对于任何材料系统而言,航空发动机都是最恶劣、要求最高的环境之一。再加上行业对更高推力、更轻重量和更高效率以及更低成本的持续要求,这意味着引入金属基复合材料(MMC)等先进复合材料将需要密集而全面的开发计划。
要确保安全地从传统的整体金属过渡到金属基复合材料,就必须了解从宏观尺度到材料微观尺度的组件行为。本文探讨了在航空发动机中使用铝和钛基复合材料的潜在好处,讨论了加工工艺,并考虑了一些相关问题。
铝复合材料的特殊属性是兼具高比刚度、良好的疲劳性能以及相对低成本和传统工艺的潜力。此外,还可以定制这些材料的机械和热性能,以满足特定应用的要求。为此,需要考虑许多变量,包括增强材料的类型和级别、基体合金的选择以及复合材料的加工工艺。
所有这些因素都是相互关联的,在开发新材料时不应孤立考虑。铝复合材料的开发已有多年历史,在此期间,人们尝试了大量不同类型的增强材料,并取得了不同程度的成功。其中包括单丝和多丝连续纤维、短纤维、晶须和微粒。
多年来,人们尝试了许多不同的基体,这些基体对复合材料所能达到的某些性能有影响。耐腐蚀性、强度水平、韧性等都深受基体合金的影响。一般来说,标准工程合金通常会被使用,但其形式会稍作改变,以接受所选的增强材料。增强材料的类型也会影响制造方法。
处理单丝的方法与处理微粒甚至短纤维加固材料的方法不同。罗尔斯-罗伊斯公司目前正在考虑将铝复合材料应用于燃气涡轮发动机,这种复合材料是微粒增强型的。
即使有这种限制,也可以采用多种加工方法,还可以进行二次加工,进一步调整材料性能,以满足特定组件的要求。在加工方面,微粒强化的最大优点是可以使用传统的金属制造方法和加工技术。与其他复合材料相比,使用铝质多孔材料更经济,因为其他复合材料传统上价格昂贵,劳动强度大。
目前,最有可能用于航空发动机部件的铝金属多层陶瓷复合材料是以细小的碳化硅颗粒(即小于12微米)增强的复合材料。这种复合材料是通过粉末冶金工艺生产的,方法是将碳化硅与元素粉末或预合金粉末进行简单混合或机械合金化,以AA2000和6000系列合金为基础。这些都是强度、延展性和韧性的最佳组合。
