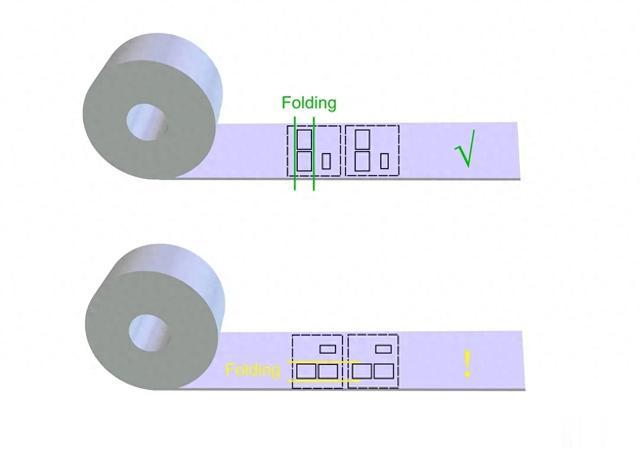
首先,人(Man):操作人员是否经验不足?有没有操作不当的情况?比如在装卸料时是不是手法不正确,导致铝塑膜被刮伤或折叠?另外,培训是否到位?有没有定期进行技能考核或者操作规范的复习?如果员工疲劳工作,也可能导致注意力不集中,从而引发问题。还有,是否按照标准作业流程操作,有没有人为了加快速度而跳过某些步骤?
接下来是机(Machine):冲压设备的状态如何?模具是否有磨损或者损坏?模具的锋利度不够可能会导致冲压时应力集中,从而撕裂铝塑膜。冲压的压力参数设置是否合适?过大的压力或者不合适的冲压速度都可能造成破损。设备有没有定期维护保养?比如润滑是否足够,有没有松动部件导致振动异常?另外,设备的定位和夹紧装置是否准确,如果定位不准,可能导致材料移位,冲压位置偏差,进而破损。
然后是料(Material):铝塑膜本身的质量有没有问题?供应商提供的材料是否有批次差异,比如厚度不均匀,或者涂层有缺陷?材料在运输和存储过程中有没有受损,比如受潮、受压变形或者被尖锐物划伤?材料的来料检验是否严格,有没有漏检的情况?铝塑膜的材质参数是否符合工艺要求,比如延展性、抗拉强度是否达标?
接下来是法(Method):成型工艺参数是否合理?比如冲压温度、速度、压力等参数是否在最佳范围内。有没有进行充分的工艺验证和DOE实验?作业指导书是否详细明确,操作人员是否严格按照指导书执行?工艺设计是否存在问题,比如模具设计不合理,导致应力分布不均,容易撕裂。有没有对工艺流程进行过优化,或者变更过参数后未进行验证?
测(Measurement):检测方法和工具是否准确可靠?有没有使用合适的检测设备,比如光学检测仪、厚度测量仪等?检测标准是否明确,有没有明确的接受和拒收标准?检测频率是否足够,是否做到了全检还是抽检,抽检的比例是否合理?检测人员是否经过培训,是否存在漏检或误判的情况?检测数据有没有统计分析,找出破损的规律?
环(Environment):生产环境是否符合要求?比如温度、湿度是否控制得当,过高或过低的温湿度是否影响铝塑膜的物理性能?车间清洁度如何,是否有灰尘、异物导致冲压时划伤材料?静电控制是否到位,铝塑膜是否因为静电吸附杂质或者自身粘连?地面和设备的振动情况如何,是否有外部振动源影响冲压精度?
