在制造业车间里,你是否常听到这样的抱怨?“工具又找不到了!”“这批零件到底合格吗?”“为什么设备突然停机?”……这些问题看似琐碎,却可能让企业每年损失百万利润。今天,我们将深入解析一种被丰田、海尔等巨头验证过的管理利器——目视化管理,看它如何让工厂“会说话”,实现降本增效的奇迹。

目视化管理(Visual Management)通过颜色、标识、图表等直观手段,将生产信息转化为“10秒内可理解”的视觉信号。比如:
红黄绿警示灯实时显示设备状态地面标线划分物料区和通行道电子看板动态更新生产进度工具形迹图让每把扳手都有“专属座位”它让复杂的管理标准变得像交通信号灯一样一目了然。
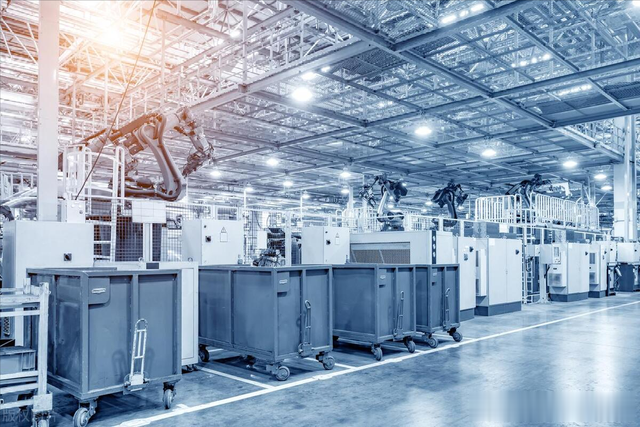
某汽车配件厂曾测算:工人每天平均花47分钟寻找工具、图纸或确认流程。通过目视化管理:
工具墙实施“形迹+颜色编码”,取用时间缩短80%工序流程图张贴在工位正前方,新人培训周期缩短50%设备异常通过LED灯柱分级报警,响应速度提升3倍数据印证:富士康深圳工厂推行目视化后,生产线平衡率从65%跃升至92%。
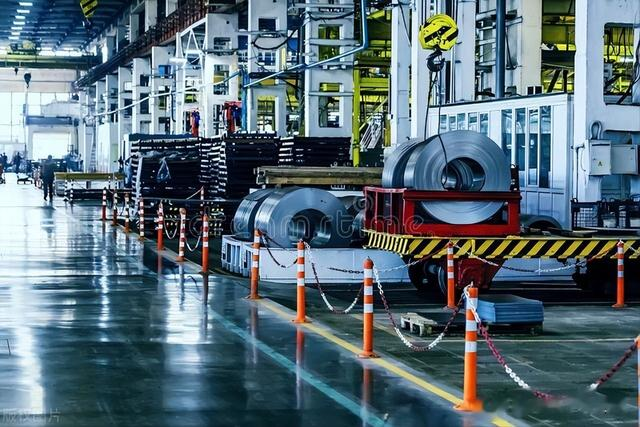
传统管理中,质量问题往往在成品检验时才被发现。而目视化管理构建了多层防线:
物料区黄线标识:库存低于安全水位自动预警首件检验展示台:每个班次的首个产品实物对比,杜绝批量错误安东系统(Andon):任何员工发现问题可立即拉绳停线,倒逼源头改善青岛某家电企业通过“缺陷可视化看板”,将产品不良率从3.2%降至0.8%。
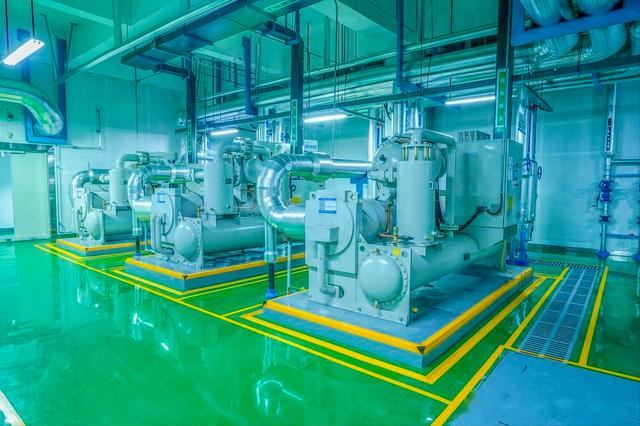
某化工企业曾因管道标识不清导致原料混淆,引发重大事故。目视化管理如何破局?
危险区域用黑黄斑马线+声光报警双重警示安全操作步骤以连环画形式张贴在设备旁每日安全状态通过“绿(安全)/红(风险)”挂牌公示日本新日铁推行安全目视化后,连续7年保持“零重大事故”纪录。

当生产数据实时呈现在车间看板上,普通工人也能成为改善专家:
绩效龙虎榜激发员工竞赛意识改善提案墙展示一线员工的智慧结晶问题追踪矩阵图让每个异常都有闭环处理记录海尔通过“人单合一”可视化系统,一年内收到员工改进提案2.3万条,创效超5000万元。
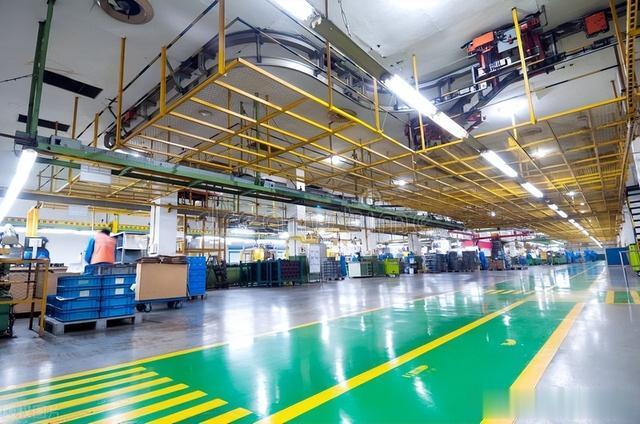
在工业4.0时代,当越来越多的企业追逐数字孪生、AI质检等高科技时,丰田却仍在车间坚持“手写看板”——因为这背后蕴含着管理的本质:让问题无处隐藏,让标准触手可及,让全员心有共识。
推行目视化管理,本质上是在打造企业的“视觉神经系统”。它可能没有炫酷的科技外壳,却是中国制造走向“高质量、低成本、快响应”的必经之路。您的工厂,准备好让每个角落都“会说话”了吗?