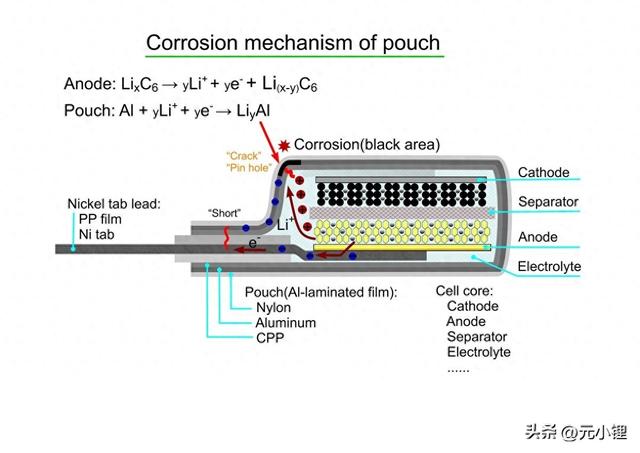
1. 人(Man):操作人员是否在操作过程中有失误?比如装配时有没有不当操作,导致电池封装不严?或者培训不足,员工对标准操作流程不熟悉?比如在搬运电池时有没有造成物理损伤,导致漏液?
2. 机(Machine):设备方面,可能的问题包括封装机的参数设置是否正确,比如温度、压力、时间是否合适。如果封装机的温度不够,可能导致封装不牢固;或者压力不均匀,导致某些部位没有密封好。另外,设备的老化或维护不足是否会影响性能?比如模具磨损导致密封边不一致?
3. 料(Material):原材料的问题可能有哪些?比如铝塑膜的质量是否合格,是否有缺陷或厚度不均?电解液的腐蚀性是否过强,导致封装材料被侵蚀?或者隔膜、极片等材料存在毛刺,刺穿包装?
4. 法(Method):工艺方法是否有问题?比如封装工艺流程是否合理,步骤是否正确,比如是否在封装前有异物残留?工艺参数是否经过验证,比如封装温度和时间是否最佳?有没有按照作业指导书执行,或者是否有遗漏的步骤?
5. 环(Environment):生产环境是否符合要求?比如温湿度控制不当,导致材料膨胀或收缩,影响密封效果?车间洁净度不够,灰尘或颗粒物进入封装区域,导致密封不良?或者环境中的振动或静电干扰设备运行?
6. 测(Measurement):检测方法是否有效?比如漏液检测的流程是否能够准确识别问题?检测设备是否校准正确,是否存在漏检的情况?或者抽样检验的比例不足,导致部分问题电池未被发现?
接下来需要逐个深入分析可能的具体原因。比如在“机”方面,可能需要检查封装机的维护记录,确认参数设置是否正确,或者进行DOE试验验证不同参数的影响。在“料”方面,可能需要检查铝塑膜的来料检验报告,或者进行材料耐腐蚀测试。在“法”方面,可能需要观察操作流程,确认是否有步骤被跳过,或者参数设定错误。
另外,可能还需要考虑生产过程中的其他因素,比如是否在某个时间段集中出现漏液,是否有更换过供应商,或者是否有新员工操作设备等。同时,漏液的位置是否集中在某个特定区域,比如边缘、角落,这可能帮助定位问题点。
需要收集数据,比如漏液电池的生产批次、时间、操作人员、设备编号等信息,进行统计分析,找出共同点。然后针对可能的因素进行实验或调整,逐一排除,找到根本原因。
可能还需要进行故障树分析(FTA)或者鱼骨图来系统化地梳理各个可能性,确保没有遗漏关键因素。例如,漏液的可能原因包括封装不良、材料缺陷、机械损伤等,每个大类别下再细分到5M1E中的各个因素。
最后,确定原因后需要制定纠正措施,比如调整设备参数、加强员工培训、更换供应商材料等,并验证措施的有效性,确保问题得到解决。
1. 人(Man)
可能原因:操作人员未按标准流程作业(如封装时未对齐、压力施加不均)。搬运或操作过程中电池受到机械损伤(碰撞、挤压)。新员工培训不足,对关键工艺参数(如封装温度、时间)理解偏差。解决建议:核查操作录像,观察是否存在违规操作。加强标准化作业(SOP)培训,并实施操作认证考核。引入防错装置(如夹具定位、压力传感器),避免人为失误。2. 机(Machine)
可能原因:封装机参数异常(温度、压力、时间偏离设定值)。设备老化导致热封模具磨损、加热板温度不均。真空封装系统泄漏,导致封装环境不达标。解决建议:校准设备参数,进行DOE试验优化温度/压力/时间组合。定期维护模具(清洁、更换),检查加热板平整度。监测真空度并记录趋势,排查管路密封性。3. 料(Material)