现在我需要把这些可能的因素系统地整理出来,每个方面都列举可能的原因,并提供对应的解决方向。同时可能需要考虑这些因素之间的相互作用,比如材料问题加上设备参数不当可能共同导致破损。另外,是否有一些数据支持,比如破损率的变化是否与某个因素变更的时间点吻合,或者破损的位置是否有特定模式,这些可能帮助定位问题根源。例如,如果破损集中在某个区域,可能是模具局部磨损;如果随机分布,可能是材料问题或操作不一致。
可能的遗漏点:比如是否在换模后出现问题,或者新员工上岗导致操作问题。或者材料供应商最近是否有变更?有没有进行过变更管理评估?设备最近是否有过维修,更换过零件?这些变更点可能引发问题。
另外,是否进行了根本原因分析,比如使用鱼骨图或5Why方法?比如为什么铝塑膜破损?因为冲压时应力过大。为什么应力过大?因为压力参数设置过高。为什么参数设置过高?因为设备校准错误,或者工艺参数未优化。需要这样层层深入。
总结来说,需要从5M1E的六个方面全面排查,结合现场观察、数据分析、实验验证等方法,逐步缩小范围,找到根本原因,然后制定相应的纠正和预防措施。
1. 人(Man)可能原因:操作不熟练:新员工培训不足,装卸料时手法不当(如过度拉扯、折叠)。未按SOP执行:跳过关键步骤(如未检查模具状态、未校准参数)。疲劳作业:长时间工作导致注意力下降,操作失误率上升。解决方向:加强操作培训与考核,重点规范装卸料动作。复查作业指导书(SOP),明确关键控制点并监督执行。优化排班制度,避免过度疲劳。2. 机(Machine)可能原因:模具问题:磨损、毛刺、对位偏差导致应力集中。设备参数异常:冲压压力/速度过高、行程设置不当。设备维护不足:润滑不良、部件松动引发振动或定位偏移。解决方向:检查模具状态,修复或更换磨损/损坏的模具。重新验证工艺参数(如DOE实验优化压力、速度)。制定定期维护计划(如清洁、润滑、紧固关键部件)。3. 料(Material)可能原因:原材料缺陷:铝塑膜厚度不均、涂层附着力差、延展性不足。存储不当:受潮、受压变形或表面划伤(搬运或存放接触尖锐物)。供应商批次差异:未检出不良来料。解决方向:加强来料检验(如拉伸测试、表面缺陷检测)。规范仓储条件(温湿度控制、防压防划措施)。与供应商联合分析,要求提供材料物性参数报告。4. 法(Method)可能原因:工艺参数不合理:温度/压力/速度超出材料承受范围。模具设计缺陷:坑槽边缘角度过锐,导致撕裂。工艺变更未验证:参数调整后未进行小批量试产。解决方向:通过实验(如正交试验)优化冲压参数。评估模具设计,优化边缘圆角或过渡区域。建立工艺变更管理制度,确保变更前验证。5. 测(Measurement)可能原因:检测标准模糊:未定义破损的判定标准(如裂纹长度、位置)。检测设备精度不足:无法识别微小缺陷。抽检频率低:漏检率高,未覆盖全批次。解决方向:明确检测标准(如使用放大镜/显微镜辅助目视检查)。引入自动化检测设备(如机器视觉系统)。调整抽样方案(如增加首检、巡检频次)。6. 环(Environment)可能原因:温湿度失控:材料脆化(低温)或软化(高温高湿)。车间清洁度差:粉尘或异物附着导致冲压时划伤。静电干扰:铝塑膜吸附杂质或自身粘连。解决方向:控制车间温湿度在工艺要求范围内(如25±3℃,湿度≤40%)。加强清洁管理(如设备除尘、地面无尘化)。增加静电消除装置(如离子风机)。综合分析建议数据追溯:统计破损发生的时段、机台、操作员及材料批次,寻找相关性。实验验证:针对疑似因素(如模具磨损、参数过载)进行对比试验。根本原因分析:使用5Why法(例如:破损→模具应力集中→模具未定期维护→维护计划缺失)。防错措施:设计防呆装置(如自动定位夹具)、增加关键参数实时监控。通过系统排查和针对性改进,可有效减少铝塑膜破损异常,提升制程稳定性。
系统排查和针对性改进
结合之前的5M1E分析,将每个因素对应的排查步骤具体化。例如,在“人”的因素中,之前提到操作培训,现在需要具体检查培训记录、现场操作等。同样,对于设备、材料、方法等,都要转化为可操作的检查点。
确保步骤的可行性,比如建议使用5Why、鱼骨图等质量工具,这些都是PQE工程师熟悉的,符合他们的工作习惯。同时,数据统计和分析方法需要具体,比如柏拉图分析,帮助定位主要问题点。
