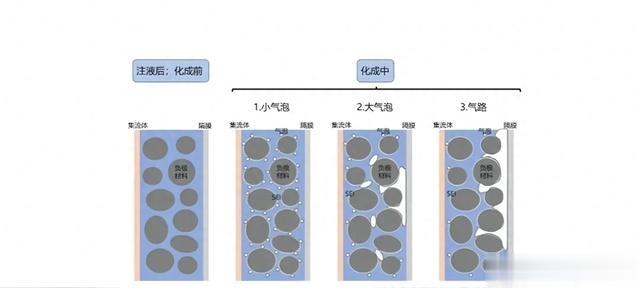
软包电池通常使用铝塑膜包装,相比圆柱或方形硬壳电池,更轻且形状灵活。Degassing,也就是排气或除气工序,在注液之后的步骤,化成之后进行的。
注液和化成过程中,电解液可能会分解产生气体。这些气体积聚在电池内部会增加内压,影响电池性能甚至导致鼓胀或安全问题。所以Degassing的主要目的应该是排除这些气体,确保电池内部没有多余的气体,同时可能还要密封电池。
同时需要控制参数,比如温度、时间、真空度,还有操作环境,比如湿度。涉及到的设备参数,比如抽真空的速度,保持真空的时间,以及密封的质量。此外,材料方面,铝塑膜的密封性能也很重要,在Degassing过程中需要加热密封,所以要控制温度,避免过高或过低导致密封不良或者材料损伤。
另外,可能要考虑气体的成分和产生的原因。比如化成过程中不同的正负极材料、电解液配方会产生不同的气体,了解这些气体的种类和量可以帮助优化Degassing的工艺参数。比如,如果产生的气体较多,可能需要更长的抽气时间或更高的真空度。
涉及工序的顺序问题。Degassing通常是在化成之后,因为化成是产气的主要阶段。在化成步骤中,SEI膜形成,副反应产气,之后需要排除这些气体。另外,是否需要在Degassing之前进行老化,让气体充分释放?或者是在Degassing之后再次进行老化测试?
还要考虑到后续工序,比如Degassing后的二次封装是否会影响电池的性能。密封的完整性是关键,否则可能导致电解液泄漏或外部空气进入,影响电池寿命。所以控制要素中,密封的温度、压力、时间都需要精确控制。
另外,安全性方面,抽气过程中是否会有电解液被抽出?如何避免电解液的损失,或者如何处理可能被抽出的电解液蒸气?这可能涉及到设备的设计,比如冷凝回收装置,或者调整真空度以避免过度抽取电解液。
环境因素,比如在Degassing过程中需要在干燥的环境中进行,避免水分进入电池内部,因为水分会与电解液反应,产生更多的气体或损害电池性能。因此,控制湿度也是一个关键点。
需要从以下几个方面展开分析并实施:
1. Degassing的主要目的:
- 排除内部气体,防止鼓胀。
- 确保电池性能和安全性。
- 为后续密封做准备。
2. 控制要素:
- 工艺参数:真空度、温度、时间、抽气速率。
- 材料因素:铝塑膜的密封性能。
- 环境控制:湿度、洁净度。
- 设备参数:密封的精度,防止泄漏。
- 气体成分分析:优化工艺参数。
- 电解液管理:避免抽出过多电解液。
软包锂电池Degassing工序的深度分析一、Degassing工序的核心目的
排除内部气体,防止鼓胀与安全隐患在注液和化成过程中,电解液分解、SEI膜形成等反应会产生气体(如CO₂、CH₄、H₂等),积聚的气体会导致电池内压升高,引发铝塑膜鼓胀甚至破裂。Degassing通过抽真空去除气体,确保电池结构稳定。残留气体会降低电解液浸润性,增加界面阻抗,影响容量和循环寿命。优化电池密封前的内部环境在抽真空后立即进行封装(热封),形成负压环境,避免外界空气(尤其是水分和氧气)渗入,减少副反应。提升一致性与安全性消除因气体分布不均导致的局部应力,避免热失控风险,同时提高电池批次一致性。二、Degassing工序的关键控制要素
工艺参数控制真空度与抽气时间真空度过低(如>-90 kPa)可能导致气体残留;过高(如<-98 kPa)可能抽出电解液蒸气,需根据电解液挥发性调整。通常控制在-95~-98 kPa。抽气时间需平衡效率与效果,一般为10~30分钟,可通过气体成分分析仪优化。温度控制热封温度需匹配铝塑膜材料(如PP层熔点约160~180℃),过高导致烧穿,过低引起密封不严。建议分阶段升温(预热+保压)。压力保持与二次抽气部分工艺采用多次抽气(如化成后首次抽气+静置后二次抽气),以应对气体缓慢释放。材料与设备适配铝塑膜性能阻隔性(水氧透过率<0.01 g/m²·day)、热封强度(>50 N/15mm)直接影响封装质量。需选择耐电解液腐蚀的层压结构(如尼龙/铝箔/PP)。设备精度真空腔体密封性、热封模具平整度(误差<0.1 mm)需定期校准,避免边缘漏气。环境与操作控制湿度控制操作环境露点需<-40℃(相对湿度<1%),防止水分在抽真空时渗入电池。洁净度管理颗粒物(如Class 1000洁净室)控制避免异物影响热封界面。气体成分与产气机制分析化成工艺优化调整化成电流曲线(如阶梯式小电流活化),减少剧烈产气。例如,硅碳负极产气量高于石墨,需延长Degassing时间。电解液配方适配含FEC添加剂的电解液产气量较低,可降低Degassing难度。三、常见问题与解决方案