可能原因:铝塑膜质量缺陷(厚度不均、涂层脱落、耐电解液腐蚀性差)。电解液成分异常(酸度过高,加速腐蚀密封层)。极片/隔膜毛刺刺穿铝塑膜。解决建议:对铝塑膜进行来料检验(拉伸强度、耐电解液测试)。分析电解液成分,验证与封装材料的兼容性。增加极片毛刺检测工序(如显微镜抽检)。4. 法(Method)
可能原因:封装工艺参数未经验证(如热封温度过高导致材料降解)。封装后未进行充分冷却,导致密封层应力开裂。工艺流程中存在异物引入(如粉尘污染封装面)。解决建议:通过正交试验优化工艺窗口(温度/压力/时间)。增加封装后冷却步骤(如梯度降温)。清洁度管控(如引入离子风机、封装前酒精擦拭)。5. 环(Environment)
可能原因:车间温湿度波动大(如高温高湿导致铝塑膜变形)。洁净度不足(颗粒物附着在封装界面,影响密封性)。静电导致铝塑膜吸附异物。解决建议:控制环境温湿度(建议25±3℃、湿度≤30%)。升级车间洁净度等级(如万级无尘车间)。增加静电消除设备(如离子风棒)。6. 测(Measurement)
可能原因:漏液检测方法不敏感(如仅依靠目视,未采用氦检或真空测漏)。检测设备未校准(如压力测试仪偏差)。抽样比例低,漏检异常批次。解决建议:引入高精度检测手段(如氦质谱检漏仪)。制定设备校准计划(每日/每周点检)。提高全检比例(尤其是首末件和异常时段产品)。综合排查步骤:
1. 数据收集:统计漏液电池的批次、设备编号、操作人员、时间段,寻找相关性。
2. 根本原因分析:使用鱼骨图或5Why法锁定关键因素(如某台封装机参数漂移)。
3. 验证措施:针对可疑因素进行小批量试产,对比漏液率变化。
4. 标准化:更新SOP、增加防错控制点,并持续监控过程能力(CPK≥1.33)。
通过系统性分析,可高效定位漏液根源,确保改进措施长效落实。
系统性排查步骤建议
首先,应该从数据收集开始,因为数据能帮助定位问题的时间和批次。然后是初步分析,比如观察漏液位置和模式,这有助于判断是工艺问题还是材料问题。接下来是分阶段排查,每个阶段针对不同的5M1E因素。
在人员方面,可能需要检查操作记录和培训情况;机器方面,设备参数的校准和维护是关键;材料方面,需要检查来料质量和存储条件;方法上,确认工艺参数和操作流程;环境方面,温湿度和洁净度的影响;测量方面,检测方法和设备的准确性。
还要考虑根本原因分析工具,比如鱼骨图或5Why,以及验证措施,如小批量试产。最后是标准化和持续监控,确保问题不会复发。需要确保步骤逻辑清晰,用户能逐步执行,同时给出实用建议,比如使用氦检或统计分析工具。可能用户需要具体的工具或方法名称,所以应该提到SPC、FMEA等。还要注意语言简洁,避免过于技术化,但保持专业性。
1. 数据收集与初步分析· 步骤:
1. 数据整理:
§ 统计漏液电池的 批次号、生产时间、设备编号、操作人员、生产线位置。
§ 记录漏液电池的 漏液位置(封装边缘、极耳处、铝塑膜表面等)和 漏液形态(喷射状、浸润状)。
2. 初步观察:
§ 对漏液电池进行 拆解分析(观察铝塑膜内层是否分层、密封界面是否污染)。
§ 检查漏液是否为电解液泄漏(通过pH试纸或成分分析确认)。
3. 模式识别:
§ 判断漏液是 随机分布(多设备、多人员)还是 集中分布(同一设备、同一班次),初步锁定异常范围。
2. 分阶段排查(5M1E)阶段1:环境与测量验证· 环境(Environment):
