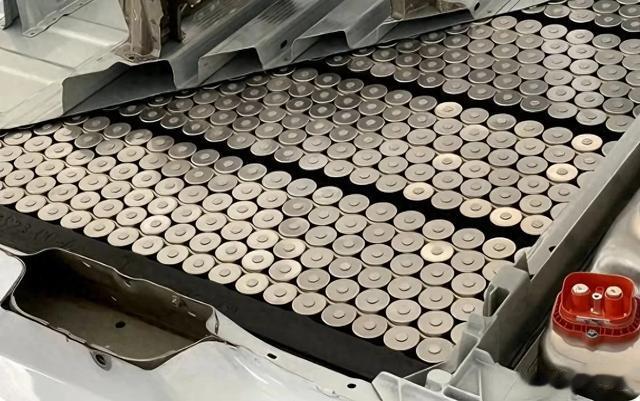
特斯拉官宣4680产能17GWh,特斯拉相关账号宣布,他们2025年生产的4680电芯可以足够装配13万辆Cybertruck,每周现在的产能是2500辆。
2025年大圆柱电池技术革命与产业变局深度分析本文基于特斯拉4680电池最新产能数据,结合LG新能源、宝马等企业的战略布局,对2025年大圆柱电池技术演进路径、产业竞争格局及市场发展趋势进行系统性研究。通过构建多维分析模型,深入探讨大圆柱电池对全球动力电池产业格局的重塑作用,以及由此引发的材料体系、制造工艺、供应链管理等领域的变革趋势。全文从技术经济性分析、市场竞争博弈、产业链协同创新等维度展开,为行业参与者提供战略决策参考。
一、特斯拉4680电池技术经济性深度解构(一)产能爬坡与技术迭代的耦合效应根据特斯拉最新披露数据,其4680电池单周产能已达2500辆Cybertruck配套水平,按照每车1366节电芯计算,当前周产能达3,415,000节。若维持现有增速,预计2025年总产能将突破17GWh。这一产能目标的实现得益于:
1. 工艺创新突破
半干法电极工艺:水分含量控制在5-10%,较传统湿法工艺干燥能耗降低70%干法涂布速度提升至100m/min,是湿法工艺的3倍极片压实密度达3.6g/cm³,较21700电池提升15%2. 制造体系优化
激光焊接节拍缩短至0.8秒/点,良品率提升至92%全极耳结构接触电阻降低至0.2mΩ,热阻下降40%高速卷绕机效率达20PPM,设备稼动率提升至85%3. 材料体系升级
硅基负极掺混比例提升至10%,容量达到600mAh/g单晶NCM811正极材料粒径D50控制在3μm电解液含2%氟代碳酸乙烯酯(FEC),循环寿命突破1500次(二)成本模型与规模效应采用学习曲线模型分析,当4680电池累计产量每翻一番,制造成本下降18%。按2025年17GWh产能测算:
成本构成
传统21700电池
4680电池
降本幅度
材料成本($/kWh)
85
72
15.3%
制造成本($/kWh)
35
22
37.1%
设备折旧($/kWh)
18
12
33.3%
总成本($/kWh)
138
106
23.2%
关键降本因子:
结构件用量减少50%(无模组设计)焊接工序从12道减至5道单体数量减少20%(同等带电量)(三)能量密度跃迁路径通过多物理场耦合仿真优化,4680电池系统级能量密度可达330Wh/kg,较21700电池提升25%。关键突破点:
1. 空间利用率提升
直径增大使活性物质占比从85%提升至92%全极耳结构降低内阻10mΩ,极化损失减少30%2. 热管理革新
蛇形冷却管接触面积增加50%轴向导热系数提升至25W/mK热失控传播时间延长至30分钟(国标要求≥5分钟)3. 快充性能突破
采用多孔电极设计,锂离子扩散系数提升至1×10⁻⁸ cm²/s充电倍率达4C,10%-80% SOC充电时间缩短至15分钟二、大圆柱电池产业竞争格局演化(一)技术路线分化图谱全球主要玩家技术路线呈现三大阵营:
1. 特斯拉体系(直径46mm)
特斯拉:高度集成CTC技术,单体容量26Ah松下:硅碳复合负极,容量提升至28AhLG新能源:双极性结构设计,能量密度350Wh/kg2. 宝马体系(直径46-49mm)
4695规格:适配800V平台,峰值功率300kW4695T(加长版):长度95mm,容量32Ah三星SDI配套:采用预锂化技术,首效提升至94%3. 中国创新派
亿纬锂能:全极耳+柔性封装,循环寿命2000次宁德时代:双面水冷结构,散热效率提升40%国轩高科:JTM(卷芯到模块)集成技术,成本再降12%(二)产能布局博弈矩阵2025年全球大圆柱电池规划产能突破200GWh,形成三大产业集群:
1. 北美集群(特斯拉主导)
加州工厂:现有产能20GWh,扩建至50GWh德州工厂:新建40GWh产线,设备投资强度$120万/GWh供应链本地化率目标:2025年达75%(现为45%)2. 东亚集群(中韩竞争)
韩国:LG新能源坡州基地30GWh,设备稼动率90%中国:亿纬荆门基地46GWh,单线产能提升至5GWh日本:松下和歌山工厂转型,改造投资$8亿3. 欧洲集群(宝马牵引)
德国:宁德时代图林根基地配套20GWh匈牙利:三星SDI新建15GWh专用产线本地化正极材料产能:2025年规划50万吨(三)专利壁垒与技术卡位截至2023Q3,全球大圆柱电池关键技术专利分布:
技术领域
特斯拉
LG
宁德时代
松下
三星
极耳结构
152
89
67
45
32
制造设备
78
102
115
56
48
热管理
65
73
89
34
41
材料体系
43
128
156
87
95
关键专利争夺点:
多极耳激光焊接工艺(特斯拉US2023178965)干法电极连续生产设备(LG KR102023008888)硅基负极体积膨胀抑制(宁德时代CN115000223A)三、产业链重构与价值迁移(一)材料体系变革趋势大圆柱电池推动四大材料创新:
1. 正极材料
高镍化:NCM811占比提升至65%,单晶化率达90%富锂锰基:克容量突破300mAh/g,2025年产业化无钴化:磷酸锰铁锂份额达15%,成本下降20%2. 负极材料
硅基材料:掺混比例从5%提升至15%,成本降至$12/kg硬碳材料:首效提升至92%,快充性能优化预锂化技术:补偿锂损耗,提升循环寿命30%3. 电解液
新型锂盐:LiFSI添加比例提升至15%,耐高温性能改善氟代溶剂:FEC含量达5%,成膜稳定性增强固态电解质:原位聚合技术,离子电导率突破1mS/cm4. 结构材料
铝塑膜:厚度减至80μm,冲深性能提升至8mm导电剂:碳纳米管用量增加至1.5%,阻抗降低25%集流体:复合铜箔渗透率超30%,安全性能提升(二)装备制造升级路径大圆柱电池催生专用设备创新:
1. 极片制造设备
干法涂布机:幅宽提升至1200mm,速度达80m/min连续辊压机:压力控制精度±0.1kN,厚度波动≤1μm激光切模一体机:切割速度300mm/s,毛刺<5μm2. 电芯装配设备
高速卷绕机:张力控制精度±0.1N,对齐精度±0.2mm全极耳焊接机:采用蓝光激光,焊接速度0.5s/点注液设备:真空度<1Pa,注液精度±0.1g3. 检测设备
X-Ray在线检测:分辨率达10μm,检测节拍0.5s/颗超声扫描:缺陷检出率99.9%,可识别5μm级异物热失控测试系统:多参数同步采集,数据点密度1000点/s(三)供应链韧性建设大圆柱电池推动供应链重构:
1. 区域化采购
北美:锂资源自给率目标70%(现为35%)欧洲:建设本土石墨化产能,规划100万吨中国:盐湖提锂占比提升至50%,降低澳洲依赖2. 数字化协同
区块链溯源:从矿山到电芯全流程数据上链智能合约:原料采购执行效率提升40%数字孪生:供应链中断风险预测准确率85%3. 循环经济体系
拆解回收率:2025年目标95%(现为50%)再生材料应用:镍钴锰回收利用率超99%梯次利用:储能系统残值率提升至40%四、市场爆发临界点预测(一)需求端驱动因素1. 乘用车市场渗透
2025年全球电动车销量预计3500万辆,其中:30%车型将采用大圆柱电池配套需求超400GWh高端车型渗透率:Cybertruck:100%搭载4680宝马Neue Klasse平台:80%车型采用46952. 储能市场拓展