电解液抽出现象:真空度过高导致电解液损失,电池容量下降。对策:采用梯度抽气法(先低真空后高真空),或添加冷凝回收装置捕获电解液蒸气。密封不良现象:热封边缘出现褶皱或裂纹,长期存放后漏气。对策:优化热封压力(0.3~0.5 MPa)与保压时间(3~5秒),采用激光辅助封口技术。气体残留检测方法:X射线成像(检测内部气泡)、氦质谱检漏(精度达10⁻⁸ Pa·m³/s)、压力差测试(ΔP<5 kPa为合格)。四、前沿技术趋势
在线监测系统:集成真空度传感器与气体质谱仪,实时反馈调整工艺参数。预Degassing工艺:在注液前对电芯进行真空烘烤,减少水分残留及后续产气。干法电极技术:从源头减少溶剂使用,降低产气量。通过精准控制Degassing参数,结合材料与设备创新,可显著提升软包电池的能量密度与可靠性,满足高镍、硅基等高活性材料体系的需求。
系统化步骤一、前期准备与参数设计
材料与设备确认铝塑膜性能验证:检查铝塑膜的阻隔性(水氧透过率、耐电解液腐蚀性)、热封层(PP层)厚度均匀性(±5%公差)。设备校准:确保真空泵抽速(≥10 m³/h)、真空腔密封性(泄漏率<1×10⁻³ Pa·m³/s)、热封模具平整度(误差<0.1 mm)。工艺窗口设计真空度分级设定:根据电解液挥发性分阶段抽气(如第一阶段-80 kPa抽5分钟,第二阶段-95 kPa抽20分钟),避免电解液蒸气损失。热封参数匹配:根据铝塑膜PP层熔点(160~180℃)设定热封温度梯度(预热→熔融→保压),压力控制在0.3~0.5 MPa。二、Degassing工序操作流程
电池预处理静置平衡:注液后静置≥4小时,确保电解液充分浸润极片,减少抽气时液体被带出。预封边检查:确认电池四边预封完整性(无褶皱、无漏液),避免抽真空时电解液泄漏。抽真空操作梯度抽气:低真空阶段(-80 kPa,5分钟):缓慢排出大气泡,防止电解液剧烈沸腾。高真空阶段(-95~-98 kPa,15~25分钟):彻底去除残留气体,实时监测真空度波动(波动范围<±1 kPa)。冷凝回收:若电解液蒸气较多,在真空管路中加装冷凝器(温度≤-10℃),回收挥发性溶剂(如DMC、DEC)。热封封装同步抽气与封口:在维持真空状态下完成热封,确保封装后电池内部维持负压(残留气压<5 kPa)。封边质量检查:封边宽度≥3 mm,热封强度≥50 N/15mm(拉力测试),目视无分层、烧焦。三、质量控制与检测
在线监测真空度曲线分析:通过传感器记录抽气过程的真空度变化,若曲线异常(如压力回升过快),需排查漏气或产气异常。气体成分检测:集成质谱仪(如QMS)分析抽出气体成分(CO₂、H₂、CH₄比例),判断SEI膜生成状态。离线检测X射线成像:检测封装后电池内部气泡残留(气泡面积占比<0.1%为合格)。氦检漏测试:氦气泄漏率<1×10⁻⁸ Pa·m³/s,确保长期密封性。循环后鼓胀测试:电池在1C充放电循环50次后,厚度膨胀率<5%。四、设备维护与工艺优化
设备定期维护每日清洁真空腔体,防止电解液残留腐蚀;每周校准热封模具温度(误差±2℃)与压力传感器。工艺持续优化数据驱动调整:结合产气量数据(如每Ah产气量<0.5 mL)优化化成工艺(如降低首圈充电电流)。新材料适配:针对硅碳负极等高产气体系,延长抽气时间至30分钟,或采用预锂化工艺减少产气。五、异常处理与标准化
常见异常对策电解液抽出:降低终段真空度至-92 kPa,或增加静置时间减少游离电解液。封边翘曲:调整热封模具压力分布,采用多段保压(如0.5 MPa保压3秒→0.3 MPa保压2秒)。标准化文件制定《Degassing工艺作业指导书》,明确关键参数容差(如真空度±2 kPa、温度±3℃);建立故障树分析(FTA)表,快速定位异常根因(如真空泵故障→密封圈老化→湿度超标)。六、人员培训与操作规范
技能培训操作员需掌握真空系统原理、热封参数调整方法,以及气体检测仪器使用。模拟异常场景训练(如突发停电时紧急保压操作)。SOP执行严格记录每批次抽气时间、真空度曲线、热封参数,实现全程可追溯。七、前沿技术整合建议
智能化监控:引入AI算法分析真空度曲线,自动识别产气异常(如电解液分解异常)。预Degassing工艺:在注液前对电芯进行真空烘烤(80℃、-90 kPa、2小时),减少水分残留导致的后期产气。干电极技术:采用无溶剂电极工艺,从源头减少溶剂挥发产气(适用于固态电池研发)。通过以上系统化步骤,可实现Degassing工序的高效、稳定控制,显著提升软包电池的良率与一致性,尤其适用于高能量密度(≥300 Wh/kg)电池的大规模生产。