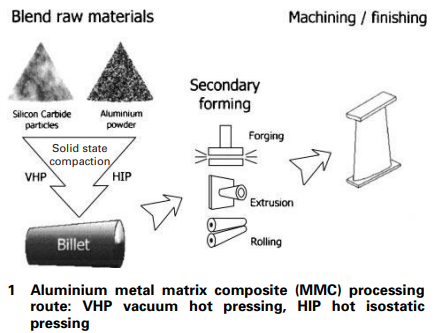
粉末在固态下通过热等静压或真空热压固结成坯料。然后可通过锻造、轧制、挤压等传统方法进行进一步加工,随后进行机加工。人们发现,等温锻造在流动特性、结构一致性、性能和尺寸精度方面效果特别好,从而减少了锻造操作。
因此,与传统锻造相比,等温锻造使用的坯料尺寸更小,所需的机加工也更少,当原材料比某些传统材料昂贵且更难加工时(建议使用金刚石工具),等温锻造是一个不错的选择。最终部件的机械性能在一定程度上受加工工艺和加工量的影响,但使用细粉可确保良好的晶粒结构控制,并保持相对各向同性的性能分布。
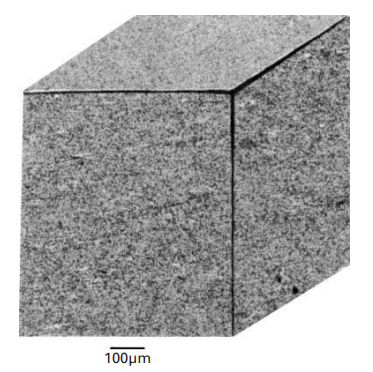
上图展示了采用粉末冶金工艺生产的铝金属挤压成型件的典型微观结构。
从目前进行的评估工作来看,预计铝MMC在发动机运行环境中需要与传统铝合金类似程度的防腐蚀和防侵蚀保护。铝MMC可以进行令人满意的阳极氧化处理,但需要对加工参数进行一些修改,以获得足够厚度的保护膜。耐侵蚀性略逊于未强化的铝。
也可以使用其他侵蚀保护涂层,但其中一些涂层需要进行脱脂处理,这可能会损害材料的结构和性能。因此,应避免使用这类涂层。
这类复合材料的机械性能通常介于未增强的铝合金和钛合金之间。不过,通过仔细选择基体合金和强化程度,可以改变性能的平衡。后者可在0和60vol.%。
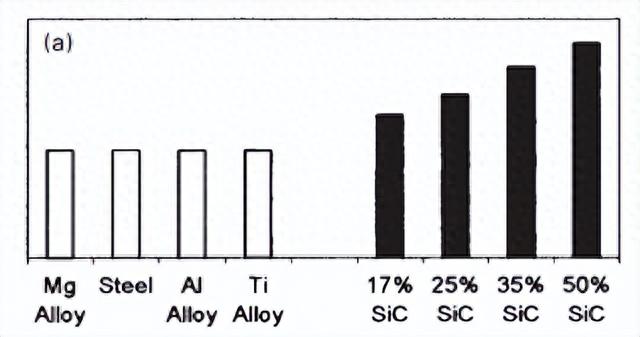
因此,可根据特定应用的要求调整其性能。考虑到密度因素,铝质多孔材料的特定性能明显高于其他常用的航空航天材料,包括钛和钢。不过,它们在工作温度范围内受到铝基体的限制。
与传统材料相比,性能改善最显著的例子可能是比模量。对于钢、镁、铝和钛合金而言,这一比率约为27,而在铝质多孔材料中,通过引入50Vol%的增强材料,这一比率可提高一倍以上。
