浅谈集成电路用金属溅射靶材研究现状
居炎鹏,李心然
(河南东微电子材料有限公司)
摘要:
文章介绍了集成电路用金属靶材的技术要求和制备工艺,并对金属溅射靶材发展趋势进行了预测和展望。
集成电路产业属于高端制造业,是信息技术领域的核心产业,事关国民经济发展和国家战略安全地位,已经成为一个国家综合国力的重要标志之一。集成电路是一种微小电子设备或元件,如各类晶体管、电阻器及电容器等均是通过电极导线连接或是通过介质材料隔离以实现特定的功能,而用于电极导线或介质材料部分是通过磁控溅射镀膜方法制得,这种磁控溅射方法就需要对应的高纯金属溅射靶材作为溅射源。溅射靶材是磁控溅射法制备集成电路薄膜的主要关键原材料,对集成电路市场及整个产业的发展具有决定性影响,它随着集成电路逻辑、存储、封装以及高性能、低功耗的新器件发展,已成为热点研究材料。集成电路用金属溅射靶材有铝、铜、钛、钽、钴、镍、钨、钼、铂、金、银、钌等[1] ,主要用于制备晶圆导电层、阻挡层以及金属栅极等。各类金属靶材于不同技术节点之内搭配使用,如集成电路中重要的逻辑芯片,铝靶主要用作110 nm 以上技术节点的布线材料,钛靶作为其配套的阻挡层材料;铜靶主要用于110 nm以下,钽靶与之配套作为阻挡层材料。溅射镀膜工艺起源于国外,对金属溅射靶材产品性能要求高,专业应用性强,长期以来靶材产业集中在美、日少数几家公司,如日本日矿金属各种靶材加工能力居全球首位,与东曹、霍尼韦尔、普莱克斯三家公司共同瓜分了全球80%以上市场份额。我国最早进入集成电路用金属靶材研究制备厂商主要代表有江丰电子和有研亿金,国内外主要供应商见表1。
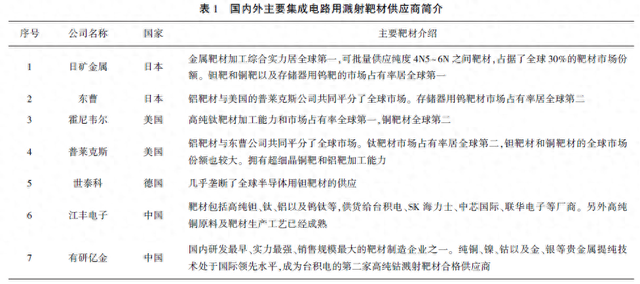
1 技术要求
1.1 纯度
金属溅射靶材的纯度与溅射镀膜的纯度息息相关,高纯度乃至超高纯度的金属材料是生产高纯金属靶材的基础。金属靶材若杂质含量高,在溅射时会影响辉光放电;还会导致薄膜电阻率的增加,从而影响薄膜均匀性,甚至会造成集成电路短路。集成电路产业的金属靶材纯度通常达99. 995% ( 4N5) 甚至99. 9999%(6N)以上,除了总杂质含量要求低之外,还要严格控制个别杂质元素的不利影响。如碱金属(K、Na、Li 等)易在绝缘层中形成可移动性离子,降低器件性能;放射性元素(U、Th 等)会释放射线,造成元器件产生软击穿;过渡族金属(Fe、Ni、Cr 等)会产生界面漏电及氧元素增加;卤素(Cl 等)离子会腐蚀电路[2] ;气体元素(C、O、N 等)损伤膜的稳定性,成为膜电阻增大的原因[3] 。如何持续降低金属靶材中杂质元素的含量,提升金属靶材的纯度是目前金属靶材制备技术发展的焦点。
金属提纯通常使用化学提纯和物理提纯两种方式。化学提纯主要分为湿法提纯与火法提纯,通过电解、热分解等方式析出主金属,如高纯Cu、Co、Ni、Ag、Ti 等都是通过电解法制备的;物理提纯则是通过蒸发结晶、电迁移、真空熔融法等步骤提纯得到主金属,高熔点金属如Ni、Ti、Co、Ta 等可采用真空电子束或电弧熔炼制备,其他金属如Al、Cu、Au、Ag 等可以用真空感应熔炼制备[4] 。需要获得超高纯金属,常用提纯方案为纯化(初步提纯)、超纯化(再提纯)到化学+物理提纯(最终提高纯度)两大步。