o 检查车间 温湿度记录(是否超出工艺窗口,如温度>30℃导致铝塑膜变形)。
o 检测 洁净度(悬浮粒子数是否超标,导致封装面污染)。
· 测量(Measurement):
o 校准漏液检测设备(如真空测漏仪、氦检仪),验证检测方法有效性。
o 复测已检出的漏液电池,确认是否为 误判(如电解液残留误判为泄漏)。
阶段2:人员与操作排查· 人员(Man):
o 调取 操作录像,检查封装、搬运过程中的异常动作(如未对准、过度挤压)。
o 核查操作记录,确认是否有人为跳过步骤(如未清洁模具直接生产)。
o 对新员工进行 技能再评估(如热封参数设置、夹具使用熟练度)。
阶段3:设备与工艺验证· 设备(Machine):
o 对封装机进行 全参数校准(温度、压力、时间),验证实际值与设定值偏差。
o 检查热封模具的 磨损程度(用投影仪测量模具齿纹深度,磨损>10%需更换)。
o 测试真空封装系统的 密封性(保压测试,确认无泄漏)。
· 方法(Method):
o 复查工艺文件,确认参数是否合理(如热封温度是否超出铝塑膜耐温极限)。
o 验证 冷却工艺(封装后是否因急速降温导致内应力开裂)。
阶段4:材料与来料追溯· 材料(Material):
o 追溯漏液批次对应的 铝塑膜供应商批次号,复测关键指标(如拉伸强度、热封层厚度)。
o 对同批次电解液进行 腐蚀性测试(浸泡铝塑膜样本,观察72小时是否分层)。
o 检查极片/隔膜的 毛刺尺寸(是否>铝塑膜抗穿刺强度,如>50μm)。
3. 根因分析工具应用· 工具选择:
o 鱼骨图(因果图):组织跨部门会议,按5M1E分类列出潜在原因。
o 5Why分析法(示例):
1. Why漏液?→ 封装密封性不足。
2. Why密封性不足?→ 热封温度过低。
3. Why温度过低?→ 设备温控模块漂移。
4. Why未发现漂移?→ 设备点检表未包含温度校准。
5. Why未纳入点检?→ 设备维护规程未更新。
o FMEA(潜在失效模式分析):对高风险工序(如封装、注液)重新评估RPN值。
4. 验证与改进· 小批量验证:
o 针对可疑因素(如某台设备温度参数异常),调整后试产 100~200pcs,跟踪漏液率。
o 对比改进前后的 密封界面微观形貌(SEM扫描电镜观察是否均匀熔合)。
· 防错设计:
o 在热封工位增加 红外温度监控(实时反馈温度波动)。
o 对铝塑膜来料增加 自动扫码校验(拦截不良批次)。
· 标准化:
o 更新 SOP(如增加封装后冷却时间)。
o 将关键参数纳入 SPC(统计过程控制) 监控(如每日采集热封温度CPK值)。
5. 长效监控与闭环· 监控措施:
o 建立 漏液问题追踪看板,按小时统计不良率并与设备参数联动分析。
o 对返工/报废的漏液电池进行 根本原因标签化(如“设备-模具磨损”“材料-铝塑膜缺陷”)。
· 闭环管理:
o 每周召开 质量复盘会,针对未关闭问题制定行动计划。
o 将漏液率纳入部门KPI,与供应商质量协议挂钩(如铝塑膜批次不良率>0.1%则索赔)。
排查优先级建议1. 高发异常优先:同一设备/人员连续产出漏液电池 → 立即停机排查。
2. 低成本验证优先:先检查温湿度、设备参数等易调整项,再深入分析材料问题。
3. 风险预防优先:对验证有效的措施(如模具更换)快速横向展开至全车间。
通过以上步骤,可系统性地缩小问题范围,避免“头痛医头”,最终实现 问题归零。