。因此,使用相同的熔体中氧气逸出数据集进行了多重相关分析。对于多种测试情况,必须调整p值以面对决策误差累积的问题。
一种可能的校正方法是邦弗朗尼程序,它将显著性水平除以元素 N 的数量,与获得调整后的显著性水平相比,元素数量乘以。
在这项研究中,进行了九次测试,这意味着N =9。因此,每个比较都经过了显著性的测试0.059=0.005¯因此,p 值低于此值时表示显著相关性。p 值<0.19=0.011¯被认为显示出一种趋势。
结论本研究通过对碳结合氧化铝复合耐火材料在钢液环境中的原位氧化层生长进行表征,得到了以下重要结论。钢液与碳氧化铝反应首先形成一层氧化铝,继而长出含Al、Fe、Mg、Mn元素的尖晶石外层。尖晶石的化学组成会随钢液中溶解氧量的增加而发生变化。
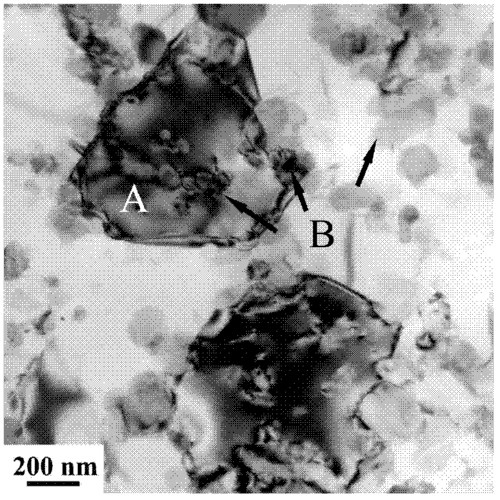
尖晶石层的形成主要受到局部氧分压的影响,与钢液整体溶解氧量关系不大。这一发现说明界面反应是一个在微区域环境下进行的较为局限的过程。
采用ISO25178标准中与定义表面高度无关的参数,可以成功定量描述不规则氧化层表面上的晶体形貌特征。这为连接反应条件与表面形态提供了有效手段。
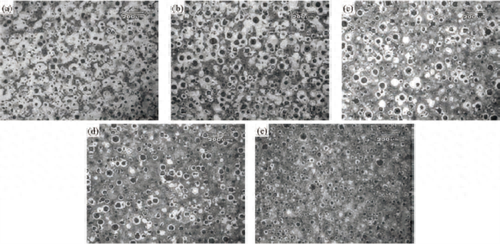
根据溶解氧量与尖晶石化学组成的对应关系,建立了一个预测钢液-耐火材料界面反应过程及氧化层形成的模型。该模型可用于优化工艺参数,延长过滤系统使用寿命。揭示了界面反应过程中的原位氧化层形成机制,获得了一系列具有重要科学意义和应用价值的创新结论。
参考文献1R. Khanna, V. Sahajwalla, B. Rodgers, F. Mccarthy, Metall. Mater. Trans. B 2006, 37, 623.
2M. Ikram-ul Haq, R. Khanna, P. Koshy, V. Sahajwalla, ISIJ Int. 2010, 50, 804.
3R. Khanna, M. Ikram-ul Haq, Y. Wang, S. Seetharaman, V. Sahajwalla, Metall. Mater. Trans. B 2011, 42, 677.