金属提纯核心技术多掌握在欧美日等企业中,尤其是日矿金属冶炼提纯能力世界一流,可批量供应纯度于4N5 ~ 6N 的金属靶材,其中铜靶材能提纯高达9N 级别,拥有行业最高的技术水平。我国有研亿金以电解精炼法和区域精炼法制备的铜稳定纯度达6N,最高能达7N,成为我国屈指可数实现6N 超高纯铜批量生产的企业。目前纯铝方面,德国、挪威和俄罗斯等多采用三层液电解精炼生产高纯铝,如挪威海德鲁公司以99.7%~99.9%的原铝为原料,先用三层液电解法提纯到99.99%,后通过偏析法提纯至5N~6N。我国已引进三层液电解精炼法和偏析熔炼法生产高纯铝,成为世界第二大高纯铝生产国。高纯钛作为常用的阻挡层薄膜材料之一,常用方法有克劳尔法、熔盐电解法、碘化法等;国际上只有美国霍尼韦尔和日本住友钛等几家用熔盐电解法制备高纯钛。国内生产高纯钛常用传统碘化法,但是生产效率低,容易受到来自反应容器的污染。日本住友钛发明一种新的碘化法,以四碘化钛为原料制备6N 的高纯钛。江丰电子通过真空电子束熔炼等工艺获得高纯度、极低氧超高纯钛材(99.9997%),彻底打破了美日等国长期垄断的局面。国内主要生产企业见表2。
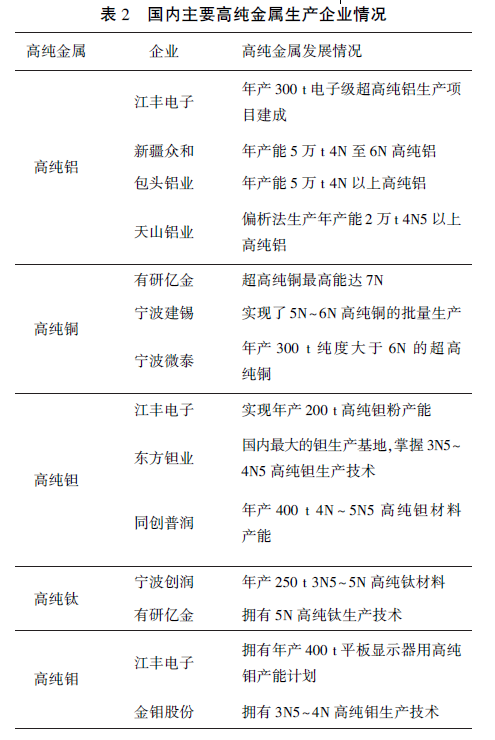
1.2 晶粒尺寸及晶面取向
晶粒尺寸的大小直接影响着溅射速率,晶粒越细小的金属靶材溅射速率越快,并且晶粒尺寸越均匀,沉积的薄膜厚度分布也比较均匀。用于集成电路的金属靶材的晶粒尺寸通常在100 μm 以下,甚至更小,因为溅射时晶界处的原子比晶粒内的原子更容易剥离刻蚀[5] ,细晶粒的晶界更多,故细小晶粒的金属靶
材有利于提高溅射薄膜的沉积效率。普莱克斯公司提供超细晶铝合金靶材晶粒尺寸可控制至0.5 μm,同样提供的12″铜靶材晶粒尺寸可控制在25 μm 以内。霍尼韦尔公司通过等通道角挤压(ECAE)技术可控制金属靶材晶粒尺寸至0.5 μm,并保持良好的均匀性。江丰电子提供的12″钨靶材晶粒尺寸虽然最细粒度能达到20 μm,但与国际先进水平相差较远。晶面取向分布也对溅射薄膜均匀性有显著影响,晶面取向越均匀一致的金属靶材溅射沉积薄膜的均匀性和质量也越好。控制晶面取向就是控制靶材溅射面上的原子排列方向相同,通常在溅射时原子会倾向于沿着最紧密排列方向优先溅射[6] 。但是完全保证晶面取向趋于最紧密排列方向是非常困难,因此要求靶材的溅射面晶面有利于溅射薄膜方向分布且均匀一致,才能获得优质沉积薄膜,尤其是充填集成电路中含有高深宽比沟槽的薄膜表现特别明显,如铝靶材晶面取向为{200}时有利于溅射薄膜的质量,钌靶材最佳晶面是(112)、(002)、(004)[7] 。Honeywell 公司能生产出整个厚度方向都是{111}织构[8] 的钽靶。虽然我国对各种金属靶材的细晶粒尺寸和有利于溅射的晶面取向研究有了一定进展,但控制工艺不成熟,织构不稳定。
1.3 致密度
金属溅射靶材致密度反映出靶材孔隙率的高低,致密度低的孔隙含量高,孔隙内壁也会吸附一些杂质元素,这些杂质元素难以消除。致密度低的金属靶材在溅射时产生不均匀冲蚀和增大薄膜应力,造成晶界取向差,进而增加了薄膜的电阻率,增加器件功耗。为了获得高致密度(>99.5%)的金属溅射靶材,可以选择改进靶材制备工艺,对于粉末冶金法,通过提高原料纯度,并采用热等静压、等离子烧结、微波烧结等技术来提高靶材致密度;对于熔炼工艺可通过磁场搅拌并减少冒口、轧制或锻造成型等方法来提高金属靶材致密度。