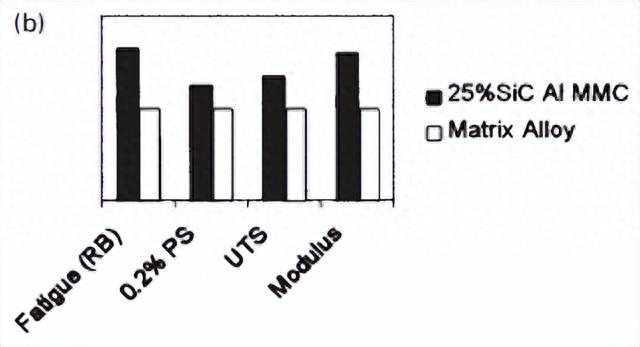
增加SiC微粒的用量也可以提高强度,但这也会导致延展性降低,因此必须达成折衷方案。对于大多数结构应用而言,这一比例应在15至25Vol.-%之间,但如果热膨胀控制非常重要,则可使用更多的SiC。
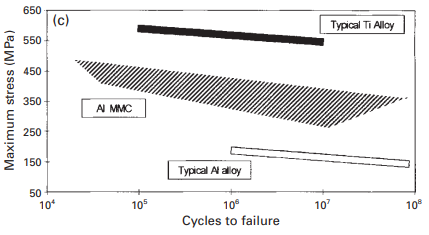
通过在铝中加入细小的碳化硅微粒,还可大幅提高疲劳极限,从而使铝MMC可用于以前仅限于钛等高抗疲劳材料的应用领域。
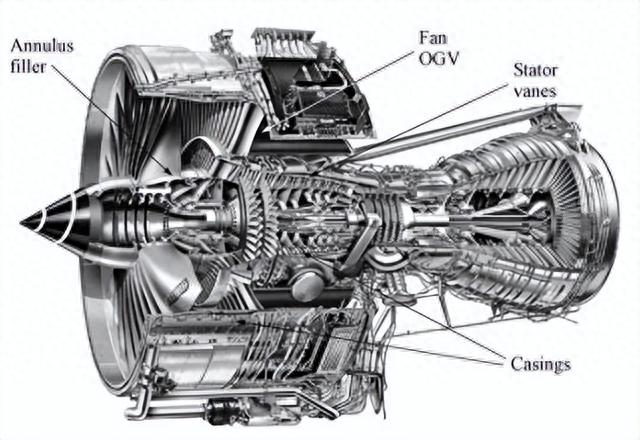
在航空发动机中的潜在应用是在压缩机前端和风扇旁路结构中,其中最高工作温度不超过150°C。铝质多孔金属锰可用作以下材料的替代品对于需要提高性能,但钛组件会增加重量的非强化铝材这是不可取的。
在减重尤为重要的情况下,铝金属流变模塑材料很可能成为钛金属的有效替代品。不过,作为原材料,AlMMC目前比Al或Ti都要昂贵,不过随着批量生产,成本应该会大大降低。
压缩机前部附近的静态和可变叶片可能是采用铝金属镁的最佳机会,因为它们将取代钛6/4锻件,从而减轻重量。目前,这种材料的强度和疲劳性能还不够高,无法用于叶片。用相同的铝金属镁锻件替代每个钛叶片可减轻重量35%成本的大幅节省将取决于原材料的成熟成本。
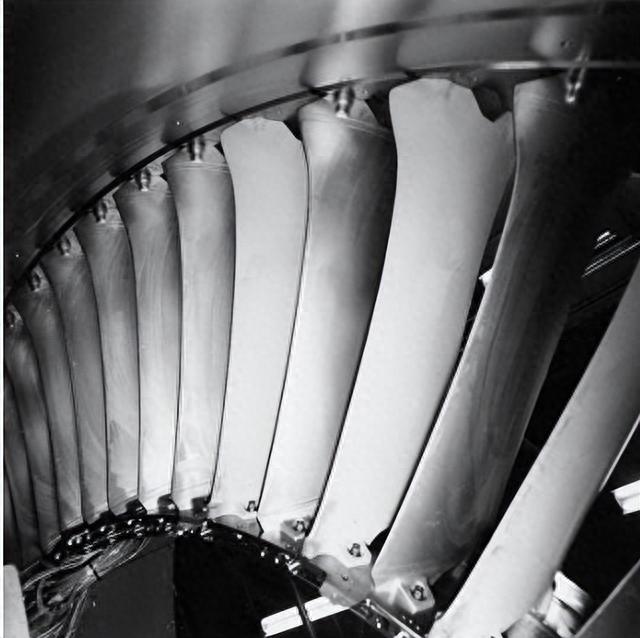
特伦特发动机的风扇出口导叶(FOGV)组件是改用铝质MMC后可节省大量成本的一个特殊应用。它位于发动机核心和机壳之间的风扇后面。这些叶片将空气导入旁通管道,因此其最高工作温度在AlMMC的限制范围内。
叶片很容易受到冰雹和鸟类的破坏,因此需要良好的耐侵蚀和耐腐蚀性能,以及AlMMC所能提供的良好疲劳性能和高硬度。目前,这些叶片是由钛制造的,分析表明,用简单的实心铝MMC锻造件直接替换其中的一些空心叶片可节省约50%的成本,每替换一个叶片可减轻约15%的重量。