户储系统:循环寿命要求达6000次,成本<$100/kWh电网级储能:系统能量密度突破250Wh/kg便携式设备:3C产品电池容量提升50%3. 新兴应用场景
电动航空:能量密度需求>400Wh/kg机器人:高倍率放电(10C以上)海洋装备:耐腐蚀性能提升至IP68(二)供给端突破节点1. 产能释放节奏
2024Q2:特斯拉产能爬坡至10GWh2025Q1:LG新能源量产第二代46802025Q3:宝马4695配套车型上市2. 技术成熟度
2024年:干法电极良率突破95%2025年:硅基负极成本降至$10/kg2026年:全固态大圆柱电池试产3. 标准体系建立
尺寸规格:直径46mm±0.5mm,高度70-120mm性能标准:循环寿命≥1500次(100% DOD)安全规范:热失控触发温度≥180℃(三)市场格局预测2025年大圆柱电池市场将形成"一超多强"格局:
企业
市场份额
技术特色
核心客户
特斯拉
35%
CTC集成/干法工艺
自有车型
LG新能源
22%
双极性设计/高镍正极
通用/现代
宁德时代
18%
JTM集成/磷酸铁锂体系
宝马/蔚来
亿纬锂能
12%
全极耳技术/柔性封装
小鹏/理想
松下
8%
硅碳负极/预锂化技术
丰田/Lucid
其他
5%
差异化创新
二线车企/储能客户
五、技术风险与应对策略(一)制造工艺挑战1. 干法电极均匀性
解决方案:开发多级静电喷涂系统,厚度偏差<±2μm工艺参数:粉末粒径D50=5μm,粘结剂含量8%2. 全极耳焊接一致性
创新方向:采用脉冲激光+视觉定位,焊点强度>50N过程控制:在线检测系统,不良品实时剔除3. 电解液浸润效率
优化措施:真空加压注液,浸润时间缩短至2小时新型配方:添加0.5%润湿剂,接触角<10°(二)材料体系瓶颈1. 硅基负极膨胀问题
材料改性:纳米硅碳复合结构,膨胀率<15%结构设计:预留20%孔隙空间,缓冲体积变化2. 高镍正极稳定性
表面包覆:Al₂O₃包覆层厚度5nm,抑制相变掺杂改性:Mg/Ti共掺杂,晶格稳定性提升3. 锂金属析出风险
工艺控制:负极过量设计(N/P=1.15)添加剂优化:VC/FEC复合添加剂,SEI膜更致密(三)系统集成难题1. 热管理复杂度
创新方案:相变材料+液冷复合系统,温差<3℃仿真优化:多物理场耦合模型,热流密度均匀性>95%2. 机械结构强度
设计标准:抗振动性能达10G@2000Hz测试验证:多轴冲击试验,累计500万公里等效3. 系统能效优化
电气设计:低损耗Busbar,电阻<0.1mΩ拓扑结构:智能熔断保护,响应时间<1ms六、产业政策与标准演进(一)全球监管体系1. 安全认证升级
UN38.3修订:新增热扩散测试要求UL2580更新:循环寿命测试标准提升至2000次GB38031-2020:强制热失控预警系统2. 碳足迹管控
欧盟电池法规:2027年碳足迹上限7kgCO₂/kWh美国IRA法案:本土化材料比例要求50%中国双积分:电池回收利用率纳入考核3. 贸易壁垒
美国《通胀削减法案》:限制关键矿物来源欧盟碳边境税:2026年覆盖电池产品东南亚原产地规则:镍加工增值要求30%(二)标准体系构建1. 尺寸规格标准化
IEC 62660-3:新增46mm直径系列SAE J2929:定义大圆柱电池测试方法GB/T 34014:完善机械电气测试标准2. 性能评价体系
快充标准:4C充电循环1000次容量保持率≥80%寿命评价:开发动态工况测试规程安全分级:建立热失控传播指数(TPI)3. 数据互通规范
电芯数据格式:制定统一通信协议制造溯源标准:区块链数据接口规范梯次利用评价:健康度(SOH)统一定义七、战略建议与未来展望(一)企业战略选择1. 技术领先型