最后,总结部分要强调系统性和持续改进,确保用户理解排查不是一次性的,而是需要长期跟踪和优化。可能用户还需要知道如何验证措施的有效性,所以步骤中包含效果确认和标准化流程是必要的。
总结起来,需要将系统性排查分为几个阶段:紧急遏制、数据收集、要因验证、防错措施、效果确认和标准化,每个阶段下详细列出具体步骤,并结合之前的5M1E因素,确保全面覆盖可能的原因。同时,语言要简洁明了,结构清晰,便于用户在实际工作中应用。
第一阶段:紧急遏制与初步定位现场隔离与遏制立即隔离问题批次铝塑膜(包括已冲压和未冲压的物料),避免不良品流入下工序。对异常机台或工位暂停生产,标记待排查区域。快速数据收集统计破损发生的 时间、机台编号、操作人员、材料批次、模具编号 等信息。记录破损形态(如撕裂位置、裂纹方向、是否伴随划痕等)。绘制 柏拉图(Pareto图) ,分析破损发生的集中性(如是否集中在某机台或某批次材料)。第二阶段:分层排查(5M1E逐项验证)1. 人员(Man)操作验证:观察操作员装卸料动作是否规范(如是否对齐模具、有无过度拉扯)。检查操作记录,确认参数设置是否与SOP一致(如压力、温度、速度)。培训追溯:确认操作员是否经过培训并考核合格,重点检查新员工或轮岗人员。2. 设备(Machine)模具状态检查:拆解模具,检查冲头、凹模是否有磨损、毛刺或异物附着。使用投影仪或3D扫描仪测量模具对位精度(如上下模间隙是否均匀)。设备参数验证:校准压力传感器、温度控制器等关键仪表,确认实际值与设定值是否一致。检查设备运行稳定性(如冲压过程中是否有异常振动或噪音)。3. 材料(Material)来料复测:对问题批次铝塑膜进行物理性能测试(如拉伸强度、延伸率、剥离力)。对比正常批次材料,检查是否存在厚度不均、涂层缺陷或表面划痕。存储条件核查:检查仓库温湿度记录,确认是否在要求范围内(如湿度是否超标导致材料吸潮)。4. 方法(Method)工艺参数验证:通过DOE(实验设计)验证当前压力、速度、温度是否超出材料承受极限。检查工艺文件是否更新,确认操作员使用的参数版本是否正确。模具设计审查:评估冲坑边缘设计(如圆角是否过小,R角是否导致应力集中)。5. 测量(Measurement)检测方法确认:复测已判定为“合格”的样品,确认是否存在漏检(如使用显微镜检查微小裂纹)。检查检测设备(如拉力机、影像测量仪)是否校准且在有效期内。标准一致性核查:确认质检员对破损的判定标准是否统一(如裂纹长度≥0.5mm才判不良)。6. 环境(Environment)环境监控:连续记录车间温湿度数据,对比破损发生时段的环境条件是否异常。检查车间清洁度(如冲压区域是否有粉尘、金属碎屑残留)。第三阶段:要因验证与根因锁定对比试验通过 单一变量法 验证疑似原因(例如:更换模具后测试破损率是否下降)。模拟极端条件(如调整温湿度、提高冲压压力),观察破损是否复现。根本原因分析工具使用 5Why分析法 深挖问题根源(示例):Why 1:为何铝塑膜冲压后破损?→ 冲压时边缘应力集中导致撕裂。Why 2:为何应力集中?→ 模具边缘圆角过小(R角设计不合理)。Why 3:为何模具设计未考虑R角?→ 模具设计阶段未进行有限元应力仿真验证。使用 鱼骨图(因果图) 汇总所有潜在因素,筛选高概率要因。第四阶段:改善与防错临时措施对已验证的要因立即调整(如降低冲压压力、更换磨损模具)。增加全检频次,确保不良品不流出。长期对策优化模具设计(如增大R角、增加过渡区域)。建立关键参数监控系统(如压力实时报警功能)。导入防错装置(如自动定位夹具防止材料偏移)。标准化与横向展开更新SOP、检验标准和设备维护计划。将改善措施推广至其他同类机台或产线。第五阶段:效果确认与跟踪效果验证统计改善后破损率(对比改善前数据,目标:降低至≤0.1%)。跟踪至少3个生产批次,确认稳定性。持续监控将破损率纳入SPC(统计过程控制)管理,设置控制限报警。定期复盘历史数据,预防类似问题复发。排查工具推荐数据分析:Minitab(柏拉图、DOE分析)、Excel(数据透视表)。检测设备:光学显微镜、拉力试验机、3D轮廓仪。仿真工具:ANSYS(模具应力仿真)、AutoForm(冲压成型模拟)。通过以上系统性排查,可高效定位铝塑膜破损的根本原因,并制定针对性解决方案,同时建立预防机制,提升工艺可靠性。