除了静态叶片和可变叶片外,还考虑了用铝质MMC制作可变进气导叶(VIGV)杠杆和相关谐振环的潜在好处。这可能需要进行一些重新标记工作,但在替代钛时可以减轻一些重量。铝质MMC的高比刚度对齐音环有利,但需要对其承受轴承应力的能力进行评估。
还可以考虑其他一些特殊应用。压缩机前端的转子外壳,其工作温度低于有可能达到150°C。铝质MMC将铝或钛的替代品。钛可能通过增加膨胀系数来改变膨胀系数可以为设计者提供另一种重要变量,以获得更好的刀尖间隙匹配,从而改善了发动机浪涌余量。
铝复合材料的密封性能虽然还没有对铝质多孔材料的延展性和强度进行详细评估,但由于铝质多孔材料的延展性较低而强度较高,因此可能需要比铝质多孔材料更厚的外壳。如果设计和实际情况允许,可以通过添加凯夫拉纤维包层来尽量减少这种情况。环形填料也可用于铝MMC。与未强化的铝合金相比,铝MMC具有更优越的疲劳和刚度性能,而且不会增加重量。
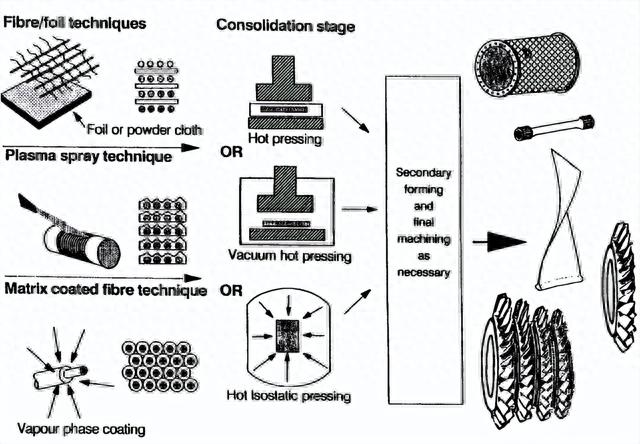
钛MMC组件的主要制造路线如上图所示,具体说明如下。
纤维和箔式方法是最成熟的方法,已被用于制造各种形状的组件。然而,由于在固结过程中会产生大量脱层,而且箔的柔韧性相对较差,因此限制了可考虑的形状的复杂性。
铝箔的成本并不低,因此,人们已经开始尝试使用不同的基体形式,如粉末或金属丝。固结时的除渣这种工艺的成本仍然很高,主要限制了它在以下方面的开放式"结构或薄环。
这种工艺能够生产大面积的单层预浸料。使用真空等离子或感应等离子喷涂系统将钛合金粉末直接沉积到缠绕纤维鼓上。生产出的板材堆叠在一起,然后以类似于预浸料的方式进行加固。
事实证明,在喷涂过程中对纤维及其涂层造成的冲击损坏是这种技术的一个问题,预浸片的柔韧性有限也限制了可制造的部件类型。