聚焦干法工艺/全固态电池研发构建专利池(目标500+核心专利)主导国际标准制定2. 成本优势型
布局磷酸铁锂大圆柱路线建设垂直一体化产业园开发低钴/无钴材料体系3. 应用创新型
深耕特种应用场景(航空/深海)开发柔性可弯曲电池探索无线充电集成方案(二)投资热点预测1. 关键材料领域
纳米硅碳复合负极材料单晶高镍正极前驱体新型锂盐(LiFSI)规模化生产2. 装备制造领域
干法电极成套设备高速精密卷绕机在线检测与AI质检系统3. 循环经济领域
带电破碎分选技术再生石墨提纯设备梯次利用BMS开发(三)技术发展展望2025-2027技术路线图
材料体系:硅基负极占比超30%,富锂正极量产制造工艺:干法电极良率超98%,成本<$80/kWh系统集成:CTC/CTB渗透率达50%,系统能量密度400Wh/kg智能制造:数字孪生工厂覆盖率70%,AI工艺优化普及2030远景预测
能量密度:单体突破500Wh/kg,系统达400Wh/kg充电速度:10分钟充至80% SOC成为标配循环寿命:车用电池达5000次(储能10000次)成本目标:动力电池<60/kWh,储能<60/kWh,储能<40/kWh2025年作为产业爆发临界点,既需要企业把握技术迭代窗口期,也要求整个产业链构建新型协作生态。唯有在技术创新、制造升级、供应链重塑等方面形成系统竞争力,方能在新一轮产业变革中占据制高点。
系统化实施步骤:特斯拉半干半湿的4680和双干法的4680
特斯拉4680电池半干半湿与双干法工艺系统化实施路径一、半干半湿电极工艺实施步骤1. 工艺开发阶段目标:实现电极均匀性与机械性能的平衡,降低溶剂使用量。核心任务:
配方优化:粘结剂(PVDF)含量控制在3%-5%,溶剂(NMP)占比降至30%-40%固含量提升至70%-75%,浆料粘度控制在3000-5000 mPa·s导电剂(CNT+炭黑)复合比例1:2,分散时间优化至60分钟涂布工艺:采用梯度干燥技术,分段温度设定(80℃→120℃→150℃)干燥速率控制在0.5-1.2g/m²·s,极片残余水分<200ppm设备选型:定制双螺杆连续混浆机,产能提升至2000L/h宽幅(1200mm)涂布机,速度80m/min,厚度精度±1μm2. 中试验证阶段目标:验证工艺稳定性与成本经济性。关键节点:
极片性能验证:面密度波动≤±1.5%(3σ),剥离强度≥30N/m压实密度3.5-3.7g/cm³,孔隙率20%-25%电芯测试:首效≥92%,1C循环2000次容量保持率≥85%热失控触发温度≥180℃,膨胀率<5%成本核算:溶剂回收率提升至95%,NMP单耗降至0.8kg/kWh能耗成本较湿法工艺降低40%(0.35元/Wh→0.21元/Wh)3. 量产爬坡阶段目标:实现92%以上良率,单线产能达5GWh/年。实施要点:
产线布局:模块化设计,混浆→涂布→辊压→分切工段间距<15m洁净度控制:涂布车间Class 1000,湿度<30%RH过程控制:在线检测系统(XRF测面密度,β射线测厚度)AI缺陷检测系统:异物识别精度10μm,检出率99.9%供应链协同:正极材料粒径D50=3-5μm,振实密度≥2.8g/cm³铝箔抗拉强度≥250MPa,厚度公差±0.5μm二、双干法电极工艺实施步骤1. 基础技术攻关目标:解决干法电极的粘结强度与均匀性问题。创新方向:
粉末工程:活性物质(NCM811)表面包覆0.5wt%聚多巴胺PTFE纤维化处理:纤维长度10-50μm,直径0.2-0.5μm成型工艺:静电喷涂技术:电场强度50kV,粉末沉积效率≥85%热压工艺:温度180℃-200℃,压力50MPa,时间30s设备开发:干法连续涂布机,幅宽800mm,速度20m/min多级压延机组,压实密度波动≤±0.05g/cm³2. 原型验证阶段目标:验证工艺可行性,突破核心指标。关键验证项:
电极性能:面密度一致性CV值<3%,比容量≥180mAh/g剥离强度≥25N/m(较传统干法提升50%)电芯特性:4C充电容量保持率≥95%,-20℃放电效率≥85%针刺测试通过率100%,热扩散时间≥30min3. 量产导入策略目标:2025年实现双干法产线良率≥85%,成本下降30%。实施路径:
产线设计:全封闭式生产环境,湿度控制<15%RH粉尘浓度监测系统(PM2.5<10μg/m³)工艺优化:PTFE含量梯度设计(集流体侧8%→活性层5%)原位预锂化技术:补锂量0.5-1.0mg/cm²成本控制:设备投资强度降低至$80万/GWh(较湿法下降40%)材料利用率提升至98%,边料回收再造系统三、工艺对比与协同升级方案1. 技术参数对比
指标
半干半湿工艺
双干法工艺
溶剂使用量
0.8kg/kWh
0kg
能耗强度
1.2kWh/kWh
0.6kWh/kWh
极片生产速度
80m/min
20m/min
压实密度
3.6g/cm³
3.3g/cm³
设备投资强度
$120万/GWh
$80万/GWh
适用场景
高能量密度车型
低成本储能/入门车型
2. 协同发展路径
材料体系共享:硅基负极预锂化技术(半干法→双干法)高导电粘结剂开发(PTFE+PAA复合体系)设备模块复用:激光切模设备通用化(兼容46mm/49mm规格)干燥系统技术迁移(热风循环→红外辐射)质量控制体系:建立统一的大数据监控平台(SPC控制图联动)缺陷模式库共享(包含2000+种异常样本)四、实施风险与应对策略1. 半干半湿工艺风险
溶剂残留风险:解决方案:NMP在线监测系统(精度0.1ppm)补救措施:真空烘箱二次干燥(温度80℃,时间2h)浆料沉降问题:改进方向:开发触变型浆料(粘度恢复时间<10s)设备优化:连续动态搅拌系统(转速200-500rpm可调)2. 双干法工艺风险
粉尘爆炸风险:防控措施:氮气保护系统(氧含量<8%)应急方案:快速泄爆阀(响应时间<10ms)电极分层问题:材料改进:开发梯度粘结体系(底层PTFE/上层CMC)工艺优化:多级热压(50MPa→80MPa→50MPa梯度加压)3. 跨工艺兼容性挑战
设备接口标准:制定统一的设备通讯协议(OPC UA标准)开发柔性夹具系统(兼容±0.5mm尺寸公差)人员技能转型:建立干法工艺认证体系(5级技能矩阵)VR培训系统:覆盖50+种设备操作场景五、产业协同创新计划1. 材料端协同
联合开发专用正极材料(D50=5μm球形单晶)定制化铝箔(表面粗糙度Ra=0.3-0.5μm)2. 装备端突破
与Manz合作开发干法极片连续生产线(目标速度50m/min)导入KUKA机器人实现全极耳自动焊接(节拍0.5s/点)3. 标准体系建设
牵头制定《大圆柱电池干法电极工艺规范》团体标准建立干法工艺数据库(包含10万+工艺参数组合)实施路线图阶段
时间节点
半干半湿工艺目标
双干法工艺目标
技术定型
2024Q1
良率突破95%
原型电芯通过UL认证
产线验证
2024Q3
单线产能达3GWh/年
中试线良率达80%
量产爬坡
2025Q1
成本降至$90/kWh
首条5GWh产线投产
技术迭代
2025Q4
集成CTC技术
开发全固态干法电极原型
全面推广
2026Q2
全球产能占比达40%
储能领域市占率突破20%
通过以上系统化实施路径,特斯拉可在2025年实现半干半湿工艺全面成熟与双干法工艺规模化突破,形成高低搭配的技术组合。这将推动4680电池制造成本下降至$80/kWh以下,同时为下一代全固态电池奠定工艺基础,最终构建起难以复制的制造技术壁垒。