有研亿金的发明专利[9] 是用多道次小变形热轧致密化钨靶表面充当热等静压包套,进行无包套烧结制备出致密度99.5%以上的细晶粒钨靶材。江丰电子的发明专利[10] 以钼粉依次经过退火、冷压和热压烧结得到钼坯,然后放入包套中经热等静压拼接后得到致密度大于99.9%钼靶材。
2 制备工艺
金属靶材主要的制备工艺分为熔融铸造法和粉末冶金法两种。熔融铸造法优点是靶材杂质含量低,密度高,能制备大型靶材;缺点是需要热处理进行处理,难以做到成分均匀化。粉末冶金法优点是靶材成分均匀,可节约成本,尤其对高熔点金属用粉末冶金方法有优势;缺点是密度低,杂质含量高。
铜、铝等低熔点或塑性较好的靶材(金、银、铂等)主要通过熔炼和热加工工艺方法。为了控制良好的晶粒尺寸和晶面取向,在熔炼后再配合轧制或锻造等塑性加工进一步优化。作为互联线用铜和铝靶材通过冷变形、热处理等工艺处理后,更有利于膜层的质量。金、银、铂及合金靶材制备优先通过真空熔炼得到低气孔率、组织均匀的高品质铸锭后,经过大于80%变形量加工和再结晶退火进行调整和控制晶粒和晶向。高熔点金属靶材(钨、钼、钌等)和脆性较大的合金靶材(钨钛、CoFeB 等)通过粉末冶金工艺来控制微观品质。主要工艺流程为混粉(或雾化)、成形、致密化烧结、机加工等,其中成形有冷压成形和热压成形,烧结方法有热压烧结、真空热压烧结、热等静压烧结、放电等离子体烧结等。用粉末冶金工艺制备出高纯或超高纯的金属靶材,要求首选用高纯、超高纯的金属粉末,并在采取快速成形和烧结方法来避免混入其他杂质后,还对制备过程中接触工具、设备、气氛都有极高的要求,以保证金属靶材的纯度要求。
3 未来的发展趋势预测
随着大规模、超大规模集成电路(VLSI)技术发展趋势,集成度越来越高,特征尺寸越来越小,对金属溅射靶材要求越来越严格。另外伴随AI 人工智能芯片浪潮下,云计算、智能汽车、智能机器人等人工智能产业快速发展,推动了金属靶材市场需求将持续增长。笔者预计未来金属溅射靶材的发展趋势如下:(1)靶材的纯度进一步提升(≥6N)。集成电路超度集成化,特征尺寸缩小化,更细小微米及纳米工艺的需求,所需的金属靶材纯度不断攀升;(2)金属靶材大尺寸化,晶圆尺寸越大,可利用效率越高,目前逐步向450 mm发展,大尺寸晶圆要求金属靶材也朝着大尺寸方向发展;(3)进一步减小靶材晶粒尺寸,提高组织均匀性,晶粒细小且组织均匀,是获得高性能集成电路关键技术之一,在极大集成电路中将会有更多的高深宽比沟槽需要溅射薄膜填充,均匀细小的晶粒能使沟槽填充薄膜更均匀。
4 结语
我国对金属靶材的各方面研究有了较大突破,但与国际先进金属靶材企业相比还有很大差距。国内靶材制造商已经制备出满足集成电路要求的金属溅射靶材,但高端、高品质靶材缺口还需要依靠国外进口来解决。在靶材技术和市场被垄断和我国金属靶材市场已成为世界靶材最大需求地区之一的背景下,我国集成电路用金属靶材研究和制造面临着机遇和挑战,在解决金属靶材制备技术上创新不足、专业人才匮乏、上下产业链沟通不及时、靶材产品验证周期长等问题后,继续加大金属溅射靶材基础研究,加强国际合作交流,加强靶材上下游企业的联动,加大科技人才培养,解决关键设备国产化,共同实现我国金属溅射靶材产业的高水平发展,以此推动我国社会经济可持续发展和巩固国家安全战略地位。