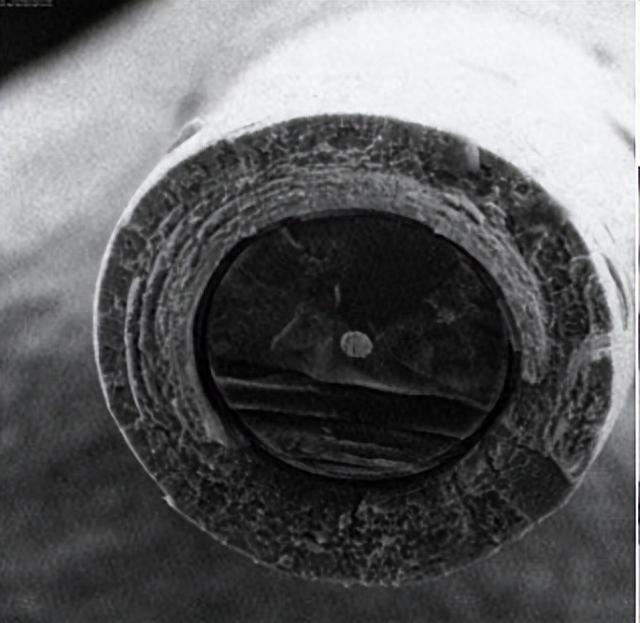
金属涂层纤维加工美国3M公司和英国DERA公司独立开发,采用电子束物理气相沉积(EBPVD)工艺将金属涂层直接涂覆在碳化硅纤维上。纤维连续通过钛合金熔池上方的蒸汽云。蒸汽凝结在移动的纤维上,形成连续均匀的基体涂层。虽然有时可以看到涂层厚度略有不同,但很明显,固化后的复合材料不可能含有接触纤维,纤维分布近乎完美。
这种工艺尤其适用于压缩机叶片等关键旋转部件。涂层工艺和后续部件制造工艺的自动化将为未来降低成本和工艺控制监测奠定基础。钛或金属间基体用连续的碳化硅纤维增强,并沿主要载荷方向排列,最有可能用于高负荷航空发动机。
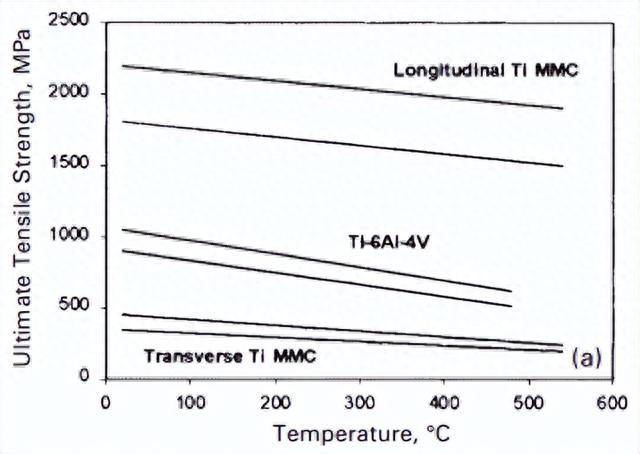
如图所示,与基体合金相比,单向复合材料在纤维方向上的强度和刚度显著增加。横向刚度保持不变,但横向强度有所降低。直到最近,钛MMC材料的机械性能仍受到制造和加工缺陷的严重影响。
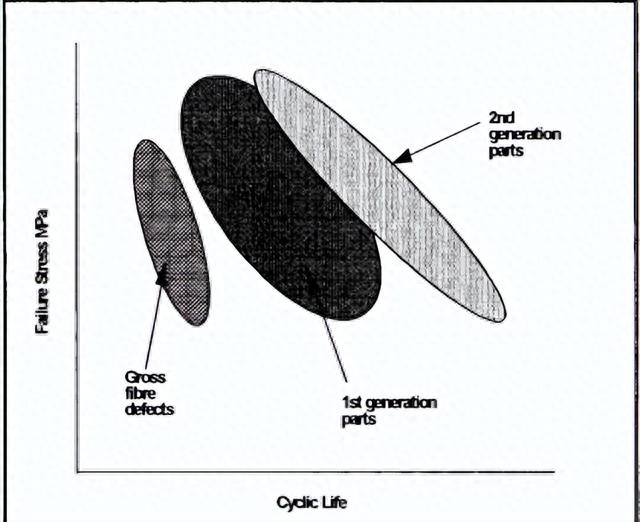
低循环疲劳性能对此最为敏感,其示意图如图所示。图中左侧的区域显示了严重纤维缺陷的影响,即相邻的几个纤维层断裂。毫不奇怪,这对机械性能的影响最大。然而,使用X射线或超声波无损评估(NDE)技术很容易发现这些缺陷。
局部纤维断裂和基体缺陷的中心区域更值得关注,因为如果不进行大量的技术开发,在这一区域进行无损检测不太可能找到所有的缺陷部件。此外,这种详细检测的成本也过高。因此,建立具有适当过程控制的高质量加工工艺对于将钛金属微晶材料成功引入航空发动机至关重要。
工作温度限制主要由基体合金决定,Ti-6Al-4V复合材料的工作温度限制为350°C和Ti6242复合材料达到500-550°C。因此,主要用于压缩机部分发动机的叶片、叶片、壳体和圆盘都是潜在的应用领域。
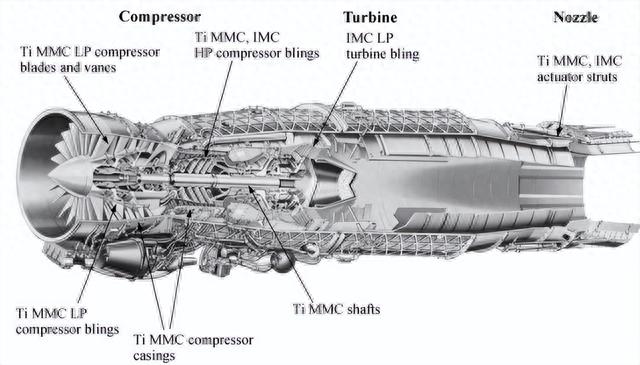
目前,高压(HP)压缩机后端的高温要求使用重型镍基超合金制造圆盘,使用钢或镍合金制造外壳。未来金属间化合物(如正交钛铝化物)的发展将为高压压缩机热端提供合适的强化基体。上图展示了军用航空发动机的这些潜在应用领域。
通过纤维增强来提高刚度,为叶片设计者提供了调整叶片负载性能的机会。提高材料刚度还能改变叶片的共振频率,从而在发动机运行范围内消除任何破坏性的振动模式,而无需过度加厚截面或增加重量。风扇叶片质量的减少会产生"连锁"效应,从而进一步减轻盘、外壳和安全壳结构的重量。
据预测,与传统的钛合金叶盘相比,钛MMC压缩机叶片(叶环)的重量最多可减轻40%。这种应用非常适合单向增强的钛MMC,因为其主要载荷在环向。横向的径向载荷可以保持在相对较低的水平。
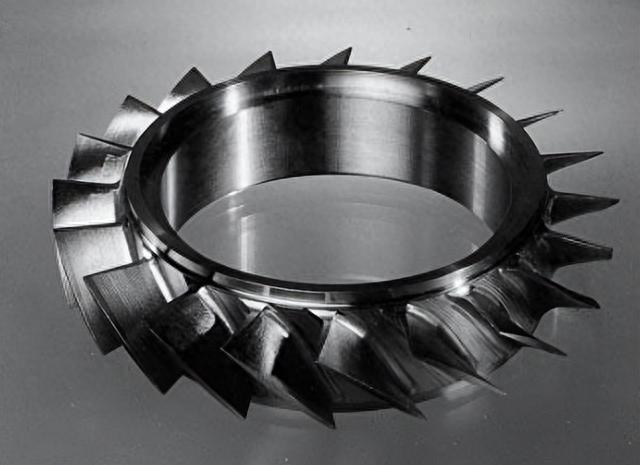
因此,简单的叶片设计既能充分发挥钛金属软管的良好纵向性能,又能保护最薄弱的横向方向。在压缩机叶片中使用钛MMC并保留可更换叶片的设计是可行的。然而,这将导致重量减轻,因为钛金属镁现在承担了叶片根部固定的额外寄生重量。
最新材料形式(被称为第二代材料)在复合材料质量方面的重大改进,将有助于建立预测性吊装能力。未来的钛MMC组件将只进行部分强化,因此将需要混合使用多种提升方法,即未强化区域将能够使用传统的整体规则。这就要求在进行应力分析时非常谨慎,以确保在从复合材料到非复合材料发生变化时,能够正确模拟潜在缺陷的影响。
本文介绍了MMC技术的一些关键领域。最新的加工技术大大提高了复合材料的质量,有望改善性能和可靠性。在关键部件的重量减轻方面具有明显的潜力。成本仍然是一个重要因素。
成本仍然是一个重要的因素,显然,要达到未来的部件成本目标,必须大力降低材料和工艺的成本。通过使用综合产品开发团队来整合制造、设计和工程活动,是最佳的发展途径。通过合作计划开展全行业的合作也是在航空发动机中成功实施MMC技术的关键。